There was a time not that long
ago, when parts of Wolverhampton constantly rang to the
sounds of industry, and night skies were ablaze with
light from numerous factories and furnaces. Today most
of our factories have gone and it’s hard to imagine what
life was like in the industrial era. One of our oldest
factories is the Crane Foundry, which occupies a foundry
site that dates back to the late 18th century.
The foundry is situated alongside the
canal and originally had its own basin. Many foundries
were built close to a canal to use the readily available
supply of water to cool their cupolas. With the opening
of the canal in 1772 the area became heavily
industrialised and for the first time raw materials
could easily be transported here and finished goods
taken away. Its early neighbours included T. & C.
Clarke’s Shakespeare Foundry, which opened in 1795; the
Shrubbery Iron Works, founded in 1824; Isaac Jenks &
Sons’ Minerva and Beaver Iron, Steel, & Spring Works;
the Osier Bed Iron Company; and the Horseley Fields
Chemical Works.
|
By 1827 the foundry was known as
Atherton’s Foundry and run by James Atherton and Henry
Crane. Initially it was a brass foundry, but by 1827
iron castings were also produced on the site.
The main products were castings for
the building industry, ironmongery and brassware. In the
1830s castings for the hand tool and lock industries
were added to the product range and by 1836 Henry Crane
had taken control of the business. |
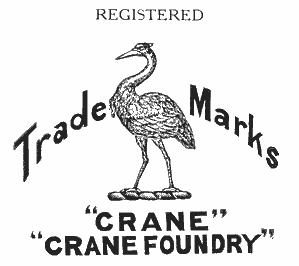 |
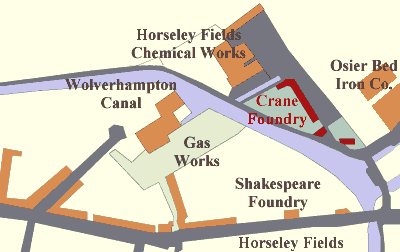
The Foundry in 1842. |
The company became known as the
Crane Foundry in 1847 with its own registered trademark.
By the 1850s iron weights were
produced, and a design was registered in 1872 with
roundels decorating the edge. Brass weights were also
produced, mainly after the regulation of 1890 that
required weights of 2oz. or less to be made of brass. |
A look at the 1881 census reveals
that the Crane family lived at Lower Street, Tettenhall.
Charles Henry Crane ran the business
and was aided by his two sons, Edward and Charles. At
the time the foundry had 150 employees.
Edward was a member of the
Wolverhampton Chamber of Commerce and became President
in 1902. |
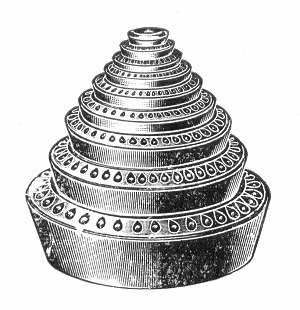
The registered design of weights
with roundels.
|
 |
Read about the
moulding and
casting process |
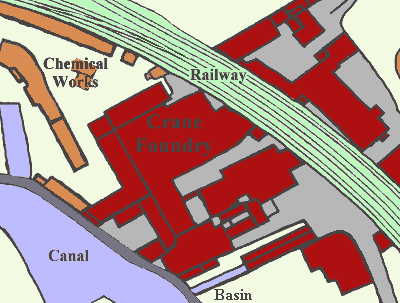
The foundry in 1919.
|
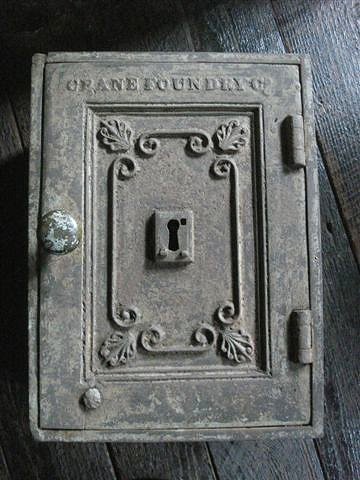
A Crane Money Chest. Courtesy of Marlena Fairbourne. |
In the early 1900s the foundry
began to produce castings for electric motors and
continued to do so throughout its life.
The Crane family
continued to control the company until 1917 when William
Cyril Parkes of lockmakers Josiah Parkes & Sons Limited,
Willenhall became a majority shareholder, with the
immediate result that the production of lock cases
greatly increased.
One of the lock-related products from the late
1920s is shown opposite. It is a cast
iron Crane Money Chest. You can still see the
original green paint in places. |
Another view
of the Crane Money Chest.
Courtesy of
Marlena Fairbourne. |
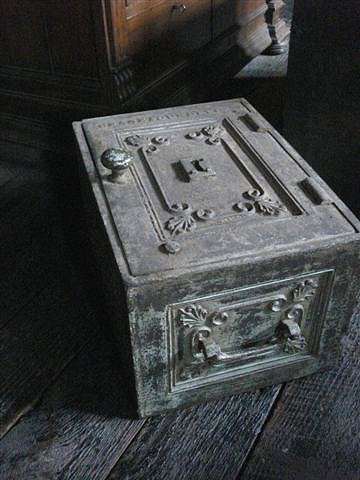 |
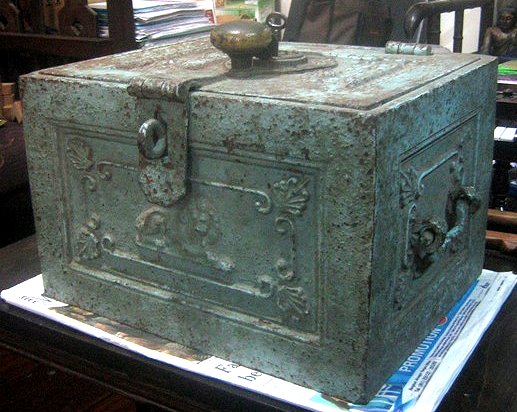 |
A lovely Crane Money Chest
that found its way to Burma.
Courtesy of
|
Another view of
|
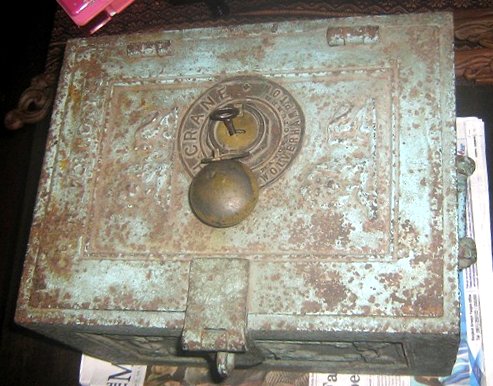 |
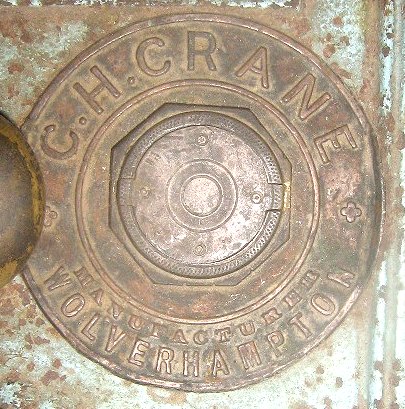 |
A close-up view of the
maker's plate that's on the front of
|
A look at the company’s 1928
catalogue reveals over 300 products including weights,
rice bowls, sad irons, ventilators, mole traps, door
knockers, and hinges.
 |
View the 1928
Crane catalogue |
|
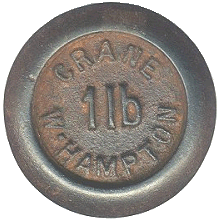 |
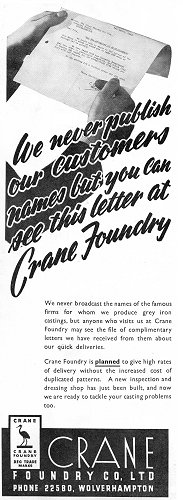
An advert from "Machinery"
30th June 1933. |
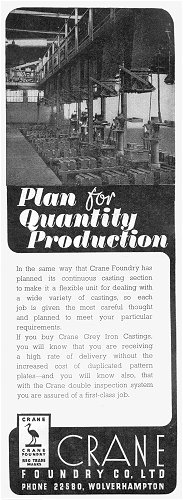
An advert from the "Electrical
Times" 20th April 1938. |
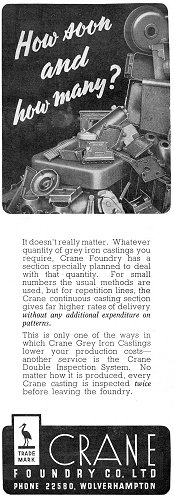
An advert from 1938.
|
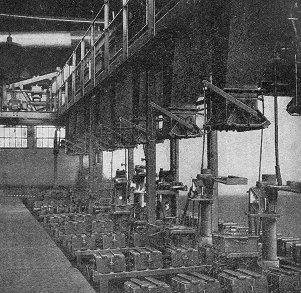
A corner of the works in 1938. |
The company began to specialise as a supplier of
castings to engineering companies, as can be seen from
the above adverts. Crane brand metalware eventually
became a thing of the past and this change in direction
helped the foundry to survive long after all of it's
local competitors had gone. By April 1937 the
metalware catalogue consisted of just five pages,
whereas the 1928 catalogue had 77 pages. The principal
metalware products in 1937 were box irons, heaters, sad
irons and weights. |
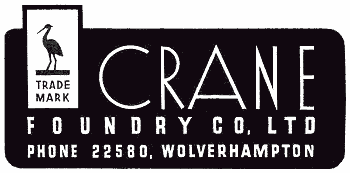
Qualcast
On 25th June, 1945 Josiah
Parkes & Sons sold the foundry to Qualcast for £9,200
and in 1949 the foundry was officially called Qualcast
(Wolverhampton) Limited. The Crane trade mark was still
retained and the factory continued to be known as the
Crane Foundry. The company also owned the nearby Swan
Gardens Iron Works off Swan Street.
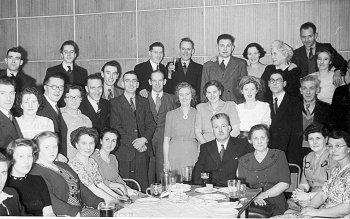
A staff social evening in 1949.
Courtesy of Crane Cast.
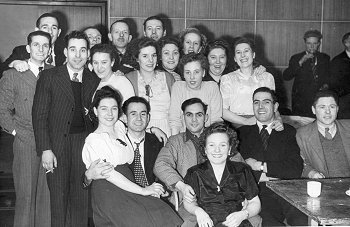
Another photograph of the event.
Courtesy of Crane Cast. |
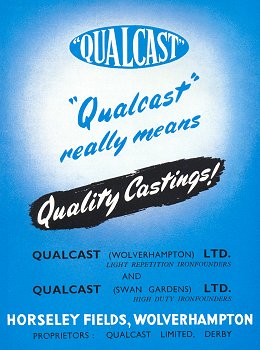
An advert from the mid 1950s. |
Production at the Crane Foundry concentrated on
light repetition work for the engineering industry. Grey
castings were produced, weighing from a few ounces to
half a hundredweight. Castings were supplied to vehicle
manufacturers, gas and electric cooker manufacturers,
hand tool makers, and lockmakers. Castings were also
made for electric motors, lawn mowers, sewing machines,
typewriters, washing machines, telephone equipment, and
conveyor rollers for the mining industry. The Swan
Gardens foundry opened in 1953 and produced larger
castings from 0.5 to 3 hundredweights for motor cars,
commercial vehicles, farm tractors, stationary engines,
electric motors, refrigerators, and domestic water
heaters. |
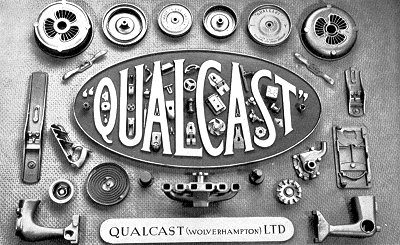
Some of the smaller castings made
at the Crane Foundry. |
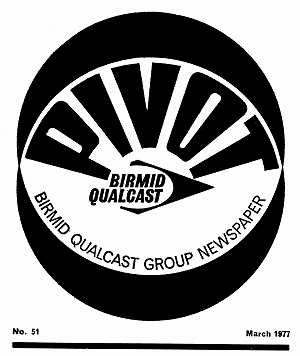
Things started to go wrong during
the recession of the 1970s when many of the country’s
foundries closed. Qualcast was hit hard by a series of
industrial disputes and the Swan Gardens Foundry lost a
lot of orders due to the recession in the tractor
industry, which resulted in the workforce being reduced
from 420 to 280. The work’s output fell from 500 to 290
tons per week and this proved to be unprofitable, with
the result that the Swan Gardens Foundry closed on 24th
June, 1972. Luckily the
Crane Foundry survived and the company decided that the
foundry's future could be secured by increasing sales to
mainland Europe. A 2,500 mile round trip to Sweden was
organised as a cost exercise to see if it would pay to
make regular deliveries to the continent. The trip also
included deliveries to existing customers to show that
the company meant business. |
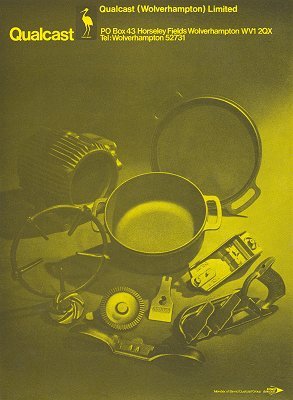 |
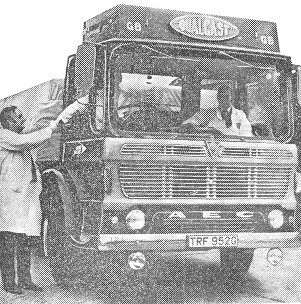
The lorry sets off on its 2,500
mile European trip.
General Manager R.M. Lackner shakes hands with driver
Arthur Lloyd and colleague Geoff Walker. Courtesy of
Crane Cast. |
The lorry left Wolverhampton on 23rd November, 1972
and took the ferry to Gothenberg in Sweden. After three
days travelling around the country visiting customers,
they took a ferry to Germany from where they drove to
France. After making deliveries to French customers they
returned to Wolverhampton via Dover. Qualcast also
produced a range of casseroles and frying pans that were
designed by Robert Welch. After some hard negotiating
and advertising the products were exported to America,
Australia, Denmark, France, Germany and Sweden. |
The lorry arrives at A-B
Vibro-Verken in Solna, Sweden.
Courtesy of Crane Cast. |
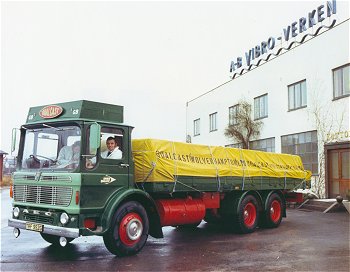 |
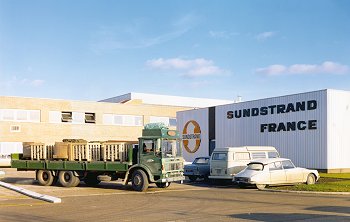
|
One of the deliveries in
France.
Courtesy of Crane Cast. |
 |
View the foundry in
Qualcast days |
 |
View some of the Qualcast
products |
By 1978 Crane Foundry employed around
600 people and produced 300 tonnes of castings per week.
The foundry specialised in intricate thin section
castings made to BS1452:1977 Grade 180 within a weight
range of 0.03kg to 35kg. Castings were made for the
automotive industry, gas cookers, multi-fuel stoves,
domestic appliances, and general engineering. |
Foundry closures continued and
most of the factories in the Qualcast group disappeared.
Crane Foundry itself was threatened with closure but
saved by the intervention of Managing Director Mr. Roger
Lackner, who purchased the unprofitable company. The
works were severely over-manned and a rationalisation
programme initiated. Unfortunately the redundancy costs
were so high that even with a healthy order book,
liquidation soon followed. |
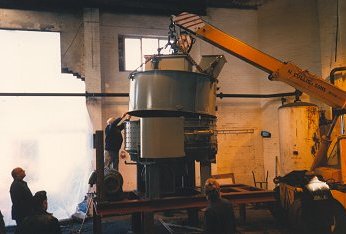
The installation of the new
cupolas in 1995. Courtesy of Crane Cast. |
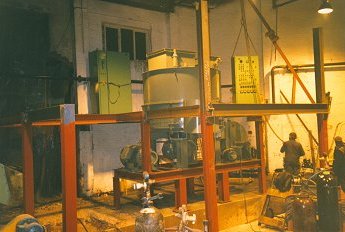
The cupola control equipment is
lifted into position. Courtesy of Crane Cast. |
|
Receivers were appointed in 1985
but Mr. Lackner managed to buy the company from the
receivers with financial backing from Crane’s two
largest customers, Stanley Tools and Brook Motors.
The new company was renamed Crane
Foundry (Wolverhampton) Limited with a workforce of just
over 130. |
The new company’s future looked
bright under the leadership of Roger Lackner and his son
Mark. A Disamatic automatic
moulding machine was installed to increase production
and the maximum weight of the castings increased to 100
kilograms. |
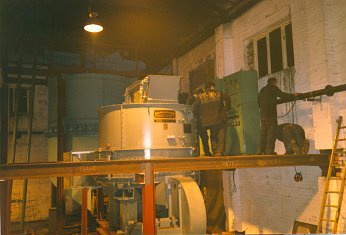
Examining the cupola control
equipment. Courtesy of Crane Cast. |
|
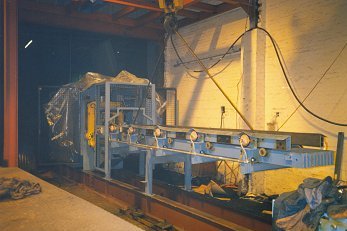
Installing the Disamatic moulding
machine in 1995. Courtesy of Crane Cast. |
|
Further improvements followed in
1995 when the company embarked on a 2.5 million pound
investment programme to ensure that the foundry was
technically and environmentally viable.
A second Disamatic moulding machine
was installed to double the work’s capacity and two 8
tonne per hour Dozamet cold blast cupolas with full fume
cleaning were added to increase iron production and
comply with the Clean Air Acts.
|
The cupolas are mechanically fed
with scrap metal, limestone and coke, and water-cooled.
The cupolas were designed so that each can work on
alternate days when the other is de-clinkered, stripped
of its clay lining and re-lined in readiness for use.
The tuyeres are fed by fan-blown air and the speed of
flow of the molten metal can be varied by changing the
air pressure. The temperature, air flow and water
cooling are precisely monitored by an electronic PLC
control system. |
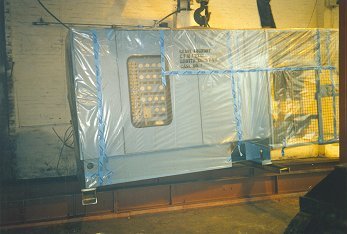
The Disamatic control panel is
lifted into place. Courtesy of Crane Cast. |
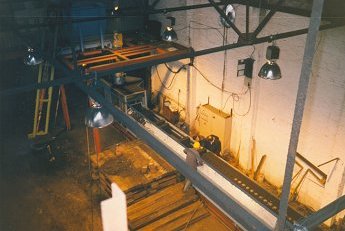
The Disamatic machine from above.
Courtesy of Crane Cast. |
A Birlec electric induction
melting furnace was installed as a reservoir for the
cupolas, which also allowed two grades of iron to be
used at the same time. The Disamatic moulding
lines can produce up to 300 castings per hour and the
foundry's automated track can produce 150 moulds per
hour.
|
The heavy moulding line is capable of 30 moulds per
hour and in-house facilities were set up for shell
cores, cold box cores, CO2 cores and a new
four tonne annealing oven. Box sizes are 600mm x 480mm
on the Disamatic lines, 660mm x 460mm on the automated
line and 760mm x 760mm on the heavy moulding line. The
castings vary in weight from 0.5kg to 80kg and grey iron
can be produced to BSEN 1561 Grades 180, 200, 220, and
250. |
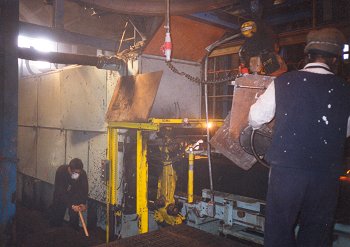
The Disamatic machine in
operation. Courtesy of Crane Cast. |
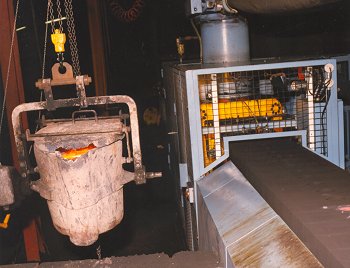
A fresh ladle of molten metal in
readiness for casting. Courtesy of Crane Cast. |
|
The Core Shop,
Fettling Shop, Dressing Shop, and the main foundry were
greatly improved and a steady stream of new customers
followed.
Sadly, even
after all of the investment the company remained
unprofitable and the workforce was reduced to 68. |
For a while Crane Foundry became part of British
Steel, but the foundry went into
receivership again on 21st
September, 2000. Luckily funding was found and the
company reformed itself as Crane Cast. |
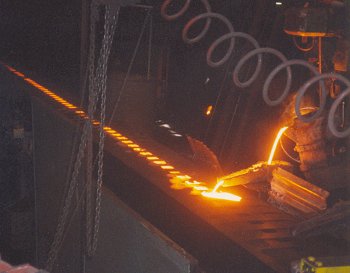
Casting on the Disamatic machine.
Courtesy of Crane Cast.
|
|
 |
View the foundry as it was
in 2005. |
Things seemed to be going well until
the company’s liabilities spiralled out of control. The
recent rise in electricity and gas costs, and the loss
of two of the company’s largest customers, meant that
the directors had no choice other than going into
liquidation in January 2006.The company and
workforce had fought hard to survive, but too many
things went wrong at once. A sad end for one of
Wolverhampton’s oldest companies.
I would like to thank Rebecca, Kevin and Mr. S.
Reacord of Crane Cast for all of their help in producing
this brief history. |
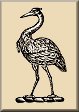 |
Return to
the museum |
|