Mander-Kidd Limited was one of the country’s largest
manufacturers of printing ink. The Heath Town factory had the
most up-to-date equipment of its kind, and produced all kinds of
printing ink for most of the printing processes that were in use
at the time. Inks were produced that were suitable for use with
all kinds of paper and boards, metal foils, and plastic films.
Ink is a complex medium, with exacting requirements. Colour
consistency is essential, across a whole range of colours, and
uniformity, so that the same result is achieved each time. Ink
must not dry in the printing machine if left overnight, but has
to dry in a split second on paper. Some inks are as thick as
putty and others have to flow like milk. |
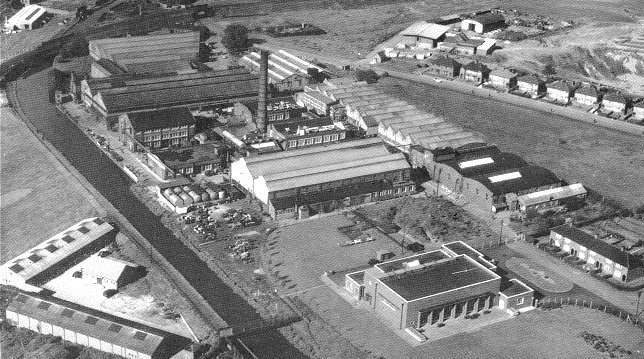
The Heath Town factory. |
Ink also had to keep-up with advances in
technology. New machines, materials and processes were
constantly introduced, so a large amount of investment had to be
put into research and development. Well-equipped and
sophisticated laboratories were essential, along with qualified
and experienced laboratory staff.
Raw materials were imported from many
countries including Africa, Brazil, Canada, Central America,
India, Korea, the Middle East, the Philippines, Scandinavia,
Spain, and the United States. The all important colour pigments
came from Britain’s coal mines. They were derived from the
distillation of coal tar, with the careful addition of
controlled quantities of rare metals such as tungsten and
molybdenum. Other important raw materials were carbon black, a
product of petroleum, and titanium, zinc and lead which were
used to produce white ink. |
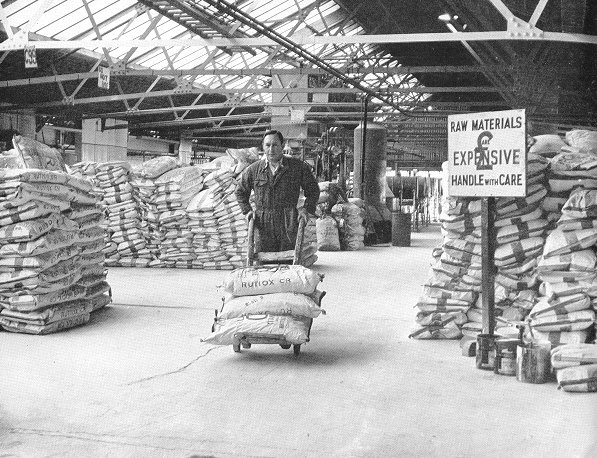
One of the raw material stores. |
Samples of all of the materials were taken on arrival, and
thoroughly examined and tested in the laboratory before being
released to the factory. This was essential to ensure that high
standards of quality and consistency could be maintained.
Careful stock control was also important to make sure that
adequate stocks were available when supplies were interrupted
due to unforeseen circumstances. |
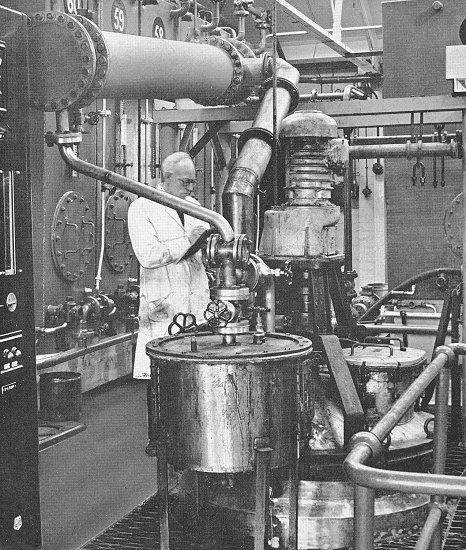
Inspecting one of the varnish pots. |
One of the most important ingredients is varnish, which is
the basis of the ink. It carries the colour, determines the
ink's behaviour in the printing machine, and the quality of the
ink film on the printing surface. It was made in the varnish
plant using the most up-to-date techniques. Manders produced
varnish for over two hundred years, during which time the
process considerably changed.
Originally heated linseed oil or semi-drying vegetable oil
was used with a natural gum such as Congo Copal, which had been
previously treated to render it soluble in the oil. This was
replaced with a range of vegetable and other oils that were
stored in a large 'tank farm'. Quantities of chemically pure
compounds were added to the oil, and the mixture was heated in a
closed vessel, which could hold about two tons of raw
ingredients. A batch would usually be finished in less than 24
hours, during which time the temperature was accurately
monitored. |
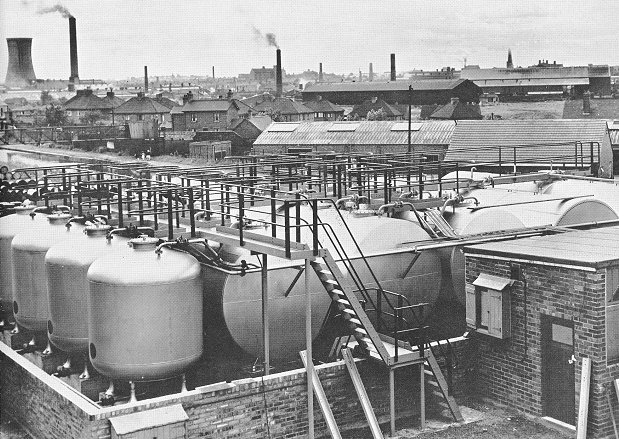
The tank farm where 50,000 gallons of
oil was stored. |
Throughout the process, by-products such as water were
continuously removed, to leave a synthetic varnish with the
precise qualities that were required for the ink. Periodically
samples were taken, and the viscosity measured. When it was
exactly right, the varnish was piped to a set of coolers, and
through a large filter press to the storage tanks. To produce
the ink, pigments were thoroughly blended with the varnish, to
which driers and reducing mediums were added in correct
proportions. The ingredients were then thoroughly mixed in
powerful mixing machines that could each handle half a ton at a
time. The machines occupied a large part of the floor space at
the factory. |
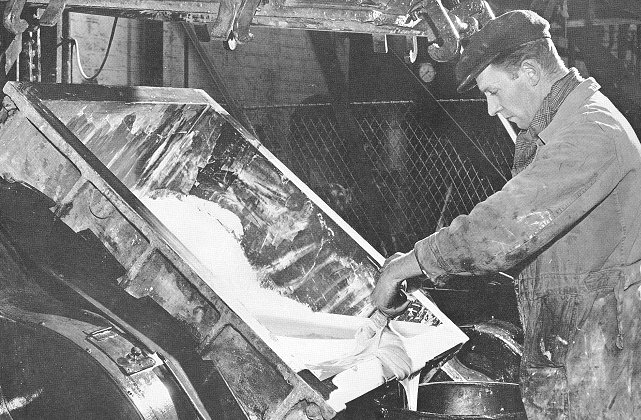
Emptying one of the mixing machines. |
When mixed, the ingredients were taken to the grinding mills
which dispersed the minute pigment particles evenly throughout
the varnish medium. The mills had three water-cooled,
electrically driven, polished steel cylinders that were geared,
so that the second cylinder rotated slightly faster than the
first, and the third cylinder rotated faster again. The degree
of 'nip' between the cylinders was carefully adjusted according
to the kind of ink being made. |
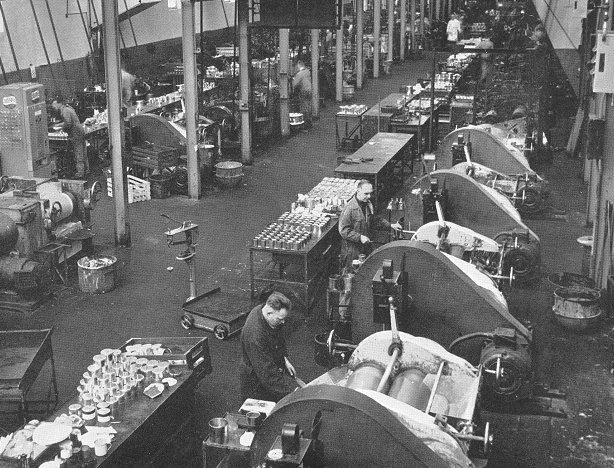
Part of the main mill room showing
some of the three roll mills. |
The operators would pass the ink through the mill for
anything up to eight times depending on the type of pigment, and
the requirements of the formula. A sample would then be taken to
the testing room to be compared with a standard sample. The
properties, including colour and consistency, tackiness and
drying speed were examined by an expert, and when correct, the
batch would be measured into cans, which were sealed and
labelled for despatch. Every can was stamped with a code number
so that the whole history of its manufacture could be traced. |
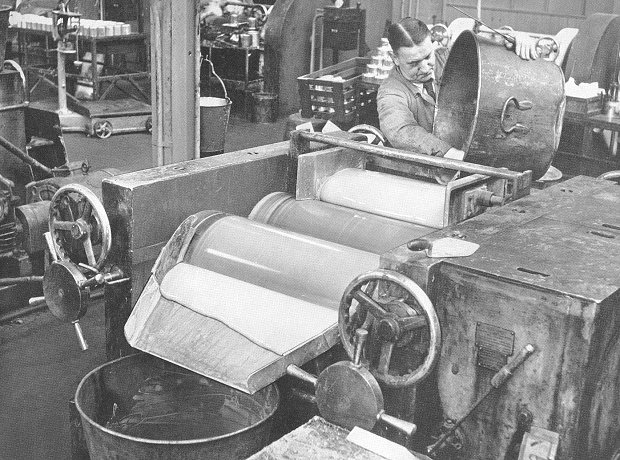
A batch of ink nearing completion on a
Torrance three roll mill. |
The company also produced batches of special
inks that were different in some way to normal inks, and catered
for customer’s unusual requirements. They were often produced
in small quantities from a mixture of standard products,
sometimes with additions, and were ground by hand on mixing
slabs or benches.
Hand mixing a special colour on a slab. |
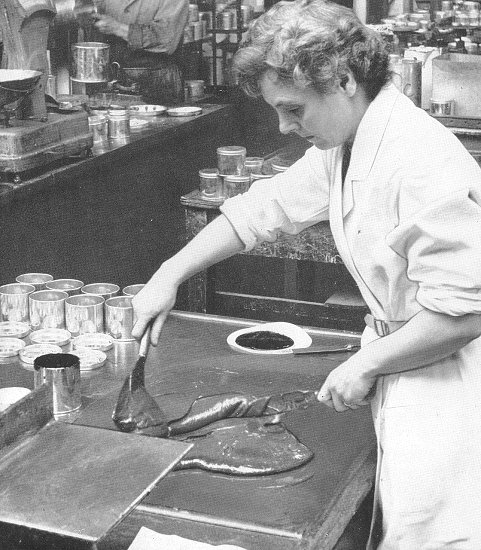 |
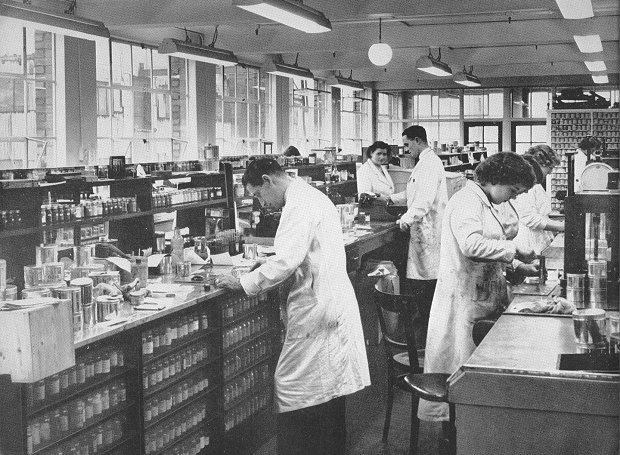
One of the laboratories with some of
the large collection of pigment standards in the foreground. |
The firm’s laboratories were an essential part of ink
manufacture. Every stage of production was carefully monitored
and subjected to stringent physical and chemical tests.
Laboratory staff also prepared formulae for new inks, and looked
after special matchings to customers' orders, and matchings to
paper. The best equipment was used, including extremely accurate
electrically controlled balances, devices for measuring colour
by spectrum analysis, viscometers, miniature grinding mills, and
a great variety of chemical apparatus. |
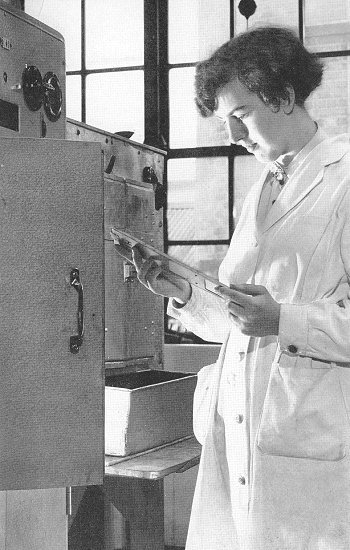 |
There was also a light fastness testing machine (seen on the
left) which could subject sample panels to the equivalent of
several months' exposure to sun and rain in a few hours, and an
automatic machine for determining the printed film's resistance
to abrasion. There were also machines to test every physical
and chemical property of ink so that the result could be
recorded in mathematical terms. |
Testing the viscosity of a new batch
of varnish in a thermostatically controlled bath. |
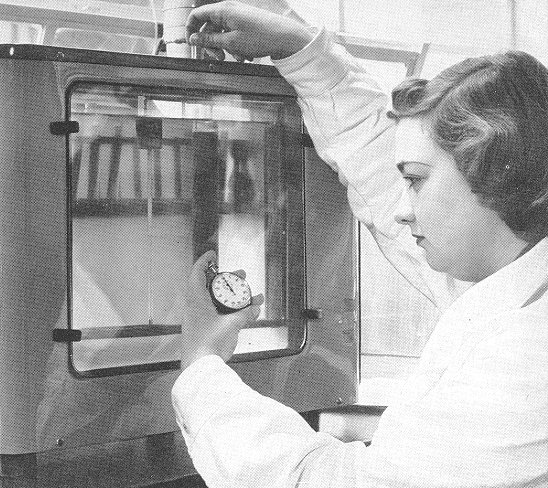 |
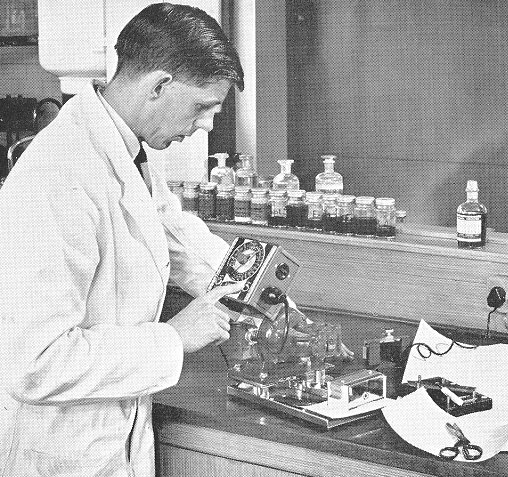 |
A carton ink being tested for abrasion
resistance with a Sutherland rub tester. |
Producing a trial quantity of ink
on a miniature three roll mill. |
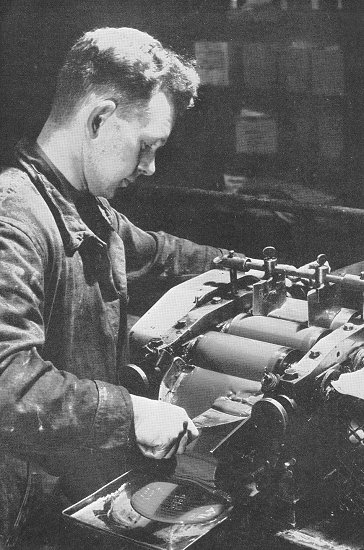 |
A continuous programme of research into possible new
materials and processes was undertaken. New papers and other
printing surfaces were minutely examined, and a close eye was
kept on developments in the printing trade so as to find a way
of meeting future requirements in advance. |
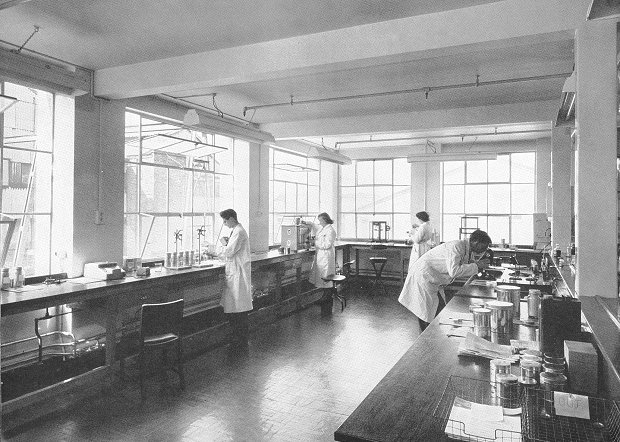
One of the research laboratories. |
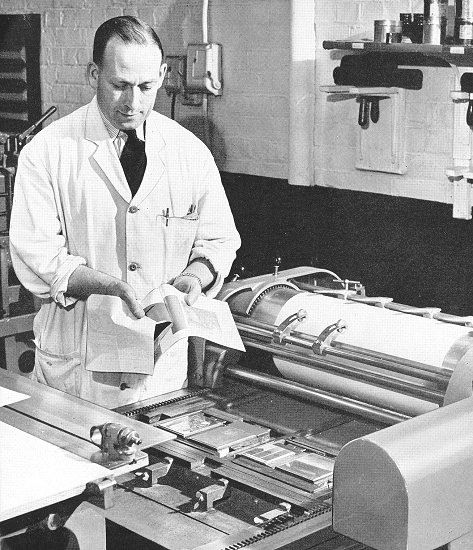 |
The factory also had a printing department,
equipped with a full range of printing machines. The
letterpress section had a flatbed Miehle, Heidelberg and Arab
platens, and a Soldan.
The offset section had an A.T.F. Chief and a Rotaprint, and
the gravure and aniline section had a Chambon.
The machines allowed the operators to test the performance of
inks under normal workshop conditions.
A proofing press in the machine room. |
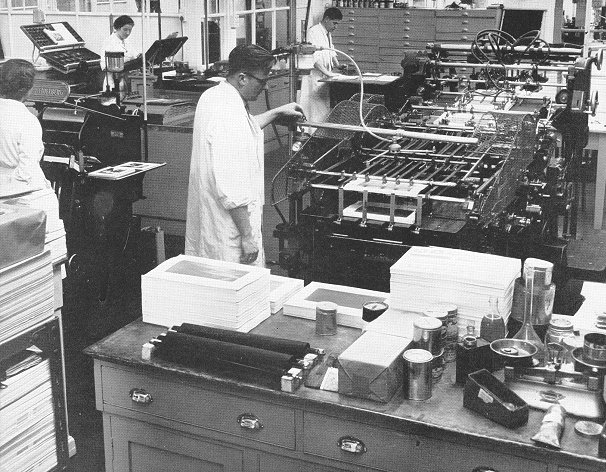
The letterpress section in the
printing department. |
After manufacture, the ink was quickly and safely
distributed to printers. Mander-Kidd was ideally situated in the
centre of the country, and able to service all areas through the
London factory or one of nine branches. All of them carried
large stocks of inks and had their own delivery service. Some of
them were also able to mix special matchings on the spot, and
the London factory had manufacturing and laboratory facilities
to cope with urgent orders. |
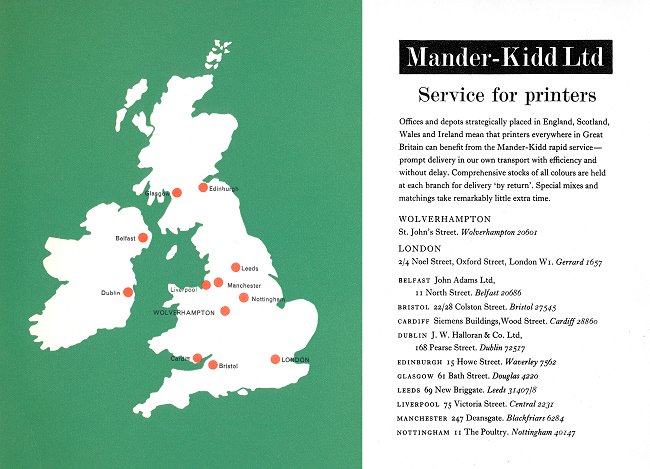
UK factories and branches. |
There were also three factories in South
Africa, one in Rhodesia, another in Australia, and over sixty
agents throughout the world. Mander-Kidd offered a service that
was second to none. It was greatly appreciated by the vast
number of customers who regularly used the products. |
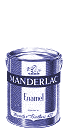 |
|
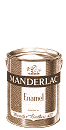 |
|
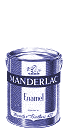 |
Return to
Heath Town |
|
Return to
the contents |
|
Proceed to
George
Cox's Memories |
|