The Patent Shaft Steel Works and Old Park Works
The Patent Shaft Steel Works became
one of the most important and well known factories in
Wednesbury. It survived for over 140 years and was very
profitable until the last few years of its
life. The factory was once a familiar sight on the
southern side of the town, and employed a large number
of people. When it closed in 1980 around 1,500 people
lost their jobs.
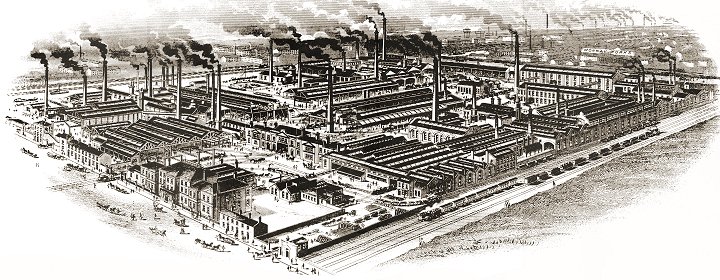
|