The Turner Manufacturing Company
originated as an engineering business around the middle
of the 19th century. Amongst their early
products were velocipedes, bicycles, tricycles and cars.
The early business had various premises including works
in Brickkiln Street, Walsall Street and later Lever
Street. It was known as Thomas Turner & Company.
Around 1902 the company’s owner,
James Burns Dumbell, a very astute business man, decided
that the way forward lay in the production of motor
cars, and so the manufacturing rights of a well
established vehicle, the Belgian Miesse steam car were
obtained. It is believed that Turners, at least for a
time, purchased running chassis from the Brussels based
company of J. Miesse and simply added their own
bodywork. |
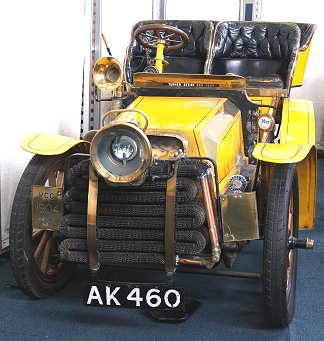
The Turner-Miesse steam car at the Black Country
Living Museum, Dudley. |
In 1906 the firm became a private
limited company under the name of the Turner Motor
Manufacturing Company Limited with Mr. Dumbell as
Managing Director. Around the same time they began to
manufacture their first petrol engined cars under the
name of Seymour-Turner.
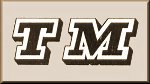 |
Read about
Turner cars |
|
Car manufacture
continued until the beginning of the First World War
when Turner’s manufacturing came under the control of
the Ministry of Munitions who gave them a contract to
produce machine tools. As a result the company developed
one of the earliest motorised capstan machines, at a
time when most pieces of machinery were still
belt-driven from overhead line shafting. The machine was
extremely advanced and it continued in production until
the Second World War when the Ministry of Defence
directed Turners to sub-contract production to Jowett of
Idle, Bradford.
Other machines
were also developed including a self-contained motorised
tool-cutter, and a gauge grinding machine, both of
advanced design. Production again continued until the
Second World War, when the Ministry of Defence
transferred the work to the Turner Tanning Machine
Company of Leeds.
After the First World War, car
manufacture restarted with an unsuccessful and
short-lived joint venture with Varley Woods, but Turner
cars did not reappear until 1923. In the early 1930s
Turners produced a small booklet which included the
details of the company's early history and described its
various departments at Wulfruna Works, Lever Street. |
The Capstan Department had an excellent range of
over 30 capstan and turret lathes from
⅛ inch to 4 inch capacity.
The machines included No. 4, No. 9, and No. 15 Herbert
capstans and several machines of the company's own
manufacture. |

The Capstan Bay. |
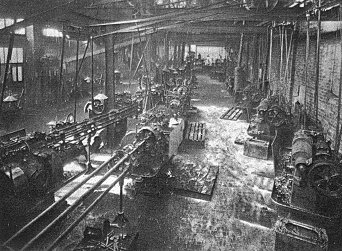
The Automatic Bay. |
The Automatic Department had a variety of 4 spindle
and single spindle machines that were used for quick
repetition work. Parts could be machined up to 1⅝
inch diameter. |
The Hardening Department had an up-to-date system
using the Muffle furnace and the salt bath method. Salt
bath furnaces were installed in the machine lines to
facilitate rapid production. All furnaces were
scientifically controlled. |
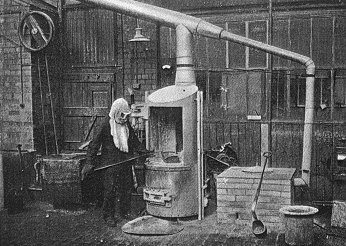
A corner of the Hardening Shop. |
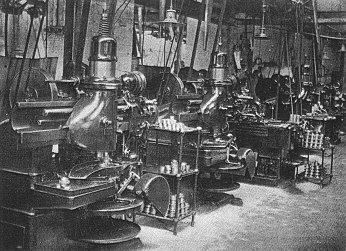
A few machines in the Gear
Cutting Department. |
The Gear Cutting Department had a variety of
machine tools including Fellowes gear shapers,
Barber Colman spline millers, broaching machines,
gear hobbing machines, and tooth rounders. Efficient
testing apparatus was also installed. |
The General Machine Shop had many special machines
and a large variety of machine tools. There were lathes,
milling machines, planing machines, boring machines, and
drilling machines. Grinding could be accommodated up to
14 inch diameter by 96 inches long. The Inspection
Department carried out careful inspection of all the
material that entered the works, using the most
up-to-date equipment. All machined parts were inspected
both during and after manufacture.
The Drawing Office facilities were available to
customers for the development of their requirements. In
the Fitting Shops complete production of a component was
preferred wherever possible. Ample space for the purpose
was available in the Assembly Shop.
The booklet ends with the company's motto: "The
accurate product at the right price".
During the inter-war years Turners
foresaw the slump that took place in the machine tool
industry and turned their attention to components for
heavy road vehicles. Many valuable contracts were
obtained for rear axles, steering boxes, and gearboxes.
Other products included air springing for cars, outboard
motors, printing machinery, baking machinery, universal
joints, and patented tie rods.
By 1926, Wolverhampton heavy
vehicle manufacturer Guy Motors had developed a rigid
six-wheeled military truck with drive on both rear
axles. |
This proved to be an excellent
cross-country vehicle for use as an artillery tractor,
mobile workshop, or searchlight generator lorry. Turners
were invited to develop a powered winch for the vehicle,
to haul it out of difficult terrain or recover field
guns etc. The winch was a great success and became
standard equipment for the Guy military trucks, which
were produced in large numbers.
In fact Turners became the leading UK
vehicle winch manufacturer, producing models for all of
the leading vehicle manufacturers and were responsible
for the complete range of powered winches used by the
British Army. |
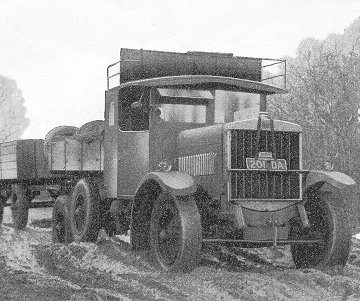
A Guy six-wheeler in operation. |
In 1928 Turners ceased to produce
cars and extended their product range to include
components for the aircraft industry. They began to do
research work for the Ministry of Defence, and in 1934
the Managing Director at the time, Mr. P.B. Dumbell
acquired a licence to manufacture Oleo pneumatic
aircraft landing gear. In 1937 the company's engineers
began to produce their own designs for pneumatic and
hydraulic undercarriages, and at the onset of World War
2 Turners became one of the three companies approved to
design aircraft undercarriages. As a result their
undercarriages were used on Spitfires, Avro Ansen
Trainers, and Stirling, Blenheim, and Lancaster bombers.
Tail wheel units were also produced for the Blenheim,
and Lancaster bombers. |
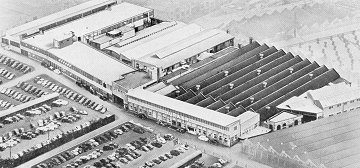
Moorfield Road Works. |
By the mid 1930s the company had
outgrown the Lever Street works and in 1936 part of the
old Sunbeam works at Moorfield Road were acquired for
expansion.
The works has since been
substantially modernised and a two-storey car park was
built on top of the machine shops. |
Large numbers of aircraft
undercarriages were produced between 1939 and 1945, but
as ever the company kept ahead of the game. Turners
realised that after the war there would be little demand
for such products and so diesel engines were developed
for automotive and marine applications. |
In the late
1940s Turners began to manufacture an agricultural
tractor, called ‘The Yeoman of England’, built around
one of their four cylinder diesel engines. The company
also formed Light Delivery Vehicles Limited who operated
from the Lever Street works and produced light delivery
vehicles such as the By-Van and the Tri-Van.
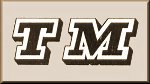 |
|
Read about the light delivery vehicles and
the tractor |
|
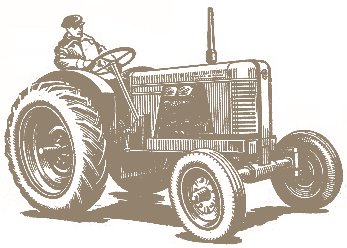
A 'Yeoman of England' agricultural
tractor. |
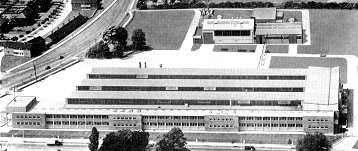
The new factory at Fordhouses. |
In 1951 the company acquired a
factory on the Stafford Road at Fordhouses, which was
expanded and developed to undertake heat-treatment,
grinding and assembly work.
|
In 1961 the neighbouring premises
owned by Spring Washers Limited was acquired and the
buildings were updated and turned into one of the most
modern heat treatment centres in the country. The entire
site now covered 15 acres.
The diesel engines continued to sell well and in 1954 at
the time of the Korean War, the company received a
contract from the Air Ministry to produce parts for the
Rolls Royce Dart engine, and parts for Westland
helicopters, including rotor heads, tail rotors, and
undercarriages. Although the orders for Rolls Royce
engine parts soon came to an end, Turners continued to
supply Westland for many years. |
In 1957 the company branched out
into the hydraulics and pneumatics field with the
formation of Hydraulics & Pneumatics Limited.
The new company manufactured all kinds of hydraulic
equipment including cargo control and handling equipment
for many of the world’s super tankers.
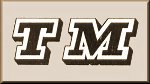 |
Read about Hydraulics
& Pneumatics Limited |
|
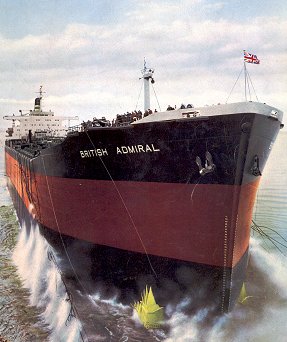
One of the super tankers fitted
with Hydraulics
& Pneumatics equipment. |
Turner’s management began to
think about the large-scale production of gearboxes and
so in 1960 the company acquired gearbox manufacturing
rights from the Clark Equipment Company of America. The
Clark design was initially used in all Turner gearboxes
until the company had designed and developed its own
range. |
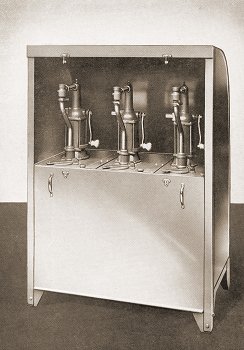
A Baelz triple 25 gallon cabinet. |
Expansion
continued in 1966 when Turners took over Baelz Equipment
of Wolverhampton. The company manufactured oil storage
and dispensing equipment, and lubricating equipment.
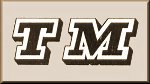 |
Read about Baelz Equipment |
|
A view of Turner's machine
shop showing a battery of vertical automatics in
operation. |
 |
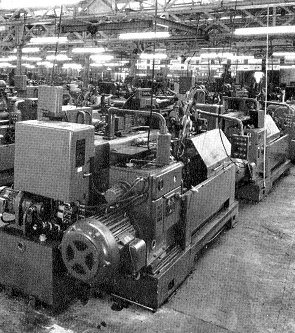 |
Another view of the machine
shop showing some
of the copy lathes. |
A view of part of the heat
treatment plant. |
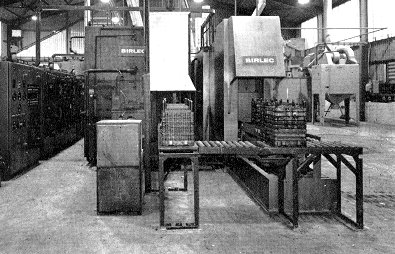 |
In June 1968 the
Turner Manufacturing Company Limited became a public
company. At the time there were 1,700 employees. The
directors were:
P. B. Dumbell |
|
Chairman. |
R. B. Dumbell |
|
Managing Director. |
C. F. Dumbell |
|
Financial Director. |
B. F. Brown. |
|
Commercial Director. |
W. E. Gibbs |
|
Production Director. |
W. M. M. Morrison |
|
Technical Director. |
M. C. Stoddart. |
|
|
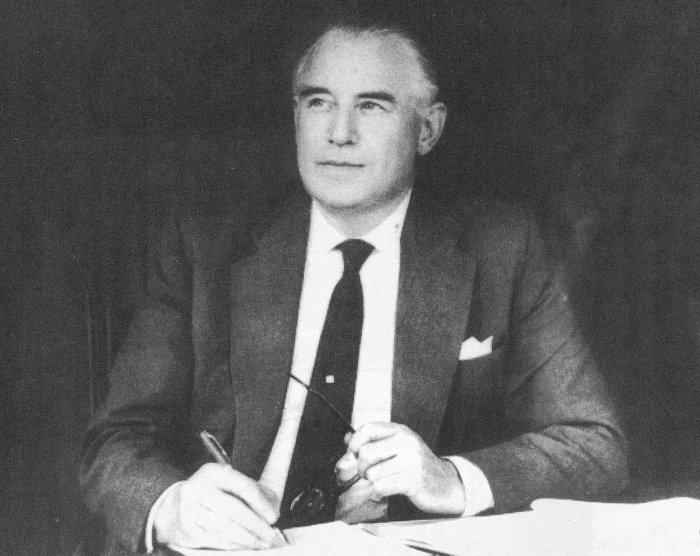
Mr. Philip Dumbell, Company
Chairman.
Philip Dumbell married Marjorie
Sharpe, and they lived at The Gables in Tettenhall.
Marjorie died in 1970, and two years later Philip
married his secretary, Elizabeth Turton. Sadly the
marriage was short-lived. Philip died in 1977.
During the
company’s first year as a public company, sales amounted
to £6,829,000 and the profit after tax was £784,743.
Around 1967 Turners purchased Earby Light Engineers
Limited, a sub-contractor who produced precision
components for the aircraft engine and airframe
industries, and specialised in high precision work
including spark erosion and electro-chemical machining.
The company continued to expand and a new factory was
purchased at Racecourse Road in 1970.
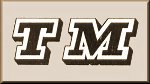 |
View some of Turner's Products |
In 1972 the Dana
Corporation of Toledo, America acquired a 35% holding in
Turners and later took the company over. Turners
suffered greatly during the recession of the 1980s with
many job losses, and the loss of the subsidiary
companies. The Moorfield Road works closed in 1988,
leaving only one surviving factory, at Racecourse Road.
I would like to thank Derek Beddows
for his help in producing this section. |
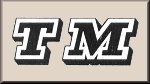 |
Return to
the
Engineering Hall |
|