The Patent Shaft
Steel Works Limited - The Factory in the Late 1970s |
 |
One of two Birlec UHP
electric arc furnaces, 5.8 metres in diameter, rated
at 45 MVA, with a nominal capacity of 88.5 tons.
They were charged with scrap
from baskets that had been loaded in the scrap
handling bay.
Each furnace had its own
load cell weighbridge with a VDU that indicated the
weight and grades of scrap required.
Oxygen for the furnace was
supplied by an oxygen lancing rig.
The molten steel was tapped
into ladles, then teemed into ingot moulds for
transfer to the primary mill. |
Teeming molten steel from
the ladle into ingot moulds, before they were taken to
the primary mill, where ingots were stripped from
their moulds and heated to a rolling temperature of
around 1,250 degrees centigrade.
They were then rolled to
produce slabs or billets, which were cut to
pre-determined lengths. |
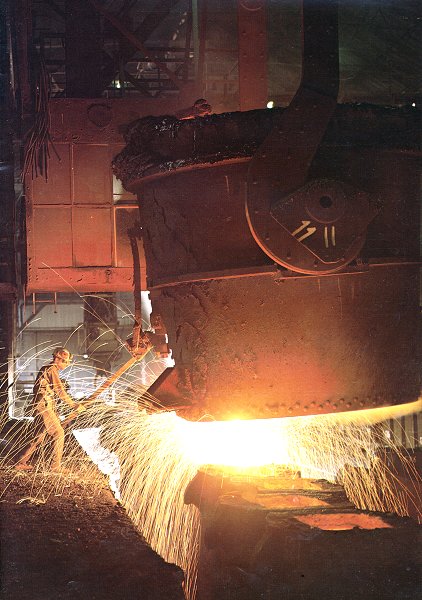 |
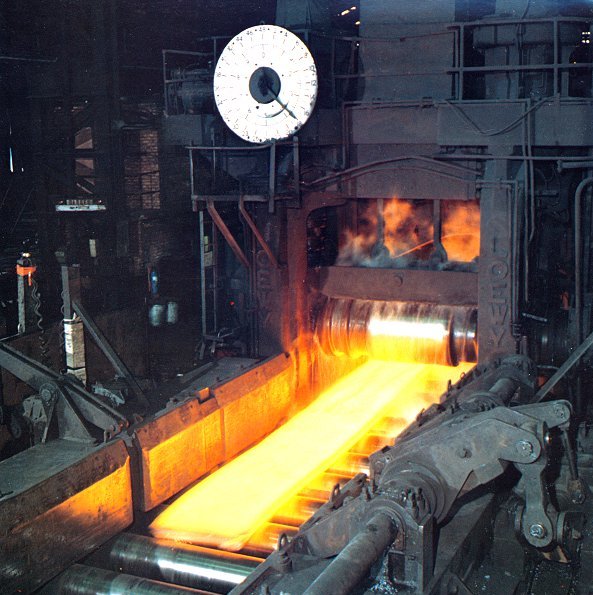
The primary rolling mill. |
 |
The plate mill
where slabs were initially heated to around 1,200
degrees centigrade in a push-down or a rotary hearth
furnace, in readiness for rolling.
After descaling, the slabs were
rolled on a 4 inch high, reversing mill. The plate
was rolled on heavy back up rolls to ensure that the
gauge was even over the entire width of the plate.
After rolling, the plates
passed through an eleven roll hot leveller, then
along a plate cooling conveyor, to the marking bed. |
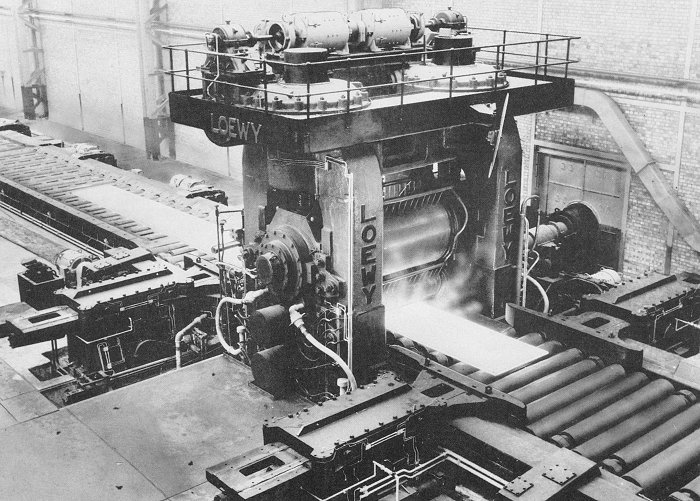
Another view of the
Loewy reversible rolling mill, in the plate
mill. |
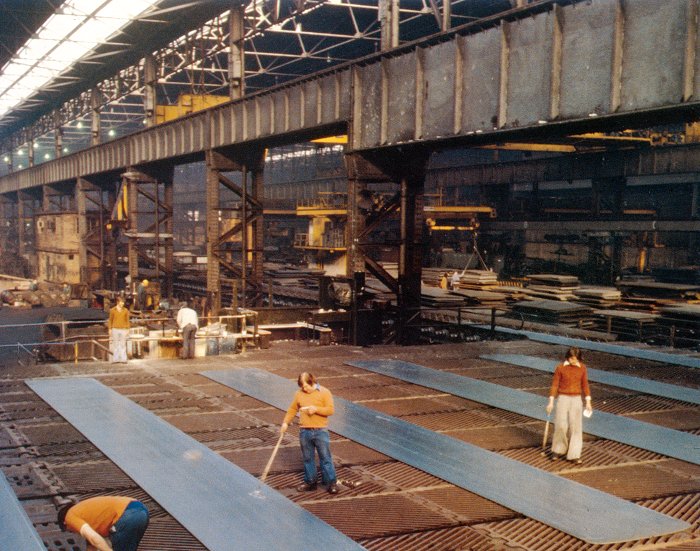
The plates were carefully
surface inspected before they were sheared, to
ensure a constant width, then cut to length by a
cross-cut shear. |

The plates were then
levelled in one of two levelling machines. |
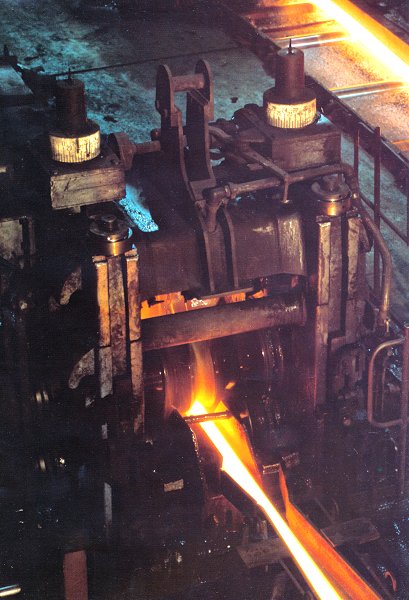 |
The bar and section mill
where billets from the primary mill were cut to size
and brought-up to a rolling temperature in a
push-down reheating furnace, before transfer to the
rolling mill. |
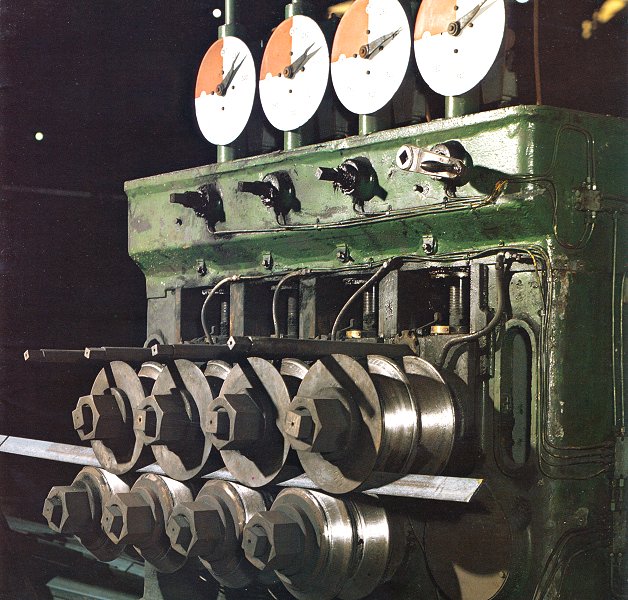
In the rolling mill the
billets were rolled to a wide range of angles, flat,
or square bars. A high degree of straightness was
maintained. Additional finishing facilities included
cold sawing, heat treatment, shot blasting, pickling
and oiling, painting and bundling. |
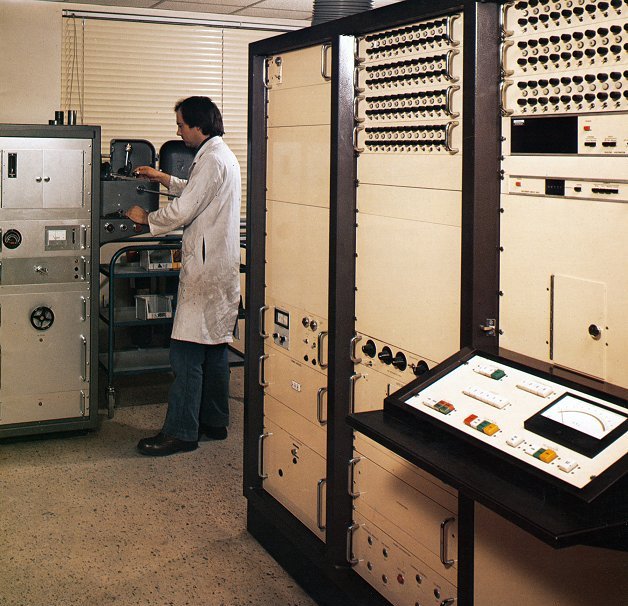
Quality control of steel
plates began with the steel itself. Two Quantovac
emission spectograph analysers were used to
determine the exact specification of the steel.
Other tests included tensile, impact, and bend
tests. |
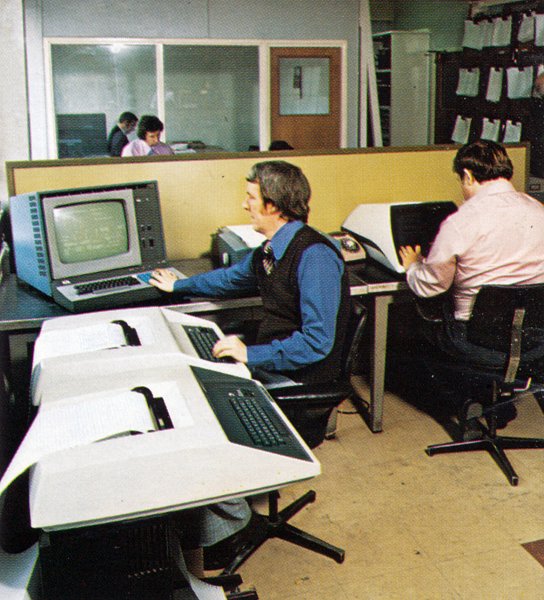 |
The sales and
production planning department ensured that the
correct product was delivered to the
correct place at the correct time.
Progress information was
continuously transferred to the planning office
where the planning was assisted by the ICL 1902A
computer. |
The maintenance
section had a machine shop, a diesel repair
workshop, and central engineering stores. Staff
included engineers, bricklayers, erectors,
carpenters, and plate layers.
The computer system
provided a record of the sequence and magnitude
of plant faults. This allowed steps to be taken
to limit the effects of major plant
breakdowns. |
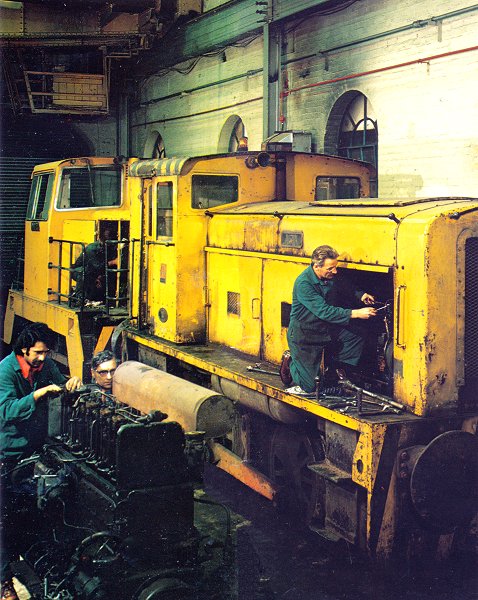 |
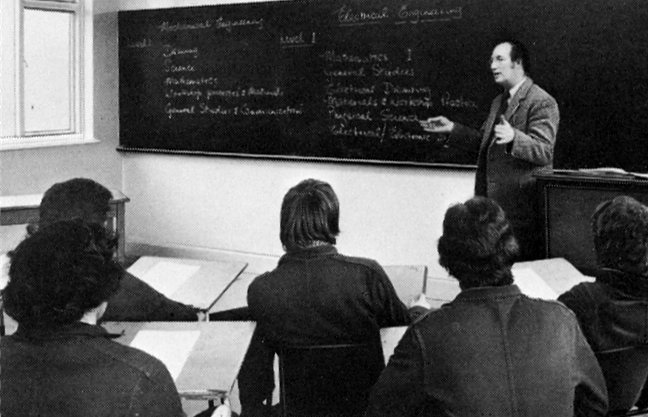
A training school was
established where full-time supervisors
taught a variety of specialised skills to
apprentices, who were encouraged to attend
courses in technical or commercial colleges
in order to obtain appropriate
qualifications. |
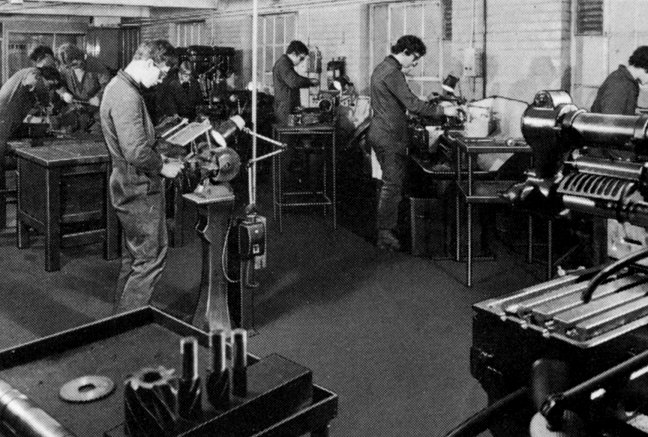
A workshop in the
training school. |
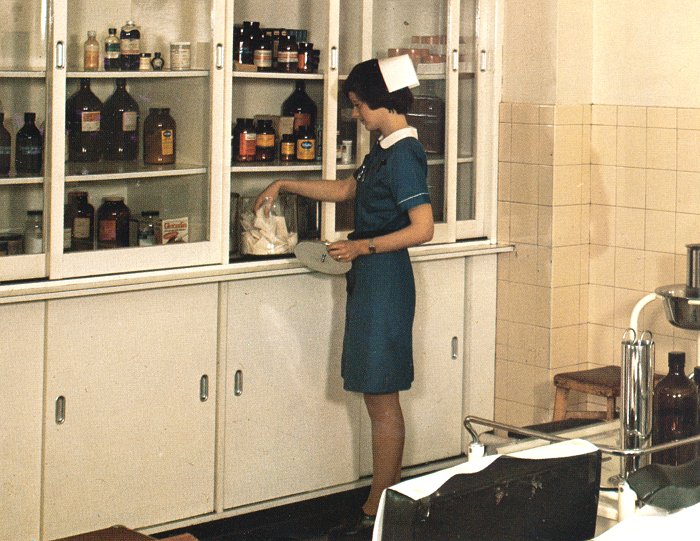
The fully equipped
surgery was available for the use of all
employees. The factory was also regularly
visited by a qualified medical officer.
There were Works Safety Committees, a Joint
Works Council, and a Staff Council where
representatives of the employees could
discuss a wide range topics with management.
There were also modern kitchen and canteen facilities
that supplied full meals or snacks to employees,
and the Shaft Social and Athletic Club
provided first class facilities for many
sporting activities including football,
fishing, snooker, badminton, and ladies'
netball. |
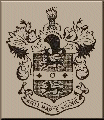 |
|
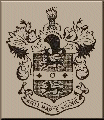 |
|
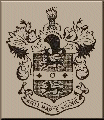 |
Return to
Development Schemes |
|
Return to the
beginning |
|
Proceed to
Closure |
|