West Bromwich grew rapidly in the
18th, 19th, and 20th centuries, thanks to the large
number of factories that opened in the area, providing
employment for the local population.
There were many industries,
including:
Aircraft accessories, Axles and Axle Trees
Bearings, Boiler Compositions, Bolts and
Nuts, Bottle makers, Box-Irons
Bricks, Bridges, Bright Drawn and Rolled
Steel, Cabinet Making
Chemicals, Collieries, Concrete Products,
Confectionery
Electrical Fittings, Engineering, Forgings,
Foundries, Furniture, Gauges
Glass, Grates, Holloware, Hydraulic
Machines, Iron Foundries, Ironmongery
Mineral Waters, Nails, Paint, Pattern
Makers, Plastics, Printing, Safes,
Springs, Tools, Trailers, Tubes,
Typewriters, Washers, Weighing Machines |
|
|
|
Read about some of the
larger industries and companies |
 |
|
Foundries
and Pattern Makers |
 |
|
Springs |
 |
|
Jensen
Motors Limited |
 |
|
J.
Brockhouse & Company Limited |
 |
|
Archibald
Kenrick & Sons Limited |
 |
|
George
Salter & Company Limited |
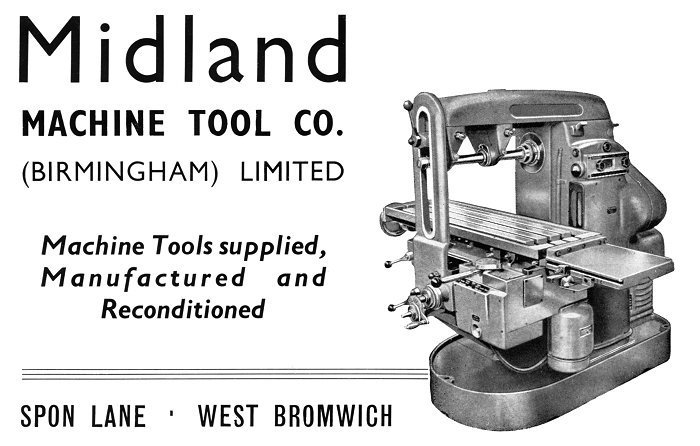
Kenrick & Jefferson Limited.
The printing business opened in
October 1878, when John Arthur
Kenrick, a member of the well-known hardware family,
formed a partnership with Frederick Thomas Jefferson, a
local solicitor, to acquire the business of 'The Free
Press', a bankrupt Liberal newspaper in West Bromwich.
Kenrick & Jefferson Limited
was incorporated as a private limited company on the 6th
January, 1900.
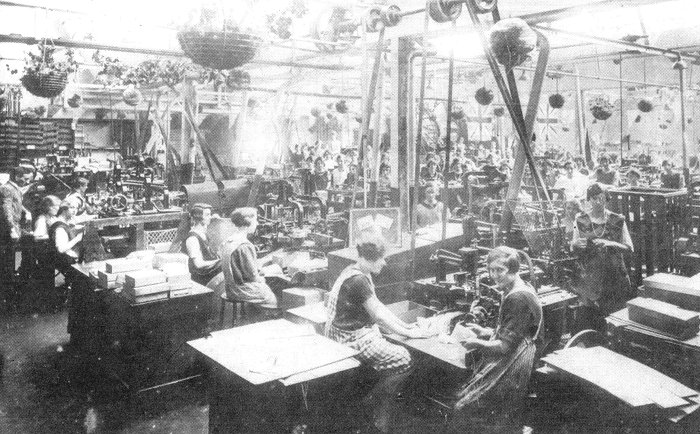
The envelope factory in 1925.
Frederick
Jefferson quickly developed the printing side of the
business, which soon moved into office equipment,
business stationery, loose leaf binders, filing systems
and even office furniture. 'The Free
Press' newspaper closed in 1933.
By the 1950s there were over
100,000 customers in Great Britain and abroad,
benefitting from the excellent printing quality, thanks
to the installation of the latest and finest plant. The
composing, letterpress and lithographic departments were
capable of handling both small and very large contracts.
Four large binderies employing over
500 people dealt with the handling of system stationery,
renewal leaf binders, filing and card index equipment
and Carbotyp stationery for simplifying clerical
operations.
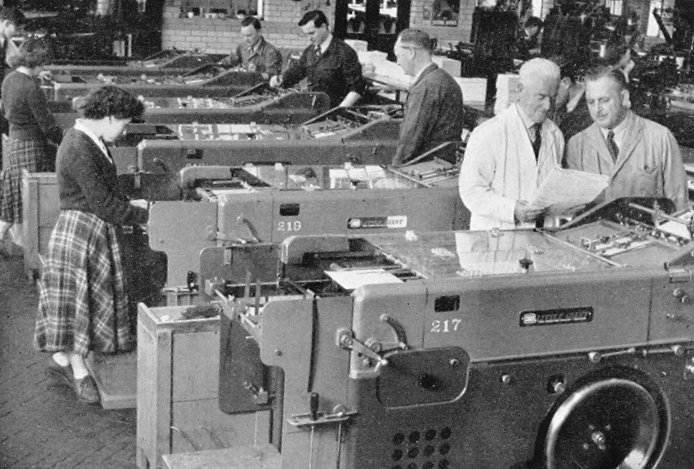
A battery of fast-running
letterpress machines.
The department devoted to relief
stamped stationery is one of the largest, if not the
largest, of its kind in the world, thanks to the hundred
or so, modern relief stamping presses that are
constantly in operation. There is also a well-equipped
envelope factory, where envelopes from the smallest to
the largest commercial sizes are available direct to
customers in a wide range of materials.
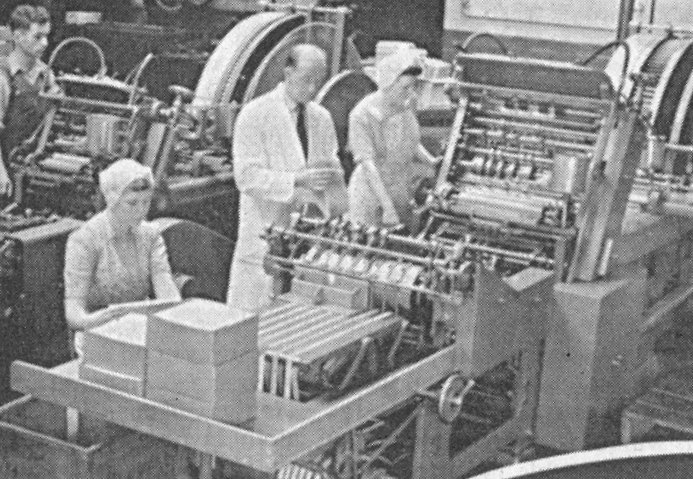
An envelope making machine.
The firm’s advisory department
provided recommendations on business organisation and
routine and the direct advertising department offered
suggestions for all kinds of advertising literature. In 1971,
the firm acquired Manchester-based, Norbury Lockwood,
manufacturer of calendars and printed stationary.
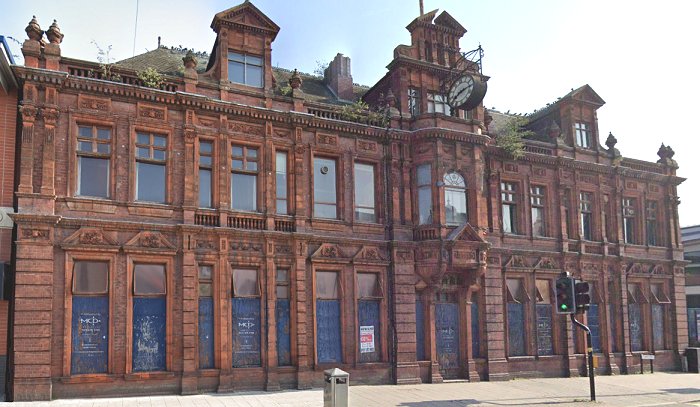
The 1883 building in High Street.
In
1995 to 1997 the firm sold off everything except its
envelope business, based on another site in the town.
That was also sold in 1999 and traded as Kenrick and
Jefferson Envelopes Limited. The High
Street premises was derelict for several years and by
the autumn of 2001 had been demolished (except for the
1883 building) for redevelopment as a shopping and
leisure centre.
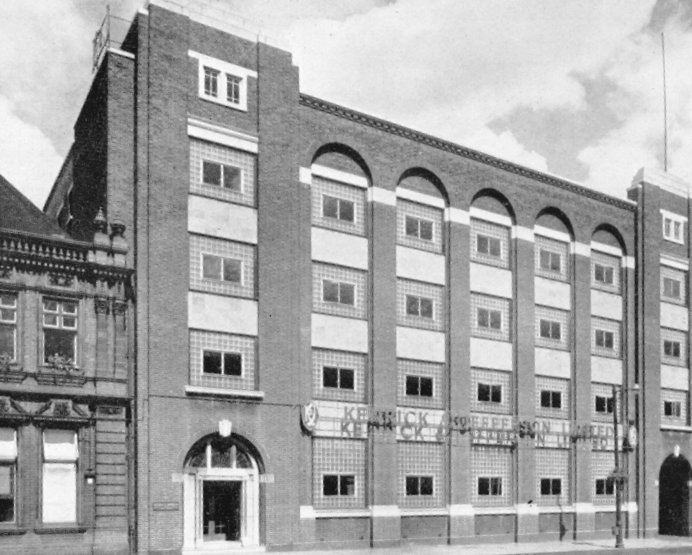
The once-familiar building on High
Street that was demolished at the turn of the century. |
Moxey Conveyor & Transporter
Company Limited.
The company, which specialised in
the design and manufacture of bulk handling conveyor
plant, primarily for the steel industry, opened a new
factory at West Bromwich in 1954. The site, covering
eight acres, included the factory with a floor area of
40,000 square feet. Building work began in May 1954 and
the factory opened in 1955. By October of that year the
production area had been extended to cover around
100,000 square feet.
Apart from conveyors to handle iron
ore, coal, coke, grain and gravel, plant was designed
for the storage of railway wagon springs, the handling
of bicycle saddles, and whale meat processes in whaling
ships.

A Moxey gravity bucket conveyor
for handling coke.
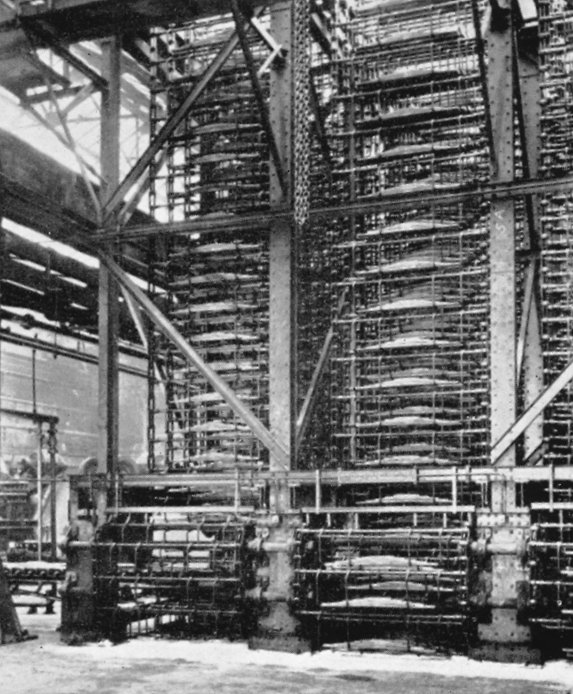
A Moxey storage tower for railway
laminated springs.
An advert from the
mid 1950s. |
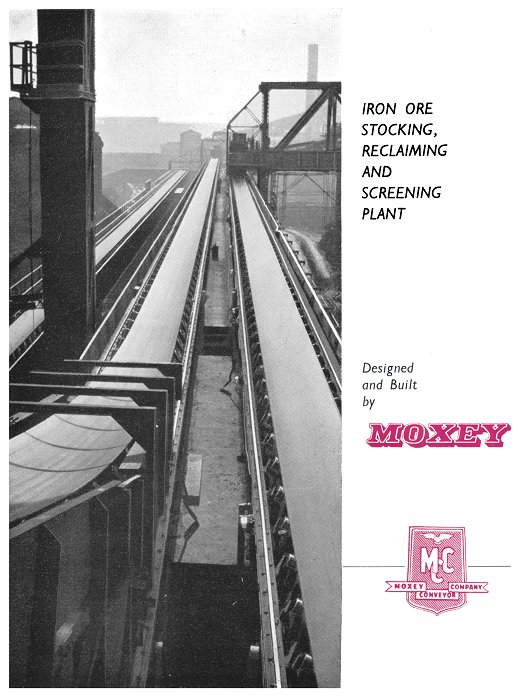 |
|
Pasco Limited.
Pasco’s factory opened in about
1920 for the manufacture of precision pressings. After
the Second World War, large power presses of up to
eighty tons capacity were installed, which enabled the
firm to undertake the production of a vast variety of
fittings and components for the motor trade.
The plant was capable of handling
complicated pressings involving a large number of
individual operations and the manufacture of fittings
for brushes, chisels, spades, shears and many similar
articles. Components for the foundry trade are also
produced. The firm regularly carried out contracts for
the Admiralty and other Government Departments and
exported pressings to Australia and New Zealand.
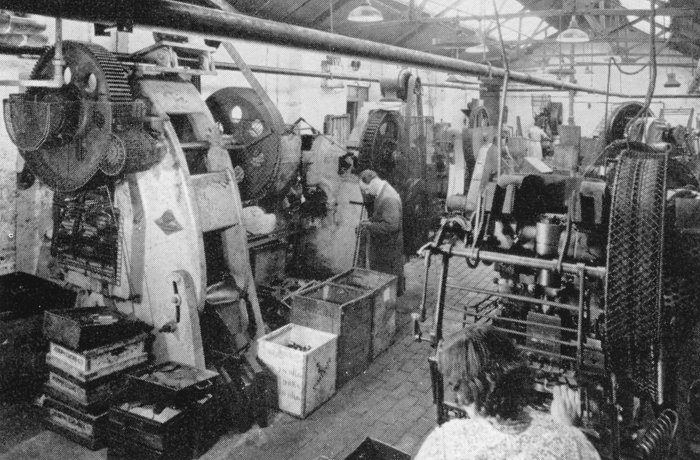
Inside the Pasco factory. |
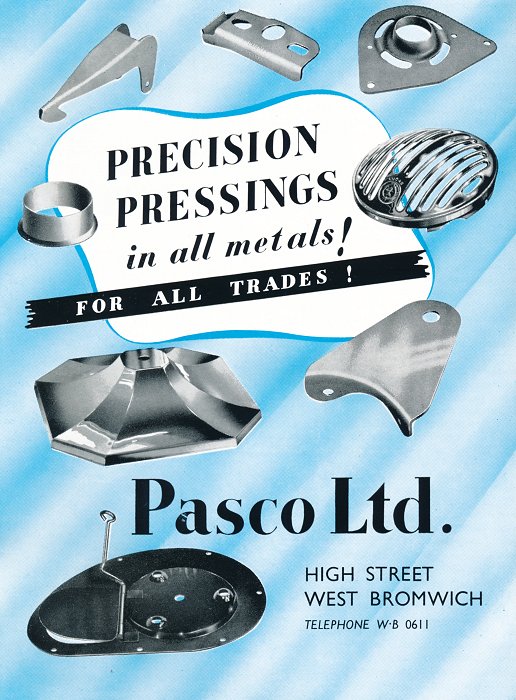 |
An advert from the mid 1950s. |
Ash & Lacy
Limited.
The firm, founded by Joseph Ash, began life in
1857. He was joined in 1864 by John Pierce Lacy to
form Ash & Lacy. In 1936 the firm moved from Great
Bridge, to a factory at
Black Lake, West Bromwich. The firm’s head
office was in Meriden Street, Birmingham. It became
a private limited company on the 5th December, 1917,
specialising in galvanised corrugated sheets for the
Dutch barn and constructional engineering trade,
supplying sheets that could be curved or cut to the
requirements of any roof or building.
Steel gutters of almost any shape or thickness were
made on powerful brake presses which also carried
out many other types of heavy bending work. The
sheet metal work included articles such as
galvanised coal bunkers, stovepipes, revolving
cowls, corn bins and garden wheelbarrows. The firm
has been extremely successful and has a head office
in Bromford Lane, West Bromwich, with many customers throughout the world.
It now produces a range of building materials
including steel frames, fabrications and cladding at
several locations. |
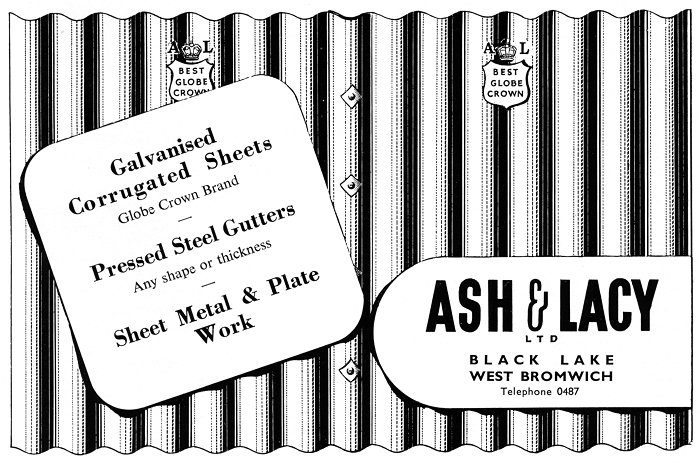
Hills (West
Bromwich) Limited.
Hills was founded in the early
1930s as Hills Patent Glazing Company Limited. The firm
broadened its activities by making windows, lanterns,
decklights, domes, office partitions, etc. In 1936 the
firm founded Universal Steel Doors, Limited, who
manufactured large sliding doors for aircraft hangars
and later complete aircraft hangars at the Kastrup
Airfield, Copenhagen.
At the beginning of the Second
World War, the firm carried out contracts for Bailey and
other military bridging equipment, rocket guns, pulley
blocks, invasion gear, light gun mountings and founded
an associated company called Chain Developments Limited,
for the manufacturing of electrically-welded steel
chains for the Admiralty and for special tanks used by
the Armoured Corps.
During the war, Hills developed the
'Presweld' system of building construction, which by the
end of 1945 had become well established. It used a
lattice type of construction consisting of built-up
beams and sub-assemblies with a high degree of
prefabrication, so as to reduce skilled work during
erection.
In 1946, the private limited
company, Hills (West Bromwich) Limited was formed and
the Hills Presweld system was first applied to steelwork
and later to other materials, such as concrete, glass
and plaster. Initially, the system was applied to
domestic housing, where the advantages of speed of
erection, with the roof completed very early on,
out-weighed the extra cost of a steel frame. It began to
be used for the erection of schools, which at the time
were in demand. Hills took a leading part in the
post-war school building programme and were associated
with about one-fifth of all the new schools built. 'Presweld'
has also been applied to factories, canteens and office
blocks.
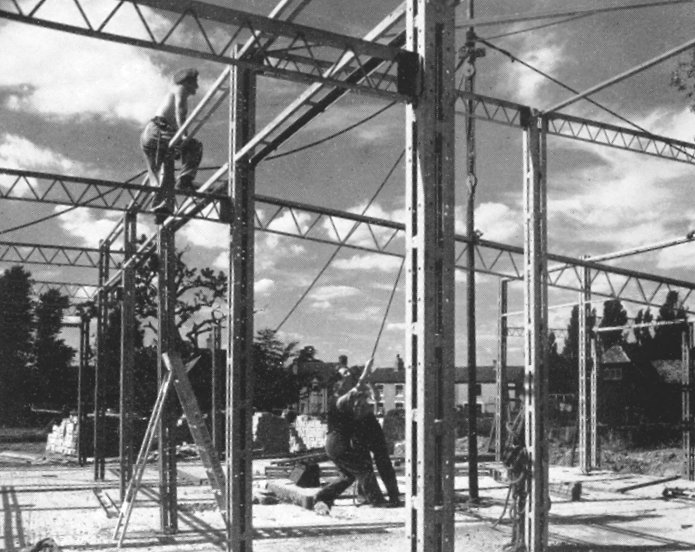
Assembling Hills' Presweld components for a new school building.
In the late 1940s, Hills developed
Glass Curtain walling, which uses a framework of
horizontal and vertical rails attached to the main
structure, whether it be a steel frame, brickwork or
reinforced concrete. Into this framework are fitted
large panes of glass with any desired degree of opening
lights and combinations of solid or opaque panelling as
the architect may desire. The finished wall of glass is
both wind and weatherproof and can also incorporate any
desired degree of insulation and permanent colour that
may be wanted. The infill panels are marketed under the
name of 'Hilsulate' and are also available for other
building applications. Here again, the company is in the
forefront of new development, having already completed
Glass Curtain Walling contracts for a number of schools,
office blocks and multi-storied flats at home and
abroad.
The firm developed another new form
of construction called 'Hilcon', consisting of pre-cast
reinforced concrete wall and floor units and included
the 'Hilsulux' roof construction system, using standard
woodwool or concrete slabs supported on steel purlins
and covered by bituminised felt.
Another product was power operated
roof ventilating shutters which virtually gave open-air
conditions at the touch of a button and were
indispensable to foundries, rolling mills and laundries,
etc., where the rapid clearance of heat, smoke and other
fumes was a problem. All the steelwork produced by the
firm was normally galvanised in Hills’ "hot dip" plant,
one of the largest of its kind in the country.
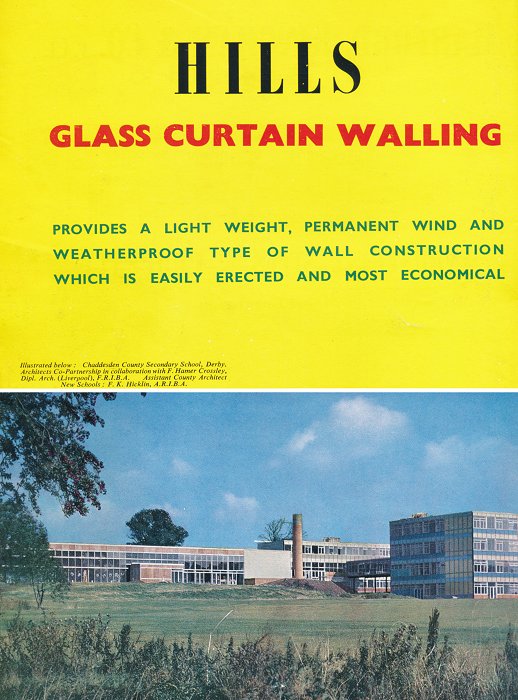 |
An advert from the mid 1950s. |
An advert from the mid 1950s. |
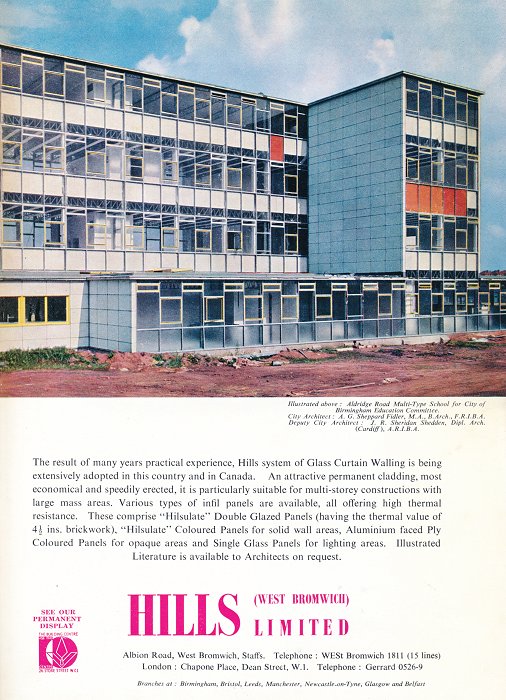 |
Hills (West Bromwich) Limited,
expanded from a small private company to an enterprise
controlling six factories, including three at West
Bromwich and eight branch offices. In addition, a
subsidiary company was formed in Canada to market and
establish the company's products, despite intense
American competition.
In the 1960s things started to go
wrong and the company went into liquidation in 1962.
From the London Gazette:
Hills (West Bromwich) Limited
Notice
is
hereby
given
pursuant
to
section
299 of
the
Companies
Act
1948
that
a
General
Meeting
of
Members
and
a
Meeting
of
Creditors
of
the
above
Company will
be held
at
Chamber
of
Commerce
House,
75
Harborne
Road,
Edgbaston,
Birmingham
15, on
Friday,
the
25th
October
1963
at
3 o'clock
and
4 o'clock
in
the
afternoon
respectively
for
the
purposes
of
having
an
account
laid before them showing
the manner in which the liquidation
has
been conducted and
the
property of
the
Company
disposed
of
during
the
first
year
of
the
liquidation,
and
of
hearing
any
explanations
that
may be given by the Liquidator.
A Member entitled
to attend and vote at the above
Meeting may appoint
a proxy to attend and vote
instead of him.
A proxy
need not be a Member of the
Company.—Dated this
30th
day
of
September
1963.
A. S. Maddison,
Liquidator. |
|
|
British Typewriters Limited.
It began in 1935 when it acquired
the sales and manufacturing rights to 'The Empire'
typewriter from George Salter. The business began in a
former grocery warehouse in Victoria Street and produced
a new typewriter called 'The Baby Empire'. Up to 70
machines were produced each week and things went well
until the outbreak of war. The firm's building was badly
damaged in air raids in November 1940 and so production
ceased until after the war.
Any machinery that could be
salvaged was moved to part of the Kenrick & Jefferson
site, where the firm was engaged
in war work, producing aero engine rods for
Armstrong Siddeley, aero engine flame traps for the
Rolls Royce Merlin engine, as well as sights and trigger boxes for
anti-tank weapons.
The firm moved to the former Hudson
Works in Queen Street and Pitt Street, which had been
used by the Civil Defence and Fire Services. Typewriter
production began there in 1946. The Empire Aristocrat
model was introduced in 1948 and over one million of
them were produced. |
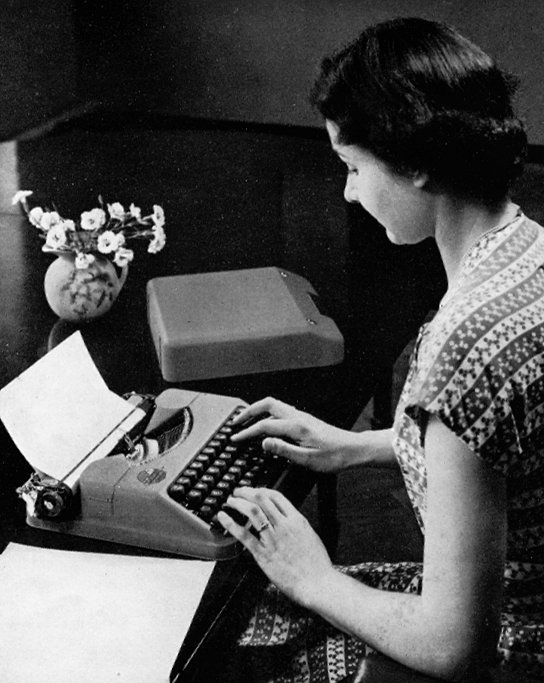
The Empire Aristocrat. |
In
the mid 1950s an updated compact model was produced,
which featured a more efficient and convenient design,
with a normal size roller, to allow the easy insertion
of paper and improved printing of type.
There was an
eraser table for the easy correction of typing errors,
specially designed plastic key tops with endurable
lettering, shaped to suit the fingers and even touch
over the whole keyboard.
In 1958, Smith Corona acquired British Typewriters,
Limited.
Manufacturing continued until the market was
being undermined by inexpensive imports from the Far
East, which resulted in the closure of the West
Bromwich, plant in 1981. |
Braithwaite & Kirk.
The firm started life as
Riley, Fleet & Newey, in 1848, as an engineering
company at Crown Works, Swan Village. It was formed by
George Newey, Thomas
Fleet and James Riley, all subcontractors in the
engineering industry. By 1861 the firm was producing a
wide variety of products including wrought-iron steam engines, boilers,
gasholders, purifiers, tanks, bridge and girder work, iron
roofs, and canal boats. The business also produced evaporating and
sugar pans, water barrels, barrows, and miners' tools.
In 1884 the firm became Braithwaite & Kirk, engineers and contractors,
based at Crown Bridge Works, West Bromwich, which was
located on the Balls Hill Branch canal Just off Henry
Street and south of Ryder Street.
In 1912 the firm became Braithwaite
& Kirk and they received an order for 24 iron composite
canal boats. A year later
Braithwaite & Company Structural Limited was formed
as a subsidiary company in India.
Braithwaite & Company also opened another factory at
Newport, Gwent, called Neptune Works.
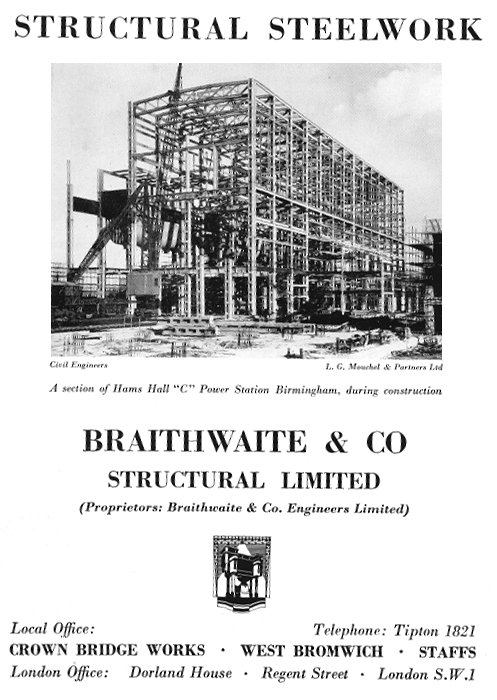
An advert from the mid 1950s. |
Each factory had the most modern machinery and provided
excellent training facilities for young men entering the
structural steelwork trade. The company’s apprentices
were encouraged to study at technical colleges, and two
scholarships were available at Birmingham University.
Many apprentices progressed to positions of trust and
were responsible for the supervision of large contracts
that were carried out by the company in all parts of the
world.
The company joined
forces with other businesses to form the
Braithwaite Group of Companies. In addition to structural steelwork
and bridgework, the business was well known for the
fabrication and erection of wharves, piers, jetties,
cast-in-situ using "Screwcrete" piles and pressed steel
sectional storage tanks.
In 1978 to 1980 all UK
operations were moved to South Wales and the
firm became part of the Rowecord Group,
which operates from Neptune Works. The firm
is now known for the design and supply of the largest
glass reinforced plastic (GRP) and
Steel water storage tanks in the world. |
|
Tom Carrington & Company Limited. Tom Carrington started in business,
in a small workshop, before the First World War, making
taps and screwing tackle under the names of "Lyndon" and
"Ega-Kut".
The business was extremely
successful prospered and Lyndon and Ega-Kut products
were known and used throughout the world. The founder
retired and handed over the business to his son Tom, who
maintained the firm's reputation for quality and
accuracy, while increasing the scope and size of the
business.
The range of products increased and
the company manufactured taps, gauges and dies, chaser
die stocks, receders, pipe cutters and screwing
machines, which were widely used in the plumbing and gas
trades.
The business remained a family
concern, that became world famous for its "Lyndon" taps
and gauges and for its" Ega-Kut" threading tools, chaser
stocks and dies. In 1963, Tom Carrington & Company
Limited, moved to Egakut Works, Willenhall Lane
Industrial Estate, Willenhall Lane, Bloxwich. Where it
still is today. |
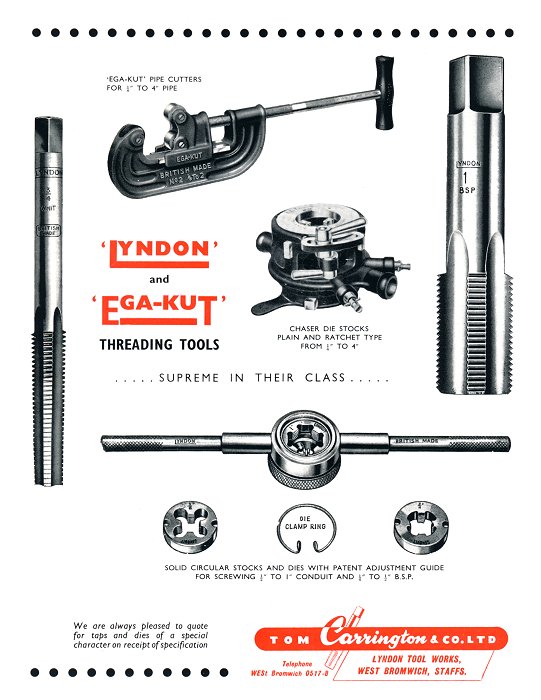 |
An advert from the mid 1950s. |
Copper and Alloys Limited. The firm was founded in the late
1940s in West Bromwich and used production methods that
came from the continent. The business produced copper by
a refining process from low grade residues and scrap.
The basic product was copper, but advancing a further
stage and utilising their technique for refining copper
they also produced an extensive range of copper based,
non-ferrous alloys from brasses to gunmetals, phosphor
bronze, manganese and aluminium bronze, and high duty
nickel bronze for the Admiralty and special industrial
applications.
All the alloys were produced in the
forms of ingots, extrusion billets or rolling slabs, and
a high standard of purity was maintained by careful
treatment of raw materials and strict laboratory control
through every stage of production to final inspection.
The process also allowed the recovery of zinc oxide at
the refining stage, which apart from providing a highly
marketable product, had the joint advantage of reducing
air pollution in the vicinity of the factory to a
minimum. In an area as highly industrialised as West
Bromwich the importance of this will be readily
appreciated.
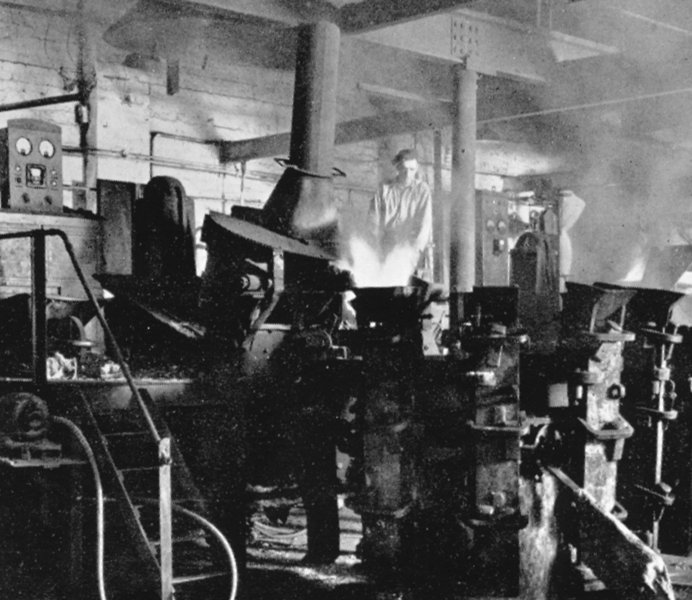
Melting brass in the electric
furnace department.
A new extrusion press was acquired
in the early 1950s, which was one of the largest brass
presses in the country. In the mid 1950s the factory was
extended with two new buildings, to extend the extrusion
capacity. In order to supply the increased number of
presses, the number of electric furnaces was increased
and the firm confidently looked towards a bright future.
|
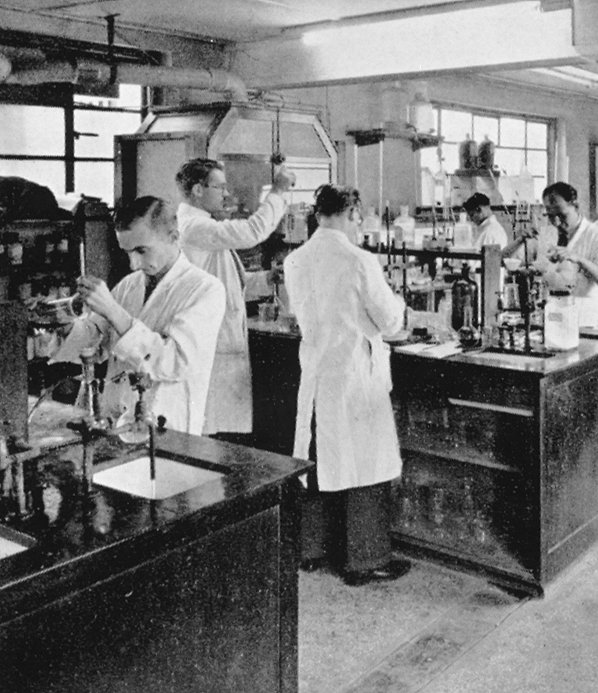 |
The chemical laboratory and
test station. |
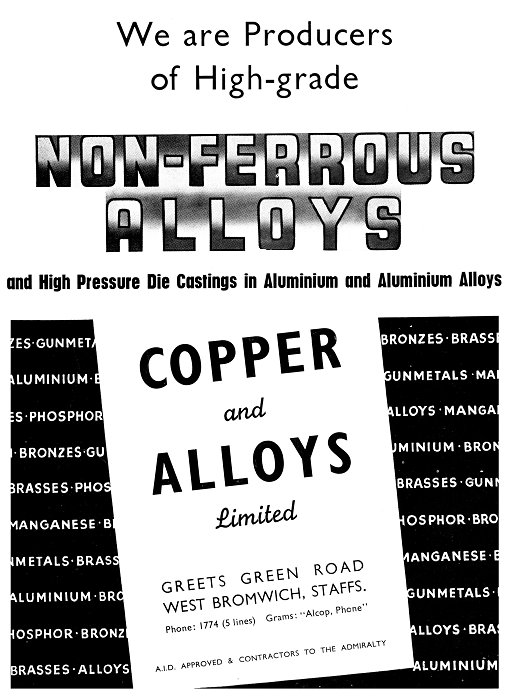 |
An advert from the mid 1950s. |
C. B. Gurmin & Company Limited.
The business was founded in 1950
in Pikehelve Street, Golds Hill, West Bromwich, for the manufacture of a new type of key for the lock
trade. In the late 1940s, Chubbs and Albert Marston
Limited of Wolverhampton were having problems with the
manufacture of satisfactory malleable cast keys. Brian Gurmin,
a welding engineer, who was the brother in law of Bill
Williams, the owner of Albert Marston Limited, began to
look into the problem and soon found a solution.
Bill Williams encouraged Brian Gurmin
to set up his own company to make welded steel keys and
blanks, which were fabricated in steel from three pieces and
projection welded together. Each key was made with great
accuracy and could be put to a lock without any fitting
whatsoever, thereby saving considerable expense. A large
range of these keys was made and exported to all parts
of the world.
On of Brian Gurmin's main customers
was Yale. He also started to produce steel blanks
which were sold to the Willen Key Company.
Unfortunately, Gurmin & Company were unable to keep-up
with the demand and so Marstons looked round to see who
else was making welded steel keys and blanks. In 1955
they turned to Arthur Hough and Sons, in Essington, who
had started to make welded steel keys in 1953. Gurmin's
production problems continued and so in the late 1950s,
production ceased and the company's welding machine was
sold to Arthur Hough and Sons, in July 1960.
Gurmins branched out into the production of all types of
formed wire work, and supplied many of the leading
manufacturers of refrigerator and electric fires. Wire
mesh cloakroom equipment including kit lockers, shoe
baskets, etc., was manufactured for both school and
factory use. Milk bottle crates were also amongst the
many other items produced.
|
An advert from the mid 1950s. |
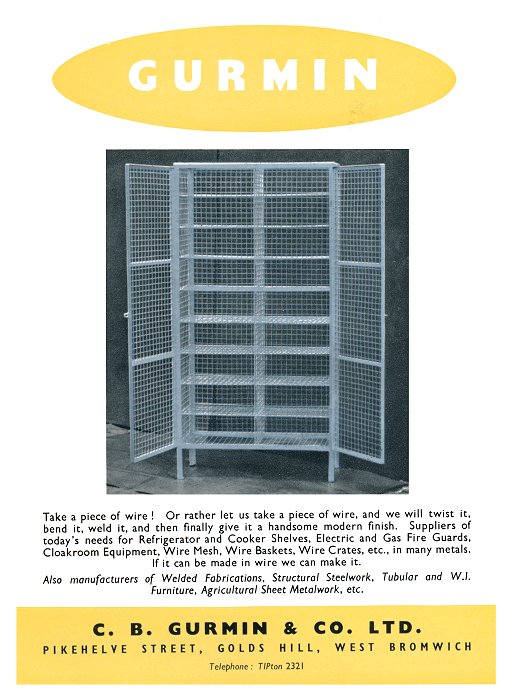 |
H. Geddes & Sons Limited.
The firm was founded in the early
20th century for the manufacture of export packing cases
and crates. There were three factories, one if West
Bromwich, another on Smethwick and a third in Oldbury.
Packing cases were produced with
waterproof lining and sealing of packing cases, tin
lining and the manufacture of cases to carry a colossal
weight.
The business was also a timber
merchant and so large stocks of wood were kept for sale,
including hardwood, plywood, seasoned hardwoods, doors,
imported softwoods and of joinery quality timber. There
was a mill available for any type of machining. The
business later moved to Dumblederry Lane, Walsall,
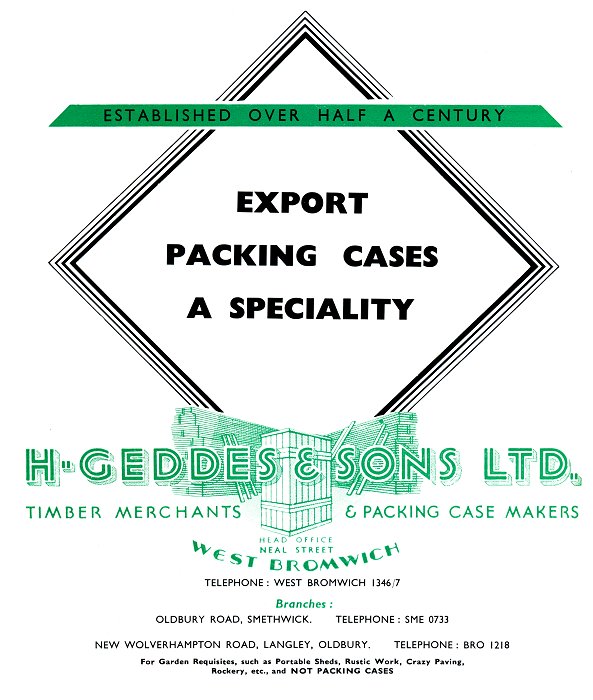
An advert from the mid 1950s. |
The Fordath Engineering Company
Limited.
The business was founded in the
1920s to manufacture all types of foundry corebinders,
which with the addition of core oils provided short
baking characteristics, which enabled many foundries to
reduce their core shop costs, because of the short time
cycle required.
Fordath corebinders were sold under
the trade name "Glyso," and were exported to Holland,
France and South Africa.
Fordath also produced a range of foundry equipment
including the Fordath "New-Type" mixing Machine. In the
1950s, the plant was modernised and the factory extended.
|
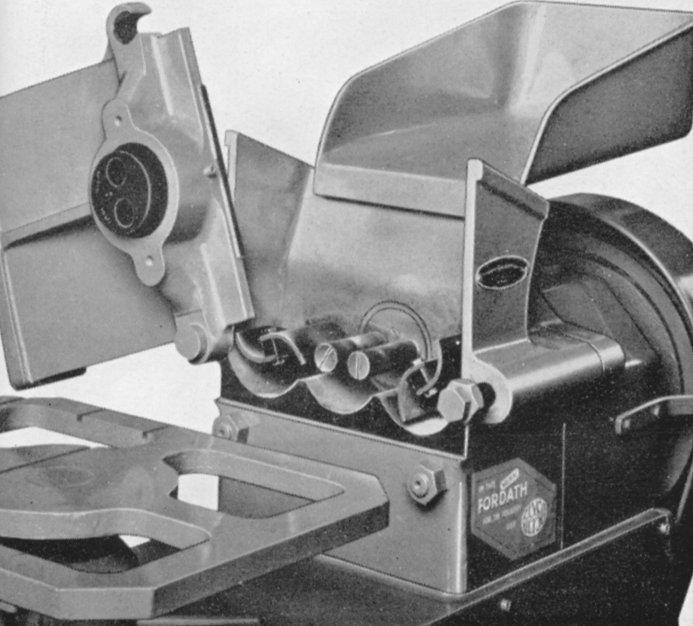
A Fordath multiplunger core
extrusion machine. |
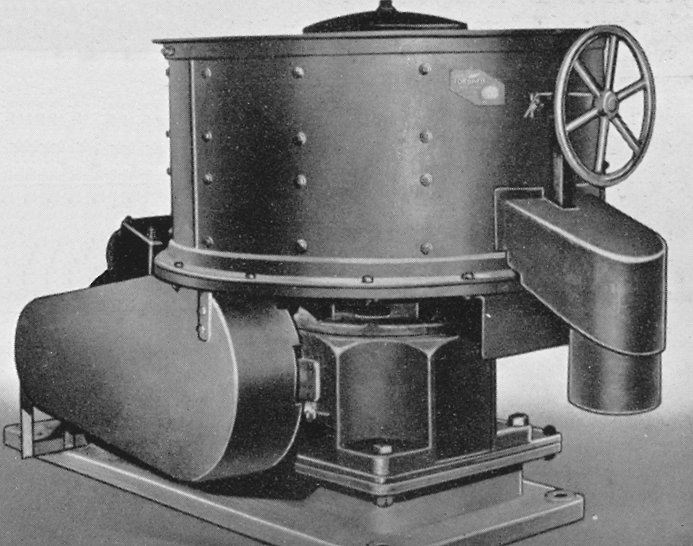
A Fordath mixing machine. |
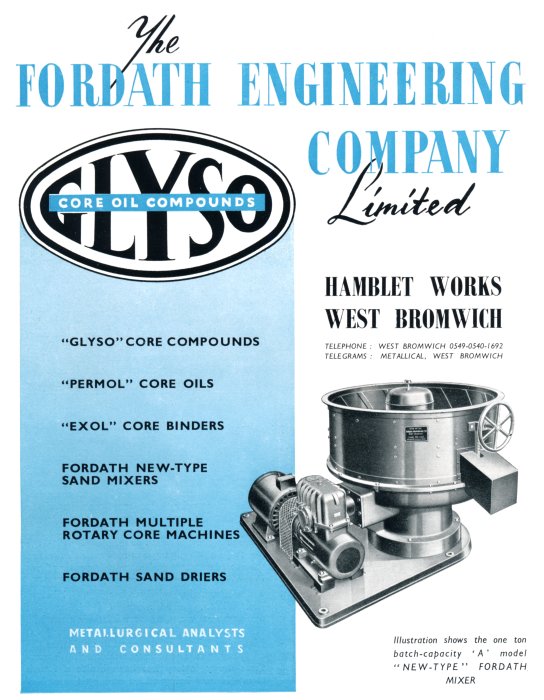 |
An advert from the mid 1950s. |
The Foundry &
Engineering Company (West Bromwich) Limited. The business was founded by Mr.
Alfred Turner, JP. and the late Mr. W. H. Smith. The
company produced good quality grey iron castings for the
motor, electrical and engineering trades and special
types of foundry plant that were used throughout the
world.
Since 1945 scores of Acme Vertical
continuous stoves for the foundry industry have been
exported to Australia, New Zealand, India, South Africa,
Canada, Sweden, Switzerland and Denmark.
The firm had a loyal team of
employees, the majority of whom were in its service for
over twenty years. Several employees brought their sons
into the business, and on the management side, Messrs.
A. E. R. Turner, Jnr., S. M. Turner and E. N. Smith were
actively engaged in the business for many years and
joined the Board of Directors.
The firm gained a high reputation
for customer service which resulted in large numbers of
"repeat" orders.
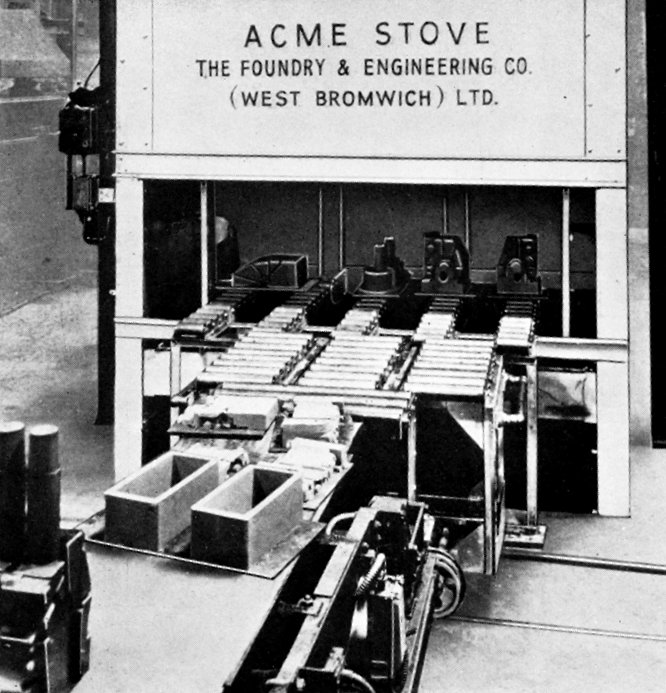
An ACME oil-fired 5 loop stove for
motor engine casting cores.
The firm went into
liquidation in 1990:
The Foundry
and Engineering Company (West
Bromwich) Limited
Notice is hereby given that the Creditors of the
above-named
Company are required on or before 31st May 1990, to send
in their
names and addresses, with particulars of their debts or
claims, and
the
names
and
addresses
of
their Solicitors
(if any), to
the
undersigned John David Travers, of Haines Watts,
Sterling House,
71 Francis Road, Edgbaston, Birmingham B16 8SP, the
Liquidator
of the said Company and, if so required by notice in
writing by the
said Liquidator, are by their Solicitors or personally
to come in and
prove their said debts or claims at such time and place
as shall be
specified in such notice, or in default thereof they
will be excluded
from the benefit of any distribution made before such
debts are
proved.
J. D. Travers,
Liquidator
NOTE.
This notice is purely formal and
all known Creditors have
been or will be paid in full.
London Gazette
1st May
1990.
|
|
|
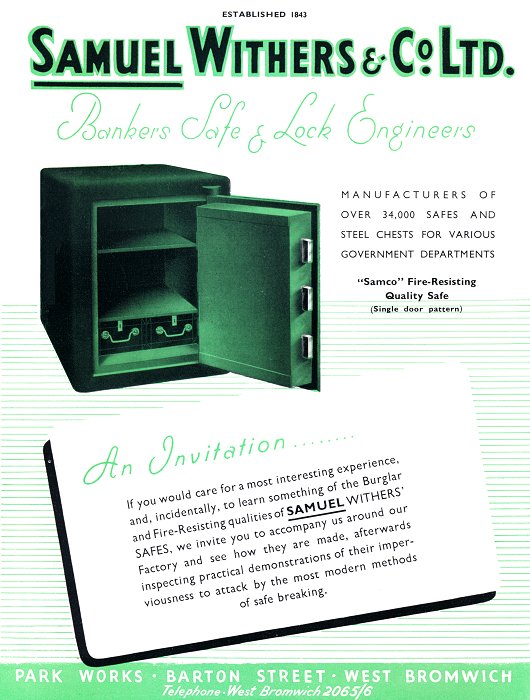 |
An advert from the mid 1950s. |
An advert from the mid 1950s. |
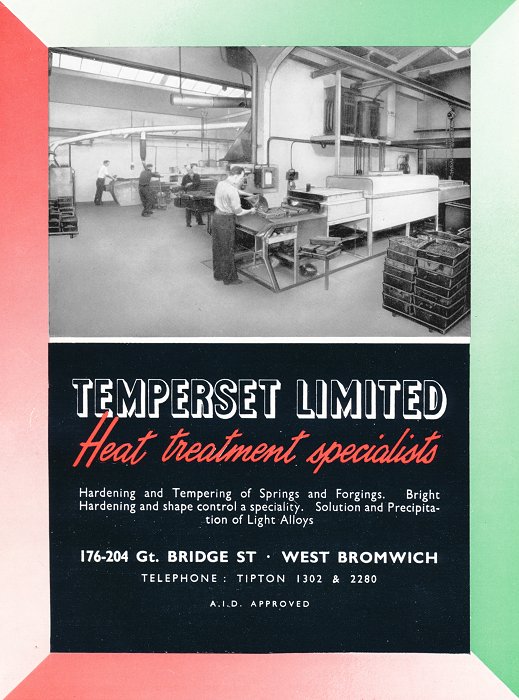 |
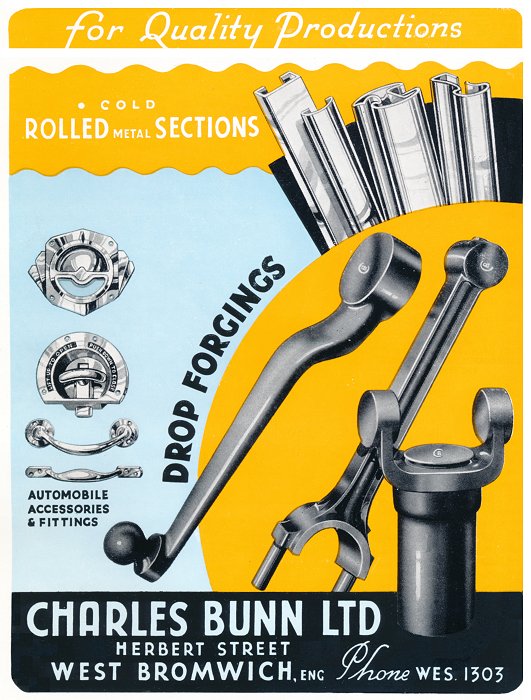 |
An advert from the mid 1950s. |
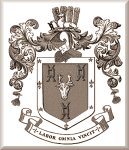 |
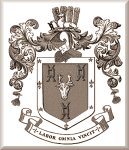 |
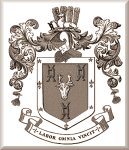 |
Return to
1861 Directory |
Return to
the contents |
Proceed to the
20th Century |
|