F. H. Lloyd & Company
Limited - The 1960s
|
|
|
Read an article about
'The Good Old Days' from the Christmas 1960 edition
of 'The Steel Casting' |
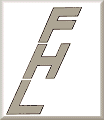 |
|
|
In 1962 the Lloyd group
acquired railway coupling manufacturer ABC Coupler,
shortly after it had gone into liquidation.
Read about
ABC Coupler Limited. |
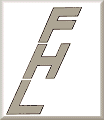 |
|
|
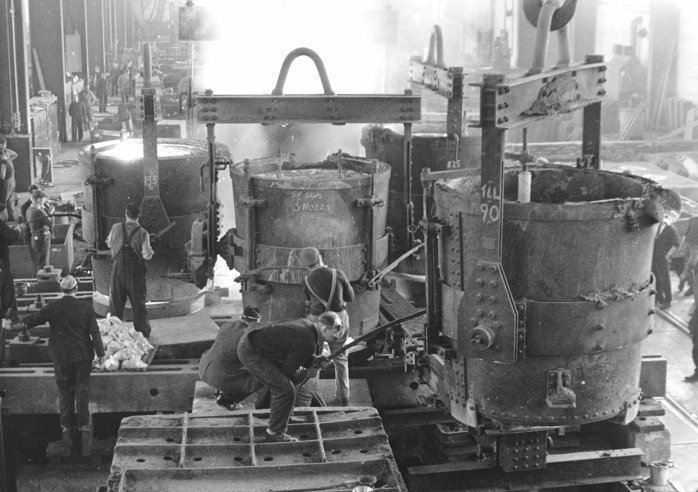
Using multi-ladles for a
large casting. From 'The Steel Casting',
courtesy of Wendy Marston. |
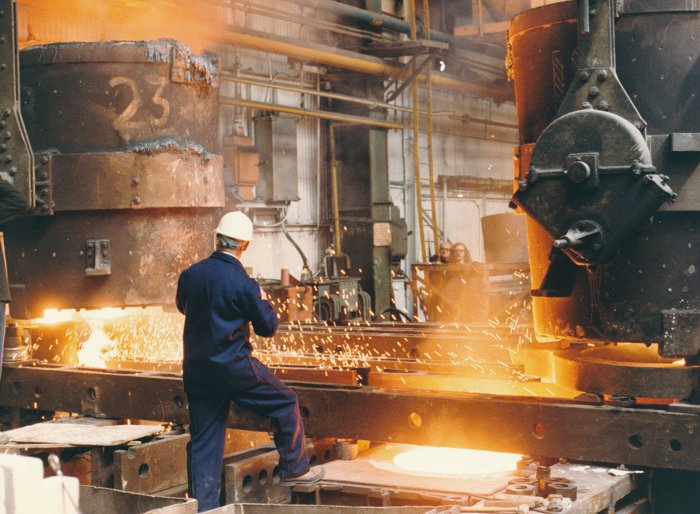
Casting another
multi-ladle job in the foundry. Courtesy of
Wendy Marston. |
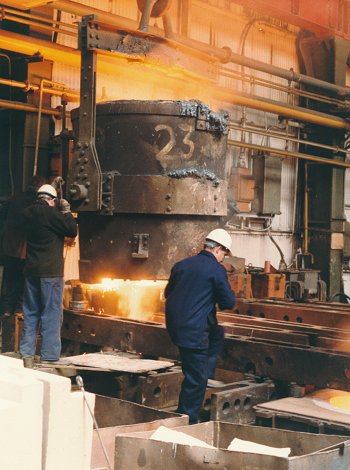 |
|
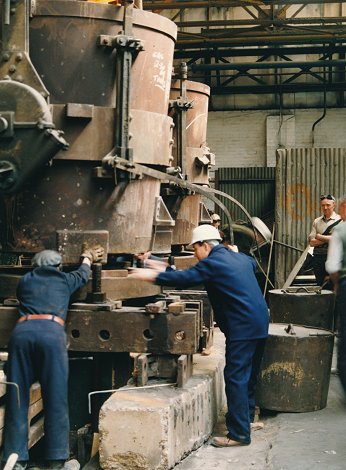 |
Two more
views of the casting process.
Courtesy of Wendy Marston. |
|
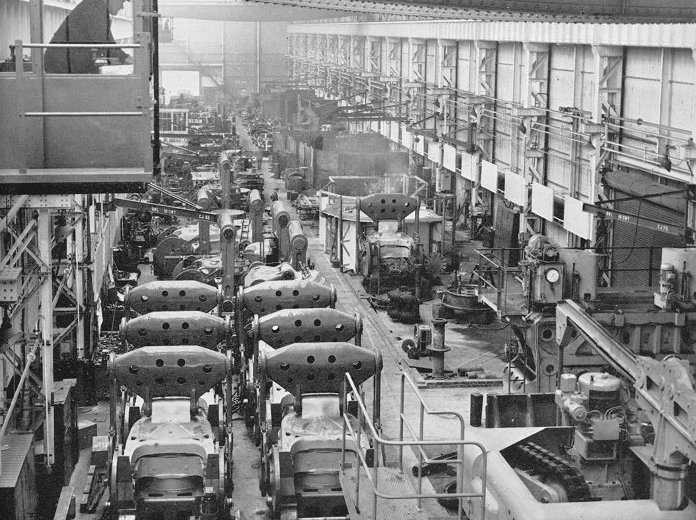
A batch of tyre presses in the
Machine Shop awaiting despatch in 1960. From 'The
Steel Casting', courtesy of Wendy Marston. |
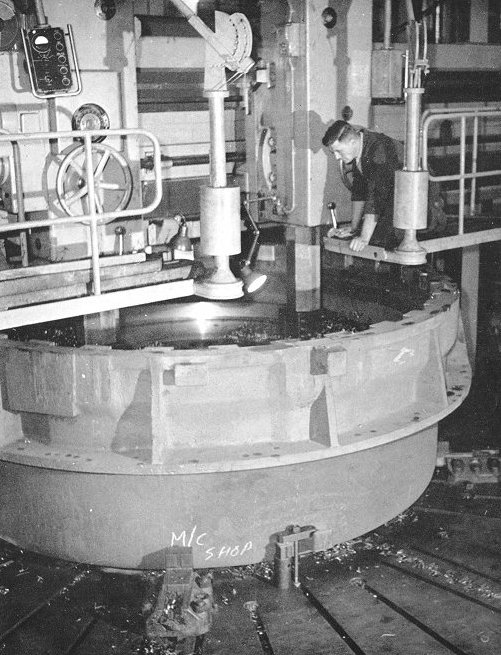 |
Precise machining in the
Machine Shop. From
'The Steel Casting', courtesy of Wendy Marston. |
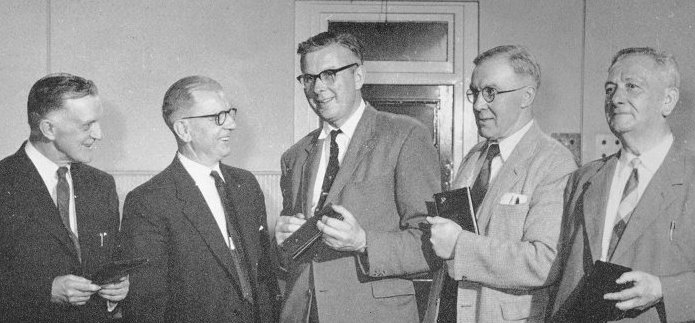
In July 1961, Mr. F. N. Lloyd
(centre) presented retirement gifts to four long
serving employees, Jack Davies, George Powell,
Roland Lavender, and Harold Parsons.
From 'The Steel Casting', courtesy of Wendy Marston. |
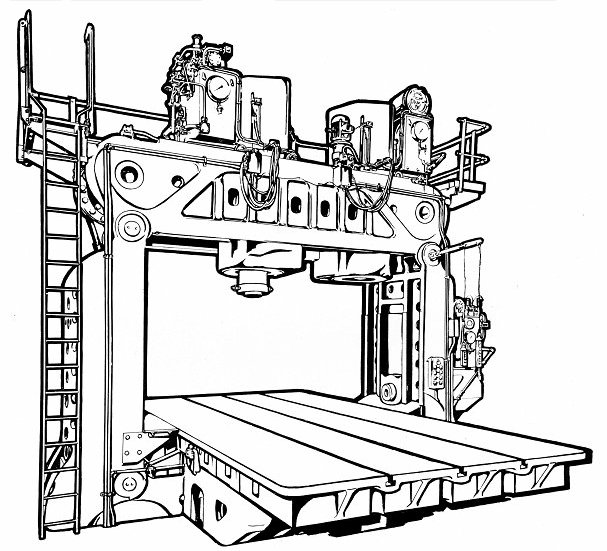
A Lloyd 400 ton press. The
presses were designed and built at the James Bridge
Works. The innovative design featured vertical and
horizontal rams, and a moving table, which were all
electrically controlled.
From 'The Steel Casting', courtesy of Wendy Marston. |
A huge steel
casting weighing 30 tons, designed and cast at James
Bridge in 1962. It is
part of a coil handling machine. |
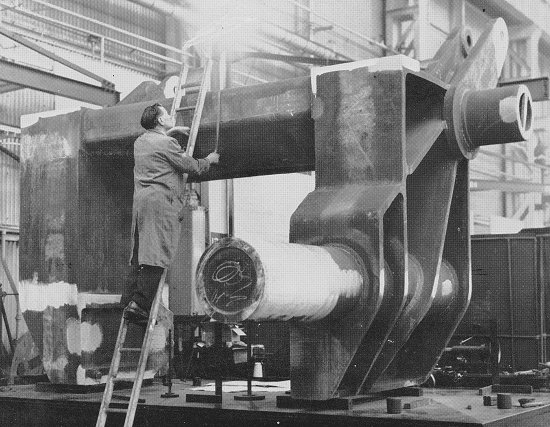 |
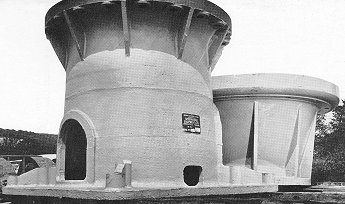 |
|
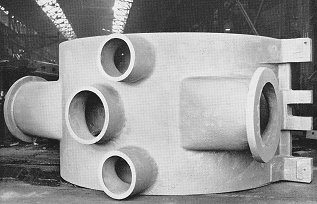 |
Two
large castings, cast at Burton and machined at
James Bridge. |
|
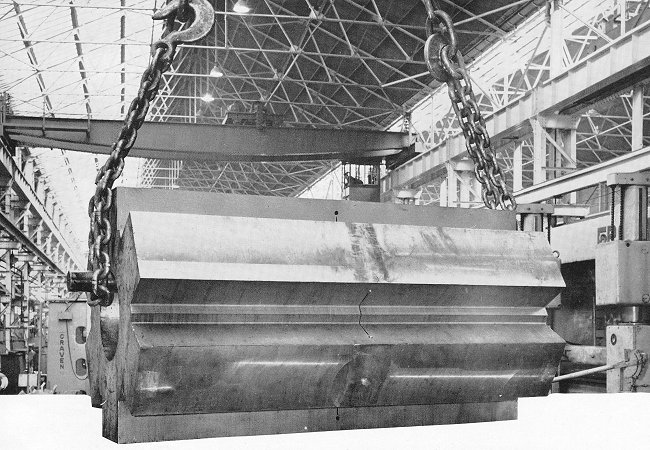
The first magnet wheel for the
C.E.G.B. to be cast in two halves and successfully
welded together at James Bridge. |
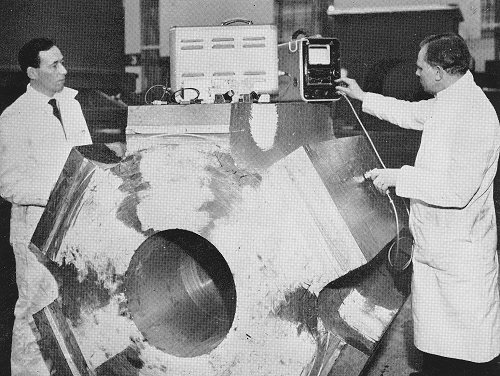 |
The 28 ton magnet wheel being
ultrasonically tested for cracks. |
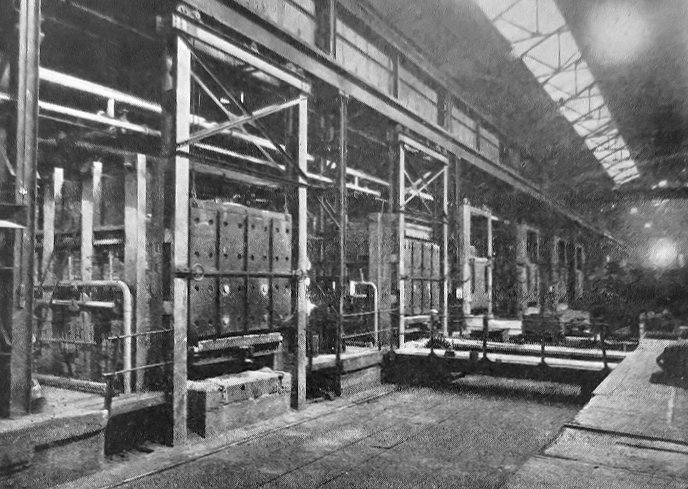
The electric heat treatment
furnaces at James Bridge were the best of their type in
the country. They had an accurate temperature range of
over 1,000 degrees Centigrade. |
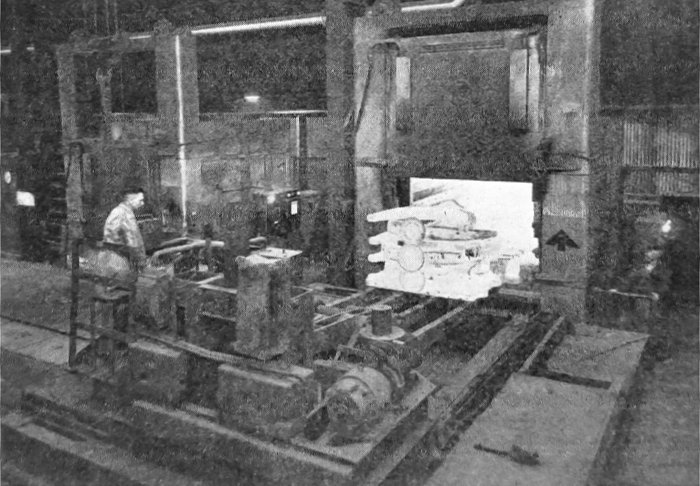
Removing castings from one of the
heat treatment furnaces. |
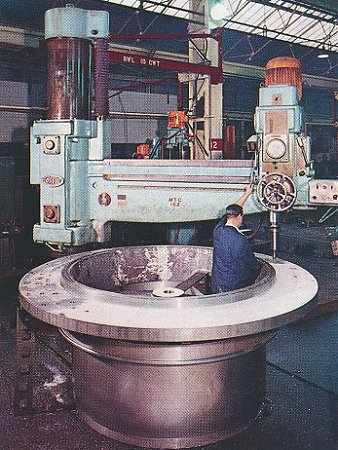 |
|
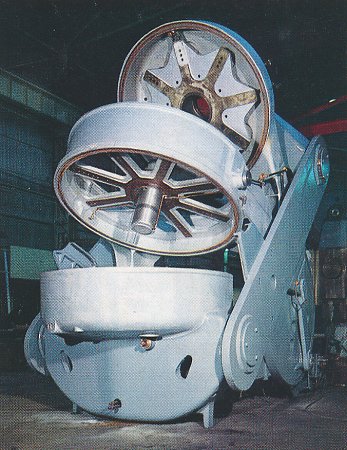 |
The firm's
largest radial drilling machine, an Asquith OD4,
at work on a power station feeder head. |
|
The
impressive MacLloyd 75 twin tyre press, designed
and built by the company. |
Part of the display
put on by Lloyds (Burton) Limited in 1962 at the
second Engineering Materials and Design
Exhibition and Conference at Earls Court. |
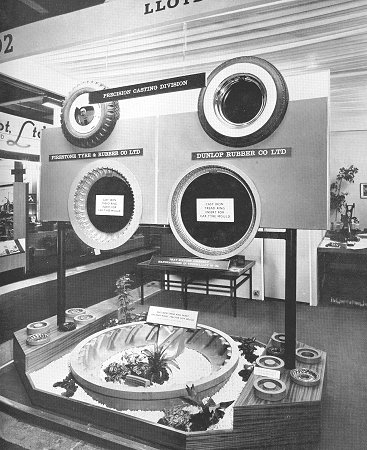 |
|
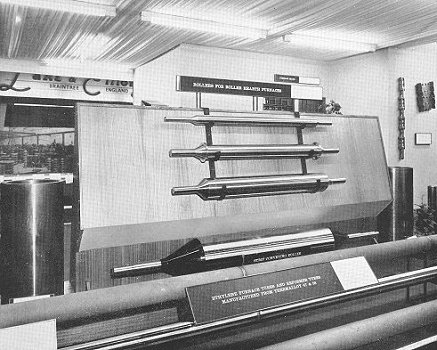 |
|
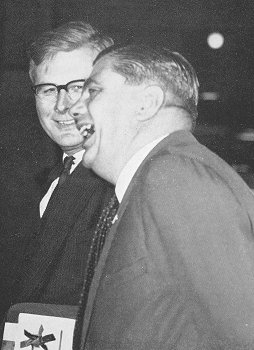 |
Another
part of the display. |
|
Mr. F.
N. Lloyd and V. T. Grantham. |
|
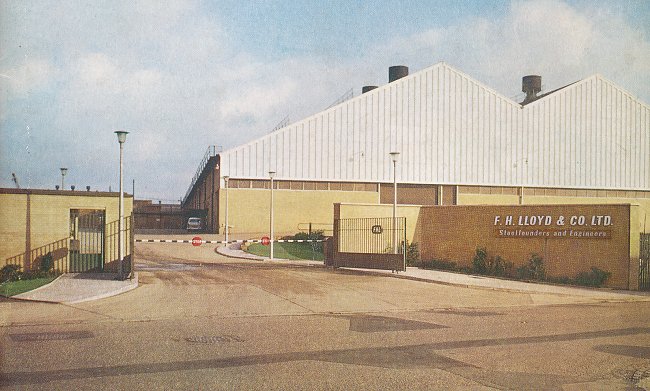
The works entrance with the
machine shop on the right. |
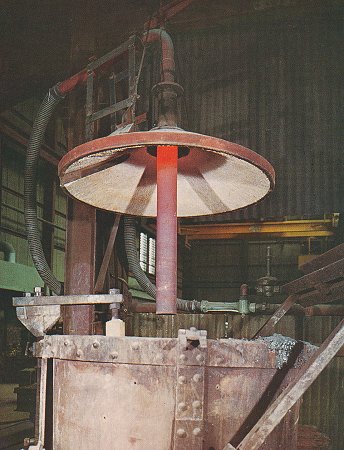
The ladle pre-heater unit. |
In 1962 one of the problems facing many foundries
was overcome at Lloyds (Burton) Limited. The ladles used
to transport molten steel around the foundry had to be
heated to ensure that there was no moisture in the
lining. Failure to do so could result in an explosion, if
the molten metal came into contact with moisture in the
lining. Ladles were usually heated using a large
burner, similar to a blowlamp, which was wasteful in
fuel and energy. Lloyds developed a radiant tube heater
using a special nickel-chromium steel, which was
resistant to oxidisation and wear, and did not distort.
The new pre-heater reduced ladle heating costs from
7s.6d. per ton to 1s.6d. per ton. 100 ton ladles could
now be heated to 600ºC. in
five hours. The first ladle heater unit was supplied to
the English Steel Rolling Mills Corporation Limited, at
Sheffield. |
An interesting job carried out
at Lloyds (Burton) Limited in 1962 was the building of
the twin expansion loop shown opposite, for the
Power-Gas Corporation of Stockton-on-Tees.
It was made of sections of
centrifugal tube that were welded together to form a
loop.
After completion it was
successfully pressure tested to 1,500 lbs. per square
inch. |
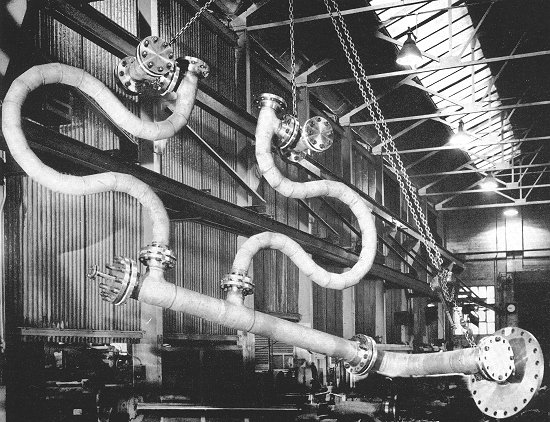 |
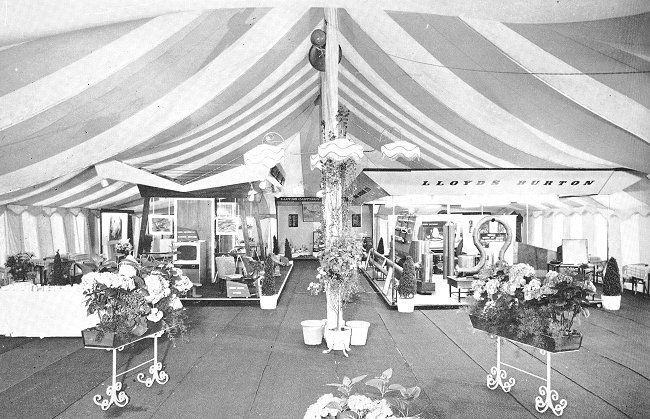
1962 was British Foundry Year,
commemorating the centenary of the opening of the first
steel-making furnace. Lloyds celebrated the event with
an exhibition, and works open days for the general
public. Vast marquees were erected on the sports ground
to display exhibits from the whole of the Lloyd Group.
During the three days of the exhibition, over 1,000
visitors and guests enjoyed the displays. |
Viewing the company's display
about a new technique called casting-weldments which
enabled Lloyds to produce a wider variety of
fabrications. Mild steel
castings and mild steel plate, varying in thickness from
1 inch to 12 inches were welded-together to form
fabrications which were then machined. |
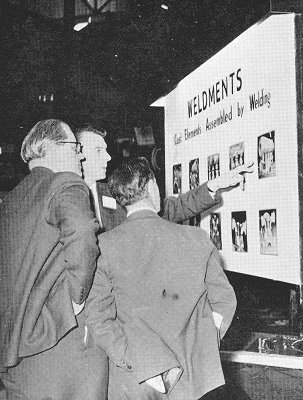 |
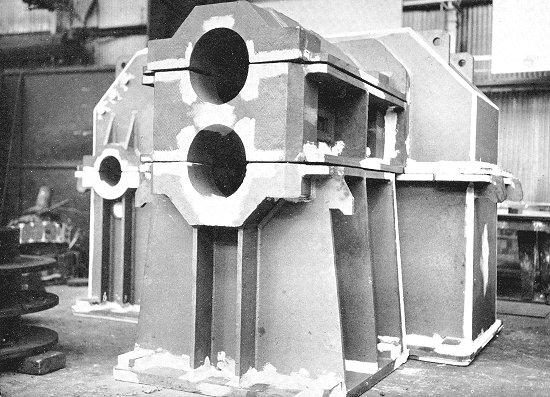
A casting-weldment
consisting of a fabricated rolling mill drive gearbox
produced for Henry Simon (Engineering Works) Limited.
It weighed 14 tons. |
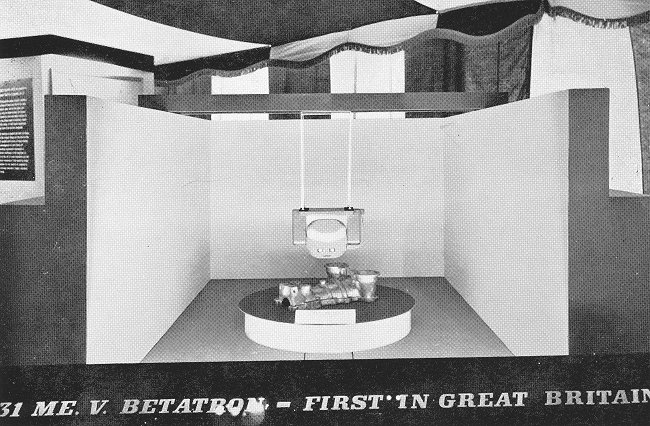
A model of the 31 MeV Betatron
that was installed at James Bridge Works. |
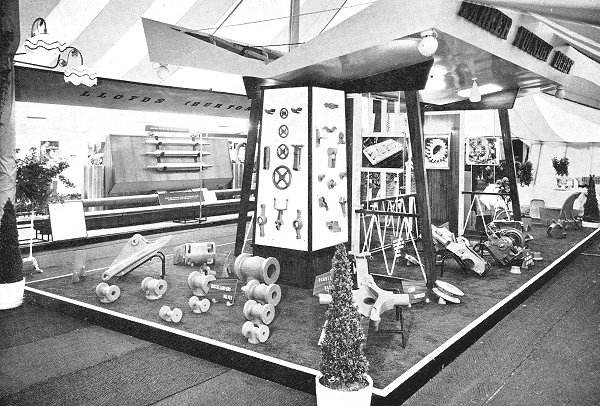
The Parker Foundry display. |
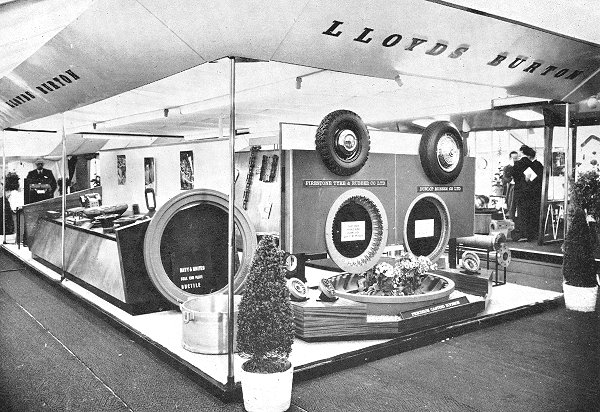
The Lloyds (Burton) display. |
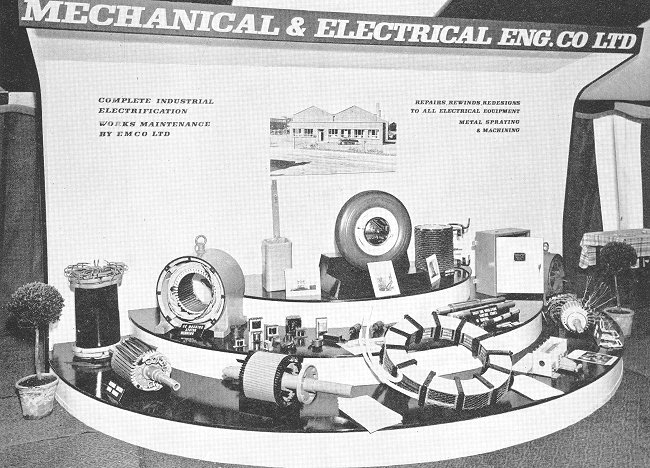
The Mechanical & Electrical
Engineering Company's display. |
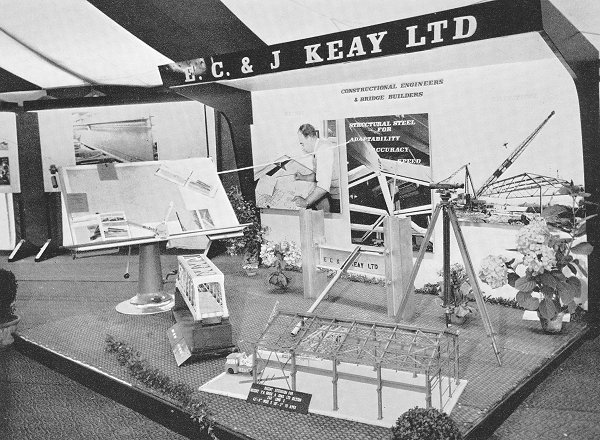
E. C. & J. Keay's display. |
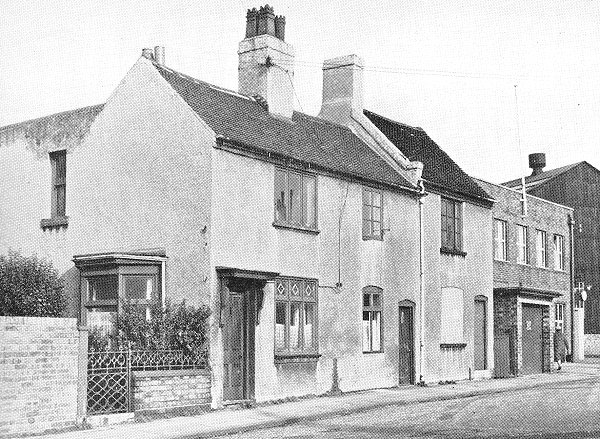
In 1962 the old cottages adjoining
the Park Lane entrance were demolished. |
In 1962 the Radiography Proving House opened at
James Bridge. It contained one of the latest pieces
of equipment for non-destructive testing, the
Betratron. The Brown Boweri 31 MeV Betatron is a
very powerful x-ray machine that was used for
radiographic inspection of thick-walled castings. It
produces x-rays of a shorter than normal wavelength
which is far more penetrative. Castings of up to 18
inches thick could be inspected. This was the first
installation of its kind in the country. |
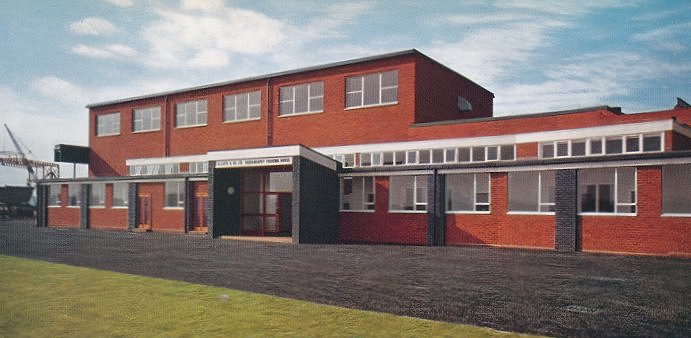
The Radiography Proving House.
From 'The Steel Casting', courtesy of Wendy Marston. |
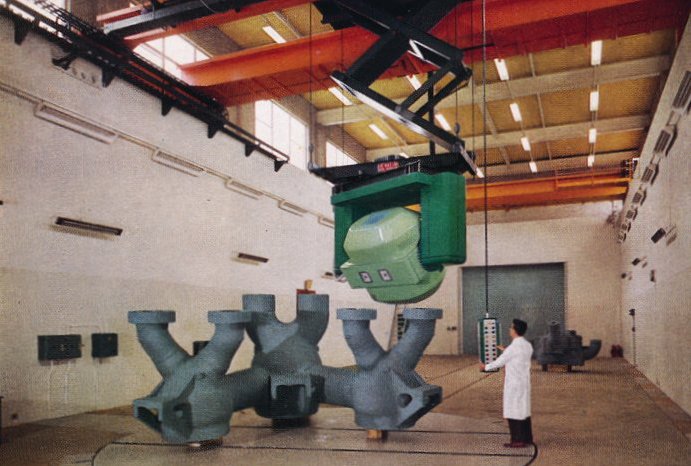
The Brown Boweri 31 MeV
Betatron. From 'The Steel Casting', courtesy of
Wendy Marston. |
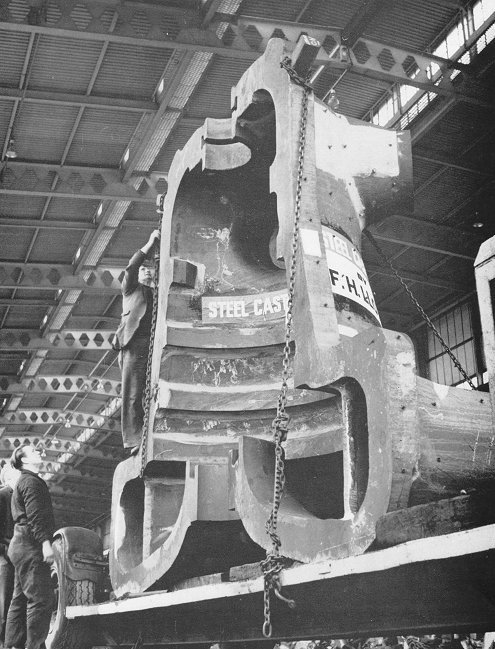 |
A large turbine casting is
got ready to be transported from the Wednesbury
site. From 'The Steel
Casting', courtesy of Wendy Marston. |
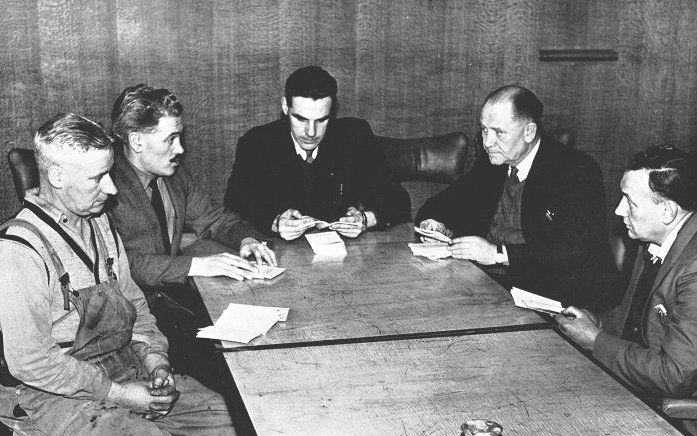
The Works Agents Committee.
Left to right: J. Rickuss, G. Williams, E. Green
(Chairman), S. Brookes, and
R. Bayliss. From 'The Steel Casting', courtesy of
Wendy Marston. |
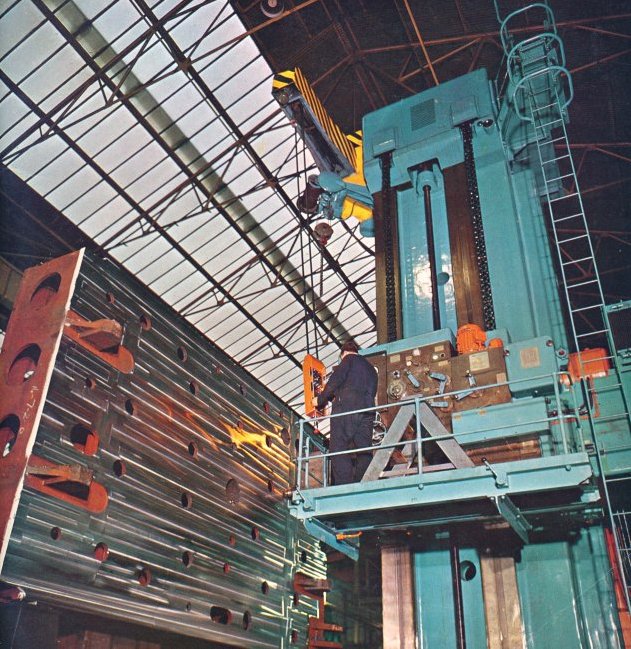
A new acquisition in the
Machine Shop in 1967 was an Asquith ram borer, seen
here machining a revolving frame for a Ruston
Bucyrus excavator. The machine had a maximum
vertical travel of 19 feet and a maximum horizontal
travel of 35 feet. It carried out both milling and
boring. From 'The Steel Casting', courtesy of Wendy
Marston. |
The Tipton Factory On 4th November, 1963 a team of men from James Bridge
works moved into the two empty bays of Wright's Forge in Factory Road, Tipton. Lloyds acquired the site in order
to fettle large turbine castings which were occupying
valuable space at James Bridge. Heading the team of ten was
George Wilkinson who had the task of setting up the
operation there. Initially there was no shotblast or heat
treatment facilities, just hard work.
Within twelve months, a shotblast plant and a heat
treatment furnace had been installed, and by the end of 1964
there were 13 welders, 17 finishers, 3 burners, 3 shotblasters, 2 heat treatment furnace men, 2 crane drivers,
and 1 labourer. By the 1970s the building had grown to four
bays covering 100,000 square feet. Around 3,000 tons of
fabrications were produced annually under the control of
George Roberts, Production Superintendent. Machinery in
the factory included a 700 ton twin 'C' frame hydraulic
press, designed and built at the James Bridge factory. It
could handle steel plate up to 16 feet wide and
¾ inch thick. There were 4
automatic gas profile cutters and fully automatic welding
machines. The Fabrications Section moved to Tipton
in 1966, and became a separate division of F. H. Lloyd and
Company Limited in 1967. Lloyds Steel Fabrications became
one of the country’s leading manufacturers of welded steel
fabrications. It was a great success.
Dick Howett was general manager, in charge of sales,
estimating and process planning, costing, buying and
production. The production superintendent was George Roberts
who was responsible for all production and work schedules.
He maintained liaison with customers on delivery and ensured that the right materials were in stock for the job.
Colin Hammond was chief planning
engineer at Tipton. His department prepared estimates
against enquiries, from which quotations were submitted. The
department also translated orders and drawings into detailed
working instructions for manufacture. George Arnold oversaw
quality control, which included checks on raw materials,
work in progress, and completed fabrications, using special
test equipment.
Muriel Simmons was secretary to Mr.
Howett, and the young lady, known as the voice of the division,
Barbara Potter, was the telephonist.
Plate preparation equipment in the
factory included four automatic gas profile cutters, a
Hancoline HL.3 and HL.4, a Hanco-ordinate c.90 and BOC
Bison, which were giant pantographs to exactly reproduce on
a sheet of steel a design or profile which was read from a
specially prepared drawing by an optical sensor. There were
also a number of straight-line cutting machines, and twin
C-frame hydraulic presses, designed and built by Lloyds.
Four welding processes were used:
manual arc, cored wire CO2, submerged arc and electra-slag,
the last two being fully automatic. The electroslag machine
is a prototype and the only one of its kind in this country,
manufact:ured by ESAB of Sweden. It could butt weld plates
up to 15 inches thick.
There was a North Sea gas fired heat
treatment furnace with a capacity of 24 ft. x 16 ft. x 11
ft. where fabrications were heated to a temperature of 650°C
to relieve any stresses set up by welding. The shot blast
plant was in a heavily shielded room measuring 27 ft. x 24
ft. x 18 ft. high with an opening top to permit the craning
in and out of fabrications. Steel pellets were 'shot' from a
nozzle by compressed air at high speed to scour the surface
scale from the fabrication and reveal the pristine grey
metal that is steel. |
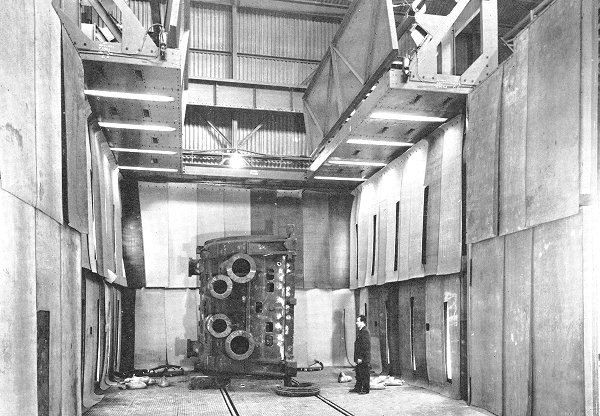
George Wilkinson and the new
shotblast at Tipton. |
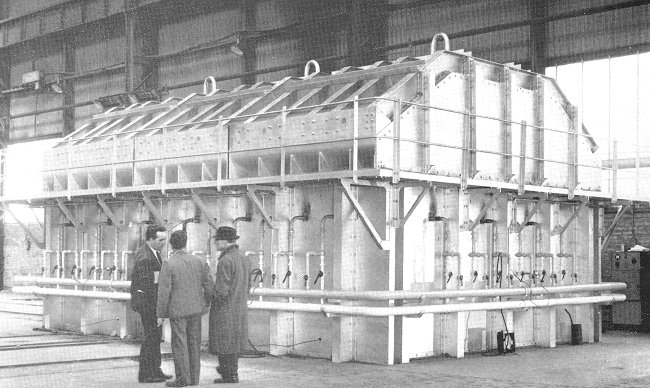
George Wilkinson on the left and
the heat treatment furnace, larger than the one at James
Bridge. |
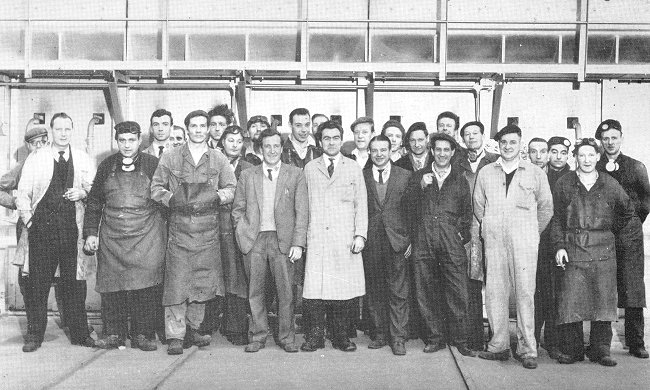
George Wilkinson and his team. |
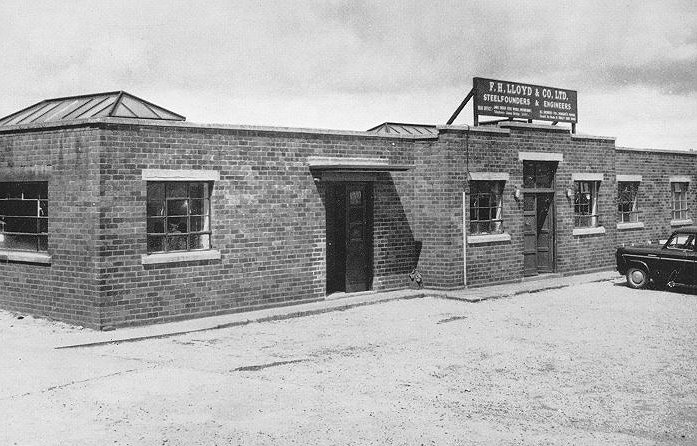
In the autumn of 1965 a new
canteen opened on the Tipton site. It became known
as the 'Wilkeyville' canteen, named after the boss,
George Wilkinson. On the opening day, hot meals were
brought from the James Bridge canteen by Ted
Hardingham, and Wilf Vann. At 12.30 the doors
opened, and in a few minutes 31 piping hot meals
were served, consisting of hot pork with all the
trimmings, followed by blueberry pie. From 'The
Steel Casting', courtesy of Wendy Marston. |
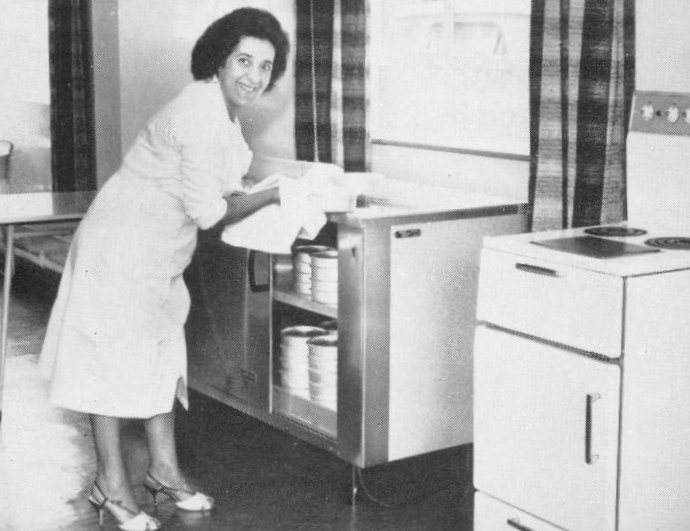
Mrs George Wilkinson gives a
helping hand. From 'The Steel Casting', courtesy of
Wendy Marston. |
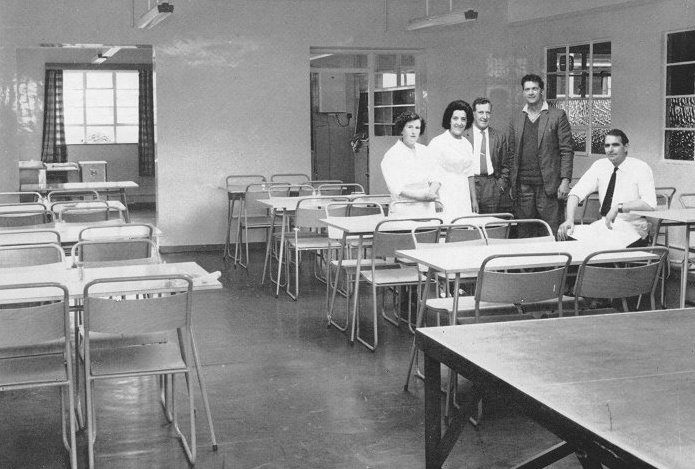
Mr. and Mrs George Wilkinson and the canteen staff
get ready for the official opening. Left to right:
Mrs Keatings, Mrs Wilkinson, George Wilkinson, Wilf
Vann, and Ted Hardingham. From 'The Steel Casting',
courtesy of Wendy Marston. |
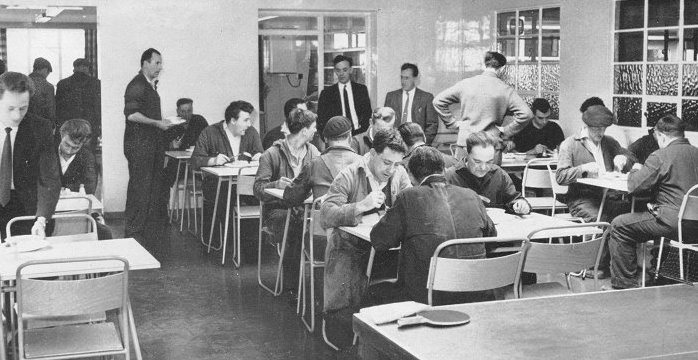
The meal is greatly enjoyed by
all of the diners. From 'The Steel Casting',
courtesy of Wendy Marston. |
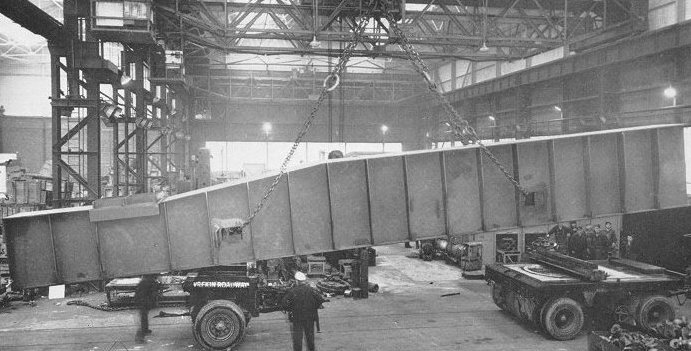
A large fabrication built at
the Tipton site, being readied for transportation.
It is a half measuring beam for a rolling mill,
weighing 40 tons, with a length of 106 feet. It is
destined for Brightside Engineering Company of
Canada. From 'The Steel Casting', courtesy of
Wendy Marston. |
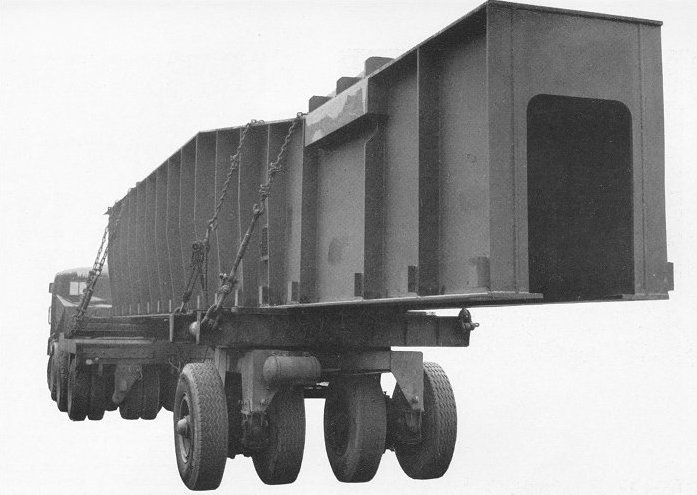
The fabrication gets underway.
From 'The Steel Casting', courtesy of Wendy Marston. |
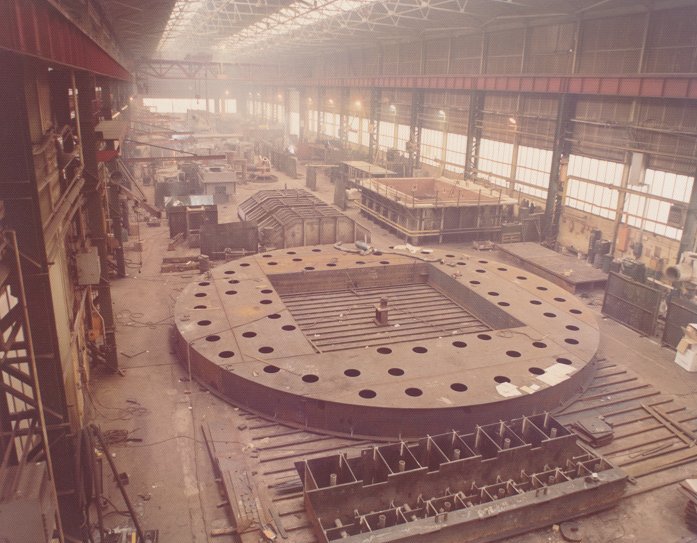
A view inside the Tipton
factory. Courtesy of Wendy Marston. |
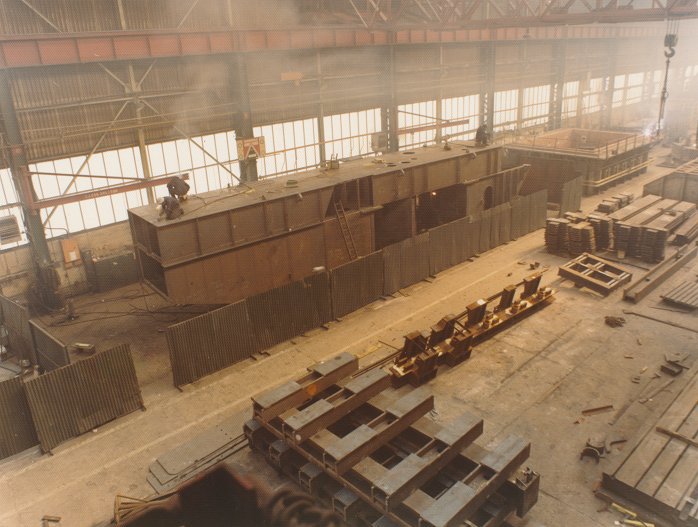
A large fabrication
nears completion in the Tipton factory.
Courtesy of Wendy Marston. |
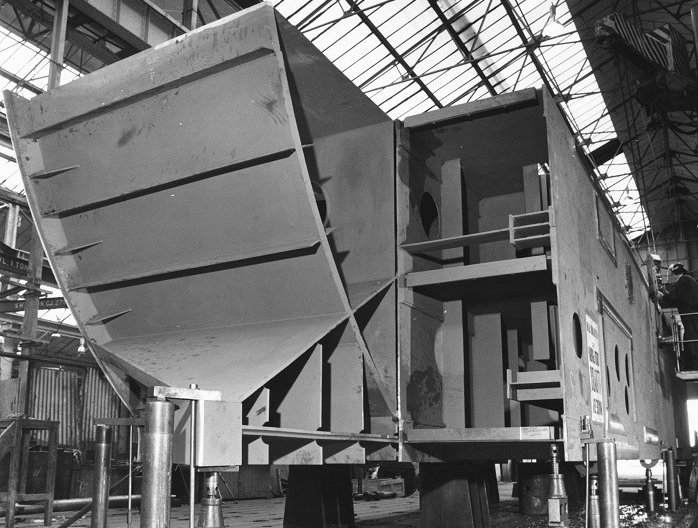
The fabrication is readied
for transportation. Courtesy of Wendy Marston. |
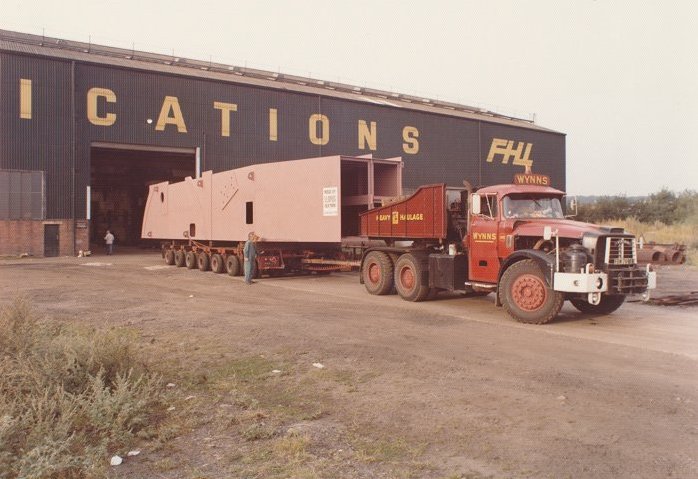
The fabrication leaves the
Tipton factory. Courtesy of Wendy Marston. |
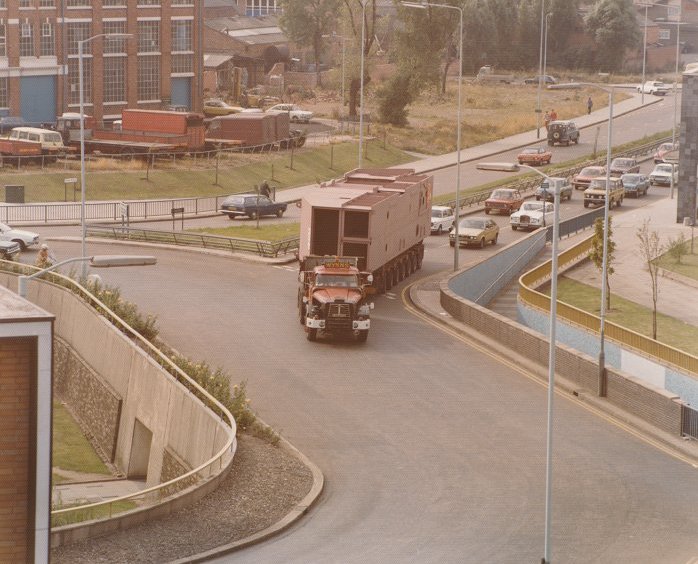
The fabrication leaves
Penn Road in Wolverhampton and enters the Ring
Road. Courtesy of Wendy Marston. |
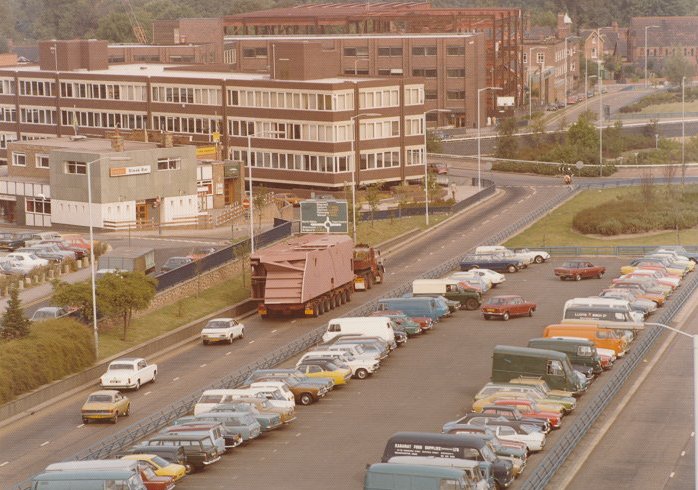
The journey continues as
the vehicle approaches Chapel Ash island.
Courtesy of Wendy Marston. |
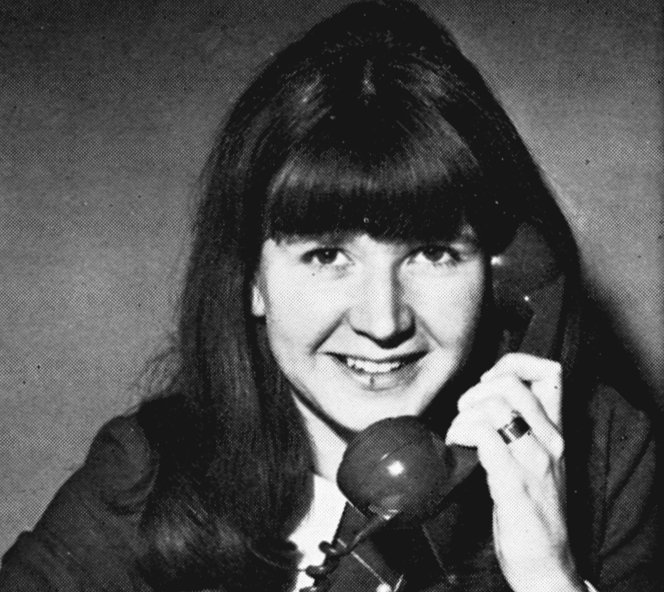
Barbara
Potter, Receptionist & Telephonist at the Tipton
factory. |
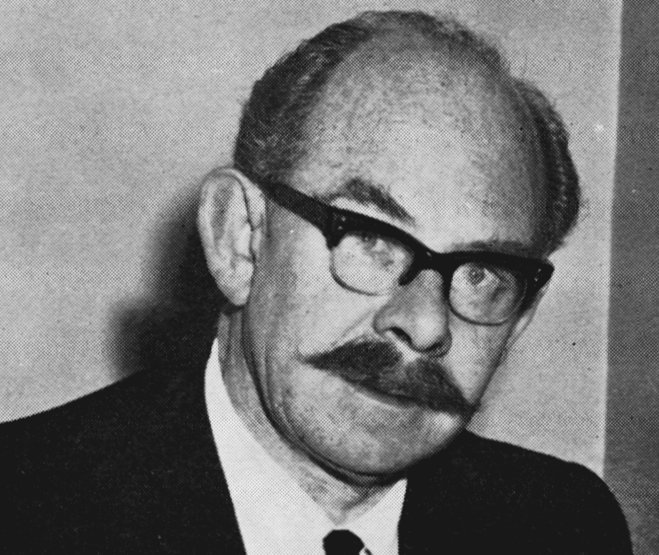
Dick
Howett, the General Manager at the Tipton
factory. |
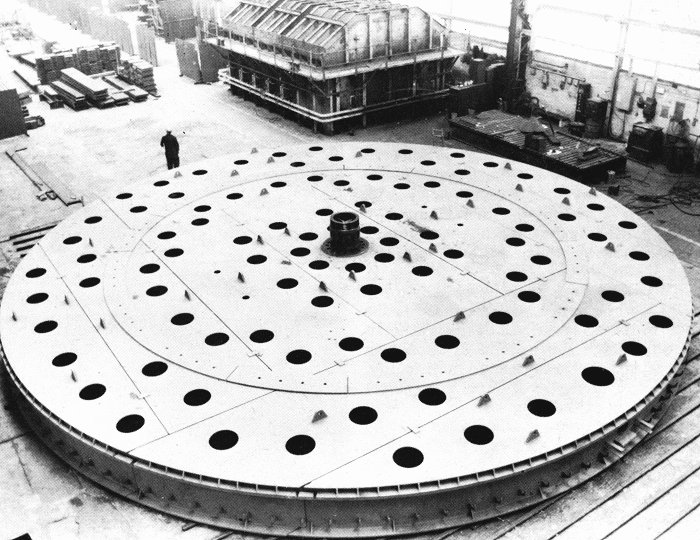
A 50 ft.
fabricated revolving base for a Bucyrus
Erie walking dragline which was built at
the Tipton site in 1975. From 'The Steel
Casting', courtesy of Wendy Marston. |
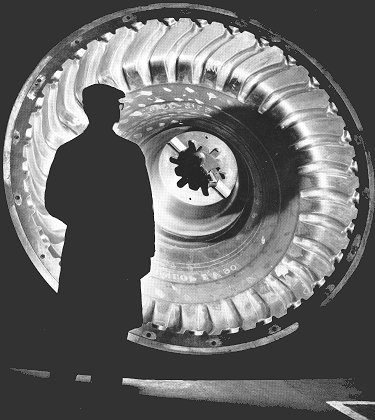
The largest British tyre mould ever
made. Produced by Lloyds (Burton)
Limited for Dunlop. |
Around 1963 the Lloyd Group expanded with the formation
of F. H. Lloyd & Company Limited, Cardiff, and new
techniques were introduced including the CO2 sand
process, particularly for cores. Also shell moulding and
shell core making, and the use of CO2 as a gas
shield for wire welding. On 1st April, 1966 the local
boundaries changed as a result of the Local Government
Reform Act, after which the whole of the James Bridge site,
except for the sports ground was in Darlaston.
|
|
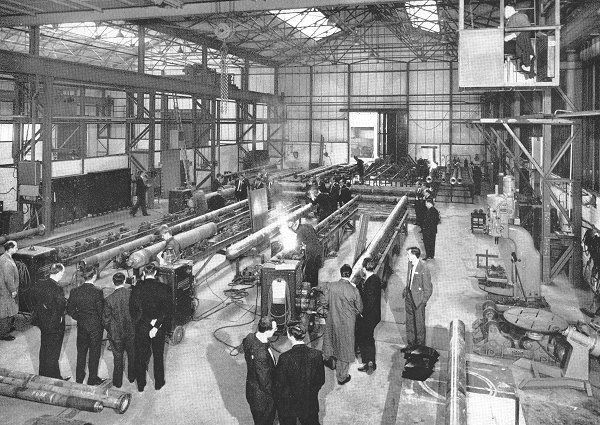
Visitors study the welding of
centrifugally-cast thermalloy tube during a two day
seminar at Lloyds (Burton) Limited. |
|
|
Read an article about
the new heavy foundry |
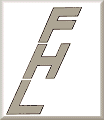 |
|
|
In 1966 The Lloyd Group acquired the group of
companies owned by N. Hingley and Sons including M. and
W. Grazebrook, Dudley; John Bagnall and Sons,
Wednesbury; Wright Hingley, Netherton; and Brown, Lenox
and Company (Pontypridd). Hingleys had previously been run by
a relative of the Lloyds, Cyril Lloyd, a descendant of
the Lloyds banking family, who died in 1963. Brown
Lennox, based at Pontypridd, were an ideal addition to
the Lloyd Group. They produced steel castings from a few
pounds to four tons in weight, in all compositions from
carbon steel to low and medium alloy steel. They had
excellent testing facilities including gamma ray,
ultrasonic, and magnetic crack detection, and a proving
room for testing chain up to 400 tons.
On 25th October, 1967 Lloyds acquired another
company, Thomas Summerson & Sons Limited of Darlington.
The company, which had been producing steel castings
since 1910 became Lloyds (Darlington) Limited. |
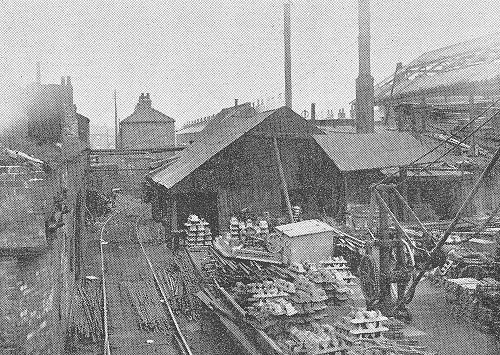 |
Thomas Summerson & Sons
original foundry at Albert Hill Works, Albert Street,
Darlington. |
Cecil Whitehouse, Managing
Director of Lloyds (Darlington) Limited, an old
foundryman whose passions included cricket, football,
and golf. It was thanks to his efforts that the old
company survived for so long. |
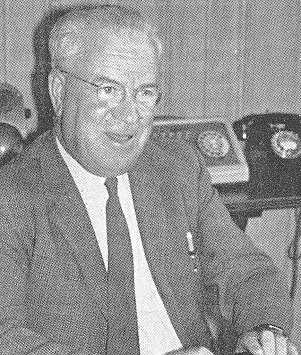 |
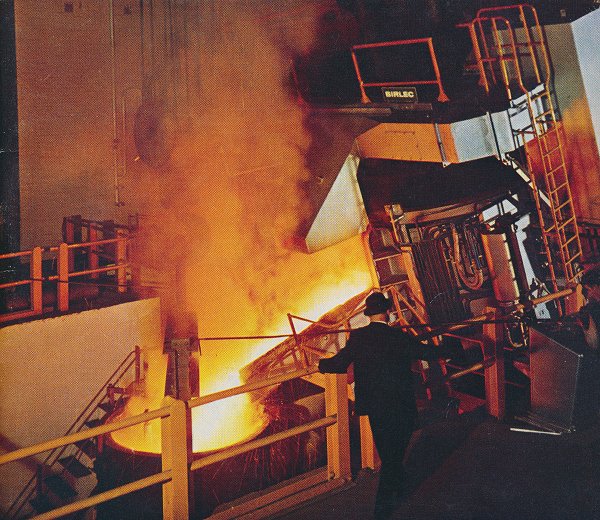
Tapping the 25 ton melting furnace
that began operating at James Bridge in January 1967. |
On 12th August 1969 F. H. Lloyds
became part of F. H. Lloyd Holdings Limited. In
August 1969 F. H. Lloyd Holdings Limited was created to
oversee the various companies in the Lloyd group. The
Managing Director was Mr. Francis Nelson Lloyd. On 5th
September, 1970, Francis Nelson Lloyd retired and
handed-over to his younger brother Mr. Michael Charles
Lloyd. |
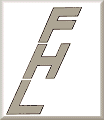 |
|
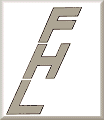 |
|
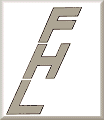 |
Return to the
late 1950s |
|
Return to
the contents |
|
Proceed to the
later years |
|