By 1799 a small stone-built blast furnace was
working at Darlaston Green, which must have
formed part of the first iron works in the town. In 1826 Richard Bills a gunlock maker of Church
Street, established a furnace and foundry at Furnace
Lane, Lower Green, where Heath Road is today. He made
his stepson Samuel Mills a full partner on his 21st
birthday in 1826, and the company became known as Bills & Mills.
Richard died on 16th June, 1849, at the age of 72.
Samuel took over the company in February of that year. |
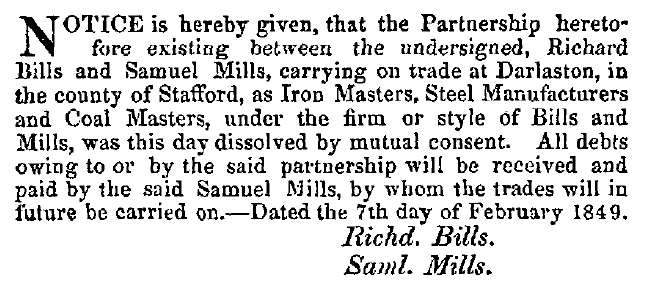
Before Richard's death, the
partnership was dissolved. From the London Gazette, 9th
February, 1849. |
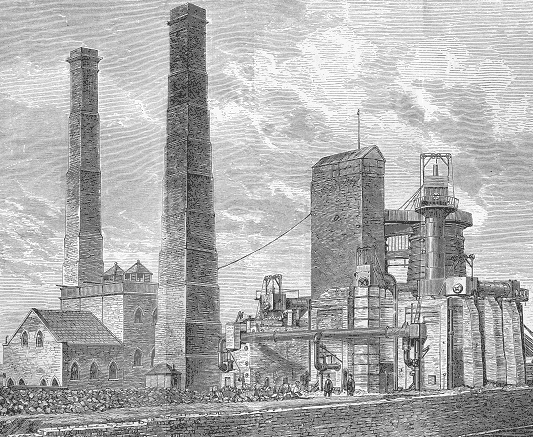 |
One of the blast furnaces. It
stood on the northern side of the canal, and is seen
here, as it was around 1870. |
By the 1850s the site covered over 55 acres, on both
sides of the canal. The southern part between the canal
and Heath Road consisted of two blast furnaces, extensive puddling furnaces,
cementation kilns, foundries, a vast metal processing
complex, and Brown's patent rolling mills.
To the north of the canal stood the oldest of the
three blast furnaces and several coal and iron ore
mines. This was one of the earliest, largest, and most
important iron and steel companies in South
Staffordshire, and had a name for good quality iron. The
company also owned a factory at Kings Hill. |
The furnaces were hand-filled from the top. The tall
brick charging tower on the left of the drawing contains an
overhead gantry, and two hoists to lift barrows of
burden up to the charging platform that ran around the
top of the furnace. Each barrow would have held around
15cwt. They ran on iron plate roads and had two sharp-tyred
wheels that could cut through obstructions that had
fallen onto the plate roads, such as pieces of coke.
The barrows were hand-filled in the ore and coke
pens, and dragged to the bridge of the hoist where the 'cager'
would load the full barrows onto the hoist, and unload
the empties. To start the hoist he rang a bell as a
signal to the engine man who operated the steam engine
that powered the hoist.
At the top was a 'filler' who wheeled the barrows to
the throat of the furnace, lowered the bell that sealed
the top, and emptied the contents into the furnace. He
would then close the bell. At night the furnace top and
the surrounding area was lit by the waste gases burning
at the 'monkey', a bypass pipe on top of the bell. |
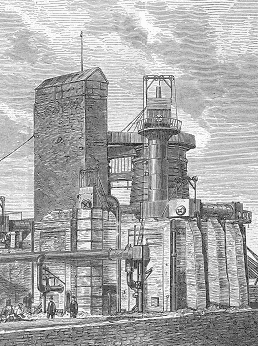 |
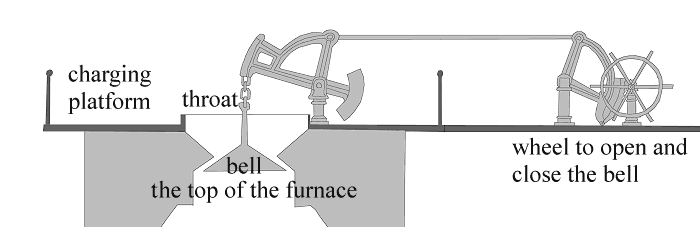
Furnace charging mechanism. |
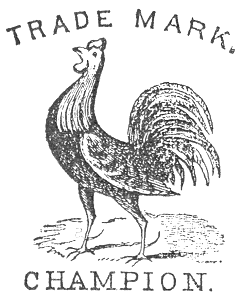 |
The furnaces had a hot blast that was produced by a
steam engine. The blast passed through large cast iron
pipes that went through brick, coal fired, heating
stoves. Two of them (one on either side of the furnace)
can be seen in the top drawing. In between to the two
chimneys on the left of the drawing is one of the engine
houses. It contained two 70 hp. beam blowing engines,
one of which also operated the hoist. The site had a
horse-drawn narrow gauge tramway. Slag was poured into
slag ladles, which were hauled by a team of three horses
to the tip. Each ladle had a tipping mechanism that was
operated by a quick release shackle.
All sizes and shapes of iron plates and bars were
produced including boiler plates, hoops, strip, tank
plates, rails, wire rods and small sizes of rounds and
squares. All kinds of steel were made using the
cementation process and these were well known and
appreciated in the market. |
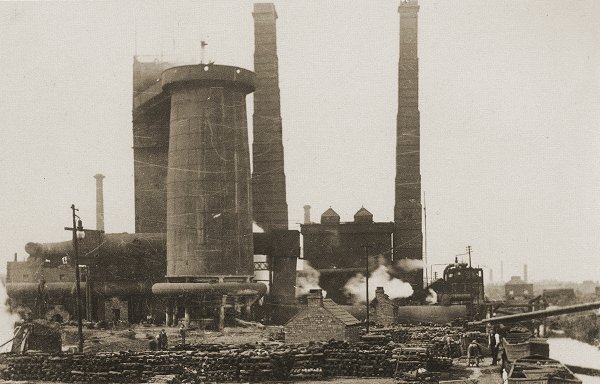
The charging tower, blast furnace,
engine house, and heating stoves. From an old postcard.
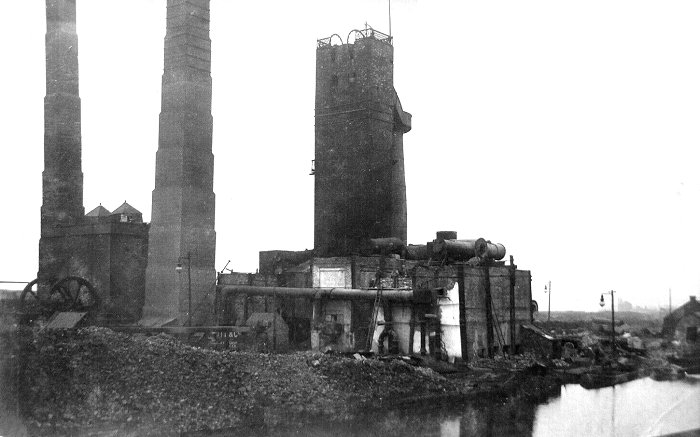
A view from the other side of the
furnace. Also from an old postcard.
Samuel Mills became a
wealthy man, thanks to the success of Bills & Mills,
and the earnings from his many collieries in the
area. In 1855 he leased the Essington Wood Colliery
which was situated on the western side of Bursnips
Road, Essington. He purchased the colliery in 1860
and ran it as a separate business alongside Bills &
Mills. The company eventually employed around 2,000
people.
On 3rd August, 1863 Samuel Mills sold the ironworks,
collieries, and plant to Samuel Lloyd, Joseph Foster
Lloyd, Wilson Lloyd, and William Henry Lloyd, for a
quarter of a million pounds, which led to the formation of the Darlaston
Steel and Iron Company. |
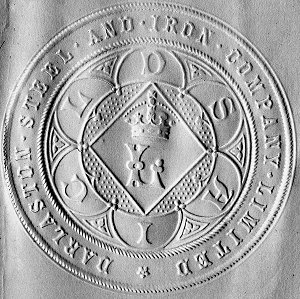
The company's seal.
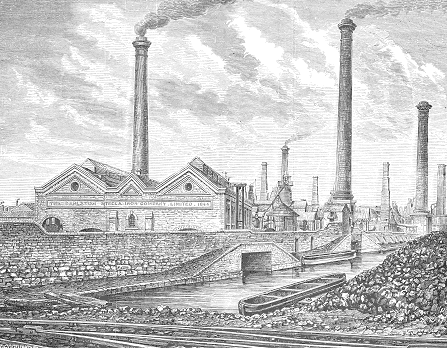
The Darlaston Steel &
Iron Company's works between the canal
and Heath Road. |
Mr. Sampson Lloyd of Wassel Grove, Stourbridge became company Chairman with
Mr. Francis Lloyd as Managing Director. The business was
re-registered as the Darlaston Steel and Iron Company on
7th November, 1872 and rapidly expanded. The number of puddling furnaces grew
to 43 with 17 reheating furnaces, 8 rolling mills, a
drawing-out forge, 63 steam engines, including the three
70h.p. blast engines for the blast furnaces, and rails,
which
were laid to all parts of the works. The rolling mills required very little manual labour
and could automatically roll enormous quantities of
strip in great lengths using Brown's patent process,
where the strip being rolled is automatically passed
through a second pair of rolls to complete the work.
There were two of Casson's patent puddling furnaces
and a Griffiths mechanical puddling machine, which worked well
together. The company's collieries and mines, mining a 12
yards thick seam, covered 850 acres, 350 of which were
freehold and 500 leasehold. Some of the seams produced
what was called "Brooch" coal and others "Heathen" coal.
There were also ironstone mines thanks to thick seams of
"Gubbin" ironstone, "New Mine", Whitestone", and "Blue
Flats" ore.
The iron industry as a whole felt the effects of the
depression between 1875 and 1886 during which many blast
furnaces, forges and mills closed. The Darlaston Steel
and Iron Company was also badly effected and closed in
1877 as can be read in the announcement below:
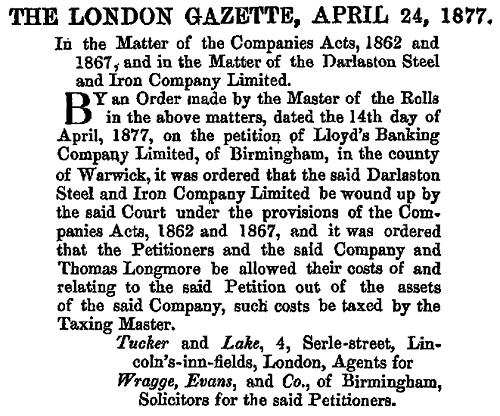 |
Another of the blast furnaces.
After the closure, Francis Lloyd brought a disused
timber yard at James Bridge, and established a small
foundry which eventually became F. H. Lloyd's James
Bridge Steel Works.
In 1877 the Darlaston Coal and Iron Company
(registered on 19th September, 1877) took
over the Darlaston Steel and Iron Company's works
with Ironmaster John Jones in charge. In 1878 he was
replaced by E. Gem. At the same time A. E. Wenham became company
secretary. The company also ran the Essington Wood
Colliery which rapidly expanded with the opening of
two new shafts, a coal screening plant, and a
railway siding.
In 1882, during the depression in the iron trade, the
Darlaston Steel & Iron Company went into liquidation
and was auctioned at Wednesbury Town Hall on 27th
February, 1882. The coal
company decided to concentrate on the mining
operation at Essington, where in 1891 the colliery
became Holly Bank Colliery, with the formation of
the Holly Bank Colliery Company Limited.
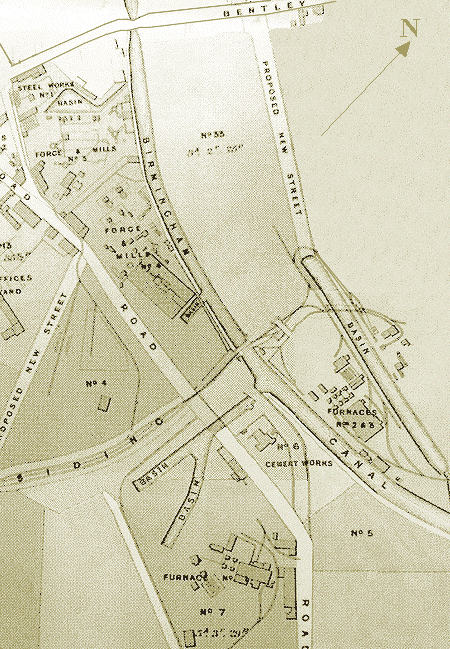
The 1882 sales plan of the
works.
William Henry (Harry)
Richards, grandson of
Charles Richards of Imperial
Works, mentions the
following in his memoirs:
Lot number 4 was bought
by George Braithwaite Lloyd,
who bought debentures from
the old iron works. In turn
it was bought by Thomas Tolley, of 47 Broad Street,
Bilston, for £5,000 on 7th
November, 1882. On 20th May,
1884, Mr. W. H. Bostock of
Burslem bought a one third
share for £5,000, as did
Richard Mentz Tolley. They
traded as Tolley, Sons &
Bostock. |
|
The two newer iron-bound brick blast furnaces on the
northern side of the canal continued to be used.
They had a charging stage, lift, and hot air oven
43ft. long, 18ft. wide and 23ft. high. In 1891 the part
between Heath Road and the canal was acquired by Charles
Richards for his Imperial bolt and nut works.
In 1900 the construction of a new steel-clad
blast furnace began. It replaced the two stone-built
furnaces on the northern side of the canal, and came
into operation in 1902. By 1905 two Cowper blast
heating stoves had also been added. The old heating
stoves were kept as a stand-by for use in
emergencies, until about 1920 when they were
demolished. By the early 1900s the local iron ore
would have been depleted and so scrap iron must have
been used instead.
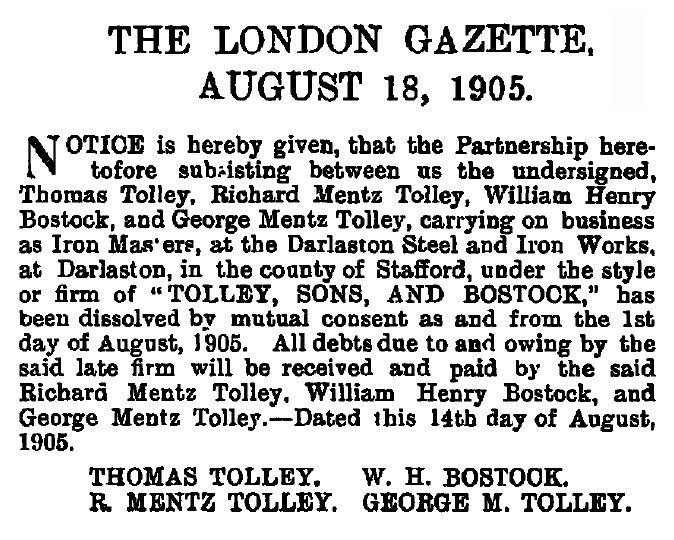
In 1905 Thomas Tolley
resigned.
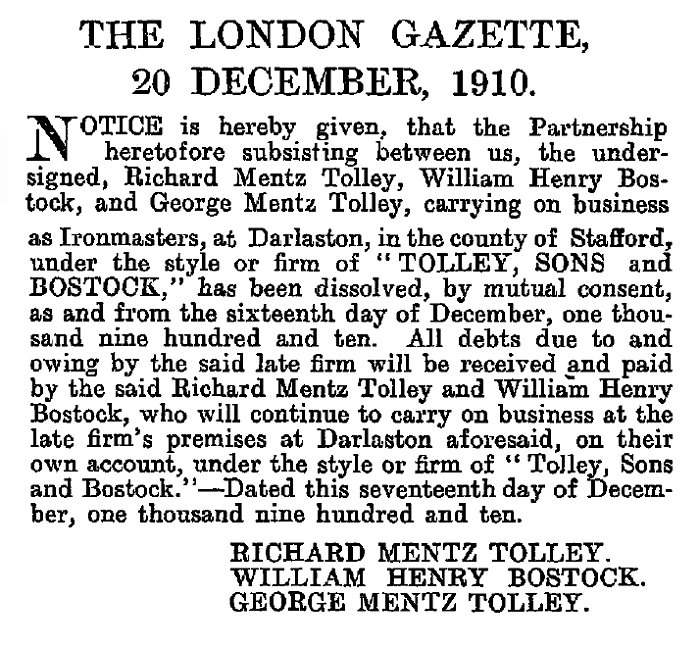
In 1910 George Mentz Tolley
sold out for £3,288..
In 1910, W. J. Foster joined the company as a foreman
and by 1914 had become works director. Around the
end of the First World War Rubery Owen & Company
built and installed a new blast plant at the works
with a double bell top, inclined skip charging, and
a travelling overhead crane over the ore and coke
pens. The ambitious scheme was never completed
because the demand for pig iron fell. The furnace
remained until the late 1930s
when it was dismantled for scrap. Around the same
time the last surviving charging tower was
demolished.
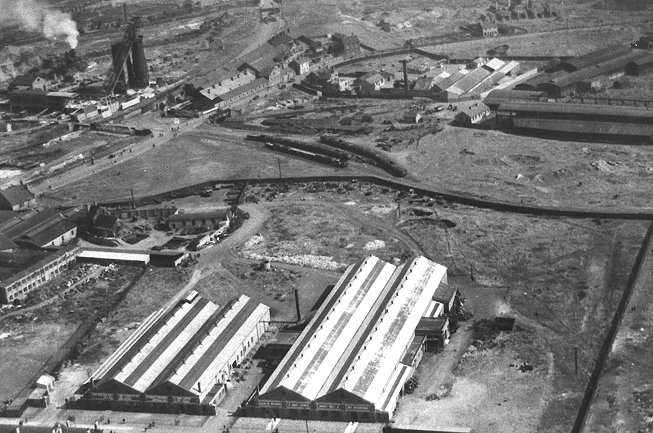
An aerial view
showing the furnace built by Rubery Owen
& Company. From the collection of the
late Howard Madeley. |
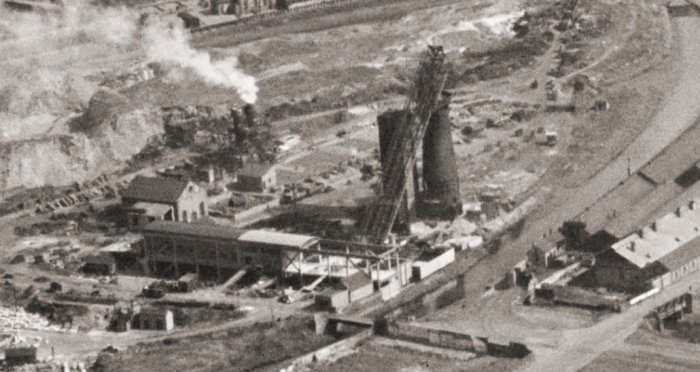
Another view
of the furnace built by Rubery Owen &
Company.
On 28th August, 1923, F. W.
Cotterill Limited, then part of
G.K.N. bought Tolley Sons & Bostock
for £16,500 in order to gain control
of their steel supplier. The firm
then became Tolley Sons & Bostock
Limited. The factory carried out all of G.K.N.'s puddling
and rolling operations for their nuts, bolts and
fastenings department, but by then the plant was
very old fashioned and so G.K.N. eventually sold
the works. |
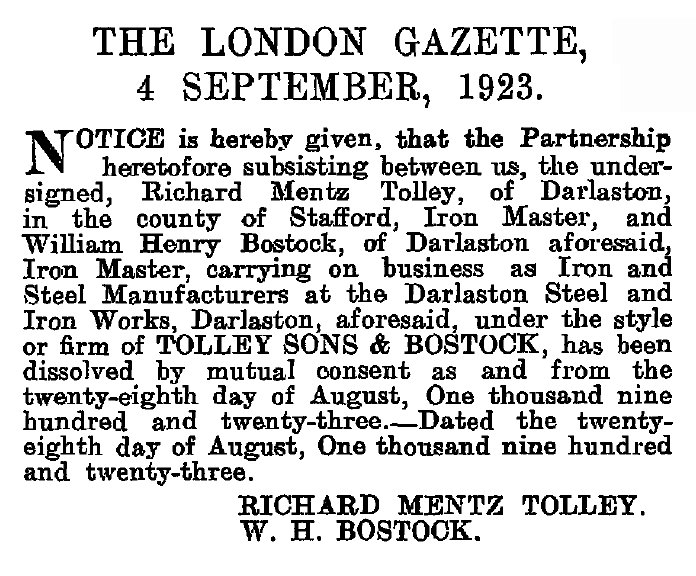
GKN decided to liquidate Tolley Sons
& Bostock Limited in 1933:
|
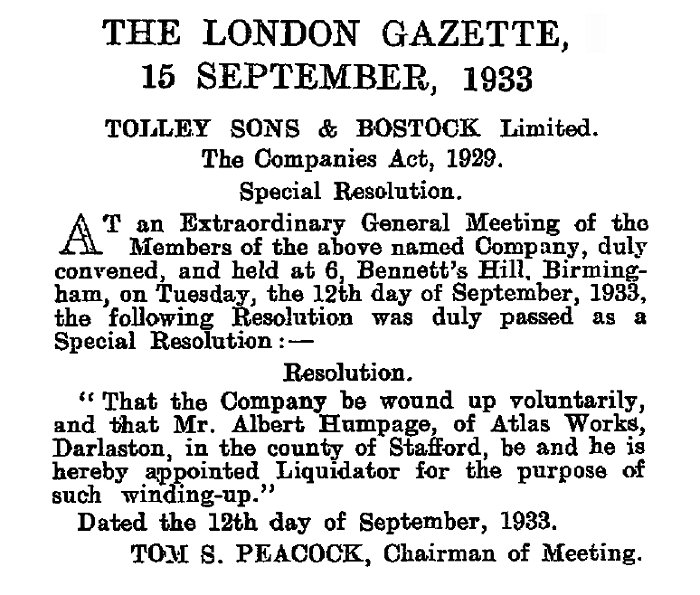
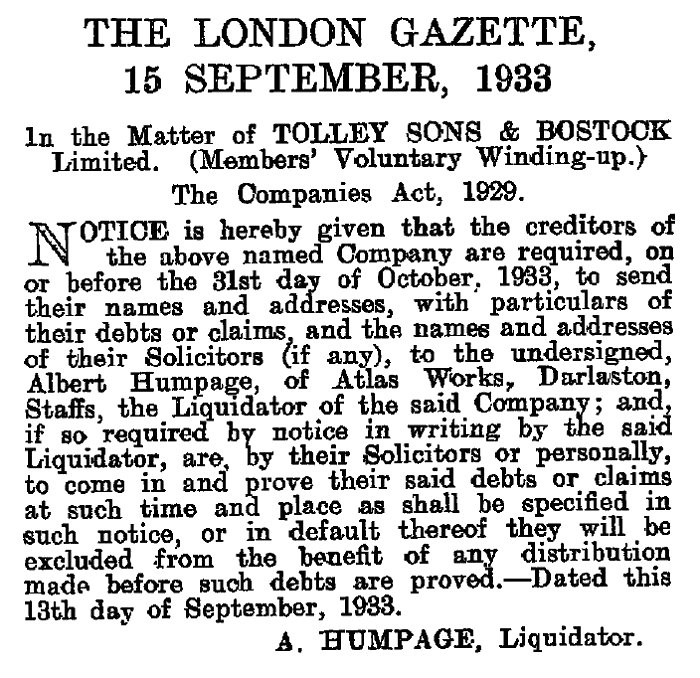
William Henry
(Harry) Richards,
grandson of Charles
Richards of Imperial
Works, recalls the
Tolleys in his memoirs,
written in the early
1960s: I do not
remember Mr. Thomas
Tolley, but he lived at
the top of Victoria
Road, opposite the
Parish Church I believe.
He was a boiler maker
by trade and used to get
inside his boilers and
do his own repairs on
Sunday mornings. Mr. Bostock used to be a
smart man in his youth
and lived in Avondale
Road, Wolverhampton and
was a Good Templar at
one period in his life.
Richard Tolley was a
'cocky' individual, he
married Nelly Horton,
daughter of Enoch Horton
who built The Grange at
Bescot.
George Tolley was a
good practical man, but
drink ruined him. He
used to have a bottle of
stout for his breakfast.
He lived at The Beeches,
Bescot, which I believe
is now a dairy. At one
time he lived at the
White house, now part of
E. C. & J. Keays.
In the early days
they used to have a
small loaf and a quarter
of corned beef for their
dinner.
I remember both
Tolleys well and Mr.
Bostock. After George
Tolley was paid out, he
became Night Manager for
a time on condition he
left the counter I
believe. He went to live
in Alexandra Road, Penn.
His son was a good
'plucked un', he came to
the works and did his
stuff on the rolling
mills in clogs and
moleskin trousers. I
used to bike home with
him sometimes.
George and his family
went to Canada and his
son joined the forces in
the First World War and
came to England again. I
haven't heard of him for
years.
Richard went to
live at Windsor, but
both he and W. H.
Bostock have passed
away. There used to be a
good school of 'em, my
uncle William Richards,
owner of the foundry,
now Wilkins and
Mitchell, George Wiley,
George Tolley, and my
uncle Silas, father of
Fred Richards of Nuts
and bolts Limited, and
C. P. Robinson, the
proprietor of
D. Robinson & Sons, the
oldest firm in the town.
This was the forerunner
of Nuts & Bolts Limited.
I have heard my
mother say that once
when the Tolleys had a
breakage of a large
wheel, old Mr. Tolley
came into the shop and
cried when he said he
would be ruined.
I have to thank Robin
Richards for the copy of
Harry Richards' Memoirs. |
|
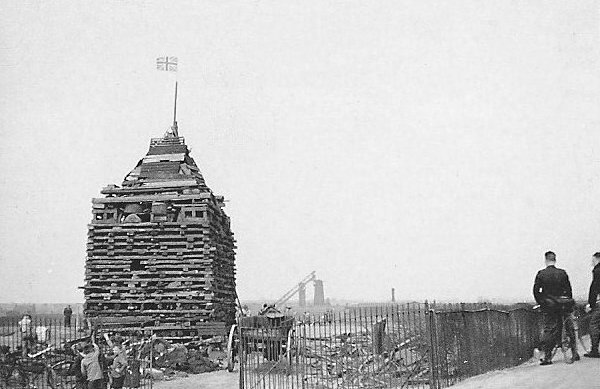
A photograph of
the bonfire on The Flatts to celebrate
the Coronation of King George VI on 12th
May, 1937. The furnace and charging
tower can be seen in the middle
distance. Photographed by the late W. J.
Ashmore. Courtesy of John & Christine
Ashmore. |
|
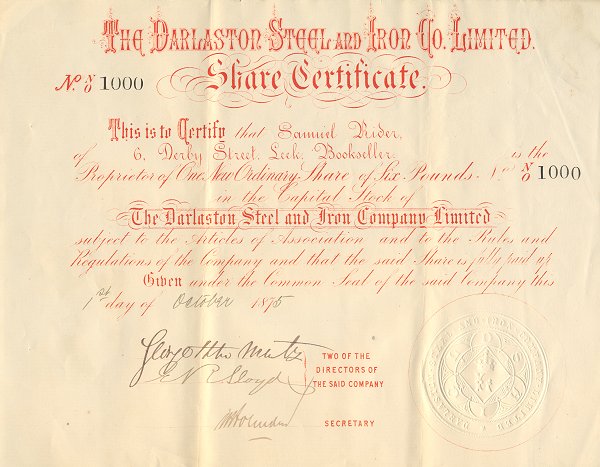
A share certificate dated October 1875.
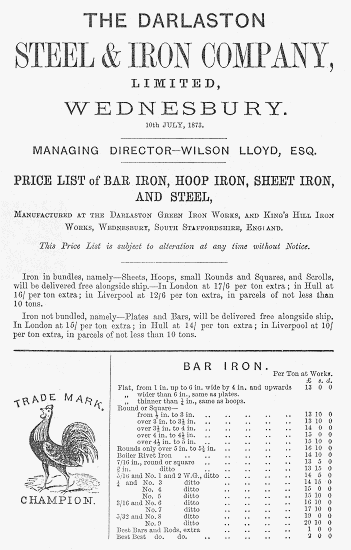
The first page of the July 1873 price list.
The site was sold to Bradley and Foster
Limited, who were there for many years. |
|
|
Read about Bradley & Foster
Limited, the largest producer of refined pig iron in the
country |
 |
|
|
Samuel Mills and his
familyThe family lived in Darlaston House on
the western end of what is now Victoria Park, where
Samuel died in 1864. The house and its surrounding land
occupied the modern Rectory Avenue, the Post Office, and
the area behind Pardoe's Cottage, where the dovecote
still stands. In the 1920s when foundations were dug for
the war memorial in Victoria Road, the ground gave way
to reveal part of the cellars of Darlaston House. The
workmen found a number of bottles of wine, much of which
was drunk there and then, although some bottles of
parsnip wine did find their way to The Green Dragon in
Church Street, were they went on sale. The original All
Saints Church in Walsall Road was built in 1872 in
memory of Samuel Mills, who died in 1864.
Jane Mills,
one of Samuel's daughters, was a public spirited lady
who did much for the town. She founded the Jane Mills
Institute in Rectory Avenue, in connection with the
Parish Church to help the needy women and girls of the
town. The building housed the institute and was given to
the town when Jane moved to Whitton Court, Whitton, near
Ludlow, in the late 1890s. The institute, later known as
the "Mothers Meeting and Girl's Institute" eventually
became a clinic and later "The Sons of Rest". The
building is now a family home.
Rough Hay Furnaces
Rough Hay Furnace & Foundry, Darlaston Green, was
founded on 27th August, 1842 by Edward Addenbrooke
Addenbrooke of Kingswinford, Thomas Smith of Cheltenham,
and Charles Pidcock of Worcester. The firm was managed
by Edward and two of his sons, John and George
Addenbrooke. The firm traded as Addenbrooke, Smith & Pidcock,
coal and iron
masters.
The family was descended from the Addenbrookes of Wollaston
Hall, Stourbridge. Their father, Edward Addenbrooke, and
grandfather, John Addenbrooke Homfray were both
ironmasters.
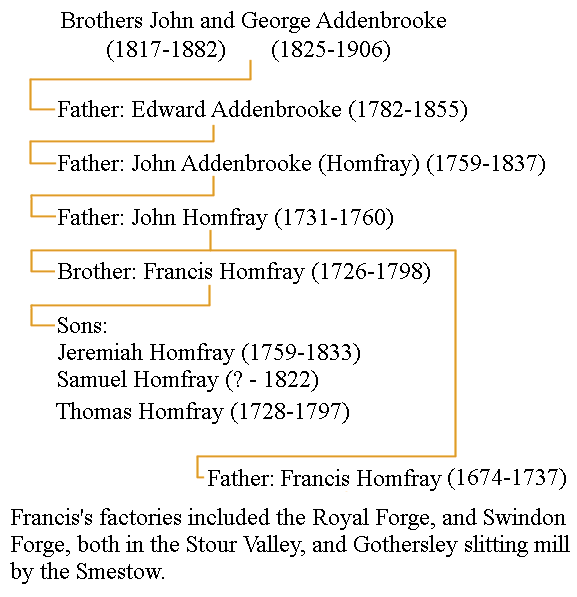
Family background
John and George Addenbrooke were descended from a
long line of ironmasters going back to the early 18th
century. It started with their great, great grandfather
Francis Homfray who owned two forges, and a slitting
mill in South Staffordshire. The family lived in style
at Wollaston Hall which stood on the western side of
Stourbridge.
John and George had family links with the huge iron
industry in South Wales. Their great grandfather's
brother Francis Homfray had three sons, Samuel, Thomas
and Jeremiah. Samuel and Thomas founded a large iron
works at Penydarren, on the banks of the Morlais Brook.
They also built a mansion nearby called Penydarren
House. Samuel is best remembered as the promoter of
Richard Trevithick's Penydarren locomotive, the
first locomotive in the world to run successfully on a
railway. The test took place on the Merthyr Tramway
which ran for 9½ miles from
Merthyr to Abercynon. It managed to haul five
wagons carrying ten tons of iron, and seventy men, at a
speed of five miles an hour. Samuel was one of the main
promoters of the Glamorgan Canal, and founder of the Tradegar Ironworks. He became High Sheriff of
Monmouthshire in 1813, and in June 1818 became Member of
Parliament for Stafford. His brother Jeremiah was one of
the founders of the Ebbw Vale Ironworks.
In 1787 John and George's grandfather John
Addenbrooke (Homfray) and his cousin Francis obtained a
lease for Lightmoor Ironworks which had two furnaces,
and stood roughly halfway
between Dawley and Ironbridge. In 1797 they obtained a
lease for the Lightmoor coal mines, and also ran the
Little Dawley coal mines. They operated the Little Dawley
mines until 1822, and Lightmoor Ironworks until 1839.
Francis was also a partner at Calcutts Ironworks near
Broseley, Shropshire, where amongst other things he made
cannons for the
American Civil War. As well as blast furnaces, he also
owned blade mills, slitting and plating mills, finery, chafery, balling furnaces, rolling mills, and forges.
John Addenbrooke's surname was originally Homfray. In
1792 he had it changed to Addenbrooke, his mothers'
maiden name.
John and George were born in Kingswinford, and had
three brothers and six sisters. Their father was Edward
A. Addenbrooke (1782 - 1855) who married Emma
Pidcock (1794-1875) in January 1815 at Old Swinford. She
came from Coalbourne Brook, near Stourbridge. In 1851
they were living in Dudley Road, Kingswinford and had
eleven children:
Edward, John, Emma, Elizabeth, Henry, Emma, George,
Thomas, Laura, Frances, and Henrietta.
John was born in 1817, and George in 1825.
1851 census: Dudley Road,
Kingswinford:
Edward A. Addenbrooke (age 69 born
Oldswinford), Iron Master employing 300
men.
His wife Emma Addenbrooke (age 57 born
Oldswinford).
Children:
Henry Addenbrooke (age 29 born
Kingswinford), Solicitor.
Priscilla Addenbrooke (age 21 born
Kingswinford).
George Addenbrooke (age 25 born
Kingswinford), Iron Master.
Thomas Addenbrooke (age 24 born
Kingswinford), Solicitor.
Laura Addenbrooke (age 22 born
Kingswinford).
Three servants. |
|
The family's ironworks and collieries in
Darlaston and the surrounding area
For several
years Edward A. Addenbrooke and three of his
sons, Edward, Henry, and John ran the Moorcroft Ironworks at Bradley,
which had two furnaces, and produced around 100 tons of
iron each week. They also ran Moorcroft Colliery and
Bradley Hall Colliery, both linked to the ironworks by
tramways. The businesses were sold in 1841. Edward A. Addenbrooke
is listed as the owner of Brickfield Mine at Rough Hay,
Darlaston, in the list of owners and occupiers that
accompanied the 1843 tithe map of Darlaston. The list
also includes details of the many fields that he owned
at Rough Hay, along with several pieces of land beside
the canal, known as Canal Bank, Rough Hay Bridge and
Long Bridge Piece.
Their ironworks at Rough Hay, Darlaston,
founded on 27th August, 1842, became very successful.
The brothers developed and patented a system for
extracting hot combustible gases from the top of the
furnaces, and used them to heat the air for the blast,
and to generate steam for the blast engine, which also
operated the hoist to lift the coal and iron ore etc. to
the top of the furnace. This technique enabled iron to
be produced more quickly and cheaply, because the
furnace remained at full operating temperature during
the blast.
|
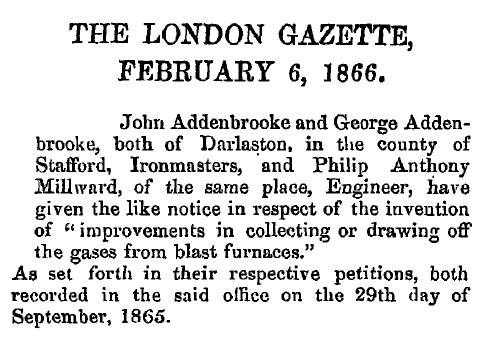 |
They also developed calcining kilns in which
the iron ore was heated by coal fires to heat the iron
ore before smelting. The process, which removed carbon
dioxide and water from the ore, and oxidised it, was
much cheaper to run than the traditional method, in
which the ore was calcined in open mounds. |
George Addenbrooke married Matilda Louise Westwood at
Wombourne in 1854. They lived at Greenhill House in
Wombourne, and their son George Leonard Addenbrooke,
born in 1860 had a distinguished career in electrical
engineering. John Addenbrooke married Elizabeth, and they had
eleven children. In 1851 they were living in Birmingham
Road, Bromsgrove, and by 1871 had moved to The Elms,
Sutton Road, Walsall. In the 1881 census their address
is given as Waterloo Terrace, Newhampton Road,
Wolverhampton.
After 1855, when Edward Addenbrooke died,
John and George ran the business on their own. Addenbrookes were Darlaston's second largest employer, until the
business closed at the beginning of 1882,
putting over 1,000 people out of work. They had three
blast furnaces at Rough Hay, all traces of which have
now disappeared. Their products included bar, rod and
sheet iron.
Addenbrooke, Smith & Pidcock also owned Rough Hay
Colliery, one of the largest coal mines in the area,
employing 500 people.
John and George owned many
collieries in the area, including a number at Leabrook
in Wednesbury, and the Bedworth Coal and Iron Company
Limited in Warwickshire.
|
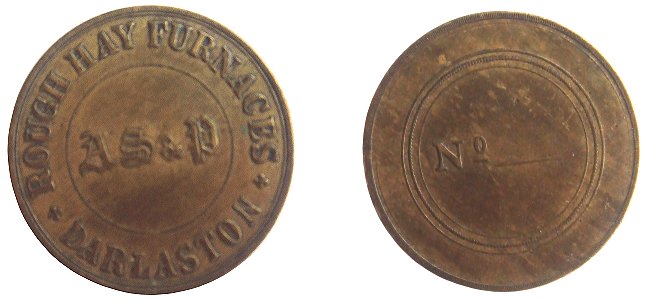
Both sides of an Addenbrooke, Smith & Pidcock
token. Courtesy of
George is remembered by the street that
is named after him; Addenbrooke Street. He was a founder
member of the Darlaston Local Board (the forerunner of
the council), a member of the Institute of Mechanical
Engineers, and churchwarden at St. George's Church. In fact
the Addenbrooke company gave the land on which St. George's
vicarage was built. He died on 20th May, 1906 at the
vicarage in Chalford, Stroud and was buried at St.
George's Church, Darlaston.
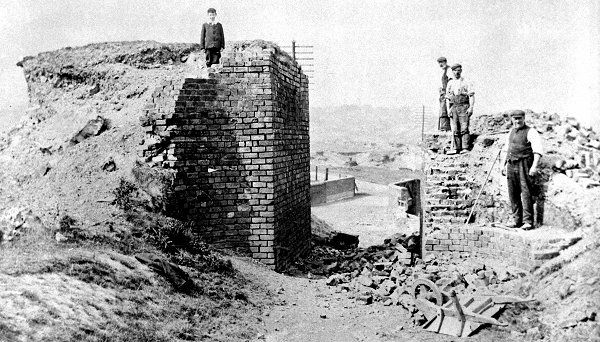
The photograph shows
the demolition of a bridge and tramway in
Rough Hay. The opening under the bridge was
known as "The Khyber Pass" and is
commemorated today by the street named
"Khyber Close". The old tramway must have
been the one that ran between Addenbrooke, Smith & Pidcock's
factory, Rough Hay Colliery, and a canal
basin. The dirt track under the bridge is now
Hall Street, and the bridge beyond crosses
another tramway that ran between two of the
coal mines. The view looks southwest towards
the Dudley-Sedgley ridge. |
A map showing the
location of "The Khyber Pass" and Addenbrooke, Smith & Pidcock's
factory, which stood roughly at the junction
of Rough Hay Road and Hall Street.
At each end of the
lower tramway was a winding machine.
There were many
abandoned mine shafts and spoil heaps in the
area, which would have looked very different
to today's flat landscape.
The council must
have had an immense task clearing the area
when the pre-war council estate was built. |
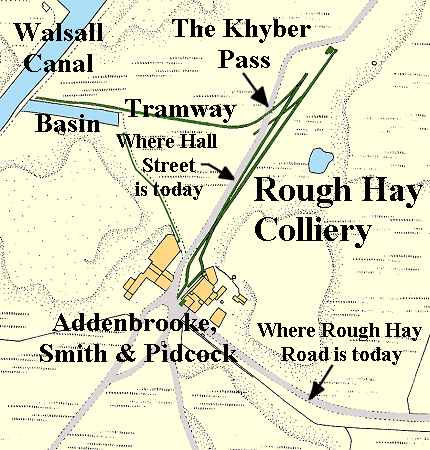 |
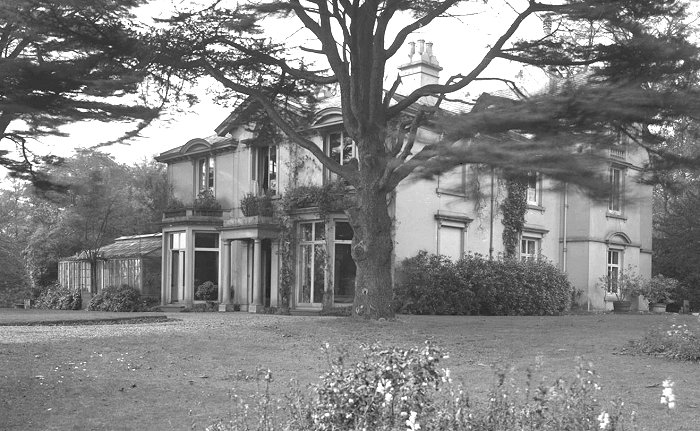
George Addenbrooke's lovely
home, Greenhill House, in Wombourne.
The Albert Works and Moxley Iron
Works The Albert works were built in 1827
and run by David Rose. The Moxley Iron Works were
founded by brothers Daniel and David Rose in 1830.
Daniel retired in the early 1840s and the younger David
ran both of the works. The works produced iron forgings
and charcoal sheet iron of all kinds that was used for
such things as boiler plates and gasometer sheets.
Galvanising and corrugating were carried out on a large
scale at the works and all kinds of bars including small
rounds and fancy iron were produced. Other products
included pan and tank plates, galvanised and corrugated
sheets, and pig iron. The Victoria Works, founded by
William Molineaux and James Jordan were also on the site
producing strip iron for such things as locomotive and
boiler tubes. |
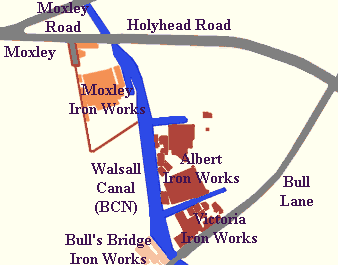
The location of the works. |
Two blast furnaces were added in the 1840s and could
turn out 20,000 tons of pig iron annually. David Rose owned a number of mines in the area and the
site included a sand pit were sand was dug and sold for
use in blast furnace and mill furnace bottoms. The clay
from some of David's mines produced high quality fire
bricks and these were one of the company's many
products. The mines also contained sufficient coal to
supply the works for 20 years. By the1870s there were 40
puddling and ball furnaces, 5 sheet mills, 1 plate mill,
1 bar mill, and one hoop mill. |
Samuel Griffiths included the following description
of the iron works in his 'Griffiths’ Guide to the Iron
Trade of Great Britain', published in 1873: |
The Albert and Moxley Iron Works
The former of these works
were built twenty-one years ago, and have since
been carried on by Mr. David Rose. The Moxley
Works, which were formerly carried on by Messrs.
Daniel and David Rose, were founded in 1830, but
on the occasion of Mr. Daniel Rose retiring from
business a few years ago, the whole of the
property was acquired by his youngest brother,
Mr. David. These works are justly celebrated for
the manufacture of use iron forgings and
charcoal sheet Iron.
The Victoria Works are
famed for the manufacture of all kinds of strip
iron, notably that for locomotive and boiler
tube purposes. The Albert Works, like Mr.
William Rose of Batman's Hill, stand well in the
market for plates and sheets, and the firm have
a good old connection with engineers and
machinists at home and on the continent of
Europe. Two blast furnaces have recently been
built here on most modern principles, and
acknowledged to be the finest plant in the South
Staffordshire District, and capable of turning
out 20,000 tons of pig iron per annum.
Mr. Rose has extensive
galvanizing works here, and carries on the trade
on the same premises to a large extent. Although
Mr. Rose is an old ironmaster, his judgment in
mines is very sound. On more than one occasion
he has purchased valuable mineral property in
the Black Country, and sold it at a large
profit.
It may be interesting to
note that near the works is a valuable sand
mine, largely used for blast furnaces and mill
furnace bottoms. It will thus be seen that
whilst the sand in being excavated forms a nice
little revenue, it is a valuable adjunct to the
works for the deposit of cinders and ashes. The
mines of coal and ironstone here, and at an
adjoining colliery of about 100 acres in extent,
are also very prolific. Clay for the manufacture
of fire-bricks is also raised, and the quality
is very superior. It is estimated that there is
sufficient coal for the supply of the works for
at least twenty years.
This is a most unique and
valuable property, for Mr. David Rose, of
Moxley, digs his own coal, sand and fire clay,
makes his own pigs and fire-bricks, puddles his
own iron, makes and galvanizes his own sheet
iron, and, we believe, raises a large portion of
the ironstone to make the pigs. We can safely
say there are no other works in England, or the
world, which can boast of the same products and
advantages on one and the same spot, stretching
over an area of comparatively only a few acres
of ground.
The works, which are
connected with the London and North Western
system, are entirely surrounded with a high
brick wall, and are exceptionally convenient and
well laid out. In all there are 40 puddling and
ball furnaces, 5 sheet mills, 1 plate mill, 1
strip mill, 1 bar mill, and one hoop mill. The
pig iron made here is good. Indeed all the iron
made at the Moxley Works, including their
galvanized sheets, stands high in the London
market. |
|
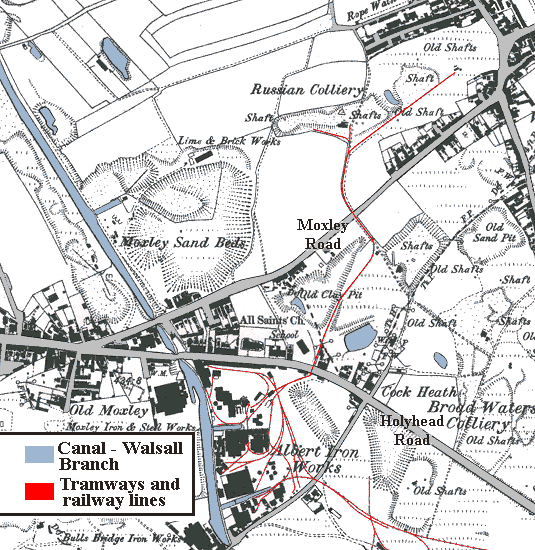 |
A map based on the 1885 O.S. map showing the many
tramways connecting the iron works to the coal mines,
and sand and clay deposits.
The railway line in the bottom
right hand corner joins the London & North Western
Railway's Darlaston Branch, near the junction of
Holyhead Road and Portway Road. |
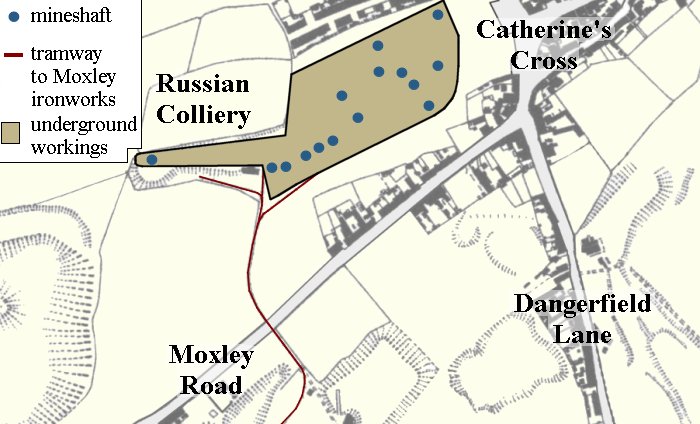
A plan of the Russian
Colliery. |
The Russian Colliery was founded and operated by
the Rose family. I first came across the name
Russian Colliery as a child, and have since been
puzzled by the name. I remember playing on the spoil
heap as a child, at the top of Woods Bank Terrace.
At that time the two shafts next to Shaw's scrap
yard were still visible. They had been capped, but
were starting to subside a little. When my mother
was a child the shafts were still open, and she
remembered throwing stones into them and listening
for the splash as they landed in water at the
bottom, far below. The puzzle about the name now
seems to have been answered. One of the descendents
of the Rose family is a geneticist who has been
analysing his own DNA. It seems that the family is
of Russian or Ukranian Jewish origin. He has matched
his DNA to members of the Rosenzweig family, so at
some point in time the British members of the family
changed their name to Rose. Which is presumably why
it was known as The Russian Colliery. |
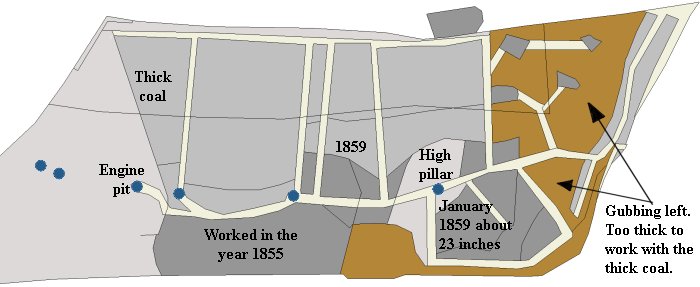
Another plan of the colliery,
based upon a contemporary diagram. |
There were fifteen shafts in all. The colliery
worked from around 1855 until sometime after 1870.
There was thick coal, 4.42 metres in thickness and
18 metres deep. Below this was heathen coal, 0.76
metres thick and 31 metres deep. There was also 'new
mine' coal 4.15 metres thick and 68 metres deep,
along with ironstone, 1 metre thick, and 43 metres
deep. So the site was very productive. |
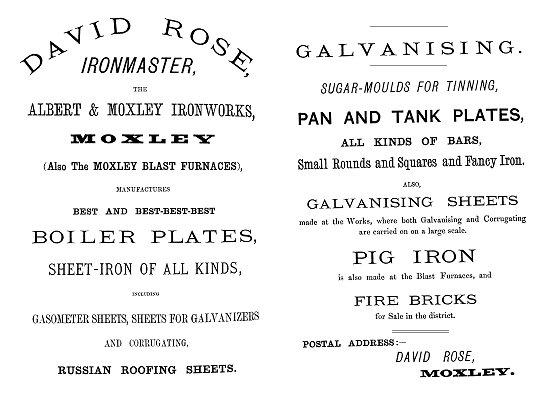
An advert from the early 1870s.
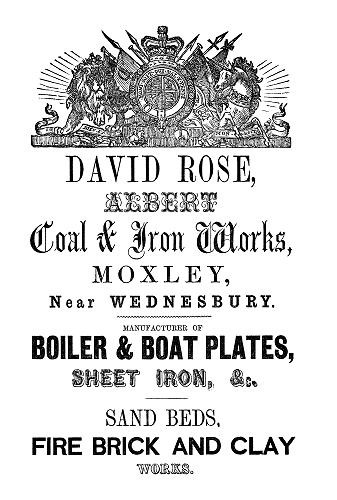
An advert from 1861. |
Victoria Ironworks was acquired by William Henry Wesson
in 1898 and he ran the works under the name of Wessons.
William died in 1936 and is buried in the graveyard at
All Saints' Church, Moxley.
Wessons became known as Ductile Wesson, a part of Niagra
LaSalle (UK) Limited.
|
|
Read the story
of the Rose family and
their ironworks at Moxley |
 |
|
|
In January 2009 the company announced
that the future of the factory was in doubt,
putting around 150 jobs in the balance. A
further announcement, made in February,
confirmed that the factory would close by
the end of the year, and 63 jobs would
go by the end of April. The factory, which
covered the site of both the Victoria Ironworks
and the Albert Ironworks was demolished in 2011. A large scrap yard and housing
estate now occupies the site of the Moxley Iron Works. |
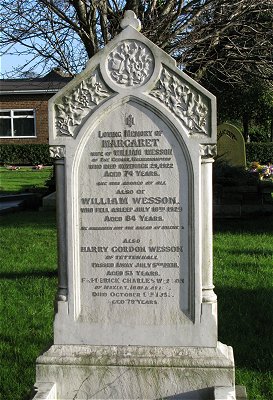
William Wesson's grave
at Moxley. |
Bull's Bridge Iron Works
Bull's Bridge Iron Works were situated in Bull Lane,
Moxley, next to Bull's Bridge on the Walsall Canal. They
were owned by E. Cresswell and Sons, and put up for sale
in November 1859.
The factory covered just over one
acre and included eleven puddling furnaces, a bar mill,
twelve other furnaces, a large cinder kiln, and a 25 hp.
steam engine to drive the machinery.
Adjoining the main
factory was a double office, a smith's shop, a
store room, stable and coach house.
The site was acquired by William Molineux & Company, and
listed in 'Griffiths' Guide to the Iron Trade of Great
Britain', published in 1873, as having 10 puddling
furnaces and 2 mills and forges. The firm mainly
produced sheet iron.
|
The notice of the
sale of Bull's Bridge Iron Works on 19th
December, 1859. |
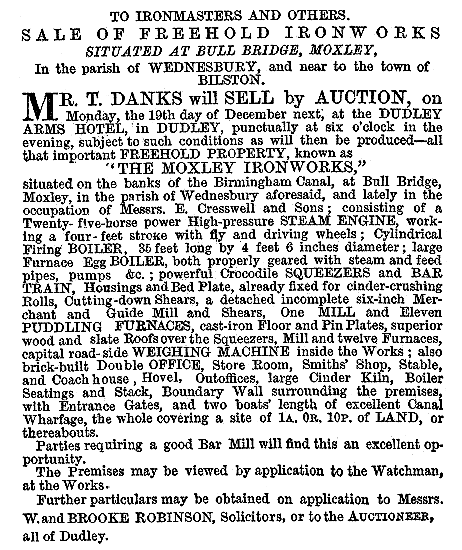 |
|
 |
 |
 |
Return to New
Roads and a Canal |
Return to
Contents |
Proceed to
Increasing Population |
|