Working at Joseph Evans
In March 2006 John Mackay, who is working on a
pump at the Bratch, wrote:
I was the first (and probably the last...) Progress
Chaser at the Culwell from end of 1954 to 1956. So I was not
an engineer but I did have the o.k. to roam around the works checking
stock (and stock taking) for outgoing orders. I worked in the
accounts office. My boss was an accountant called Mills and the
feeling was that he was closely involved with the Pulsometer takeover
and eventual transfer of the whole production to Reading.
"The foundries cast iron and bronze too, I think. The company was very old fashioned. The Machine Shops were full of Belt
Driven Lathes etc. At the back of our office, which was to the
left as you went through the gates, there was a vaulted roofed stockroom
and a storeroom which kept paperwork and old catalogues, leaflets etc.,
ranging from Shadufs, to Archimedian, to their well known Hand Pumps,
Rotary and Steam driven pumps of recent date.
"I am almost certain that the start date for Joseph
Evans was very much earlier than the early 1800s. We had spares
and parts for pumps possibly older than that and my memory goes back
to large catalogue books going back to about 1760. Stuff for the Great
Exhibition too. I left to join Bayliss Jones and Bayliss after about 18
months.
|
In November 2007 Mike Langford wrote:
I was 15 when I became an apprentice at Joseph Evans
& Sons, starting on December 26th 1952 until November 1959. During this period I worked in the fitting departments, machines
shops, foundries (where I also learned core making) and the marking
off department.
As reported elsewhere, the machine shops in both B &
C Departments when I started there were predominately belt driven.
This meant that whenever an operator had to replace the belt to his
machine all other machines were forced to cease work. I was
astounded that some of the operators took their personal safety so
lightly that when they wanted to change the machine speed, instead
of using the supplied wooden tool to flip the belt to a different
pulley, they simply used their hand. The belts were coupled together
with interlocking metal staples with a sort of leather plug holding
the two ends together. As you can imagine there were some
pretty horrendous accidents although really they weren't accidents
at all. Slowly self contained machines were introduced but
still, when I left the company, the drive shafting was still in use
throughout the shop.
|
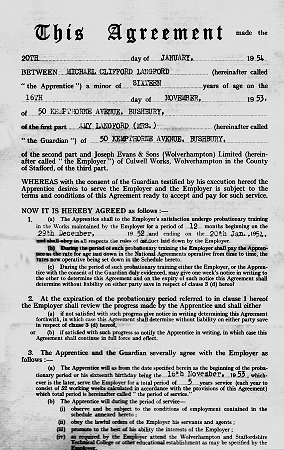
Part of the first page of Mike's
appenticeship acceptance, to start on his 16th birthday
in 1953. His mother had to pay £10.00, which was taken
from my wages at 2/6d per week, and was to be spent on
tools. |
A friend that I was at school with lived in one of a
block of terraced houses on the A449 Stafford Road just
out of Wolverhampton, and at the back of these houses
was their water supply, a J E & S hand pump about 6ft
tall. Very often my friend's mother would make the
journey to Frederick Street in Heath Town to purchase a
new leather cup washer to enable the pump to work
efficiently again. This was still going on well
into the late 1950s.
In my spell in the fitting shop one of the pumps I
worked on with my chargehand, Mr Tom Barker, was a
very tall centrifugal pump that was apparently to be
used for pumping molten lead.
Most of my other
fitting shop jobs were on Pulsometer centrifugal pumps.
These were much easier to build than the previous J E &
S reciprocating types, which really were a work of art.
A main part of these pumps was called a steam
valve chest and these really were extremely complicated,
with valves and pistons opening and closing in a
specific sequence to enable the pump to function.
I came upon something very similar when I joined a
company called H M Hobson, only in this case they were
for flying controls. |
There were many times that I would fetch a drawing
from the drawing stores and find it had been made in 1890 or 1901
and these were on linen not paper, with each different
material shown in a different colour: they were superb. I
loved my time in this industry and it was widely held in the area
that if you had served your time at the Culwell you could work
anywhere. I stayed on for another year after my apprenticeship ended
and then decided that affection for my place of work was not enough.
Working on the marking off table I was on the top rate on the shop
floor: 198 shillings and 4 pence -just under £10 per week for
a 46 hour week. The work had started to become scarce and I
was 21 so I went to pastures new. But I have never forgotten
the factory, the people and the atmosphere. For almost eight years
they were my life, my formative years - and I enjoyed every one of
them.
|
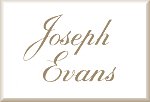 |
|
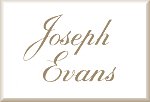 |
|
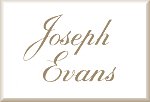 |
Return to the
1930 catalogue |
|
Return to
the beginning |
|
Proceed to
Evans pumps today |
|