Bayliss, Jones & Bayliss
William Bayliss,
the founder of the firm, was born in 1803 into a
Shropshire family who moved to Priestfield, where he was
born. His father Moses came from Benthall Edge, his
mother came from Horsehay. He worked for Samuel Ferriday
who owned coal mines and an ironworks at Priestfield.
Moses was a blacksmith who had his own blacksmith's shop
and looked after the mine pumping engines. Much of his
work was for the miners, sharpening their picks, shoeing
their horses and repairing hand tools.
William was the
third of eleven children. He disliked school and left as
soon as possible. Before his tenth birthday he was
working seven days a week in one of Samuel Ferriday's
mine pumping engines. Although an easy job, he was left
much to his own devices, and rarely saw anyone else. He
particularly disliked working at night when he had to
walk in the dark, to or from the engine.
|
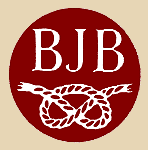 |
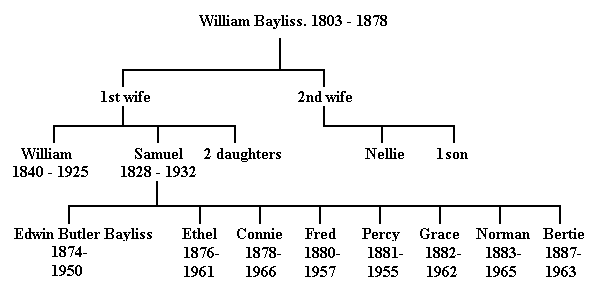
A simplified family tree.
When William was
around eleven years of age his father moved his business
to Monmore Green to look after Mr. Ferriday's engines
there, and William worked on one of the pumping engines
on the site. When he was about fifteen years old he
began working on a winding engine, which meant that he
didn't have to work on Sundays. His father wanted him to
improve himself and so found him a job as a blacksmith.
Work was much harder in the blacksmith's shop, but it
was not so lonely, and much more enjoyable. Around this
time he became a devout Christian which would soon
dominate his life.
William gradually took over his father's business. He
was an efficient lad and when he started keeping records
and introduced "pay on the nail", it excused his dad the
Saturday journey around the public houses trying to get
his mining customers to pay their bills.
|
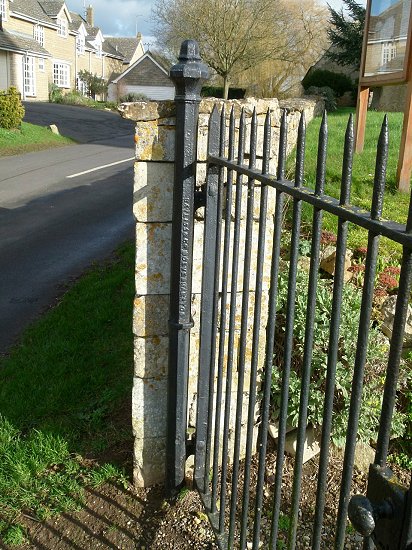 |
This photo, which was taken at
the churchyard at Empingham, Rutland, was kindly sent by
Alan Murray-Rust. It
carries the following lettering:
Bayliss & Co. Wolverhampton.
Could this be an early example
of William Bayliss's work?
If anyone can confirm this,
please
send me an
email.
|
In 1825, at the age of
twenty one, William married one of his Sunday school
teachers. She was a regular member of
the Wesleyan Chapel in John Street, Ettingshall, where he was class leader of the weekly
prayer meetings. They moved into a house in George
Street, Ettingshall and over a period of around twenty
five years had 14 children, but ten of them died young.
The survivors were two daughters, and two sons, William and Samuel,
who later joined the firm.
A few months later his
father suddenly died. William took over the business,
but as well as his work in the blacksmith's shop, he had
to carry out repairs on the mine pumping engines. It was
extremely dangerous work. Many people were killed or
injured in mine shafts as a result of brick or rock
falls. They were dry-bricked, or un-bricked where there
was rock or coal. The shafts were deep with three
rod-operated pumps. The lowest pumped water into a
cistern, the second pumped water from the cistern into a
second cistern, and the third pumped the water to the
surface.
|
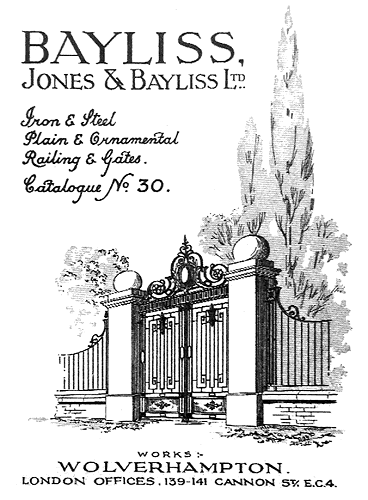 |
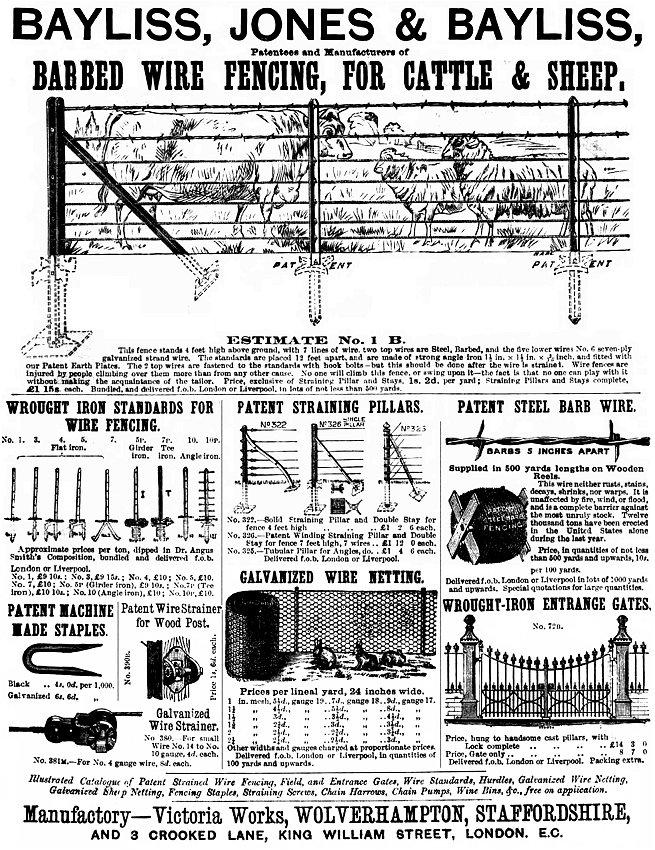
An advert from the British Trade Journal,
1st June, 1882.
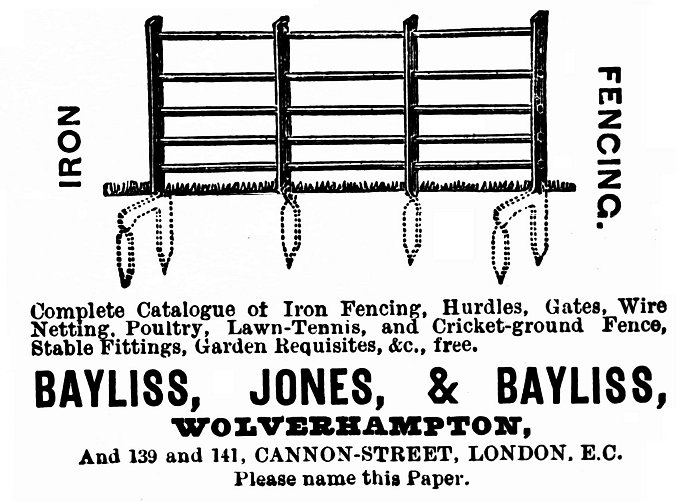
An advert from 1885.
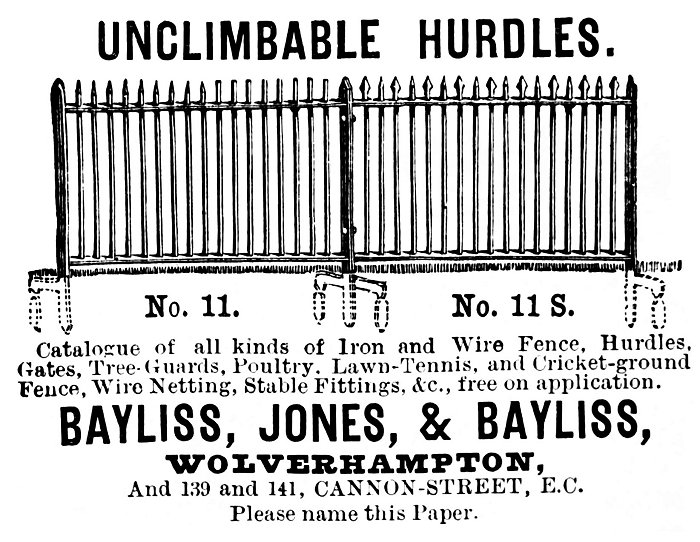
An advert from 1885.
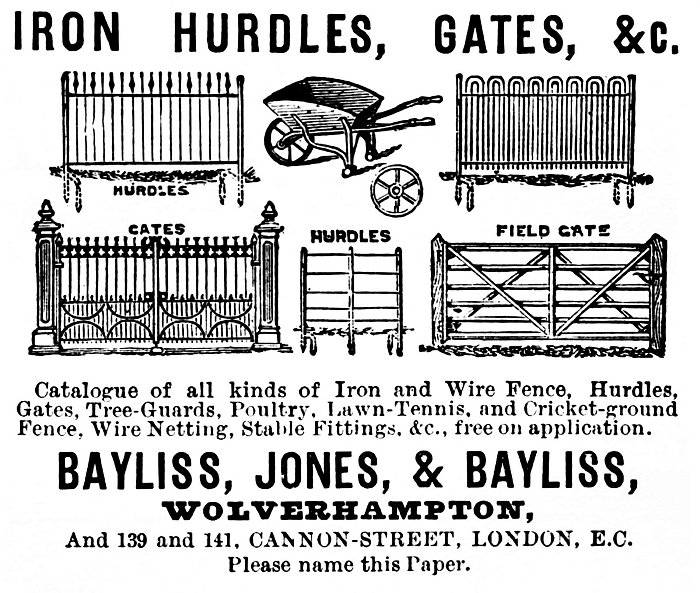
An advert from 1885.
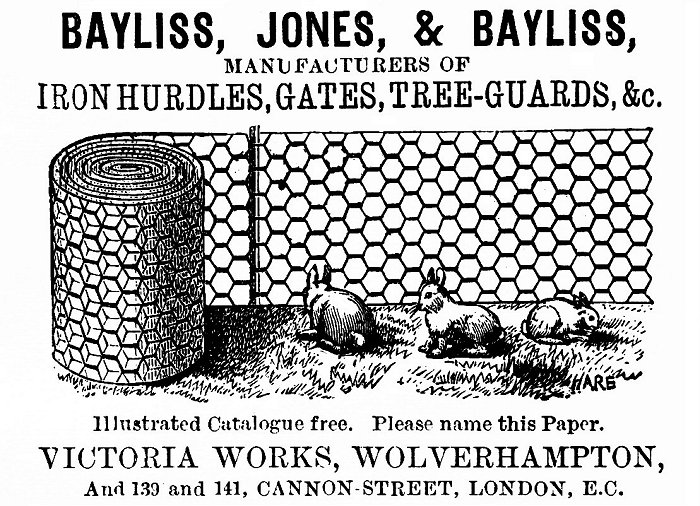
An advert from 1885.

An advert from 1912.
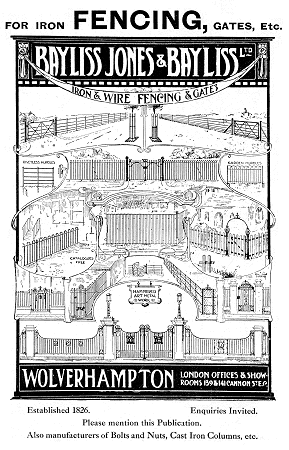
An advert from 1914. |
William saved
hard and bought a large plot of wasteland in Cable
Street, Wolverhampton where he established the Victoria
Works in 1826. He began to produce iron products
including sheep hurdles, railings, gates, stable
fittings, ornamental ironwork and chains for mining and
shipping.
Sadly William's first wife died young. She discovered
a lump in one her breasts, and had a mastectomy.
Although successful, other cancerous growths appeared in
her lungs. A little while after her death he married
again. His second wife had previously married and had a
daughter from her first marriage. William entered into a
business partnership, but was having health problems
caused by the smoke and sulphurous fumes that were often
in the air at Ettingshall. Because of his chest
complaint he was unable to cope at work, and felt that
his partners were taking advantage of him. After a
disagreement in 1853 the partnership was dissolved. |
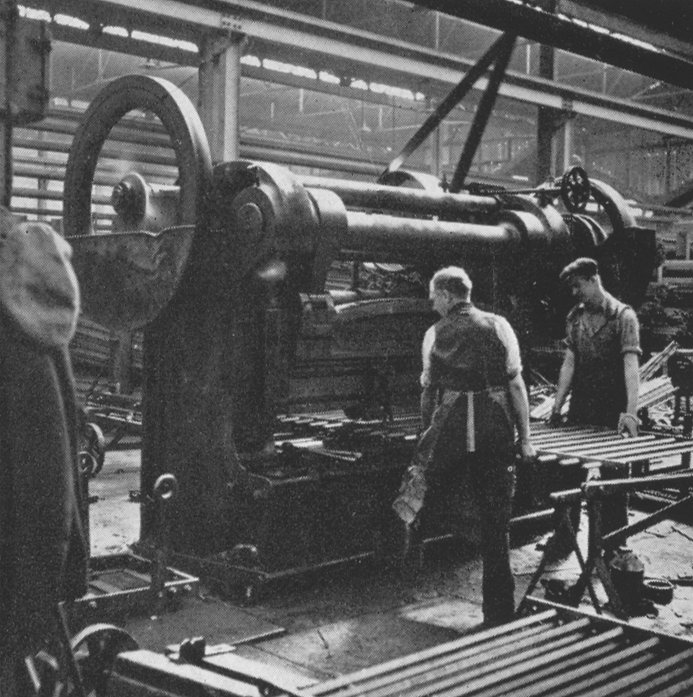
Making railings in the machine
shop. |
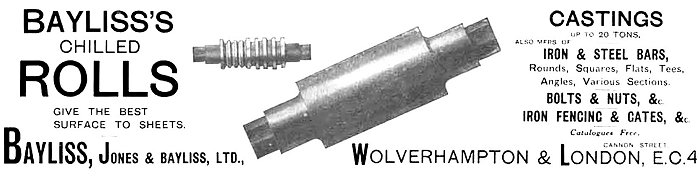
An advert from 1924.
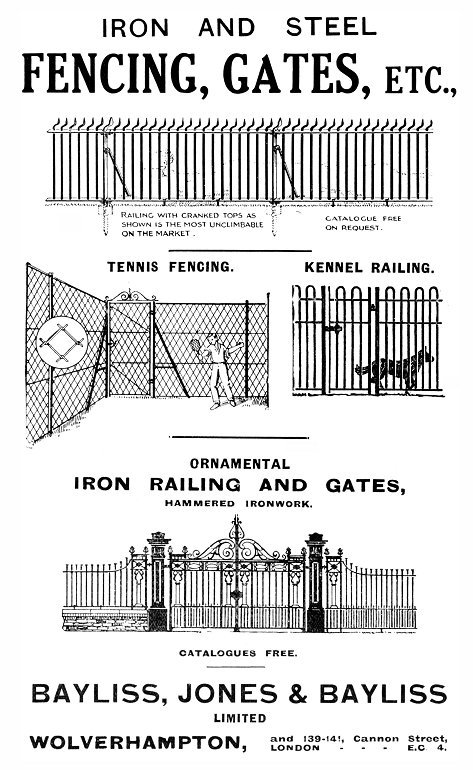
An advert from 1929. |
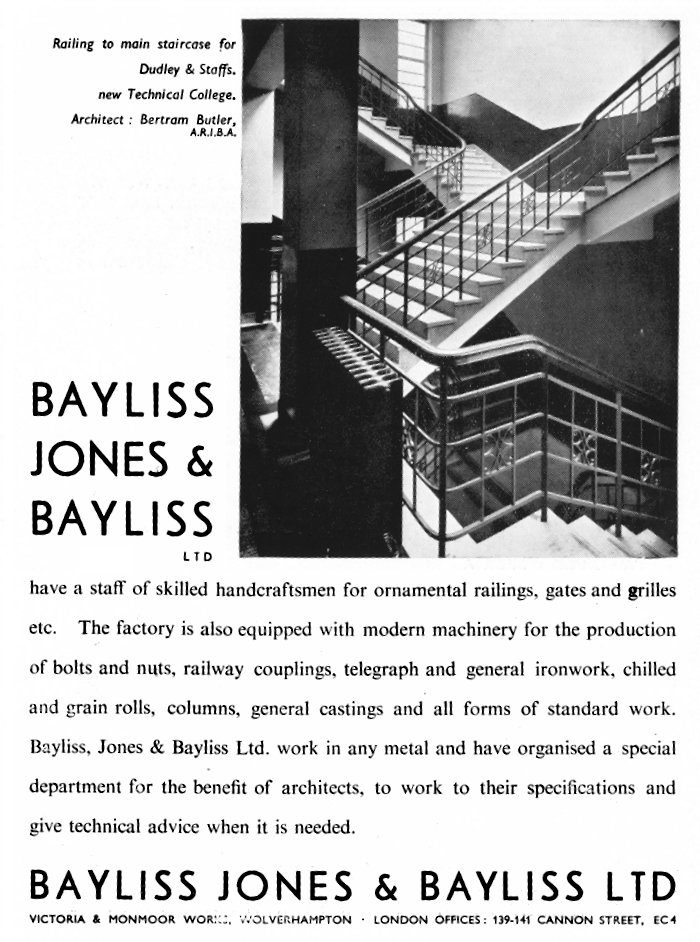
An advert from the 1930s. |
Eventually his
brother Moses, who had been a nut and bolt maker at
Providence Works, Darlaston, joined him in the venture.
The two firms were amalgamated as W. & M. Bayliss of
Victoria Works, Monmoor Green and Providence Works,
Darlaston, with a London office at 43 Fish Street Hill,
Eastcheap. In 1859 they were joined by Edwin Jones, an
iron trader from South Wales who had previously married
William's daughter, Jane. The partnership then became
Bayliss, Jones and Bayliss.
|
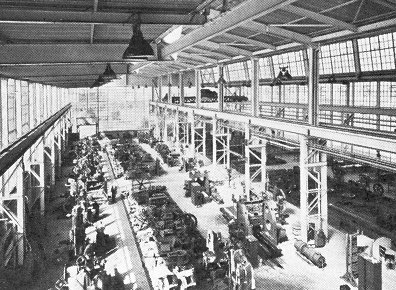
The new machine shop in 1949. |
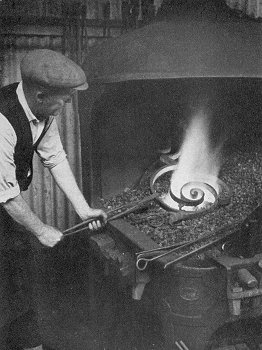
Traditional methods still in use
in 1953. |
The company were very successful
and Mr Jones became resident in London, running an
office at 84 Cannon Street E.C.
It seems that Moses went to America
to introduce the rolling of corrugated sheet iron, but
this can't be verified. However, Moses was the father of
Wolverhampton born Sir William Maddock Bayliss, who
later became a distinguished physiologist. In 1902, at
University College London, with E.H. Starling, he
discovered the hormone secretin and established the role
of hormones. Secretin is used today as an intervention
for autism.
Sir William was also a
non-executive director of Bayliss, Jones & Bayliss.
In 1873 a Wolverhampton Trade
Directory lists William, the founding member of the
firm, as living in Oaks Crescent. |
William moved
there to get away from the smoke and fumes in Monmore Green.
He had been
advised to “move to the fresher atmosphere of
Wolverhampton”. Oaks Crescent was on the edge of a rural
district. His journal expresses his pleasure at the
blossoming trees, the clean air and the singing of the
birds in the garden of his new home. A few years later,
his doctors advised him to retire to the south. The
family initially moved to Clifton, but because of the
smoke and fog there they moved again to Torquay, where
William lived until his death in 1878.
|
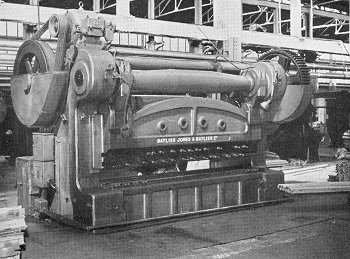
One of the company's large
machines. |
|
|
View the fine example
of Bayliss, Jones & Bayliss fencing and gates that
are in Grangewood Park, South Norwood, London. |
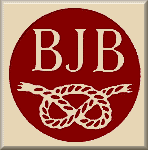 |
|
|
The following article appeared in 'The Engineer' on
1st October, 1880: |
Bayliss, Jones and Bayliss –
Rivetless Hurdles
Messrs. Bayliss, Jones and
Bayliss of Wolverhampton, and King William
Street, EC, have recently brought out an
improvement in iron hurdles, gates, etc. which
consists of securely fastening the ends of the
horizontal bars to the uprights without
riveting. |
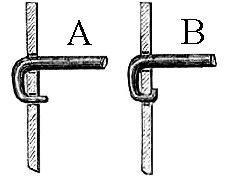 |
It is shown by the annexed
engravings.
A
shows the horizontal bar threaded through the
upright, ready for clenching; and drawing
B the horizontal bar
after it has been clenched to the upright, from
which it is impossible to move without cutting
the horizontal and upright to pieces.
Hurdles made upon this
principle are found to be very strong and rigid. |
The mode of manufacture moreover, demands
the employment of first-class iron, as none
other will stand the test of clenching the ends
at the short bend. The hurdles will consequently
bear the rough usage to which they are very
often necessarily exposed. |
|
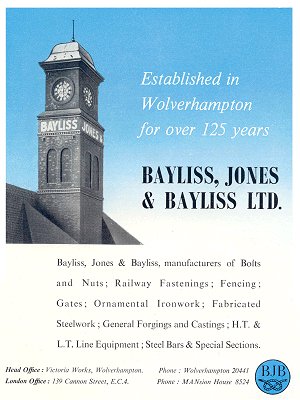
An advert from 1953. |
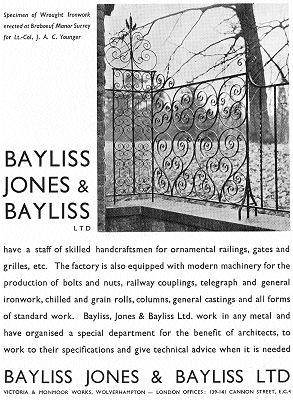
An advert from 1935. |
An article from The
Engineer. 30th October, 1885.
The Eureka Lock Nut
The lock nut
illustrated in the accompanying engravings
is now being brought out by the patentees
and manufacturers, Messrs. Bayliss, Jones,
and Bayliss, of Wolverhampton and Cannon
Street. A simple and effective locking
arrangement for such work as fishing rails
is a great desideratum.
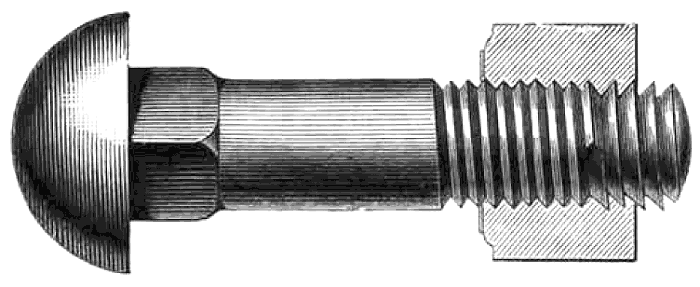
Many forms
have been brought out, but none
so simple as the Eureka, which
is made in the ordinary way,
with the exception that on the
outside surface of it, a small
pyramidical prominence is left,
as seen in Fig. 1. After
screwing the nut, this
prominence is compressed and the
outside surface made level, but
in the act of compressing it,
three threads of the nut are
deformed where the prominence
has been pressed into the nut,
as shown in Fig. 2. |
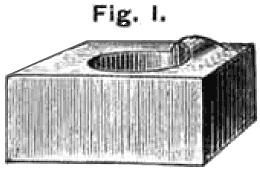 |
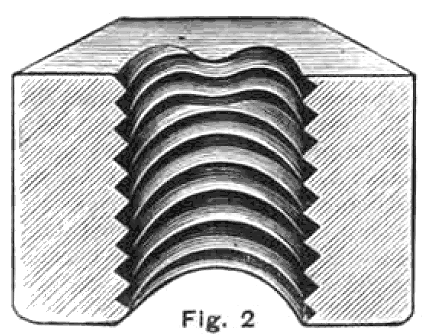 |
The nut will run easily on
the male screw or bolt until the
deformed or irregular threads
are reached in the nut, when the
spanner is necessary, and with
its aid the nut, while passing
along the bolt, deforms the
thread, as seen in Fig. 3. so
that at the point where the
operation of screwing
terminates, the threads of the
bolt accommodate their shape to
the deviation in the three
threads of the nut in such a way
that it is impossible for the
bolt or nut to be moved either
way without the aid of a spanner
and considerable force. |
The makers have had these
nuts on a large and powerful
multiple press for nine months
without requiring to be touched,
whereas previously they had used
other lock nuts, which, owing to
the continual vibration of the
machine, needed constant
supervision and daily
tightening. |
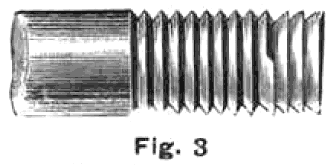 |
They claim several
advantages as possessed by this nut,
including simplicity, security, cheapness,
that it will not move even if the bolt
becomes elongated in work, and that it can
be used several times. They make them in
iron and in steel, but they specially
commend mild steel bolts and nuts. |
|
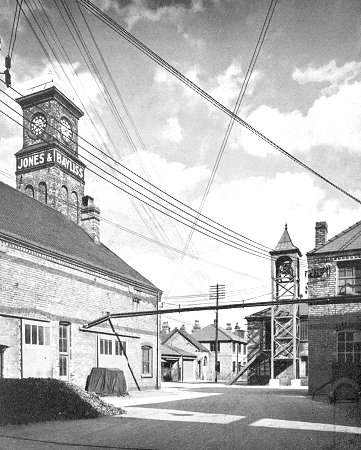
Victoria Works yard and the old clock tower.
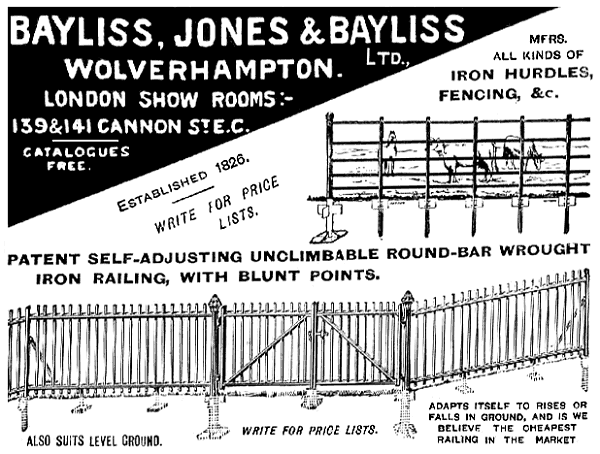
An advert from 1901.
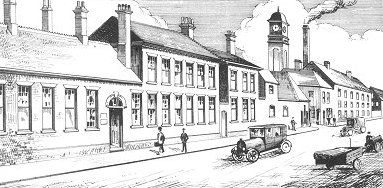
Cable Street. From the 1928
catalogue. |
By this time the company produced large numbers of
rails, fish plates,
chair spikes, fastenings and nuts, for the railways, and
nuts & bolts, and all kinds of iron work, from massive
cables and anchors to half-inch chains and small screws. |
His son William, a quiet and
retiring sort of man, who was at home in the office,
lived at The Firs, Merridale Road.
Samuel, his brother, was more
active and worked in the pattern shop of the foundry.
William would later become chairman and be succeeded by
Samuel in 1925. |
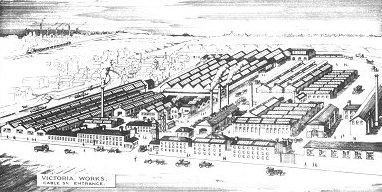
Victoria Works. From the 1928
catalogue. |
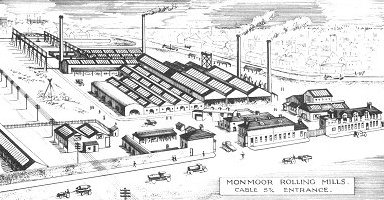
Monmoor Rolling Mills. From the
1928 catalogue. |
In 1896 the company purchased the
Monmoor Ironworks on the other side of Cable Street,
which included rolling mills and puddling furnaces. The
iron works were founded by Mr. E.T. Wright and Mr. David
North to produce high quality iron plates and sheets
using the 'Monmoor Works' brand name. From the late
1850s they were managed by George Adams, who founded the
Mars Iron Works. |
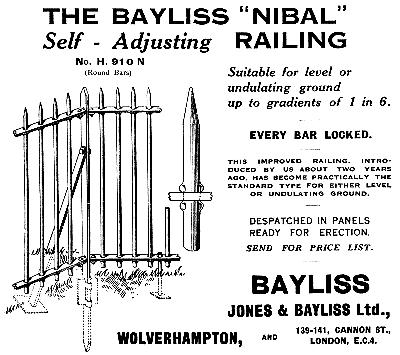
An advert from the GWR Magazine, July 1932.
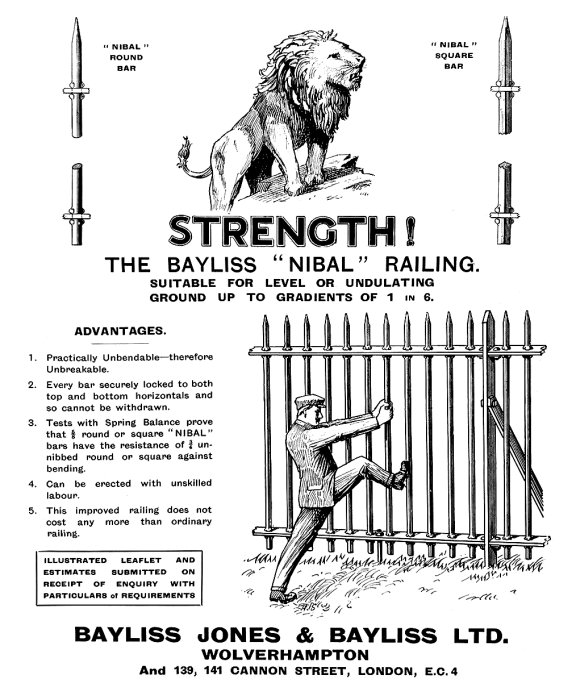
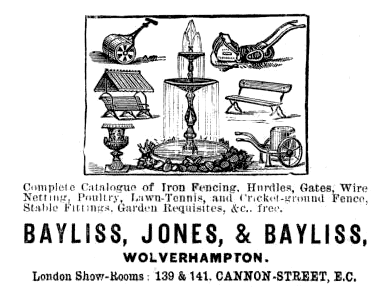 |
The company produced a wide range
of products for use in the garden, in sports grounds, and on
the farm, as can be seen from the advert opposite.
Courtesy of Brian Shaw. |
A bench-end that was cast in the
company's foundry. Courtesy
of Brian Shaw. |
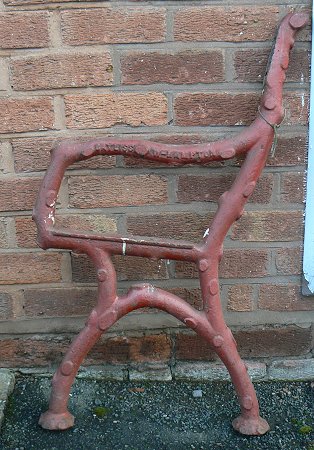 |
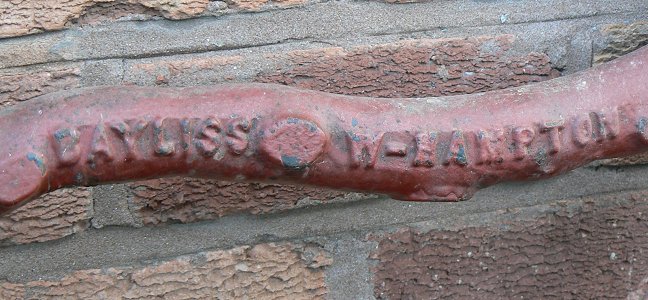
A close-up view of the maker's name on the
bench-end. Courtesy of Brian Shaw.
By the early 1870s Mr. David
North retired after accumulating a large fortune, and
E. T. Wright continued to run the business alone.
It is believed that George Adams
still continued to manage the works as well as running
his own nearby iron works.
In 1901 the company was floated on
the Stock Exchange, but in the early 1920s sales fell
and problems followed. Sales to the railway companies
were the worst affected, although the fencing side of
the business suffered as well.
|
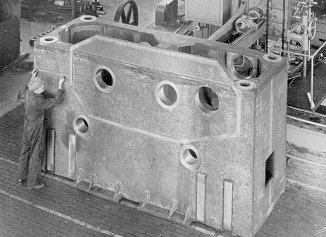
A typical large fabrication made
at the works. |
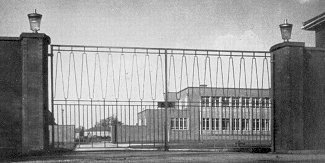
Gates made at the
works for the Territorial Association
Headquarters in Wolverhampton. |
|
The G.K.N. company history
reports the rumour that "William Bayliss, the then
chairman and son of the founder, had diverted capital
from the business into a country estate and had
speculated unsuccessfully on the Birmingham Stock
Exchange, drawing the company in to debt". |
Around 1922
Thomas Swift Peacock, representing the G.K.N. Group of
Companies, negotiated the purchase of Bayliss, Jones and
Bayliss. Peacock was in charge of the group’s Atlas
Works in Darlaston. The G.K.N. Board had given him full
control of the nut and bolt and railway fastening
departments of the Midlands.
Though a subsidiary of G.K.N. from
1922, the company kept its own name and the Bayliss
family continued to provide its management. It is
generally understood that Mr. Jones, who was still in
control of the London offices, forced the issue by
declaring his willingness to sell his portion of shares
to G.K.N. Mr Jones' son Edwin, his son-in-law, Sir
Murray Hyslop and finally his grandson Roy Hyslop,
followed him in managing the London office and
showrooms, which had expanded to 139-141 Cannon Street
by 1938. |
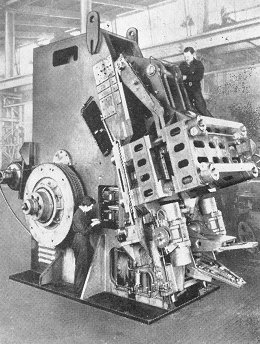
A special purpose BJB swaging
machine. |
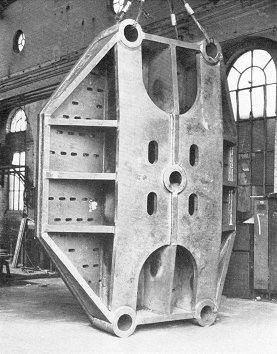
A 13ft. by 10ft. 6ins. press head
constructed at the works in the late 1950s. |
Under Thomas
Peacock, in 1927 and 1928, a new screw rolling shop
opened, the bolt works were reorganised to make
production more efficient and a new mill for the
conversion of billet into bar, opened at Monmoor Works.
The company
seems to have concentrated more on the fencing, railing
and general ornamental ironwork side. In the great
slump of 1929-30 they were hit hard but recovered
strongly from the mid 1930s, which were the company’s
most successful years.
Samuel Bayliss
died in 1932. His sons, P.S. and F.W. Bayliss, joined
the board in 1921 and 1925 respectively, and they became
the joint managing directors in 1928. |
The company
continued to produce high quality ornamental ironwork
such as gates, fences, balustrading, railings, and tree
guards, and became well known for its products.
A large
proportion of the work at this time was for county
councils, carrying out their 'improvements' of
substituting railings for hedges. Demand for
balustrading to span the many new bridges extending over
Britain's motorways also kept the firm busy.
|

The Forging Shop built in the late
1950s. |
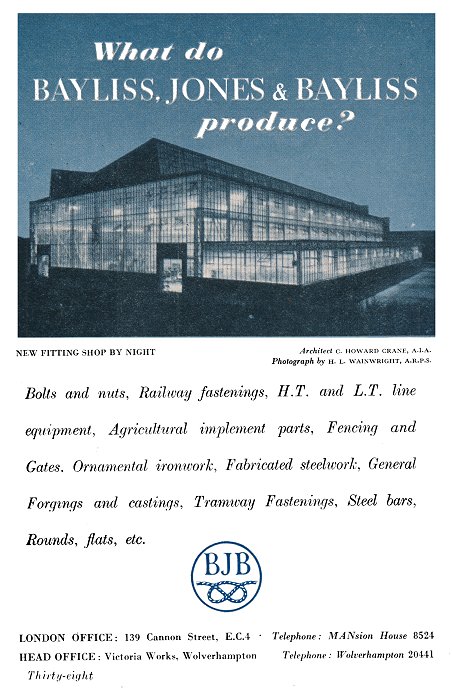
An advert from 1948. |
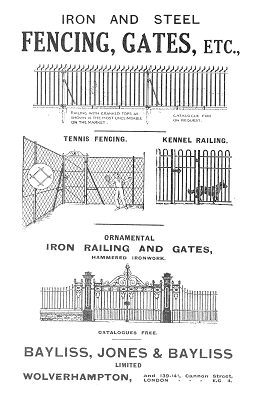
An advert from 1927. |
The products
which the 1953 Wolverhampton Official Handbook mentions
include: plain and ornamental wrought iron
fencing; for railways - black bolts and nuts, screw
spikes, chair bolts, fishbolts and other fastenings;
equipment for overhead telegraph and telephone lines;
fabricated steelwork; general forgings;
agricultural equipment - tractor toolbars, heavy tractor
cultivators, plough beams and brackets, hay rake frames,
etc.; and a recently created department for the welded
steel fabrication of machinery frames, bed-plates, mill
plant, constructional steelwork, agricultural
implements, containers, stillages, hoppers and guards.
The company's
steel rolling mills, with a capacity of 1,000 tons per
week, were kept busy, as orders for miles of railings at
a time were not uncommon. The amount of metal being used
in the works must have been enormous. The modern
galvanising shop had a capacity of 350 tons per week and
was not only used for the company's own products, but
also did outside work. |
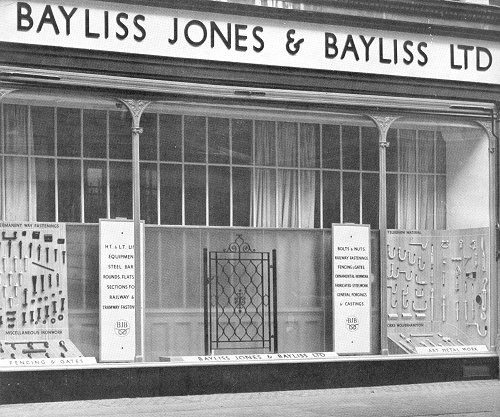
The London office and showroom at 139 Cannon
Street.
By the mid 1950s the company employed around 1,500
people, many of whom had completed 30, 40, 50, or even
60 years service at the works. There were tennis courts,
a bowling green, a netball court, a sports ground,
football and hockey pitches, a cricket ground, and a
children's playground, complete with swings,
roundabouts, and a paddling pool. The Managing
Director at the time was Mr. Roy M. Hyslop, the great
grandson of Mr. Jones, one of the company's founders. |
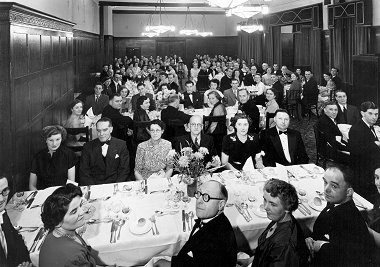
A company dinner
at the Victoria Hotel, in November 1952.
Courtesy of Nina McCarthy. |
|
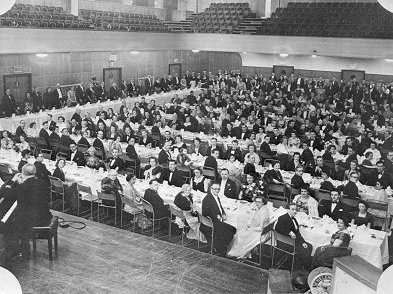
Employees were out
in force at the Civic Hall, to celebrate a
colleague's wedding. 27th March, 1952.
Courtesy of Nina McCarthy. |
|
At this time the
company had a wide variety of customers, including local
authorities, architects, power stations, the Admiralty,
the war Office, the Ministry of Works, the Air Ministry,
and private companies.
The company
produced rail fastenings for British Rail and designed
various types of fasteners, mostly resilient fastenings
for long welded rails. In addition to their standard
lines of railings and gates, they also made one-off
pieces to the designs of the individual customer, or
very often, his or her architect.
|
The canteen could provide hot meals for up to 400
people.
It had a polished wood block floor to enable the
dining area to be quickly converted into a dance floor
for evening events. |
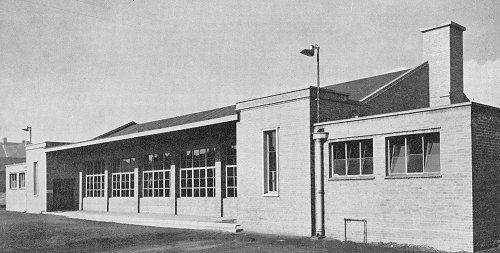
The canteen. |
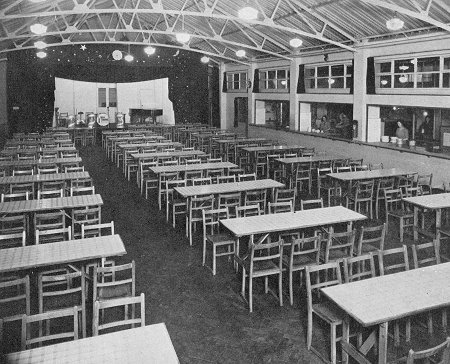
The dining room. |
The dining room had a fully equipped stage so
that all kinds of events could be held there. The
serving hatches can be seen along the right-hand wall.
|
A corner of the large kitchen. |
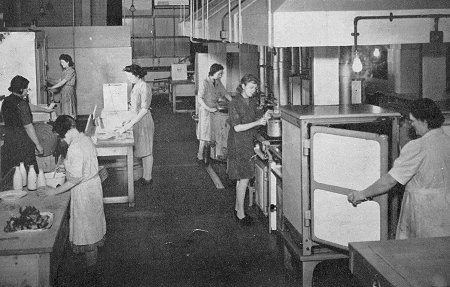 |
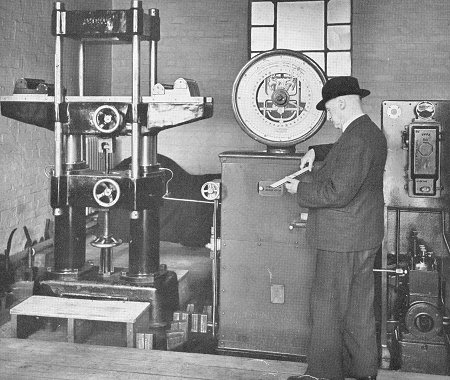 |
Part of the Test House for
tensile, Brinell, and Izod tests. |
Part of the tool room that
supplied precision tools and forging dies. |
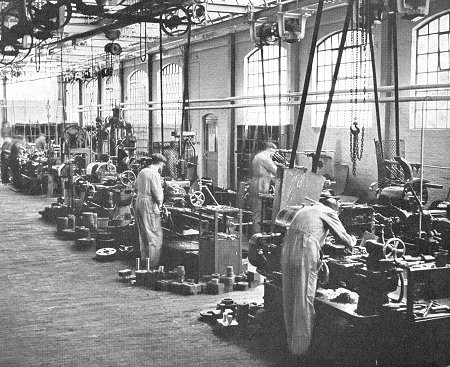 |
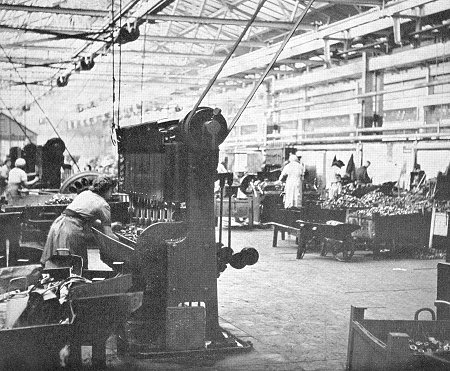 |
A corner of the Screw Shop
where nuts and bolts were finished after forging. |
Part of the Bolt and Screw
Spike Forging Shop. |
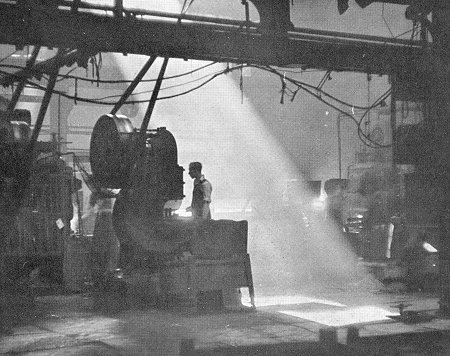 |
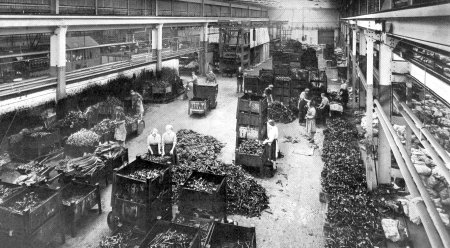 |
The Inspection,
Packing and Despatching Warehouse from where goods were
sent by road, rail and canal. |
Another view of
the Inspection, Packing and Despatching Warehouse. |
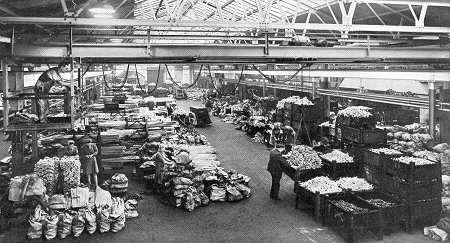 |
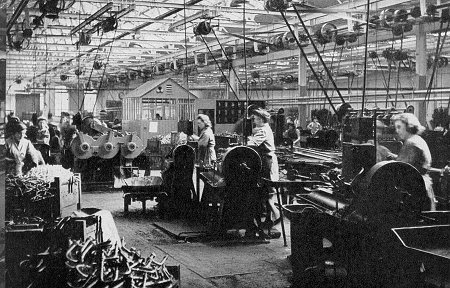 |
The Production
Machine Shop for the company's electrical overhead
transmission line equipment. |
A horizontal
forging machine producing parts for the electrical
overhead transmission line equipment. |
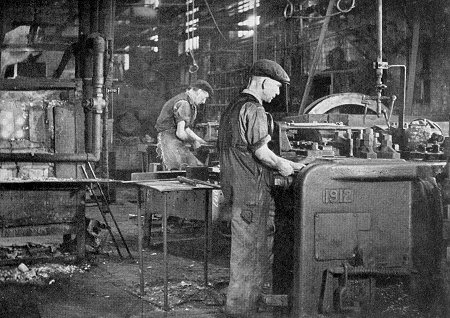 |
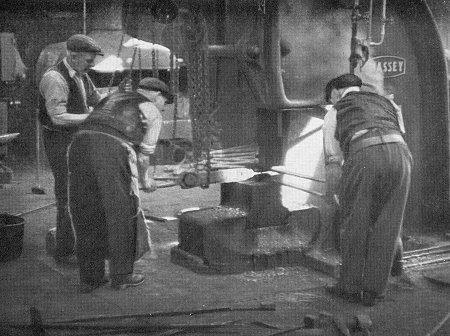 |
Working on one of the Massey
Hammers in the Smithy. |
Another of the Massey Hammers
in the Smithy. |
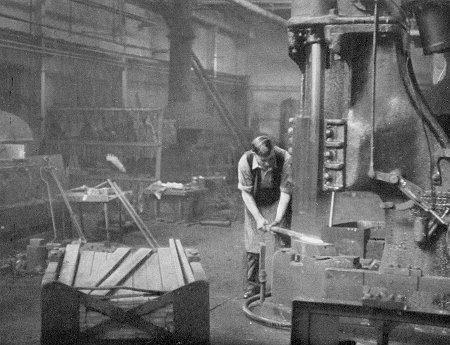 |
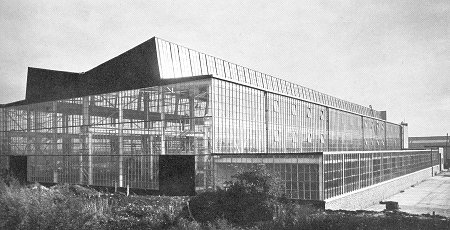 |
The new Machine Shop. |
The new Machine Shop at night. |
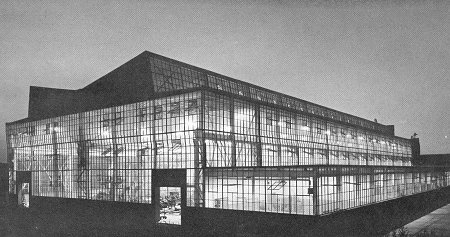 |
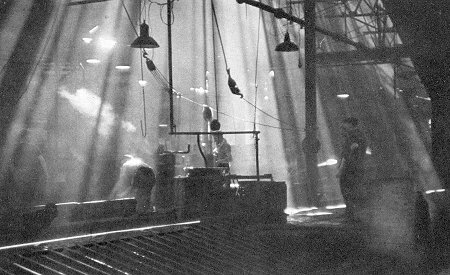 |
Number 3 Rolling Mill. |
The gravity, semi-mechanical
cooling bed for the rolling mill. |
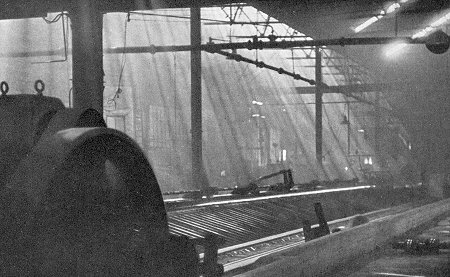 |
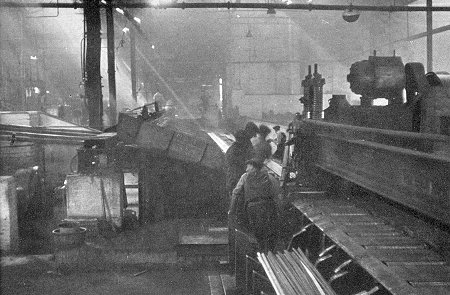 |
The cutting machine that could
cut twelve ⅞ inch diameter
bars in one operation. |
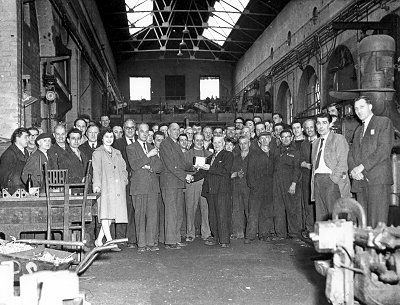
A presentation in the works. Courtesy of Nina
McCarthy.
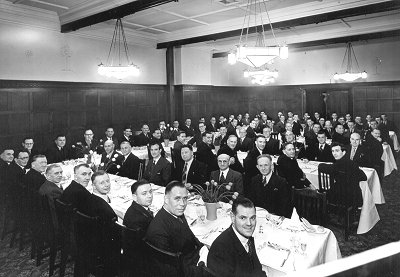
The foreman's dinner at the
Victoria Hotel, May 1951. Courtesy
of Nina McCarthy. |
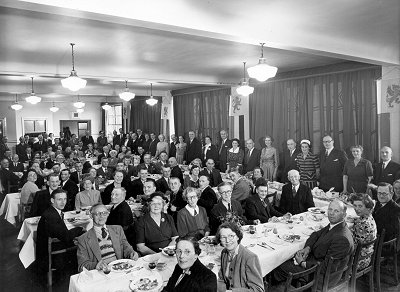
Long service awards, July 1953. Courtesy
of Nina McCarthy.
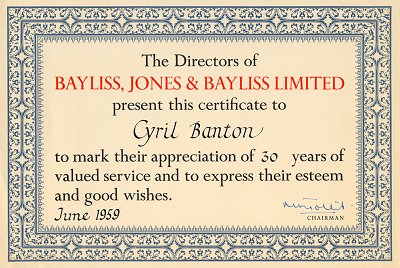
Cyril Banton's long service
award. Courtesy of his daughter, Nina McCarthy. |
|
|
View some of the
forgings made by the company |
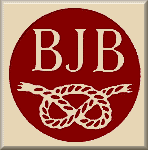 |
|
|
|
|
View some of the
electrical overhead transmission line equipment
made by the company |
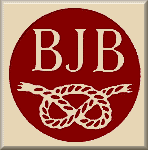 |
|
|
From 1968
exciting times lay ahead when the factory was
reorganised, and much of the plant and buildings
were brought up-to-date. Large sums of money were
invested in the site, which became known as GKN
Machinery Limited. The new company was formed
following the merger of several GKN companies,
including Bayliss, Jones & Bayliss Limited,
and Peco Machinery Limited,
The 1,450
skilled workforce became engaged in the design,
development and manufacture of a wide range of new
engineering products. Many of the company's
traditional products were still produced, such as
fencing and heavy machinery, and the new company was
divided into four divisions. |
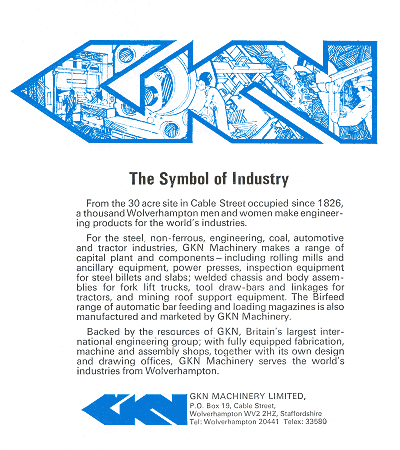
An advert from 1971. |
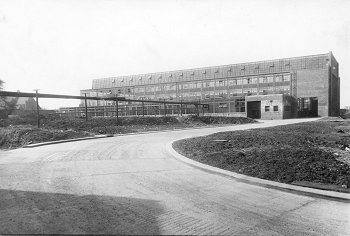
The Metal Forming Plant building
on the Monmoor Works site. Courtesy of Nina McCarthy. |
|
The Metal Forming Plant
Division (MFP) manufactured rolling mills and
ancillary equipment under licence from Moeller &
Neumann, G.M.B.H. West Germany.
Products included steelworks
plant, billet inspection machinery, special purpose
machine tools, steel fabrications up to 100 tons,
and general engineering projects. |
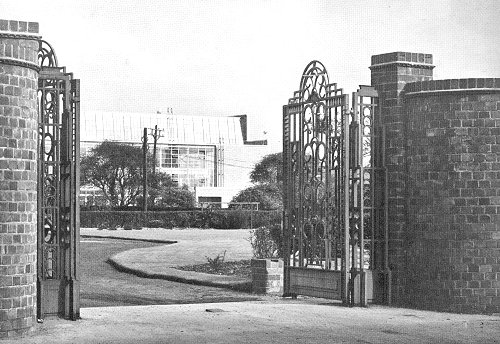
The entrance to the canteen and grounds
with the new machine shop in the background. 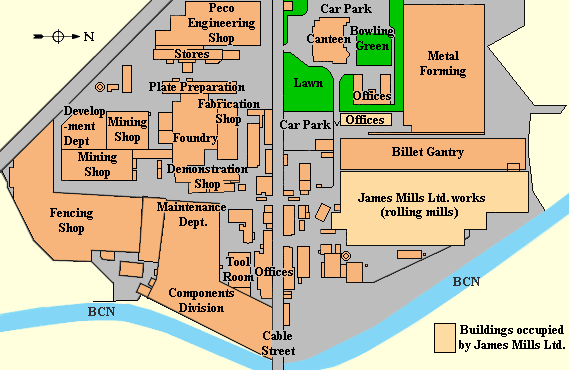
A map showing the layout of GKN Machinery
Limited.
The Peco Division produced Peco
injection moulding machines for thermoplastic,
thermosets, and rubber compounds, extrusion machinery
for thermoplastics, and spark erosion machines for
cutting dies and press tools. A machine demonstration
area was built at Cable Street along with a
comprehensively equipped machine development department,
where complete plastics production facilities could be
designed and then manufactured for customers anywhere in
the world. |
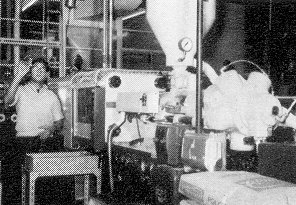
A Peco 25 MR injection moulding
machine. |
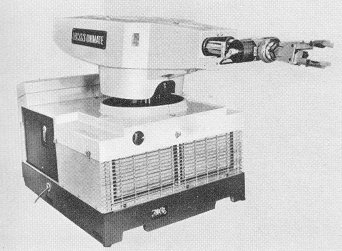
A GKN 'Unimate' industrial robot. |
The Unimation Division produced GKN 'Unimate'
universal automation equipment, and programme control
systems for capstan lathes and automation. |
The Components Division produced Bayliss, Jones &
Bayliss motorway and bridge parapet railing, fencing and
gates, and mining support equipment. Early contracts
for GKN Machinery included a 235 ton double-side
trimming shear, capable of trimming plates from
¼ inch to 1½ inch
thickness, and the world's most advanced heavy plate
mill, the biggest of its kind in the country. It could
deliver up to 8,000 tons of standard quality steel plate
per week. |
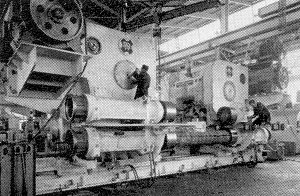
A double side-trimming shear under
construction. |
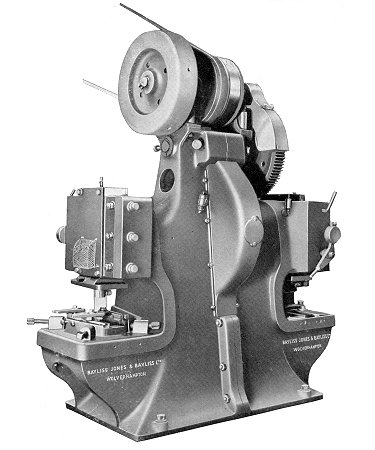 |
A Bayliss, Jones & Bayliss
double ended press. |
A Bayliss, Jones & Bayliss
multiple punching and shearing machine. |
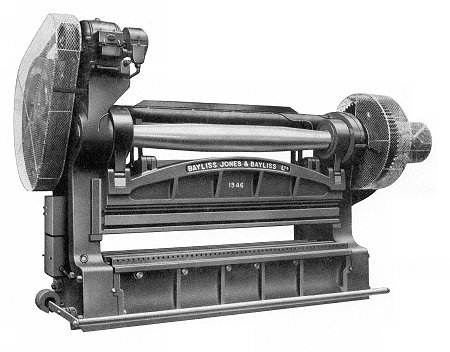 |
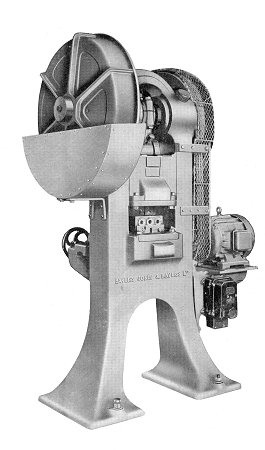 |
A Bayliss, Jones & Bayliss bar
cropping machine. |
A Bayliss, Jones & Bayliss
rolling and straightening machine. |
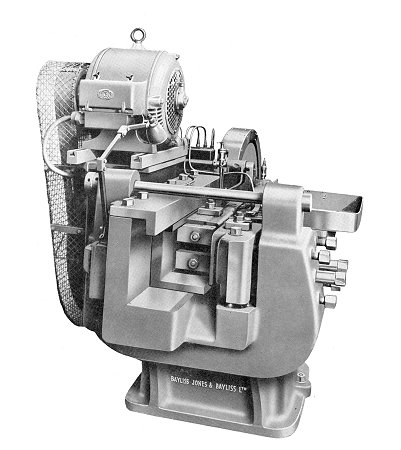 |
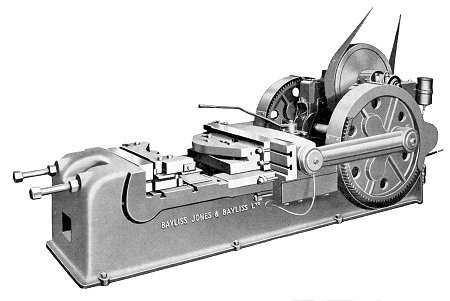 |
A Bayliss, Jones & Bayliss
horizontal bending and forming machine. |
A Bayliss, Jones & Bayliss
single end press. |
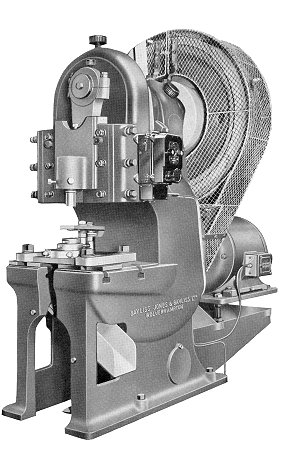 |
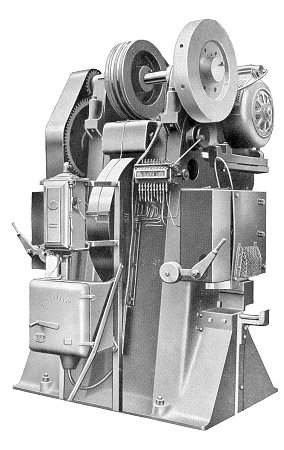 |
A Bayliss, Jones & Bayliss
billet and bar cropping machine. |
A Bayliss, Jones & Bayliss
roll turning lathe. |
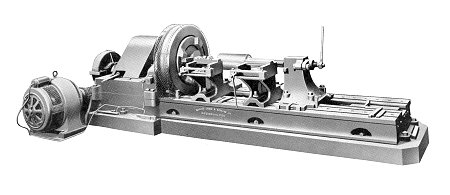 |
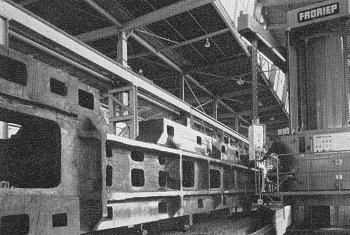
Machining a 36ft.
long, 40 ton casting in the Heavy
Engineering Department. |
|
Under a £1m. improvement scheme a completely new
assembly bay, 75ft. wide was constructed on one side of
the main workshop. It had several cranes installed to
handle loads of up to 100 tons, with a maximum lifting
height of 45ft. The main workshop was also extended to a
length of 425ft.to increase the internal area to 65,000
square ft.
Many large new machine tools were installed, some
featuring a digital readout, which was new technology in
the late 1960s. |
The heavy fabrication department had facilities for
submerged arc and CO2 automatic and
semi-automatic welding. Other facilities included
profile and straight line cutting up to any size of
plate, and plate thicknesses up to 2ft. The product
range also included power presses,
inspection equipment for steel billets and slabs, welded
chassis and body assembly for fork lift trucks, tool
drawer bars, linkages for tractors and the 'Birfeed'
range of automatic bar feeding and loading magazines.
In the late 1960s the Metal Forming Plant Division
obtained a computer using the I.B.M. Kraus system. The
machine was used for costing orders and to trace the
progression of orders through the works. |
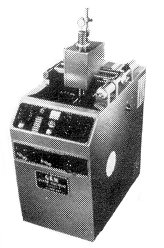
A Model 'C' spark erosion machine. |
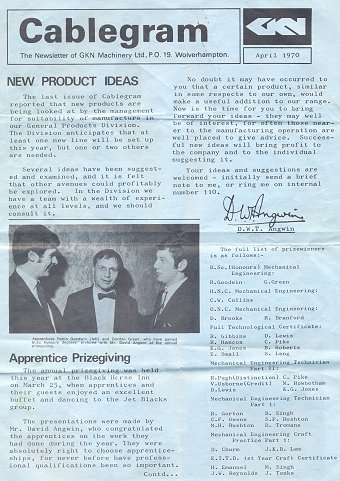
The company's newsletter.
Courtesy of Nina McCarthy.
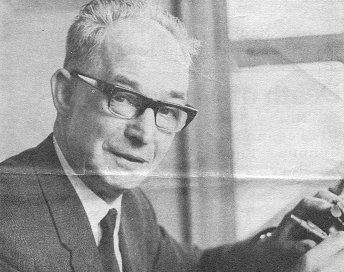
Cyril Banton. Courtesy of his
daughter, Nina McCarthy. |
The company's Works Engineer, Cyril Banton retired
in April 1970 after serving 41 years with the company.
He followed in his father's footsteps, who had worked in
the foundry for 40 years. Cyril's son Jimmy also worked
there for many years. Cyril was originally an
electrical engineer until 1963 when his predecessor Bert
Denny retired. Cyril was involved in several large
projects during the modernisation of the works,
including the new rolling mill and the machine and
assembly shop. |
By 1970 the rolling mills were run
by James Mills Limited and the Metal Forming Plant
Division were producing sophisticated servo-hydraulic
control systems. One order, worth £250,000 was for a
control system for a large rolling mill for Germany's
most prominent producer of tin plate and cold reduced
steel strip, Rasselstein A.G. of Neuwied/Rhein.
It all came to an end in the 1980s
when GKN decided to close the steel side of the business
and so the works were sold.
This article is based on
the following:
An article written by Helen Priddey, which can be found in the Museum Metalware Hall
on this website.
The History of GKN, volume 2 by Edgar Jones.
Material from Nina McCarthy whose father worked for the
company.
Various Wolverhampton Handbooks.
Bayliss, Jones & Bayliss catalogues. |
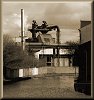 |
Return to the
previous page |
|