Dudley had a wide variety of industries, thanks to the
building of the canal network in the late 18th century
and a plentiful supply of raw materials in the form of
coal, iron ore, limestone and fireclay. As the
industries grew, the landscape became dominated by pit
heads, chimneys and glass cones.
The
area was ideally situated for the many industries that
appeared, because of its location in the central part of
the country and the excellent transport links in the
form of canals, followed by the railways and the
improved road network.
The
industries were extremely successful until modern times,
when most disappeared because of competition from cheap
foreign imports.
|
John
Barnsley and Sons Limited
The Barnsley family were
originally farmers who opened an iron foundry in
1809. They specialised in lifting tackle for
builders and structural engineers and were also
world famous for making Jews Harps, which at the
time were being produced by dozens of similar
companies based in and around the Dudley area.
They were popular for many years until people
started buying harmonicas.
John Barnsley and Sons also
produced a range of cranes, until the firm began
to specialise in the production of lifting
equipment, starting with pulley blocks. By the
1950s the firm produced a variety of overhead
travelling cranes, which were very successful.
In the 1970s the firm produced explosion proof
equipment for North Sea oil rigs and the oil and
gas industries. Development of the cranes
continued and today the firm is a world leader
in the production of explosion proof cranes and
hoists. |
|
|
|
 |
|
Coal, Iron
and Limestone Mines |
 |
|
Ironworks |
 |
|
Dudley's
Glass Makers |
 |
|
Beans
Industries |
 |
|
BSR |
 |
|
N. Hingley and
Sons |
 |
|
H. and T.
Danks and Edwin Danks |
 |
|
Round Oak
Iron and Steel Works |
|
|
|
Nail Making The
making of hand-made nails was a long established
industry that continued until the latter part of
the 19th century. Thanks to Richard Foley, who
set up a slitting mill at The Hyde, in Kinver to
produce iron rods for nailers, nail making
became a simple operation that could be carried
out by unskilled people. All they had to do was
to cut the rod to the correct length, point one
end, and make the head. It was one of the first
examples of mass production, because large
quantities of nails could be made simply and
quickly. |
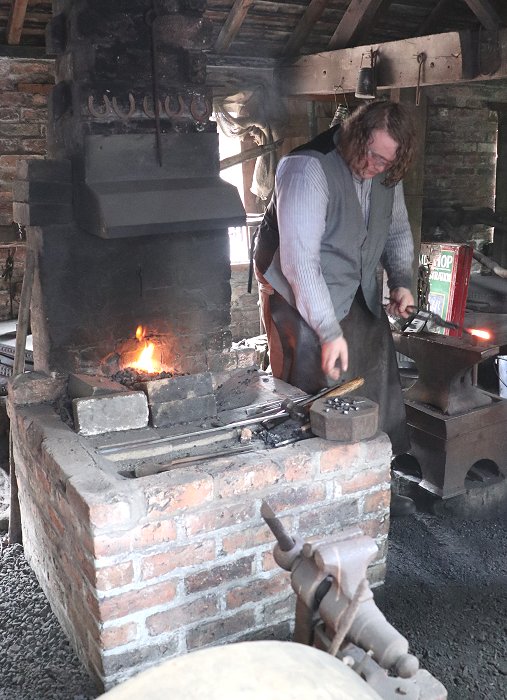
Making nails in the nail shop
at the Black Country Living Museum. |
The nailers couldn't afford to buy the rods
themselves, they were advanced to them by the mills,
to where they returned the completed nails and were
paid for them. They were also given standard
allowances for waste. A bundle of rods weighed 60
pounds and was 4ft 6" long. The nails were
characterised according to the number produced from
a given weight of iron. Long thousand (1,200) nails
weighing 4 pounds, were known as four penny bundles.
Larger nails were called 100 work, and were
priced by the hundred. They were more profitable
than the smaller ones, as less work was required to
produce them, and less waste produced.
There were many types of nails including
brads, tacks,
spriggs, dog-eared frost nails, sheath nails, and
sparrables. |
In 1852
around one quarter of the male and female
workers in Dudley and the surrounding area were
still producing nails, usually in a small
workshop at the back of their home. There was
some unrest in 1842 when nail makers’ wages were
reduced. Around 15,000 to 20,000 men met in the
town on the 25th April and kidnapped several of
the nail masters by force. The Riot Act was read
by the Mayor and troops were called-in from
Birmingham. The nail masters were only released
after promising to cancel the wage reduction. |
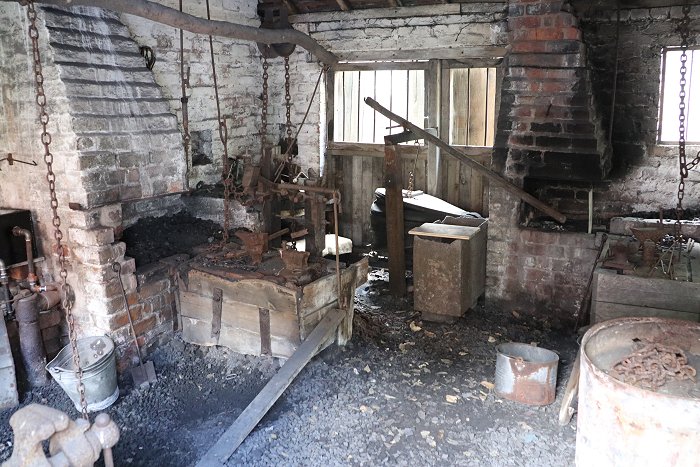
Another view of the
nail shop at the Black Country Living Museum. |
Samuel Lewis
and Company Limited
The business was
established at Netherton in about 1750, as a
nail manufacturer, specialising in horse and
mule shoe nails. The firm began to produce
pressings and forgings, particularly for farm
harrows, and handmade chain for specialised uses
such as horse gear. There were hundreds of
customers for nails, including the Admiralty,
the War Office and the India Office. They were
exported to many parts of the world.
M. and W. Grazebrook
The business, based at Netherton Iron Works,
Dudley, was founded in 1750. The firm mined coal
locally and originally had an old square blast
furnace. This was replaced by two blast furnaces, with a cold
blast, to produce iron. In 1817 the firm
purchased a Boulton and Watt blowing engine. There were three
partners, William Grazebrook, Michael Phillips
Grazebrook, and John Phillips Grazebrook. In
1865 William Grazebrook retired and the business
continued as before, with the same name, but run
by Michael and John Phillips Grazebrook.
It became a private limited company in 1914
and a public limited company in 1950. In about
1931, engineering, welding and foundry shops
were added to the factory. During World War Two
the firm helped develop 8,000lb. and 12,000lb.
block buster bombs.
In 1961 the business was acquired by N.
Hingley & Sons and was listed as a general heavy
engineering company and iron producer, with 250
employees, manufacturing all types of welded
fabrications, oil and chemical plant, rail tank
wagons, homogenous lead lined vessels and iron
castings. Also carrying out general machining. |
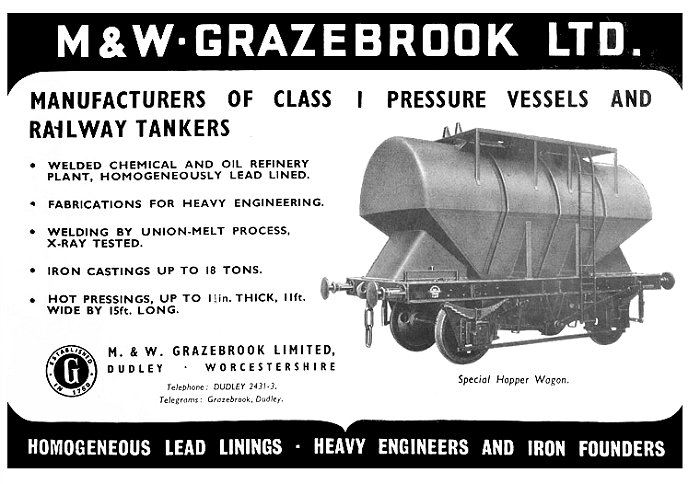
An advert from 1953. |
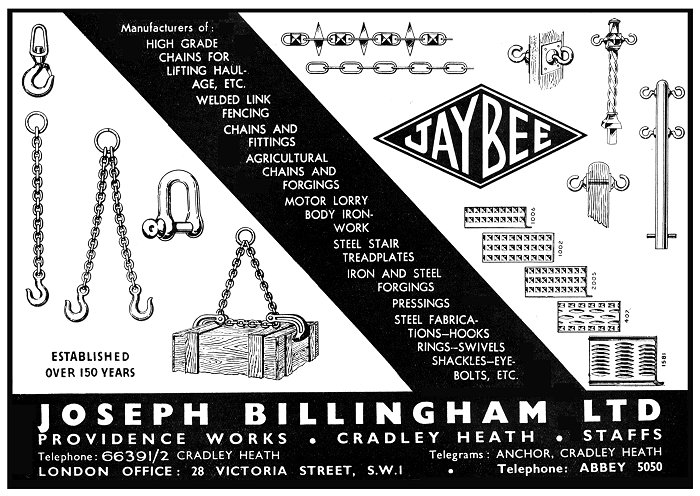
An advert from 1958. |
James
Griffin and Sons
Dudley once had a thriving
holloware industry, particularly thanks to the
products manufactured under the ‘Griffin’ name
by James Griffin & Sons of Withymore Works, in
Northfield Road, Netherton, alongside the canal.
The firm, founded in the late 18th century,
produced a wide range of products including
scythes, spades, forks, nails, spikes,
horseshoes, chains and buckets. James Griffin
died in 1818 and his son took over the running
of the business.
The firm was taken over by C. E. Swindell and
Company in 1856 and manufactured edge tools. The
business was later taken over by Joseph Russell
and taken over again in the 20th century by
chain maker Eliza Tinsley. The firm stopped
trading in 2005. |
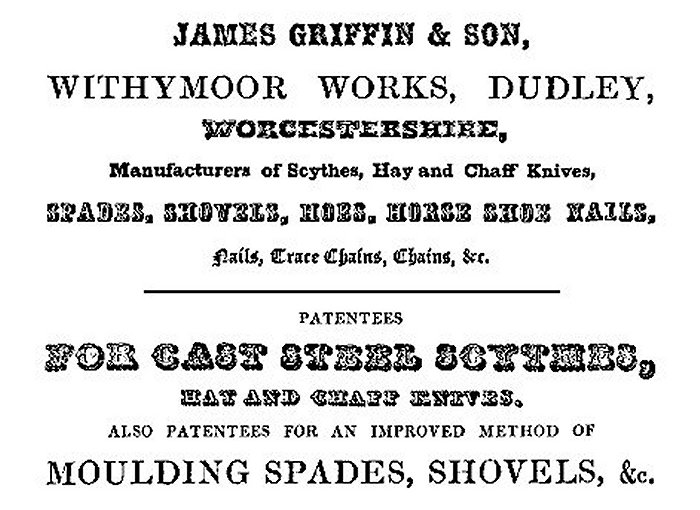
An advert from 1849. |
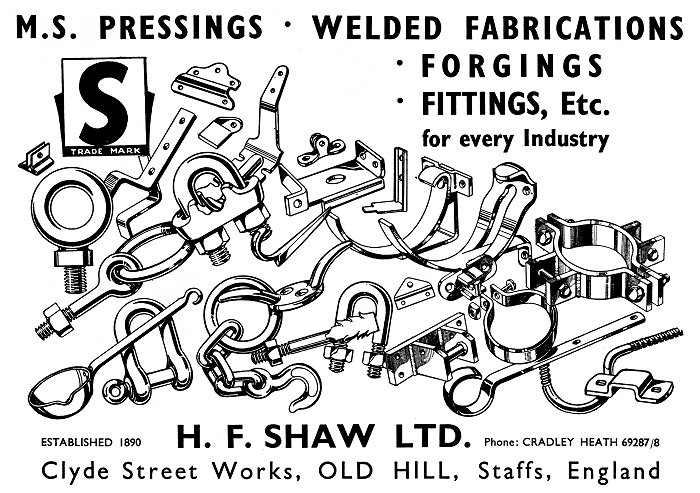
An advert from 1958. |
J. G. Walker
& Son
J. G. Walker & Son, was
established in about 1814 by John Griffin
Walker, at Darby End (also known as Darby Hand),
Primrose Hill, Netherton. The firm produced
wrought iron nails, chain, high strength chain
cables and anchors. It began as a partnership
between Joseph Griffin Walker, William George
Griffin Walker and Henry Griffin Walker. In 1833
Henry Griffin Walker retired and the business
was then run by William and Joseph Walker.
Joseph Griffin Walker died
in 1864 and his grandson, W. H.
Walker Higgs, took his place in the business.
In 1866 William George Griffin Walker was
registered as a debtor by the Registrar of
Bankruptcy, but was allowed to carry on trading
in order to pay off the creditors. In 1881
William George Griffin Walker, died
and the business was then run by
W. H. Walker Higgs.
In the early 1900s the firm specialised in
crane and mining chains, ship chains and cables.
Most of the chain was exported to Australia, New
Zealand and South Africa. |
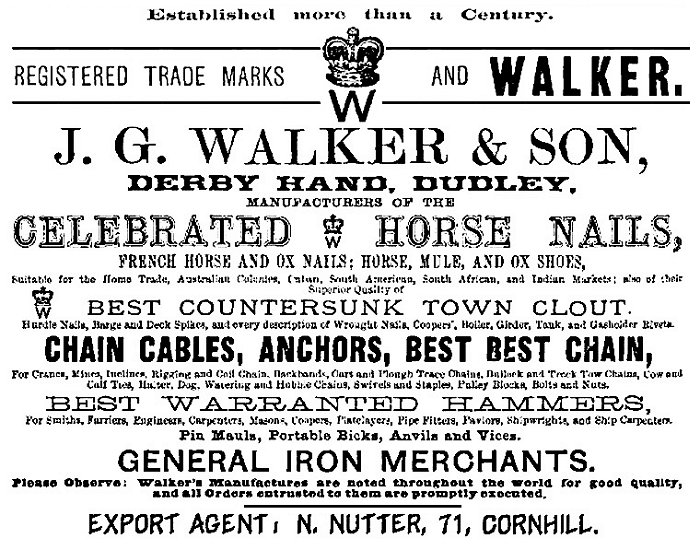
An advert from 1891. |
Lloyds Proving
House, Netherton
Lloyds Proving House was situated in Cradley Road,
Netherton, alongside the canal.
In 1865
it received a license from the Board of Trade for the
testing of chain cables, chains, and anchors. The first
superintendent was Mr. S. Tregenner.
In
1894, Henry Green was appointed as
superintendent and more powerful machinery was installed
to meet the requirements of various Acts of Parliament,
and of the rapid developments that were taking place in
the manufacture of chain, cable, and anchors.
It became
the largest and most complete proving house in the
country. In 1900 the establishment became part of
Lloyd's British Testing Company.
Henry Green remained as
superintendent until his retirement in 1936 and was
responsible for many reports on the testing of anchor
chains and cables. In 1926 he visited continental
testing houses to study their facilities for examining
chains and drew up specifications for many of the
testing machines installed at other testing houses. The
Netherton Proving House closed in 1990. |
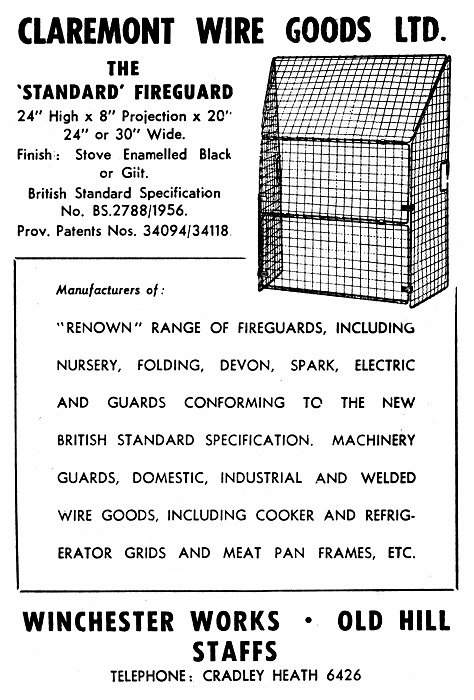
An advert from 1958. |
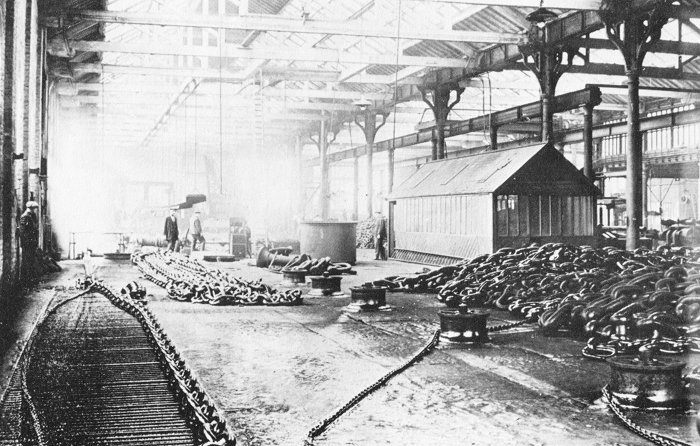
Lloyds Proving House
at Netherton. From an old postcard. |
Atlas Tube
Works, Netherton
Atlas Tube Works in Netherton
was established in 1858 by Henry Parkes Skidmore,
born in January, 1831. In the first part of the 19th
century there was a great demand for wrought iron
tubes to carry town gas from local gasworks to all
parts of the area. This became possible thanks to
Cornelius Whitehouse of Wednesbury, who patented a
greatly improved method of manufacturing tubes in
1825.
Atlas Tube Works was
established to produce tubes using Cornelius
Whitehouse’s patented method. Around 140 men were
employed, making the tubes at the factory using some
of the best and most up-to-date machinery. Strip
iron for making the tubes was purchased locally as
was bar iron, used to make the sockets and fittings.
Around 60 to 80 tons of tubes and fittings were
produced each week, as well as a large number of
garden seats that had supports made from tubing.
The firm also produced wrought
iron welded coils for boilers etc. and the patented
Atlas hot water coil stove that formed the basis of
an early central heating system. There was a tramway
at the factory to move things around the works and
onto the adjacent canal wharf.
Henry Parkes Skidmore married
Blanche Jones in 1857 and they lived at Hill House
in Netherton. He died of diphtheria on the 9th
October, 1861. His son, Henry Parkes Skidmore, born
in 1860 took over the business in partnership with
Thomas Jones. In the 1881 census he is listed as
living in Church Road, Netherton. In 1883 he bought
Stonehouse Farm at Fockbury near Bromsgrove and by
1891 had retired to Austin's Close, Harberton in
Devon. Henry Parkes Skidmore junior, died in Devon
on the 9th March, 1897 at the age of 36. |
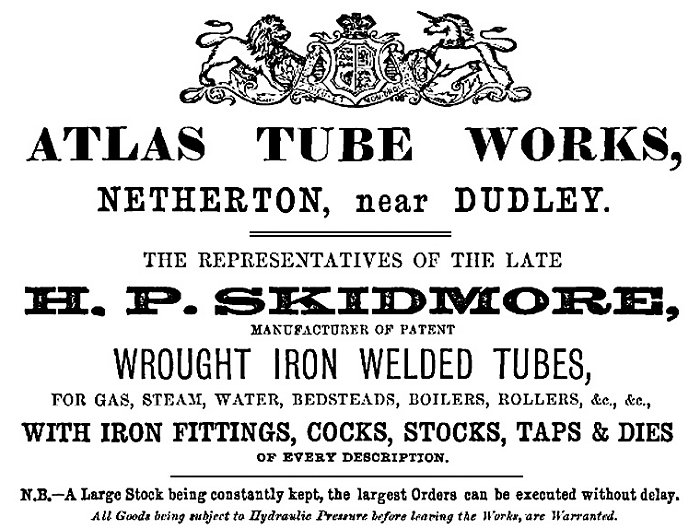
An advert from 1876. |
W. & S. Gorton W. & S. Gorton of Eve Hill had
a rope walk beside the grave yard belonging to St.
James' Church. The business was founded in 1788 and
produced a wide range of ropes, including boat
lines, using the 'Samson' brand name. On the rope
walk, fibres of mainly hemp were twisted into rope.
There was a similar business at Holly Hall, run by
Benjamin Whitehouse. |
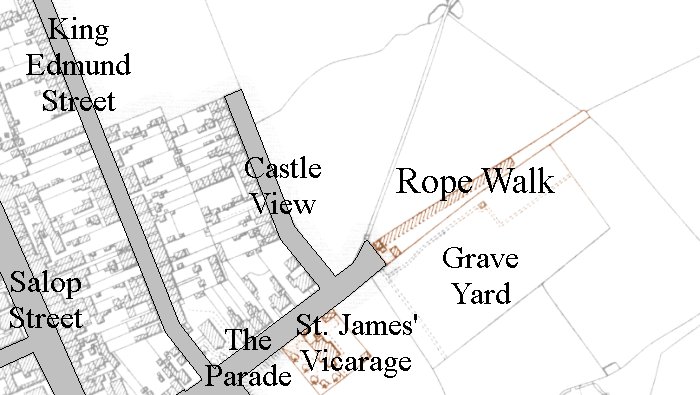
The location of W. & S.
Gorton, Eve Hill. |
Peter Wright
& Sons
Peter Wright started
producing vices and anvils in the early 19th
century in Black Acre Road, where Shedden Street
now stands. Peter Wright was
born in Dudley on the 15th March, 1803 and
started in business in the trade that had been
carried out by his family in the same place for
over 100 years.
He made many improvements in
the manufacturing of anvils and vices and became
senior partner in Peter Wright and Sons, of
Dudley and Oldbury. In 1848 he invented and made
the machinery for cutting the internal screws of
vice-boxes out of solid iron, making the
‘solid box vice,’ and in 1852 he invented the
'solid anvil', the first to be forged in one
piece by means of dies and by turning it
frequently under the hammer during forging.
Over 11,000 of them were sent to America
alone.
In 1862 he invented the parallel vice, and an
improved railway wheel. He died on the 28th
August, 1874 at the age of 71. The
firm was acquired by Isaac Nash in 1904 to 1905
and was later a part of the Spear & Jackson
Group. |
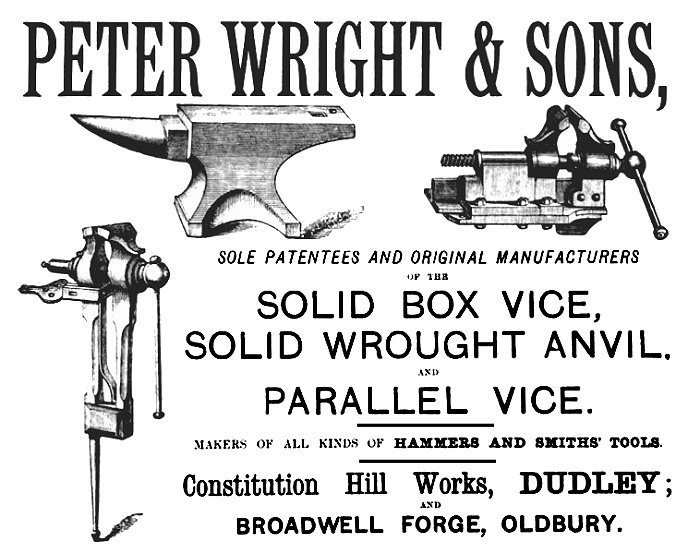
An advert from 1890. |
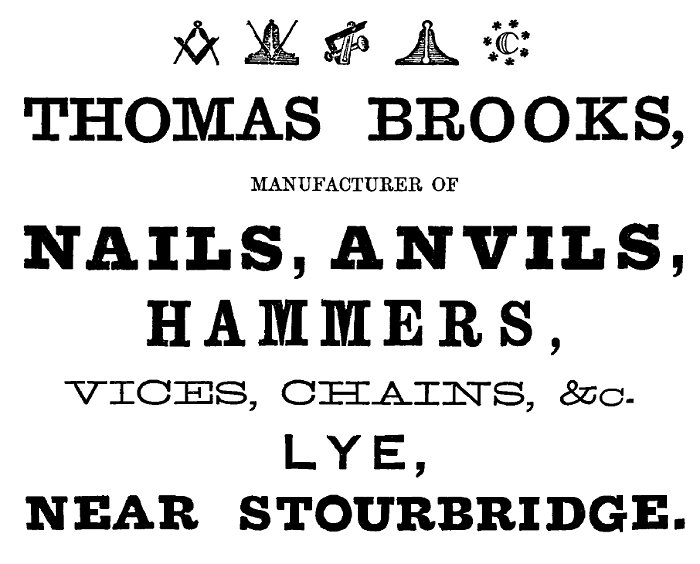
An advert from
1855. |
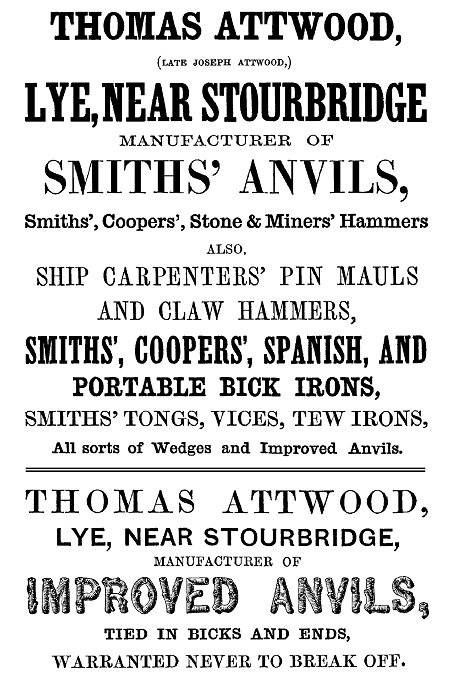
An advert from
1855. |
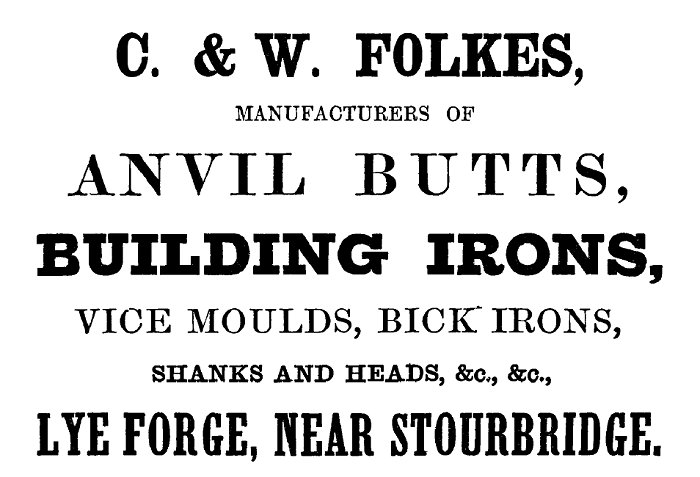
An advert from 1855. |
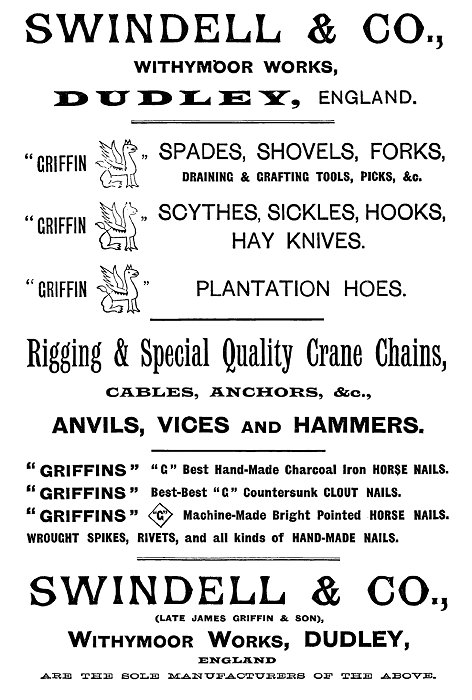
An advert from 1896.
Hermit Industries.
The firm was established
in 1947 at 21 Hermit Street,
Upper Gornal. In February
1964 a fire broke out in the
pattern shop, which was
badly damaged.
The factory closed in
about 1970 and moved to a
new site in Holloway Street,
Lower Gornal, adjacent to
the Fibre Form Company. |
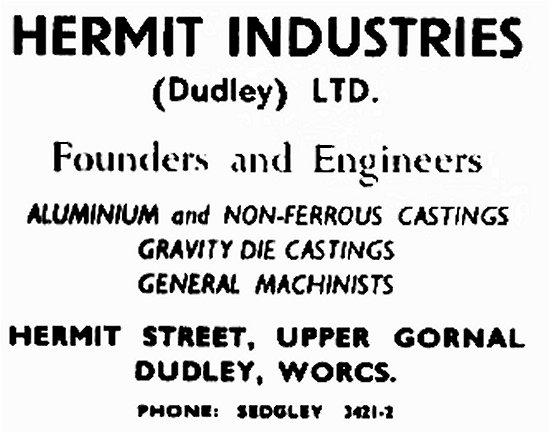
An
advert from 1960. |
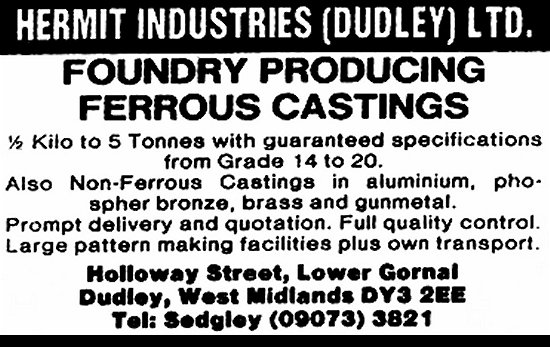
An advert from
1985.
The factory produced both ferrous and
non-ferrous castings for the engineering
industry and had two coke fired cupola
furnaces with tall chimneys, which stood
out on the hillside.
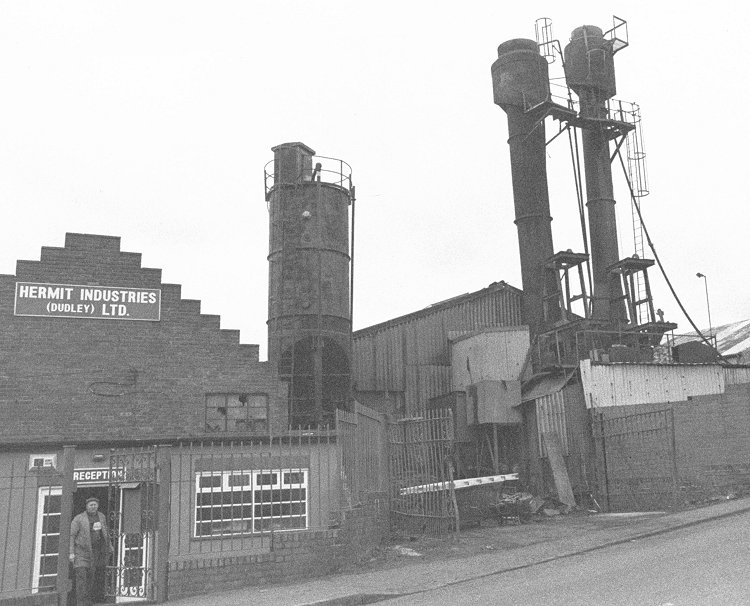
The factory in
1990.
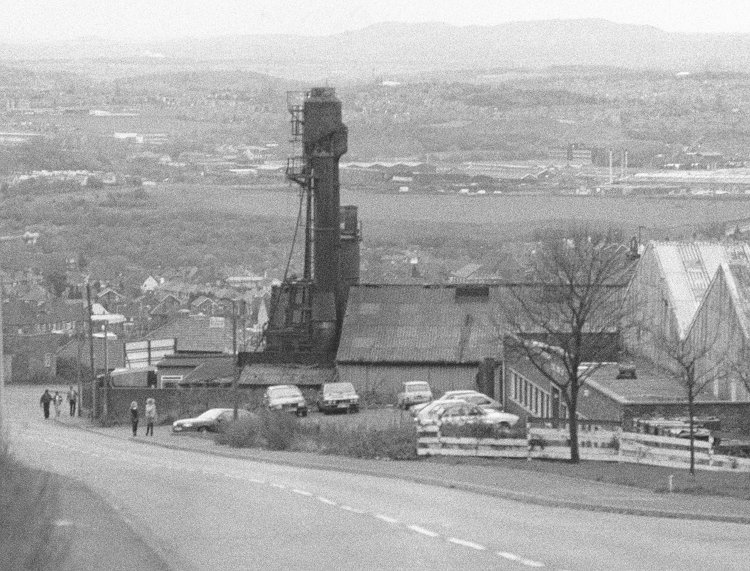
Another view of
the factory in 1990.
Residents who lived in the nearby
housing estate were annoyed by the smell
and the dust that was emitted from the
prominent fifty foot high chimneys. The
factory closed in 1992 because it was
unable to meet the legal pollution
requirements and an excessive amount of
foreign competition. Eighteen people
were made redundant and the company went
into voluntary liquidation in February
2000.
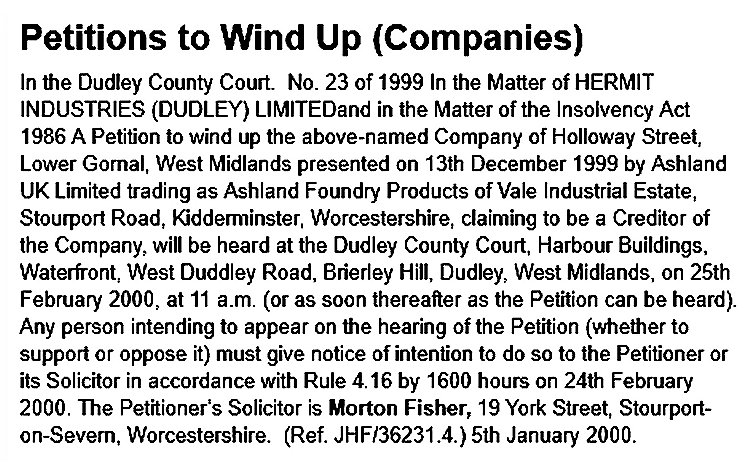
From the Gazette.
The factory was demolished, as was
the adjacent Fibre Form works and the
area is now a large housing estate.
|
James
Smellie Limited
James Smellie was born on a
farm in Ayrshire on the 31st May
1861. In 1878 after going to school at Hutton
Hall Academy, he served an apprenticeship as an
ironmonger in Dumfries and continued his
education by attending classes in several
subjects including Mathematics, Chemistry and
Geology.
In 1882 he
worked for a while in an iron monger’s shop in
London, followed by two years in Penrith, before
moving to Birmingham in 1887, where he became a
representative for a manufacturer that
specialised in steel fire irons and burnished
steel and ormolu fenders.
He purchased a partnership
with a manufacturer of cheap iron and brass rail
fenders in Dudley, in 1893 and they began to
produce a wide range of brass, copper, pierced
and forged hearth suites, grates and fire
places.
He travelled throughout the
country promoting the company’s products,
opening over 2,000 new accounts. Thanks to his
efforts they became the largest manufacturer of
hearth suites in the country.
In 1901 James was elected as a member of
Dudley School Board and became a local
councillor in 1903, representing the St Thomas
Ward.
On the 8th January, 1904 the
partnership was dissolved on friendly terms, and
James purchased the works, the property, the
patterns etc. and continued to run the business
under his own name.
The firm was based at
Ivanhoe, Cellini and Crator Works, Oxford
Street, Dudley. The business thrived and in 1906
became a private limited company with 30,000
ordinary one pound shares, all owned by members
of his family. Products included fenders, hearth
suites, dog grates, coal boxes, lamps, fire
screens and the polished steel ‘Ivanhoe’
fireplace, one of which was supplied to Princess
Mary. Ivanhoe fireplaces were then supplied to
many of the old historical castles as well as
wealthier households and the largest hotels in
the country. The firm also supplied all of the
brass tomb railing for the Sultan of Morocco’s
grave. |
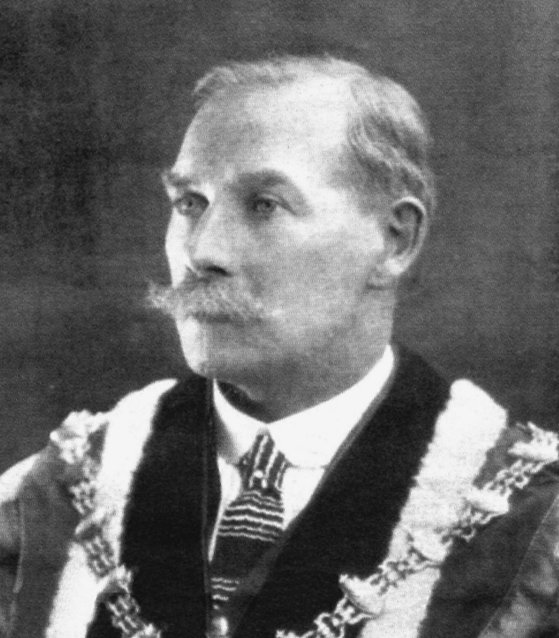
James Smellie in his
mayoral robe. |
In 1909 James became Chairman of the
Elementary, Higher and Technical Education
committees and became a magistrate in 1917. In
1924 he became an alderman and was Mayor of
Dudley from 1924 until 1926.
He lived at Comberton House, Kidderminster.
By the mid 1930s, James Smellie Limited also
produced coal and electric fires. The firm still
exists and is based at Halesowen.
|
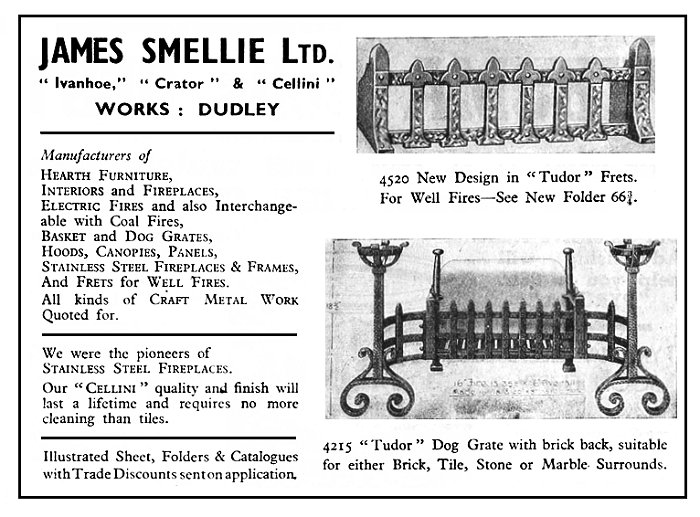
An advert from 1938. |
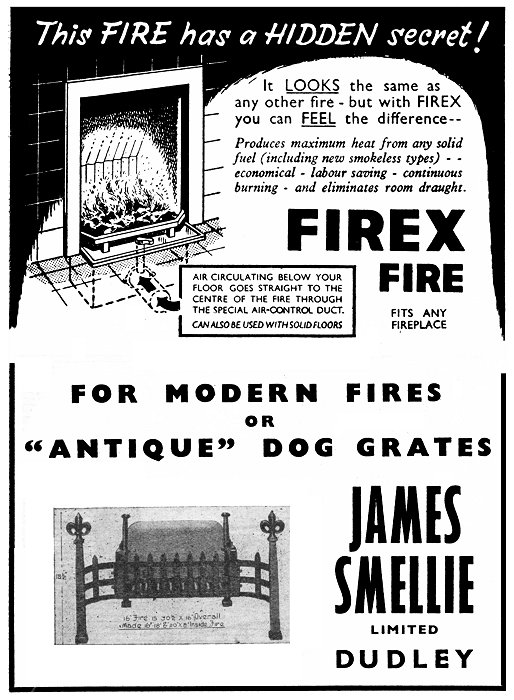
An advert from 1958. |
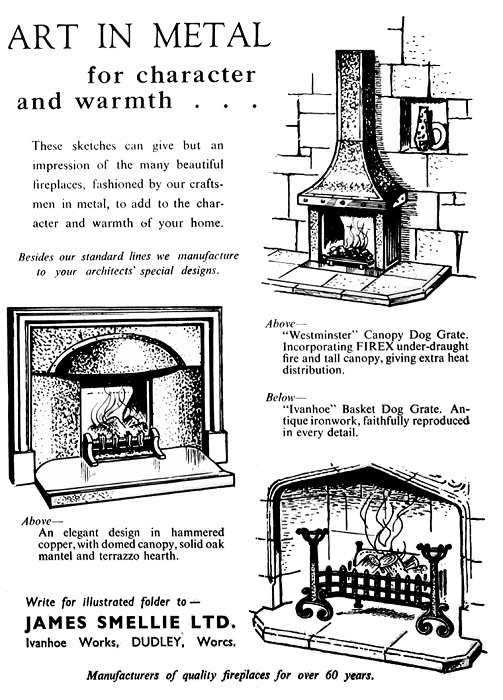
An advert from 1961. |
Dudley also had a number of
leather producers.
Hillmans, founded in 1852,
in Newhall Street, supplied leather to
cobblers. They then moved to 14 Hall Street,
a 3 storey building with a shop at the
front.
By 1870 they
produced whole hides, morocco leather, goats,
fancy leathers, belts, cases, oil seals, special
types of industrial leathers including oil butts
and stale butts for collieries, footballs,
tennis equipment and sports gear.
The firm was known as J. &
H. Hillman of Castle Leather Works in the 1890s,
and later as J. and A. Hillman.
They began to manufacture
industrial belting, which was very popular and
moved to larger premises on the corner of
Trindle Road and Porter Street.
In 1906 they took over the
neighbouring tannery of J. R. Tilley.
The firm later specialised
in handbags,
motor hides, belting and harness leather. In
1958 there was a fire in part of the
works. |
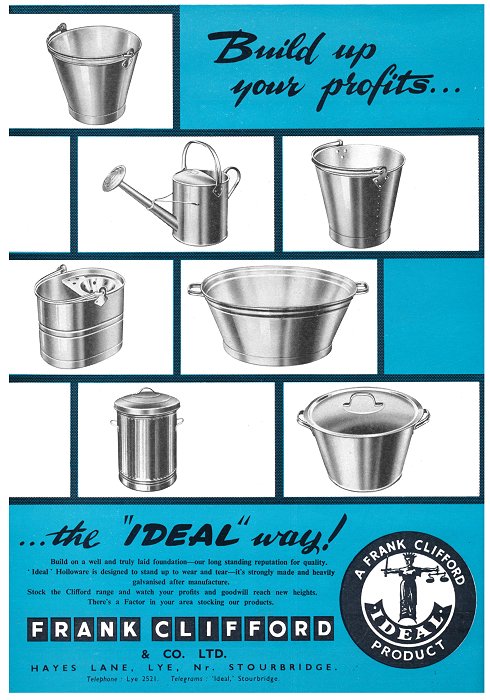
An advert from 1958. |
John Nayler & Son of Castle Belting Works,
Dudley, made leather belting.
John Douglas, Son and Company of Trindle Works,
made a range of products in 1922 including footballs,
golf bags, leggings and gaiters, purses and
wallets, fancy goods, fishing bags, game bags
and camera cases.
In 1947, Trindle Works was run
by
John Douglas, Sons and Company.
Their product
range included high
class fancy leather goods, handbags, wallets,
notecases, travel bags, document cases, attaché
cases, suit cases and golf bags.
|
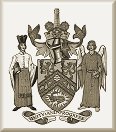 |
|
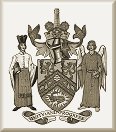 |
|
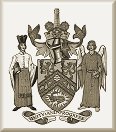 |
Return to the
20th Century |
|
Return to
the contents |
|
Proceed to
World War One |
|