Iron and
Steel
In the 19th century, Walsall had several
ironworks, which must have been a spectacular sight.
Birchills Furnace
|
The earliest known blast furnace in the
town, which opened in 1803 was built in Birchills, and known
as ‘Old Birchills’.
It is listed in Thomas Pearce’s
History and Directory of Walsall, published in 1813. At the
time it was owned by Stubbs & James, and stood just to the
north of Reedswood Park.
The business is listed in David
Mushet's 'Papers of Iron & Steel, Practical and
Experimental' published in 1840 which states that in 1839 the
company was run by E. Tyler.
There was one blast furnace in
use, with a hot blast, producing around 45 tons of iron per
week.
The total production in 1839 was 2,340 tons. In 1872
the factory was run by J. Bissell and Son.
There were 16 puddling furnaces and 3 mills and forges.
|
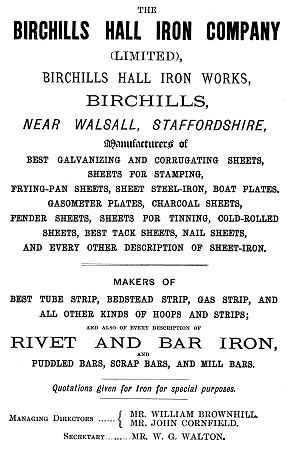
An advert from1873. |
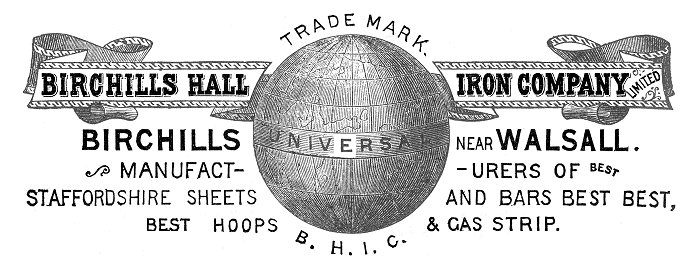
An advert from 1873.
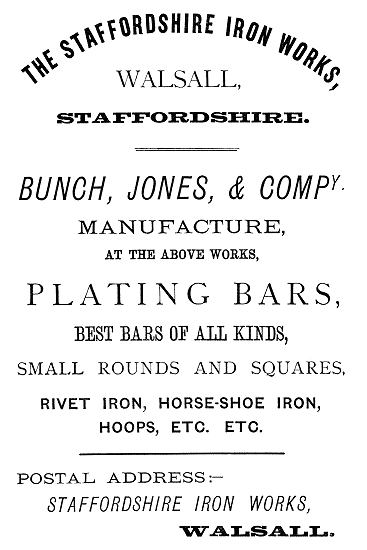
An advert from 1873. |
It continued in use until the mid
1870s, by which time two new furnaces had been built near to
the Wyrley & Essington Canal.
The first, known as ‘New Birchills’ opened around 1840, and was built on the northern
side of the canal close to Green Lane, near to where the
TK-Maxx warehouse is today.
The owner, George Jones, who
lived in Shackerley, Donington, Shropshire, had several
nearby coalmines, Birchills Field, Harden, and Forest.
The
factory became known as Birchills Hall Ironworks, and later
as Staffordshire Ironworks.
By the early 1850s there were
five furnaces, and around 400 employees, producing around
20,000 tons of pig iron a year.
|
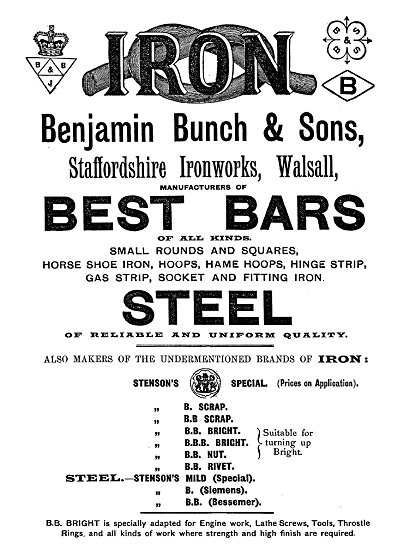 |
An advert from 1896. |
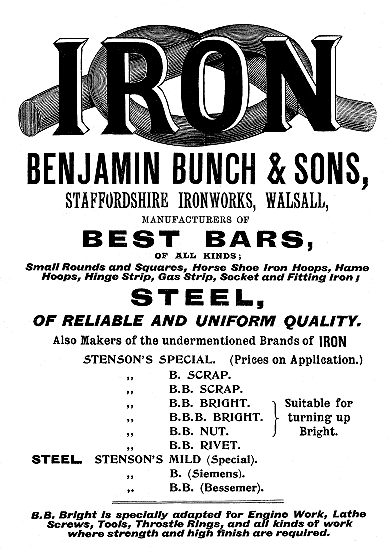
An advert from1899. |
In the mid 1850s George
Jones’ son John took over the business, which he ran until
1867, when it was sold.
At the time there were 28 puddling
furnaces, a foundry, and rolling mills.
It was taken over by
J. Brayford, who had died by 1872. He had 4 blast furnaces,
and operated 12 puddling furnaces, and 2 mills and forges.
The factory was soon divided into two
separate concerns.
In 1872 the rolling mills and finishing
plant were sold to two companies, Bunch, Jones & Company
(later Benjamin Bunch & Sons),
and the Birchills Hall Iron Company Limited.
The blast-furnaces were
acquired by the Birchills Estate Company, which sold them to
the Castle Coal & Iron Company in the late 1870s.
|
The location of Birchills Hall
Iron Works. |
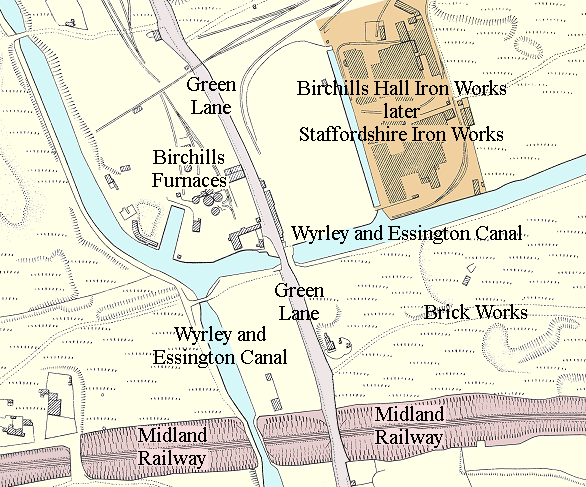 |
Another ironworks stood on the
opposite side of Green Lane, between the road and the canal,
just north of Birchills Junction where a landscaped open
space is today. It was built in 1851, and owned by Frederick
Parkes. The factory had two furnaces and became known as
Green Lane Furnaces. In the 1860s it was acquired by the
Walsall Iron Company, owned John Jones & Sons, and in 1894
was sold to John Russell & Company, wrought-iron and tube
manufacturers.
Around 1907 the factory was taken over by Birchills Furnaces Limited, and continued in operation until
around the end of the First World War. It closed in the mid
1920s and was demolished in the late 1930s.
There were two terrible accidents at ironworks in
Birchills. The first took place on 15th October, 1875 at
Birchills Iron Works, where a blast furnace exploded as
it was being tapped. The explosion was caused by a burst
tuyère, which resulted in furnace workers being covered
with molten metal and red hot ashes. Three men died
instantly, and twelve others, all with serious burns
were rushed to the Cottage Hospital.
Sister Dora immediately took charge
of the men and treated them alone, shutting herself up
in their side ward, nursing them both day and night for
several weeks. Despite all of her efforts, ten of them
died from their terrible injuries.
The second explosion occurred on
the 15th of May, 1880, when a Rastrick boiler exploded
at Birchills Ironworks. Twenty five people were killed,
and thirty injured, many of whom had very serious
injuries. |
|
|
|
|
|
Read about the explosion
at
Birchills Hall Iron Works in 1880 |
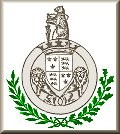 |
|
Read about the explosion
at
Birchills Iron
Works in 1875 |
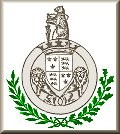 |
|
|
|
|
|
Pelsall Ironworks
Another large ironworks was built at
Pelsall on the northern side of the Wyley & Essington Canal, to the east of the Cannock
Extension.
Pelsall Ironworks opened in 1832 and was built by Mr.
Richard Fryer, a Wolverhampton banker who became one of the
first two members of parliament for Wolverhampton, and
owned, and lived at the Wergs Estate.
|
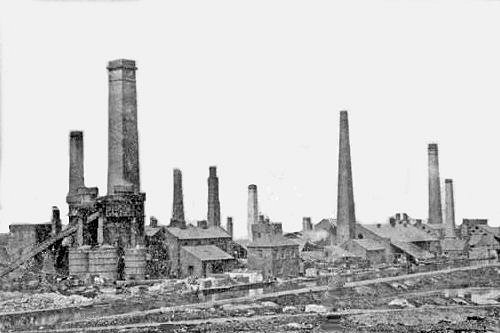
Pelsall Ironworks. |
After his death in 1846 the ironworks was sold to Davis
and Bloomer. It is listed in William White’s 1851 History,
Gazetteer, and Directory of Staffordshire as producing bar
and sheet iron of the best quality. After Mr. Davis’s
retirement, the firm was run by Boaz Bloomer and his son who owned
several nearby coal mines, which supplied the ironworks.
They changed the name of the business to The Pelsall Coal and Iron Company.
It grew into an extensive ironworks with two blast
furnaces, forty puddling furnaces, seven mills and forges, a
gashouse and gasometer, and an large tramway with locomotive
and wagon sheds.
Several hundred people worked on
the site, and iron was exported to many countries throughout
the world including America, India, and China. Success
continued until the recession in the iron trade in the
latter quarter of the 19th century. In 1891 the firm lost
£3,647.11s.7d. The company was forced into liquidation in
1892 when repayment was demanded for an overdraft of
£20,000.
The coal mines were sold to the Walsall
Wood Colliery Company, and the plant was sold-off cheaply to
Alfred Hickman of Bilston Steelworks. It was a sad end to
such an important local employer. Its demise led to a crisis
in the village because of the large number of inhabitants
who lost their jobs. Many of whom had previously moved to
Pelsall after finding employment at the works. The Bloomer
family were strong Methodists and benefactors. They were
greatly involved in the building of the Methodist Chapel in
1858, and the Wesleyan day school in 1866. In the 1860s Boaz
Bloomer opened a room at the works where daily newspapers
and periodicals were available for employees to read.
The ironworks had a Tommy shop in Wood
Lane near the canal bridge, where the employees could
exchange the tokens (that were given as part of their wages)
for all kinds of goods. After the closure of the firm, the
Bloomers moved away from the area, but left a lasting impression on the
local community. The chimney stacks, the last remaining part
of the factory, were demolished in the 1920s.
Hatherton Furnaces
In 1845 Richard Fryer who founded
Pelsall Ironworks leased a piece of land from Lord Hatherton
on which to build an ironworks, and mine coal. The land was
on the northern side of Leamore Lane, alongside the canal.
When Richard died in 1846 his son William took over the
lease. The factory, which became known as Hatherton
Furnaces, had two furnaces. Around 1870 it was leased to
George and Richard Thomas of Bloxwich, whose company became
G. & R. Thomas Limited. Richard Thomas died in 1920, and the
firm survived until 1935, when it went into liquidation. Its
assets were sold, and the furnaces continued in use until
1948. The site was later used as a foundry.
Ironworks at Pleck
In the latter half of the 19th century, Pleck became an important manufacturing centre when many
heavy industries grew-up alongside the canal. It began in
1851 with the opening of Sinkinson & Lancaster in Pleck
Road. The firm produced bar and sheet iron, and rolled
sections. Within a few years it was taken over by Brayford &
Lancaster. |
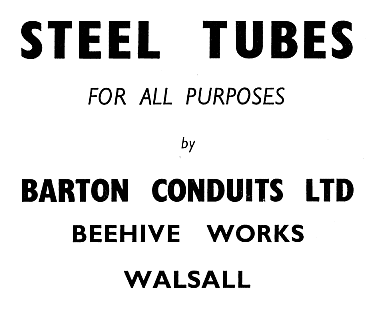
An advert from 1953. |
The largest ironworks in the area was
Edward Russell's Cyclops Ironworks in Pleck Road which had
22 puddling furnaces and 3 rolling-mills.
The firm produced
iron and steel tubes of all kinds. |
|
|
|
|
|
Read about John
Russell &
Company |
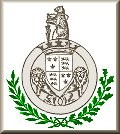 |
|
Read about tube making |
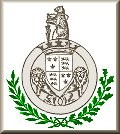 |
|
|
|
|
|
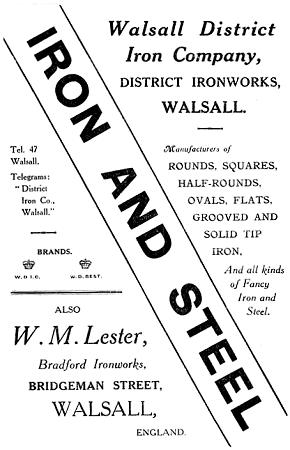 |
Another large factory on Pleck Road was
the Staffordshire Galvanising and Iron Company which was in
operation by 1875. The business was extremely successful and
took over the adjacent Victoria Ironworks in about 1890.
In
the late 1870s it became Walker Brothers, which in turn
became part of the Benford Fabrications Group. Products
included galvanising and sheet metal work, wire netting,
sheep troughs, and iron roofs. Some of the products were
exported to the Far East and South Africa. After the second
World War galvanised sheet production ended and the company
concentrated on galvanised steelwork.
Other factories in Pleck Road included
Walsall Tube Works, Crescent Chain Works, James Iron
Foundry, the Bridge and Roofing Works, and Junction Saw
Mills. On the other side of the canal was Bradford Tube
Works, Bradford Iron Works, and Globe Iron Works. |
Another manufacturer based in Pleck Road was Hope
Works Limited. The firm, which moved to Pleck Road from
Selbourne Street, had been acquired by Walsall iron
merchants Thomas Franks and Sons Limited, in
Wolverhampton Street. One of Thomas Franks' sons
Alfred, became Chairman of Hope Works Limited, which
subsequently opened a branch in Bloxwich.
The firm eventually became part of Laidlow & Thomson
Limited, 60 Cannon Street, Manchester.
The image on the right is from the cover of the
company's catalogue produced in the early 1940s. It
contains all kinds of ornamental ironwork which were
coated with "Corresista", a rust preventing zinc paint,
and treated with Hopsall stove synthetic finish. At
extra cost, all the company's products could be
Sherardized, and were also available in solid brass,
finished in an old-looking colour.
A few of the many products from the catalogue can be
seen below: |
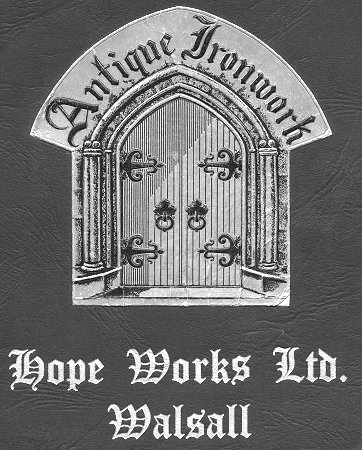 |
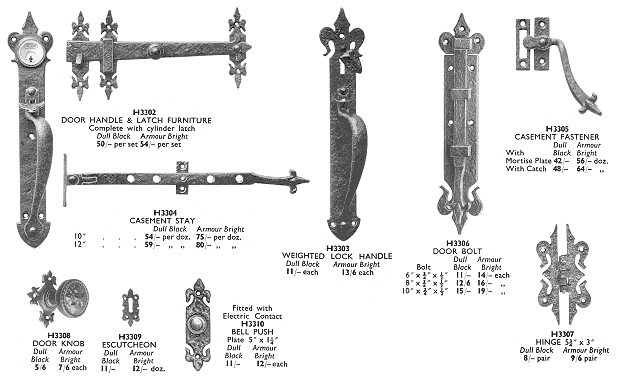
Door and window fittings.
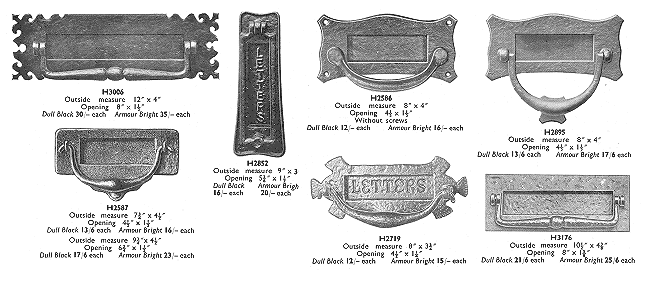
Letterboxes with handles and knockers.
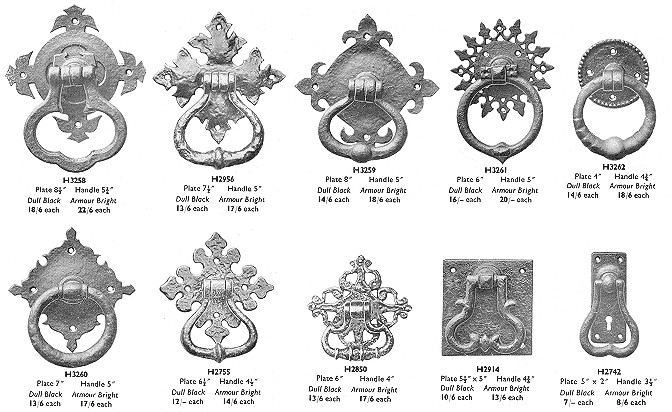
Door or gate handles.
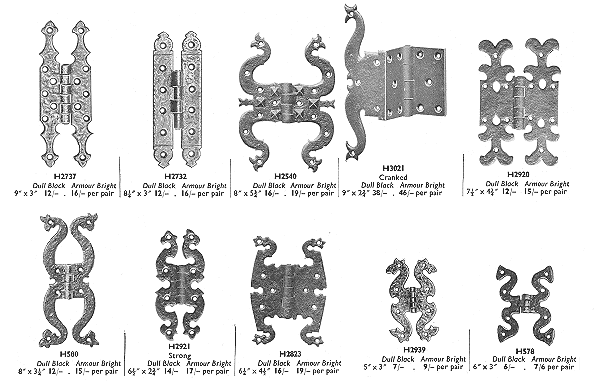
Hinges.
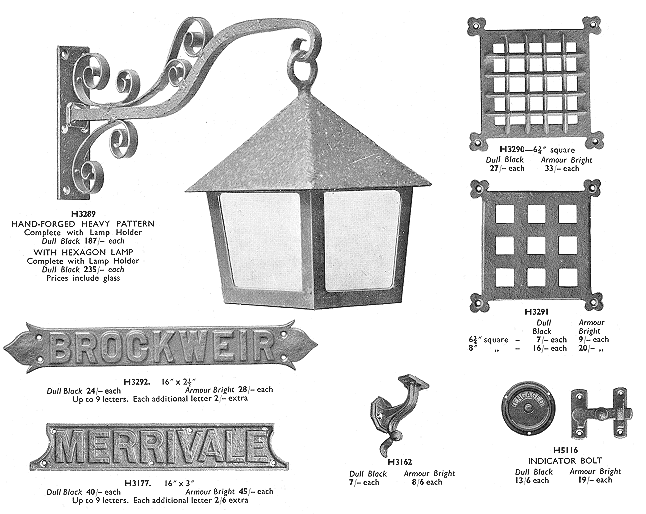
Nameplates, grills, and hanging lamp.
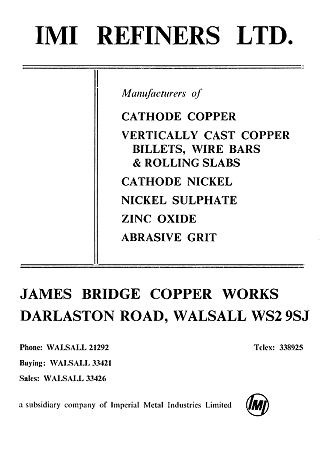
An advert from 1976. |
Until recently, a once well-known
factory
stood at the western end of Pleck beside the canal, on the
site of the former James Bridge Brick Works. This was the
James Bridge Copper Works which opened in 1919 as a
subsidiary of the Wolverhampton Metal Company Limited.
In
1931 the factory was forced to close by Walsall Town Council
after a series of complaints about the sulphurous fumes that
came from the 100ft. high chimney. At the time around 150 manual
workers who worked in the factory lost their jobs. Taller
chimneys were built, and the factory reopened the following
year.
It was forced to close again
in World War 2 because of blackout problems, but reopened
after the war to recover copper from war surplus items.
The
firm became a Limited company in 1946, and in the early 1950s
became one of the country’s leading copper reclamation
companies. All kinds of waste materials including ash and
foundry residues were transported to the factory to produce
high quality copper. |
In 1967 the plant was updated to increase production of
high grade electrolytic copper from 15,000 to 50,000 tons a
year. During the same year James Bridge Copper Works Limited
became part of IMI Limited (Imperial Metal Industries
Limited) and became known as IMI Refiners Limited. It was
the last copper refining business in the country, but sadly
closed on 31st December, 1999. The factory was demolished in
2000. |
Other tube manufacturers
In the 19th century Walsall became an
important centre for the production of the wrought iron
tubes that were essential for the supply of town gas. The
industry began in Walsall with the formation of Edward and
William Dixon’s firm in 1829. The company started making gas
tubes in Birmingham Street in 1830, and around four years
later moved to the Alpha Tube Works on the western side of Ablewell Street.
By 1868 the firm changed its name to
Lambert Brothers, and in the early 20th century moved to new
premises beside the canal in Green Lane, also called Alpha
Tube Works. Along with wrought iron and mild steel gas
tubes, the company produced gas valves, lamp columns and
manhole covers.
The largest tube manufacturer in the
town was the Talbot-Stead Tube Company Limited, founded in
1906 by W. J. Talbot and Geoffrey Stead. They opened a
factory in Green Lane for the production of seamless steel
tubes. In the First World War the company supplied around a
quarter of the boiler tubes used by the Royal Navy.
In 1931 the firm became part of Tube
Investments Limited, and in 1962 became T.I. Stainless Tubes
Limited. The factory closed in 1972, and in 1973 was
acquired by T.I. Chesterfield Limited. |
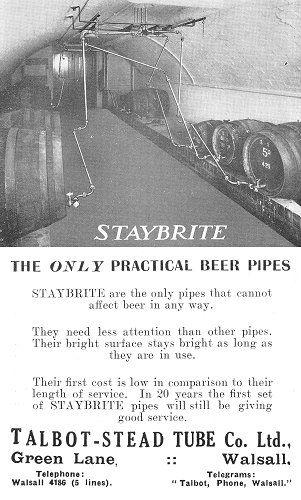
An advert from 1935.
|
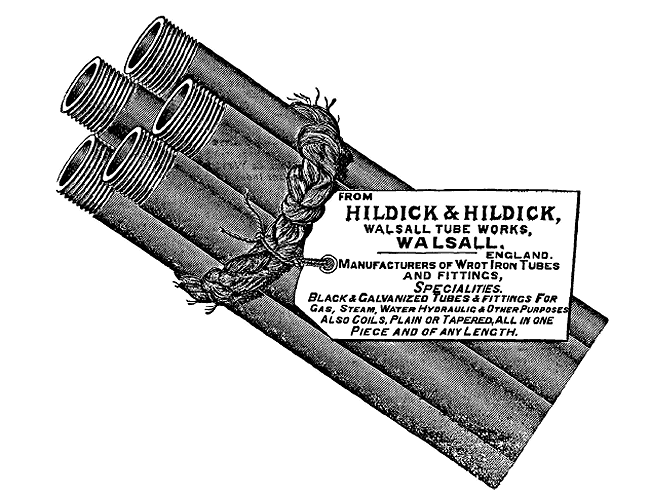
An advert from 1896 for Hildick &
Hildick, Walsall Tube Works, Pleck Road. |
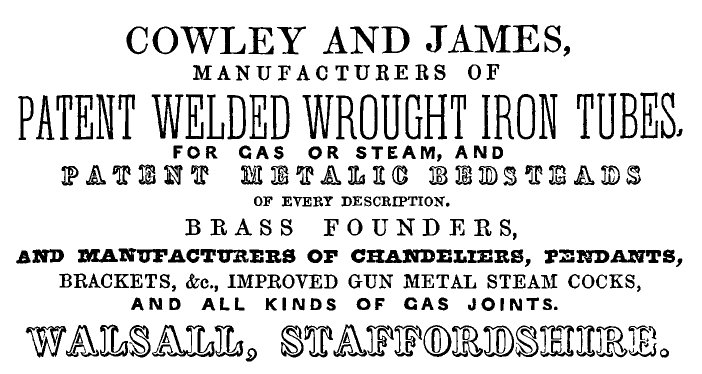
An advert from 1851.
Other non-ferrous metal producers |
McKechnie Metals Limited
In 1871 Duncan McKechnie established a
factory at
St. Helens, Lancashire, for copper extraction,
where he produced refined copper ingots, bar silver, pig
lead and copper sulphate. In 1894 the firm became an early
pioneer in the brass and copper alloys extrusion business,
after opening a factory in Birmingham.
Over the years the demand for the
company's products grew, which led to the construction
of a new factory in Middlemore Lane, Aldridge in 1954. The
factory was equipped with the most up-to-date equipment, and
soon all of the company’s production was moved there. The
firm specialised in the production of alloys to individual
customer’s specifications, and the extrusion some of the
more unusual materials. Products also included large numbers
of brass ingots, particularly in die-casting qualities, and
billets to all
specifications.
Branches of the company were
established in South Africa and New Zealand. |
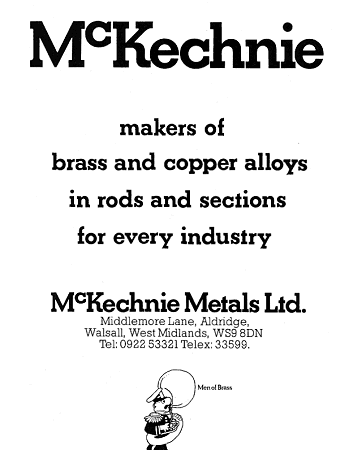
An advert from 1976. |
The firm became known as known as McKechnie Brass Limited and produced a wide range of alloys
for many diverse applications. Brass products include
billets, round rod, shaped rod, turned parts and stampings
for the water, gas and electrical industries. Other products
included, locks, handles, lift tracks, showers, electrical
fittings, and copper trolley wire, which was used to supply
electric power to high-speed trains, locomotives and trolley
buses. Sadly the firm went out of business in 2013, having
accrued debts of £3.8 million. Sixty people lost their jobs.
In 1902 another non-ferrous metal
manufacturer, New Delaville Spelter Company Limited opened
the Delaville Spelter Works in Willenhall Lane, Bloxwich. By
1918 the company had eight furnaces on the site for smelting
zinc ash, and two others for recovering zinc from hard spelter.
Products included zinc oxide, and zinc dust. In 1933 the
firm was taken over by the Imperial Smelting Corporation.
After the Second World War production was limited to zinc
dust, Mazak zinc alloy for die-casting, and high purity zinc anodes. |
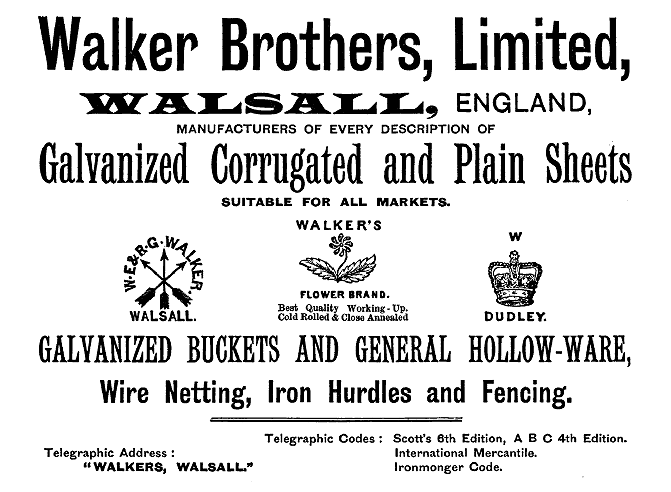
An advert from 1896. Walker Brothers were
based in Pleck Road.
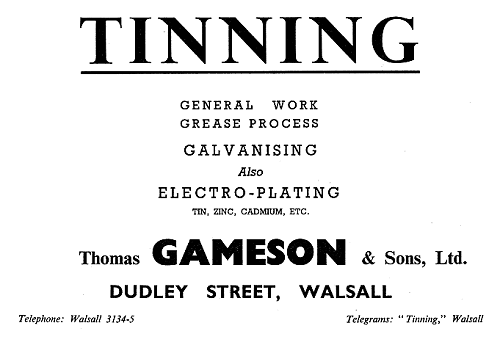
An advert from 1958.
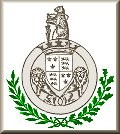 |
Return to
the
previous page |
|