The Patent Shaft
Steel Works Limited - Development Schemes |
Throughout 1971 studies on the
development of the company, considered to be
essential for its future well being, were carried
out, and a report was prepared and submitted to The
Laird Group in May 1972. The recommendations were
based on developing the company at a minimum capital
cost, in order to provide moderate growth and to
enable further development at a later date, to meet
technological and commercial changes.
|
The report recommended that
steel plant production should be increased by
replacing two of the six open hearth furnaces with
one electric arc furnace, the plate mill finishing
facilities should be improved, as should the quality
of the section mill products by installing an
independently driven finishing stand and a walking
beam cooling bank.
The Board decided that the
development work recommended should be carried out
in phases, commencing with improvements to the plate
mill which produced plate in thicknesses from 5mm to
80mm, and with a maximum plate width of 2,290 mm, and
a maximum plate weight of 39 tons.
A new mill complex consisting
of a slab yard, a reheating furnace, a rolling mill,
a plate shearing line, and handling facilities was
installed on the Lea Works site to process plate
production from 4,576 tons of slabs per week. Work
on the new plant was completed in December 1973.
|

An advert from the early 1960s. |
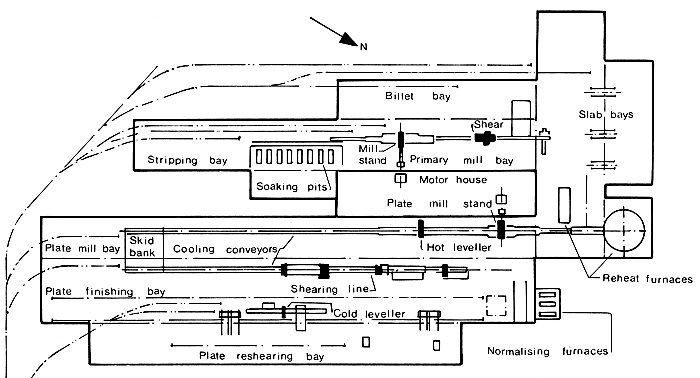
Layout of the primary and
plate mills at Lea Works. |
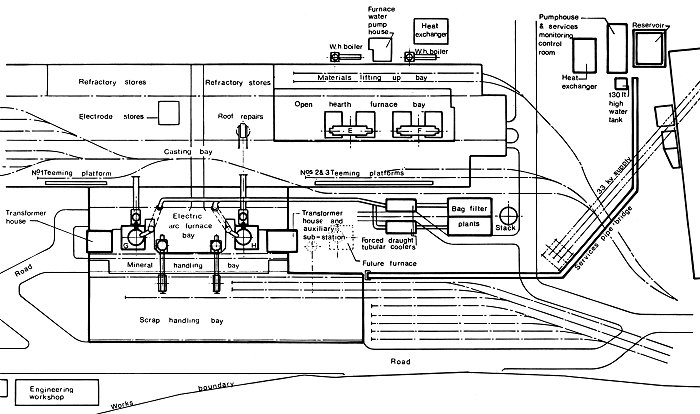
Layout of the new steel plant
at Brunswick Works. |
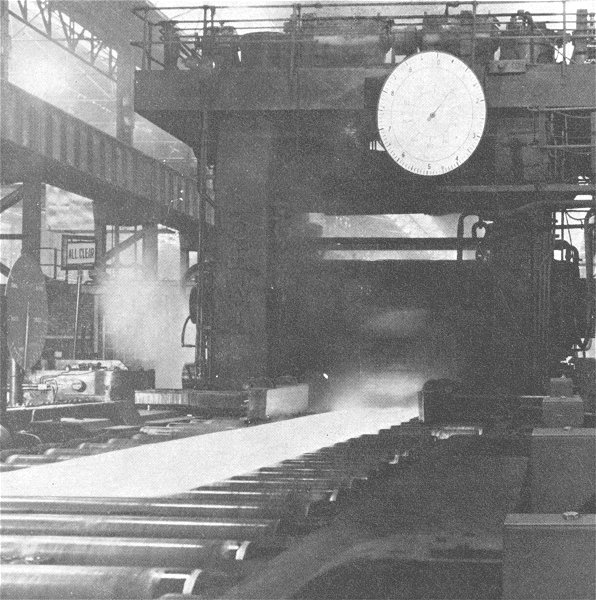 |
The Plate Mill. |
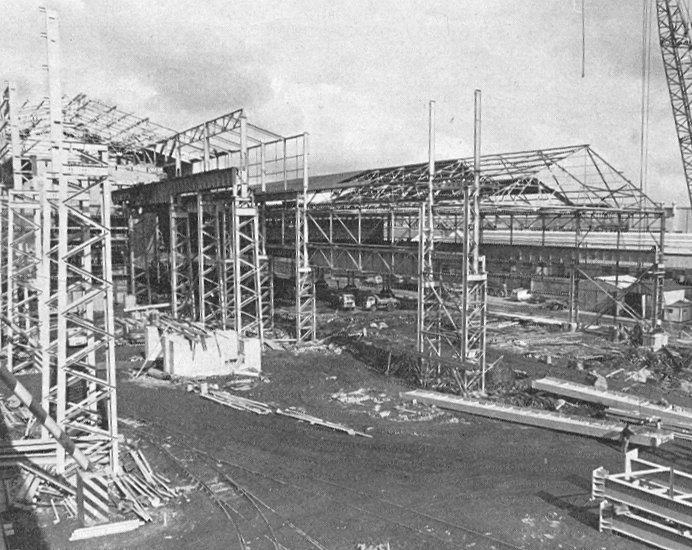
Building the electric
arc furnace bay, the minerals handling bay,
and the scrap handling bay. |
The second phase of development
included the installation of an electric arc furnace
at Brunswick Works. It was housed in a new casting
bay, on the outside of the existing bay. In November
1973, following the international oil crisis, a
second electric arc furnace was installed to reduce
the company's dependence on oil supplies.
The new
installation was designed by The International
Construction Company Limited; which had acted as
consultants in the major development scheme of
1956-59.
The electric arc furnaces were
5.8 metres diameter with a nominal capacity of 88.5
tons. They had 500 mm diameter electrodes and were
fed from transformers rated at 45MVA.
They were
equipped for automatic power input control and had
an interface facility for possible future computer
control. The new furnaces proved to be entirely
satisfactory in service.
|
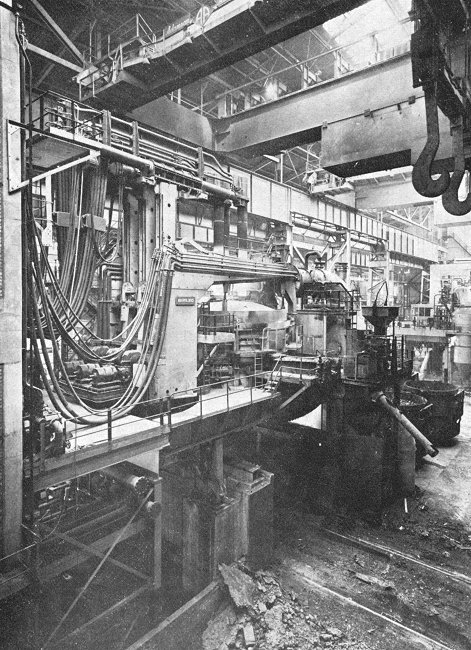
The electric arc furnaces. |
The scrap handling bay was
re-sited and lengthened. It had four overhead
cranes, each equipped with a magnet. A new minerals
bay for the handling of lime and coke etc. was
added, alongside a new furnace bay that housed two
UHP electric arc furnaces, located 7 metres above the
ground at charger platform level. Slag from the
steelmaking process was tipped into a shallow
depression from where it was removed by a traxcavator, a combined tractor and
excavator. |
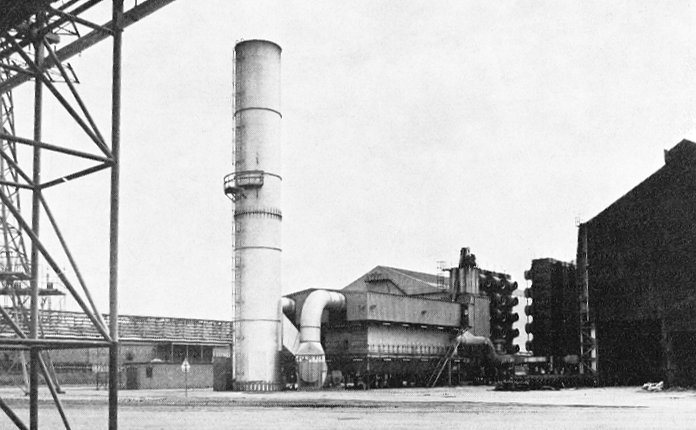
The fume cleaning plant. |
Other new
buildings included a state of the art fume cleaning
plant, and a new electricity sub-station. The first
of the two new furnaces began operating on 1st
December, 1975, after the Central Electricity
Generating Board had installed a 33kV supply. The
second furnace went into service on 30th March,
1976. At the same time a new section mill was built
at Monway Works, which began operation in December
1975. |
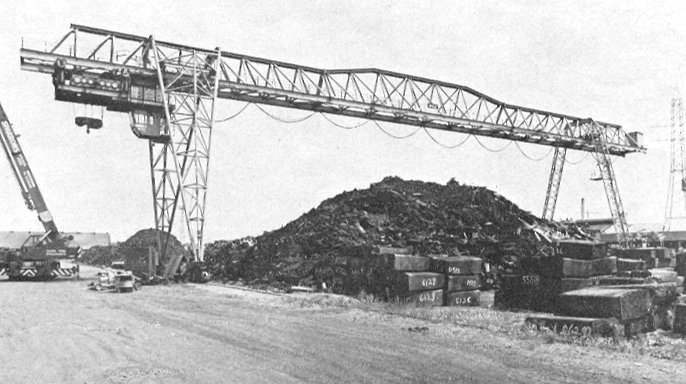
'Goliath' materials handling
crane. It could travel over 230 metres and covered
an area of 3.8 acres. |
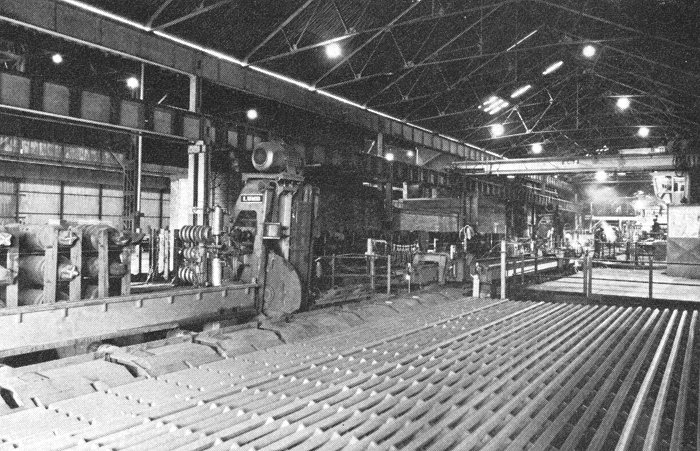
The walking beam cooling bed
and the saws, in the section mill at Monway Works.
|
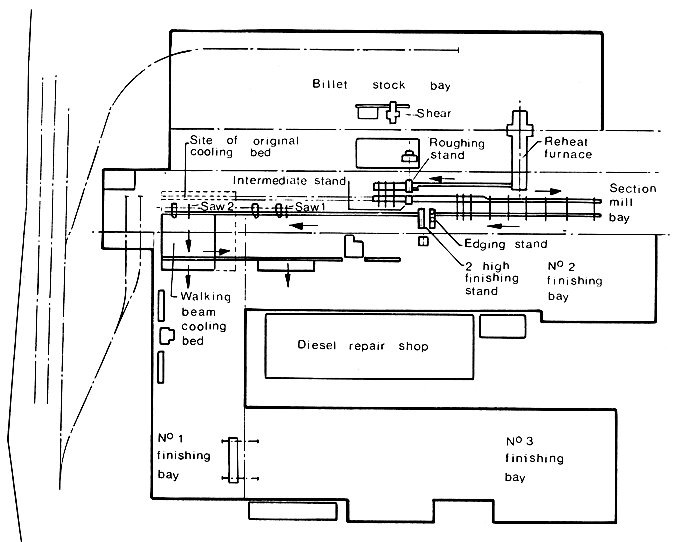
The section mill at Monway
Works. |
On-line computer planning of
slab production in the primary plate mill began to
be used in order to increase the output by
determining each slab length after an ingot was
rolled, but before it was cut, resulting in an
increase in throughput without a loss of overall
yield. A new computer building was erected to house
two Digital Equipment PDP 11/40 computers, as well as
the firm’s existing ICL 1902A, which was used for
planning, invoicing, and general accounting. The new
computers were connected to 36 terminals, situated
at various points in the mill and soaking pit areas,
as well as in the steel plant, laboratory, and
planning department. Details of ingots cast and
reheated were fed to the computer which then
determined optimum slab dimensions and issued
instructions through display panels to the rollers,
shear operators, and other personnel concerned. |
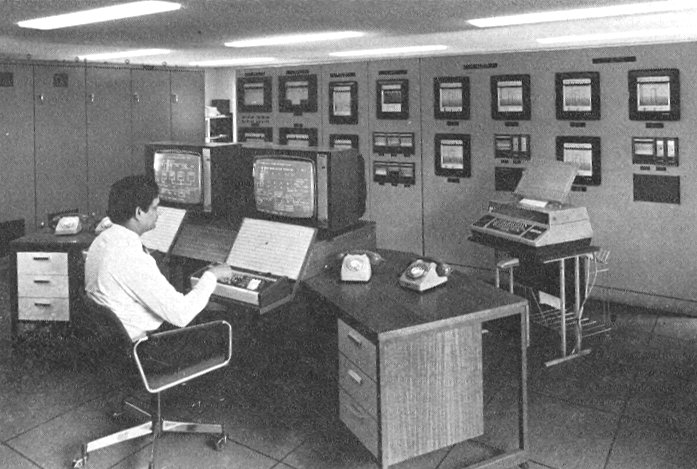
The services monitoring
control room. On the left in the background is the
computer, on the right the strip chart display
panel, and in the foreground the control desk, VDUs
and one of two teleprinters. |
A centralised works services
monitoring and control system had operated since
1965, based on conventional instrumentation. By
1973, due to the considerable expansion on the site,
it needed expanding and updating. A small computer,
a printer, and several terminals were purchased for
the purpose. Details of any plant faults could be
printed out, and operators could see clearly and
immediately when a fault developed. In the early 1970s the company
purchased the old Monway Canal Branch that had been
used for the delivery of coal to a Lancashire boiler
range, and more recently as part of the works water
supply.
The canal now formed a physical
barrier between the three main works areas and was
limiting further development. It was drained in
sections and back filled. A reservoir was
constructed, adjacent to the new water services pump
house for the electric arc furnaces, which was
connected by a 0.75 metre diameter pipe to the main
canal.
As a result of the development
scheme, the number of people working on the site was
reduced from 1,800 to 1,725. The resulted in only
four redundancies, 36 men were redeployed, and 35
accepted voluntary redundancy.
The redevelopment scheme, completed in 1976, cost around £11.3 million.
|

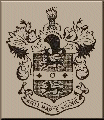 |
|
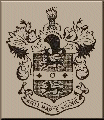 |
|
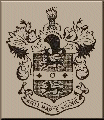 |
Return to
Take Over |
|
Return to the
beginning |
|
Proceed to the Factory
in the Late 1970s |
|