Other Industries
Wednesbury was at the centre of a
vast area of industrialisation, which greatly affected
the landscape and everyday sights and sounds.
In 1854 John Nock Bagnall published
his book "A History of Wednesbury in the County of
Stafford" which includes a chapter describing Wednesbury
as it was at the time. In the book he describes the view
from Church Hill at night:
Notwithstanding the great change that
has taken place in the appearance of the
surrounding country, there are but few
places which afford so extensive and
striking a panorama of the mine and
metal district as Wednesbury Hill,
"taking in," as a modern historian
expresses it, "within its lofty glance
the burning, fiery furnaces of West
Bromwich, Tipton, Coseley, Bilston, and
Darlaston; the horizon, miles upon
miles, dotted about with smoking,
blazing coke hearths, appears under the
black, sooty roof of nightfall, like a
large illuminated minster, devoted to a
ritual of the ancient Parsees, or fire
worshippers, and eclipsing the very
clouds of heaven in their gigantic
wreath of incense.
And a strange, wild, savage music seems
to accompany these loud litanies; bell
and ball, hammer and shears, crank and
chains, wheels and rolls, steam, blast
and engine screams, yell and howl, and
shriek and roar and hiss, and above them
all, the big shout of the forgeman, or
call of the collier, seems ever and anon
to set them yelling, howling, shrieking,
roaring, and hissing with a renewed grim
energy, as if they were resolved to
deafen every other tone of mortal sound
except their own hideous minstrelsy.
And when the mild, quiet moon looks down
at times upon the riot, like a 'blue
light' on a field of fireworks, so
stillness looks more still in the
contrast of the rioting, and she seems
timidly to steal away faster than usual
through the mountain masses of drifting
smoke clouds, that irreverently smoke
her face as if she was a common street
lamp.
The stranger shudders as he beholds the
scene. Far as the eye can reach it is a
series of fires; there seems to be too
much fire and too much fury to be ever
put out again. The dread is that it must
grow and spread beyond its flaming
boundaries, till the whole realm be in a
general blaze, which all its island
waters cannot quench, and bonny England
become a holocaust."
|
|
Today the scene couldn't be more
different. It is now a tranquil scene, only broken by
the roar of traffic on its way through the town, and
illuminated at night by countless street lamps,
enveloping the whole area in an orange glow.
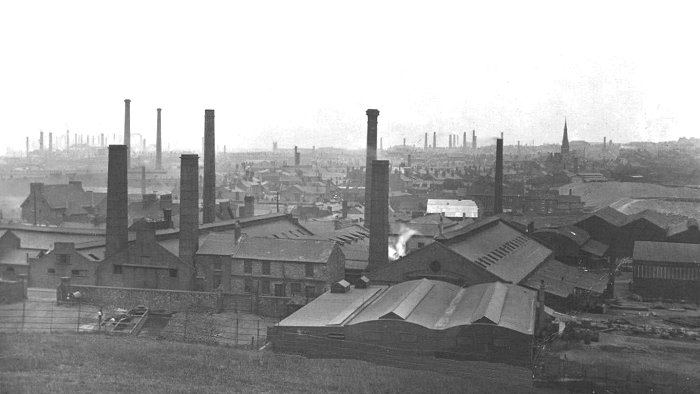
Industrial Wednesbury. From an old
postcard.
Wednesbury
manufacturing companies, listed in Peck's 1896
to 97 Circular Directory:
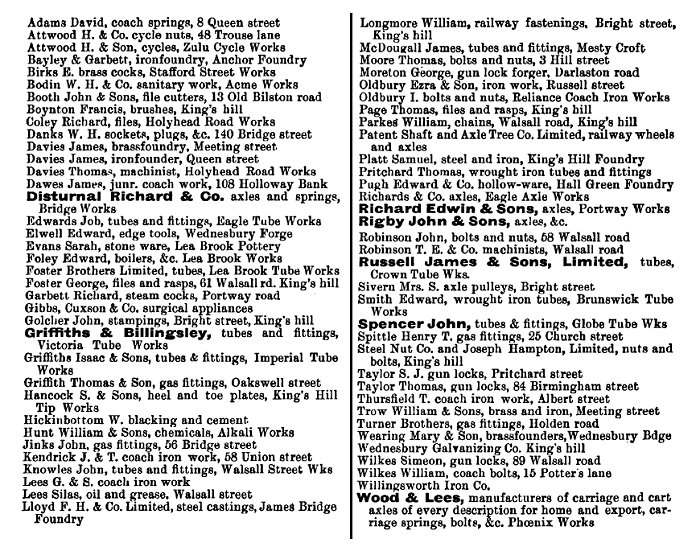 |
Iron and
Steel
The earliest references to iron
mining in the area are from 1315 but there are no
records of iron smelting until the 16th
century. Much of the local ore would have been exported
to other towns until the later part of the 18th
century when the growth of local industry provided a new
market. Early iron making used large amounts of
charcoal, and so much of the local woodland would have
disappeared in the process. The locally found iron ore
would have been heated with a large amount of charcoal
in a bloomery, consisting of a hearth of stones, covered
by a dome of clay. A constant blast of air would be
applied using bellows, and a spongy, metallic bloom of
iron would be the result. The bloom would then be
reheated and worked down with a large hammer to remove
some of the impurities (slag and clinker), to make the
iron hard enough for forging. The end product would then
be wrought into bars or rods for the production of
horseshoes, nails or tools.
In 1597 there was a water-powered iron mill (a
forge) owned by William Comberford and leased to William
Whorwood, which is mentioned in the records of the
Quarter Sessions. Two of the employees were Blaise
Uyntam,
a finer, and William Heeley, a hammer man. In
1606 Walter Coleman leased the forge for 21 years. It
had finery and chafery hearths. In 1708 it was owned by
Richard Shelton and leased to John Willetts, who
probably used it as a rolling mill.
|
In 1726 he is listed as a saw maker. The forge was
possibly at Wood Green and later known as Wednesbury
Forge, owned by the Elwell family and situated at the
confluence of the southern and western branches of the
Tame. The power came from two water sources, which were
dammed, and drove waterwheels from the floodgates. The
wheels would power a large hammer consisting of
a timber beam
bound with iron hoops (the helve), set in an iron pivot
(the hurst). A cast-iron head weighing 7 or 8 cwt would
be fitted to the end of the helve, and this would fall
onto the iron bloom placed on the anvil below. The
hammer was operated by cams and large wooden pegs fixed
in a drum. At intervals the iron would be removed from
the anvil and reheated, the process continuing until it
had been converted into wrought iron.
There were two
types of hearth at the forge, the
finery and the chafery. Both would have burned charcoal
and been fed with air from bellows. In the smaller
finery the lump of iron was re-melted
to produce a bloom; a lump of iron with slag. |
The bloom would be hammered to
consolidate the iron and remove much of the slag. It
would then be reheated in the larger chafery and
hammered to draw it out into a bar of various widths and
lengths suitable for blacksmiths, coopers, nail
makers, toolmakers, and wheelwrights.
The chafery would have held several bars at a time,
all in various stages of production. |
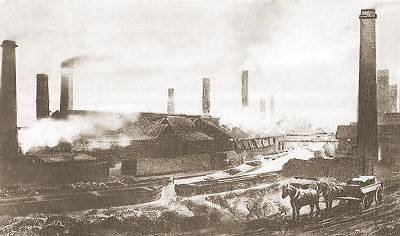
The Patent Shaft &
Axletree Company at the turn of the 20th
century. |
|
In 1675 Frederick de Blewstone from
Germany constructed an experimental furnace in the town,
in an attempt to smelt iron using coal, traditional
charcoal being in short supply. Unfortunately the
attempt failed because of contamination from the
sulphurous gasses emitted by the coal.
By 1785 there were 4 forges in the
town:
Wednesbury Forge,
Wood Green |
Adams’s Forge,
Camp Hill Lane |
Sparrow’s Forge,
Fallings Heath |
The iron mill at
Wednesbury Bridge |
Adams’s Forge opened in Camp Hill
Lane around 1760 in the middle of the Seven Years War.
The business sold special quality iron to the
government, made from specially selected scrap. As the
forge was situated on the south side of the town, well
away from any natural watercourse, the hammers were
powered by a horse gin. This was superseded by one of
the earliest Watt steam engines in the area, and
supplied with water from a large reservoir extending
from Camp Hill Lane to Camp Street, possibly from a
spring. Unfortunately unhealthy gases arose from the
water and so in 1869 the company moved to Ridgeacre,
West Bromwich.
Sparrow’s Forge was run by Mr.
Edwards in partnership with Edward Elwell, who later ran
Wednesbury Forge. It was situated next to Forge Pool and
Forge Pool Colliery, just off Sparrow’s Forge Road, now
called Park Lane. The forge was initially powered by a
horse gin, and later used water from the adjacent Forge
Pool, which flowed into Willenhall Brook. By 1851 it
became Heath Works, owned by Addison
Russell, and sometime before 1900 the works
closed, and the buildings were demolished.
The most common method of producing
wrought iron from pig iron in the 19th century was
puddling, invented by Henry Cort in 1784.
|
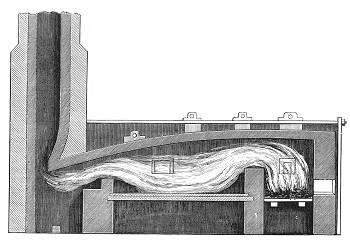
A section through a puddling
furnace. |
Pig iron or scrap cast iron was melted in a puddling
furnace and stirred with a long pole, which reduced the
carbon content by bringing it into contact with air, in
which it burned.
The puddling furnace heated the iron by reflecting the
exhaust gases from the fire down onto it. In the drawing
opposite, the iron would be placed in the central
section. Because it was not in contact with the fire,
cheaper, poor quality fuel could be used. After puddling
the iron was hammered and rolled to remove the slag. |
The iron mill at Wednesbury Bridge opened in the 17th
century and may have been built by William Comberford,
who planned such a mill in 1606. In 1761 the buildings
were owned by John Wood, the son of ironmaster William
Wood who lived at the Deanery in Wolverhampton. |
John obtained a patent in 1761 for making malleable
iron from pig iron. He also melted selected scrap, and
produced iron that was as good as the best Swedish iron
of the day, often being used by the local gun barrel
makers. In 1816 the works included a lift hammer, a tilt
hammer, and sufficient warehouses for storing scrap, and
finished iron. According to F.W. Hackwood, John lived
“in great splendour” in the town, and was buried there
after his death in 1779. |
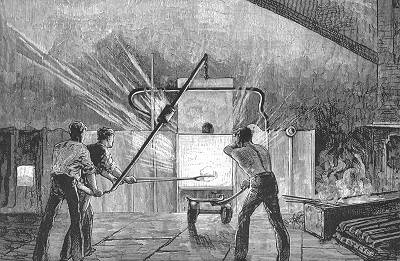
Puddlers at work. |
The first coke furnace in the town
was at Hallens’ Ironworks, which stood by the canal on
part of the site later occupied by the Patent Shaft
Steelworks. The following description of the works is
from Aris’s Gazette of 6th January, 1800:
A capital set of ironworks,
consisting of a blast furnace, foundry, boring mill,
forges, slitting and rolling mills, pattern and smiths
shops, warehouses, six workmen’s houses and every
suitable convenience for carrying on a very extensive
trade, advantageously situated on the banks of the
Birmingham Canal at Wednesbury: the whole comprising of
about two and a half acres of freehold land with
valuable mines of coal, ironstone and clay under the
same; together with all the machinery, implements and
tools now on the premises.
By 1830 there
were only two furnaces in the town that were used for
iron smelting, which is surprising considering that
large amounts of iron ore were mined locally. The first
was Matthews and Company who ran Broadwaters Furnaces.
They had 2 furnaces which produced 6,368 tons of pig
iron in 1830. The second was Lloyds and Fosters at Old
Park Iron Works. In 1823 they had one furnace which
produced 2,600 tons of pig iron in 1823, and in 1830
there were two furnaces producing 5,280 tons of pig
iron.
|
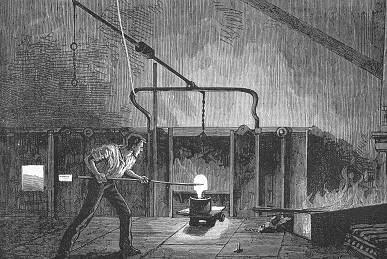
Tapping a puddling furnace. |
Marshall & Mills who ran Monway
Iron Works produced the best gun barrel iron in the
world. Their customers included the Birmingham gun
makers, and the British and American governments. By
1844 their iron sold for £44 a ton.
Also in the 1840s Adams & Richards of
Bridge Street were producing coach springs. |
|
|
Read a report from 1843
about
the employment of children in
the town |
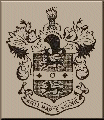 |
|
|
White’s
directory of Staffordshire from 1851 lists the following
iron and steel companies in Wednesbury:
George Adams & Company,
Camp Hill Lane |
John Bagnall & Sons,
Imperial Works, Leabrook |
Colburn & Groucett,
Broadwaters |
Fletcher, Rose & Company,
Victoria Works, Leabrook |
Lloyds, Fosters &
Company, Old Park Works |
John Marshall, Monway
Iron and Steel Works, Leabrook |
Maybury & Williams,
Leabrook |
David Rose, Moxley Forge |
Addison Russell, Heath
Works |
Thomas Wells, Moxley Iron
& Steel Works |
Others included
Gospel Oak Ironworks owned by Philip Williams & Sons,
Brunswick Iron Works, owned by Henry Pitt, and Bull's
Bridge Ironworks owned by Molineux & Company.
The Victoria
Ironworks at Leabrook were run by the Thorneycroft
brothers, Edward and George Bernard Thorneycroft, who
also ran Shrubbery Iron Works in Wolverhampton. Their
business in Wednesbury was declared bankrupt, as can be
seen from the notice below. The factory was then
acquired by
Fletcher, Rose & Company
and in 1852 by the Patent Shaft and Axletree Company.
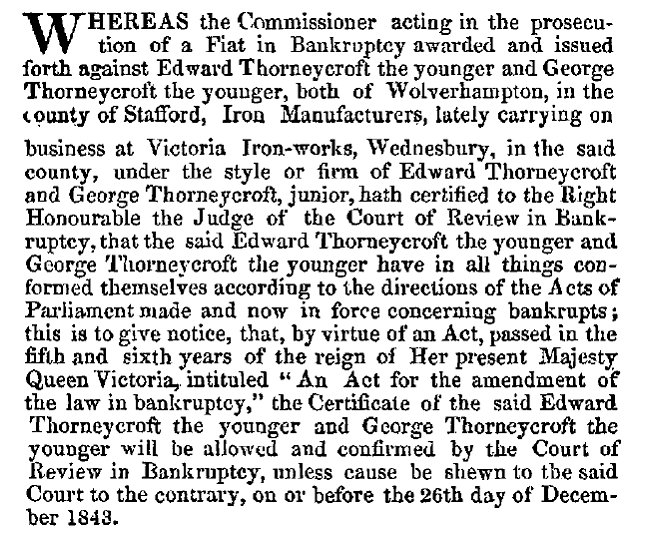
From the London Gazette, 5th
December, 1843.
Most of the
early iron and steel works closed as a result of the
depression of 1875 to 1886 after which the main players
were the Old Park Works, the Patent Shaft, and F.H.
Lloyd at James Bridge Steel Works.
Wednesbury had
many foundries including:
John Deyrick, established
in 1818 |
Addenbrooke & Lloyds
Fosters, established in 1829 |
Edward & John Blakemore &
Company, brass and iron, Camp Street |
J.H. Blakemore, brass &
iron. Trouse Lane |
Thomas Elwell, Bull Lane |
By the 1850s
Wednesbury had secured a monopoly of the new iron tube
trade and had become the largest local supplier of iron
to the railways.
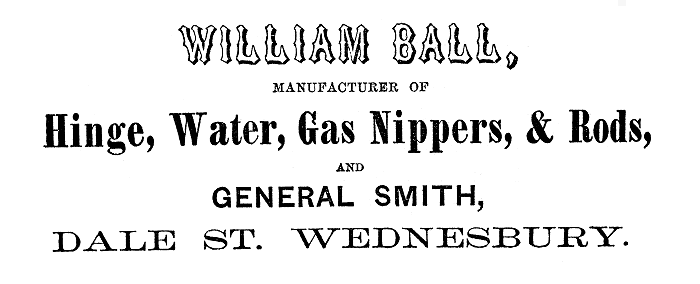
An advert from 1861.
Wednesbury Forge
Wednesbury Forge
was leased by Edward Elwell in 1817 and purchased
by him in 1831. His father, William Elwell, an
ironfounder at Walsall, became Mayor of the town in 1778
and 1787. Edward trained as a surgeon and served with
the Royal Artillery from 1807 to 1811. After returning
to Walsall and practicing there for a while he set
himself up as a maker of edge tools at Sparrow’s Forge
in Wednesbury.
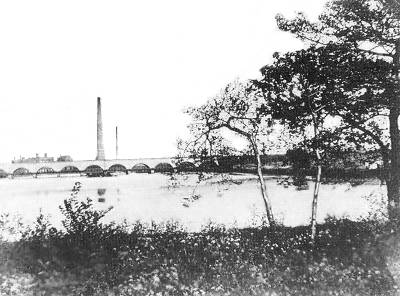
Elwell's Pool and Forge.
|
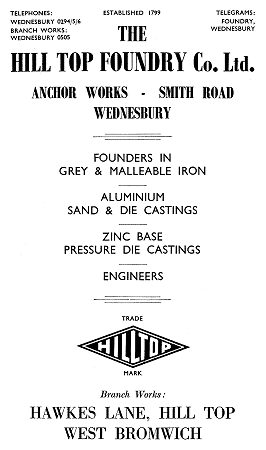
An advert from 1949. |
The Elwell family had another
industrial link with the town because Edward’s uncle,
Edward Elwell established an ironworks in Wednesbury
producing cast iron holloware. It later became Hill Top
Foundry.
|
Read about
Hill Top Foundry |
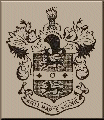 |
|
In 1831 Wednesbury Forge consisted
of a forge or iron mill, a grinding mill which had
previously been a windmill, 2 mill pools covering 25
acres, with a watercourse, a house and 13 cottages,
which were previously workshops.
The machinery at the
forge was driven by steam and water power, and the water
rights provided a worthwhile income from the canal
company and other local firms. By 1851 management of the business
had passed into the hands of Edward’s son, Edward
junior.
|
Unfortunately Edward junior died prematurely and so
his father, now elderly, resumed control of the business
until his death in 1869.
During the American Civil War (1861 to 1865) the company
sold large quantities of edge tools to America, greatly
benefiting from the war, and also exported its products
to many countries. The company's catalogue listed over
1,200 types and sizes of heavier hand tools, such as
axes, forks, hoes, pick axes, shovels, and spades. By
1889 there were around 200 employees. |
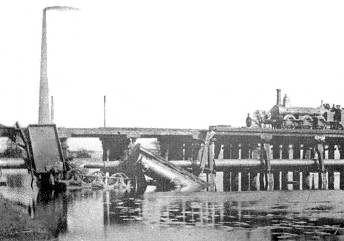
A railway accident at Elwell's
Pool in 1859. |
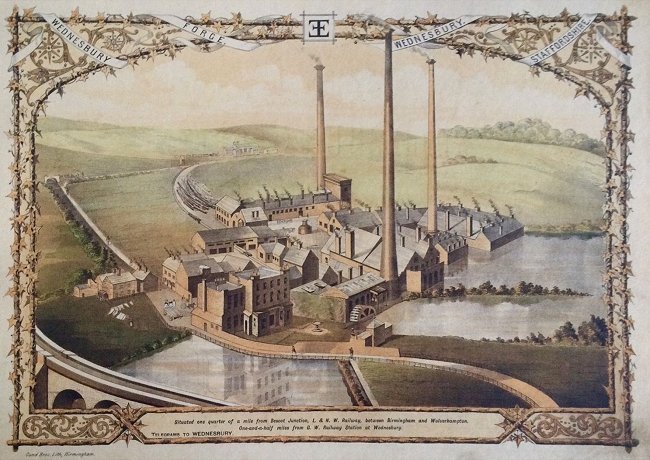
Wednesbury Forge. From the 1869 Elwell
catalogue.
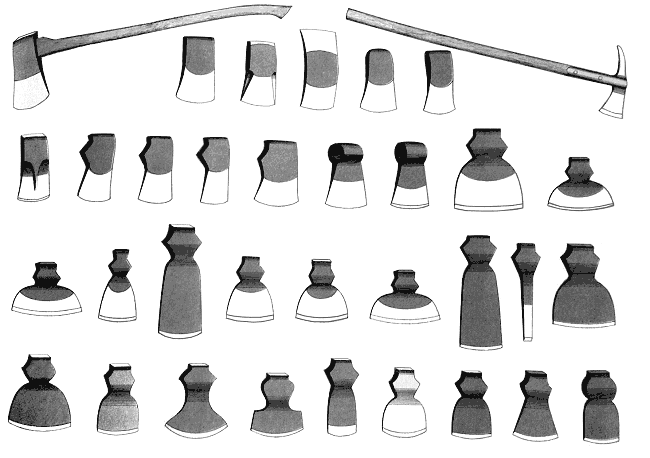
Elwell tools from the 1869 catalogue.
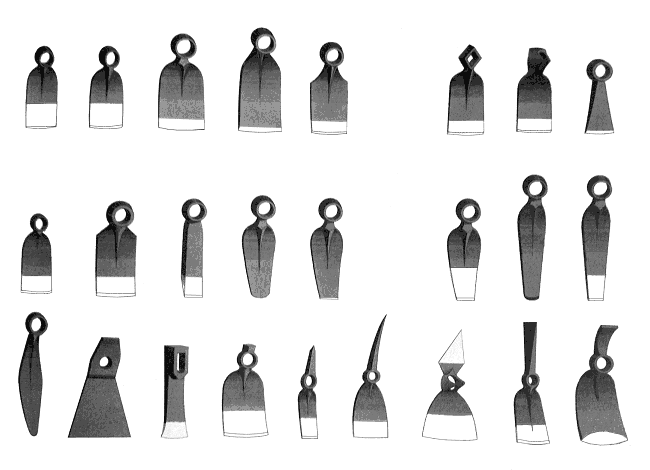
More Elwell tools from the catalogue.
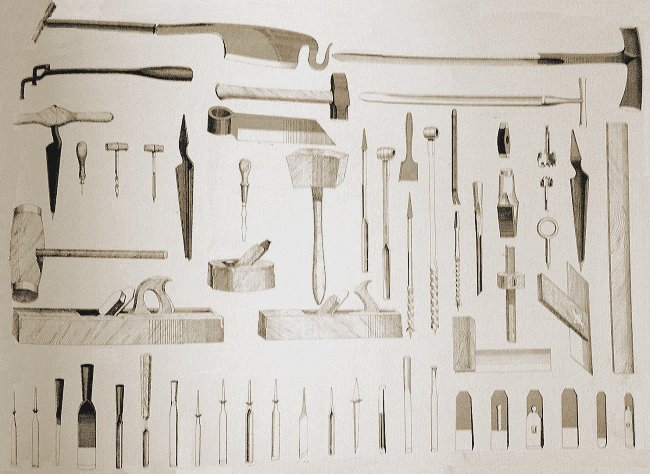
More of the wide range of Elwell tools
made in the 1860s.
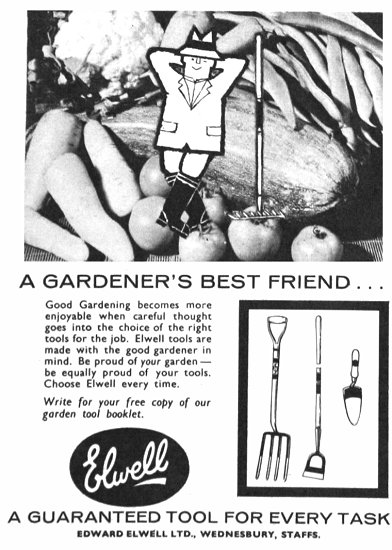
An advert from 1962. |
Edward Elwell never recovered from
the death of his son and became a sad and morose man. He
helped to establish St. James’ Church and a school for
the children of his workmen. After his death Alfred Elwell, a grandson, took over the running of the
business, and on his death in 1902 it became a private
limited company. Two years later the water wheels were
replaced by water turbines.
Around 1930 Edward Elwell Limited and
the Chillington Tool Company of Wolverhampton combined
and formed a holding company; Edge Tool Industries
Limited, and in 1937 the firm displayed a range of tools
at the British Industries Fair, including agricultural
tools, axes, billhooks, choppers, cleavers, earth
borers, edge tools, forks, foundry ladles,
hammers, hatchets, hoes, horticultural tools, matchets,
picks, road contractors' tools, shovels, spades, and
slashers.
In 1962 Eva Industries acquired
Edge Tool Industries Limited, and in 1967 Spearwell
Tools was formed to merge the gardening and agricultural
interests of Spear and Jackson and Eva Industries. |
Spearwell Tools was jointly owned by the 2 companies,
but after several years of losses, Spear and Jackson
acquired the whole group, taking over Wednesbury Forge
in 1970. In 1995 the company became Spear and Jackson
plc.
Wednesbury Forge continued to
produce tools until Christmas 2005, when the factory
closed. The administrative, warehousing and maintenance
sections continued to operate throughout part of 2006.
In 2007 the buildings were demolished, and the site
cleared.
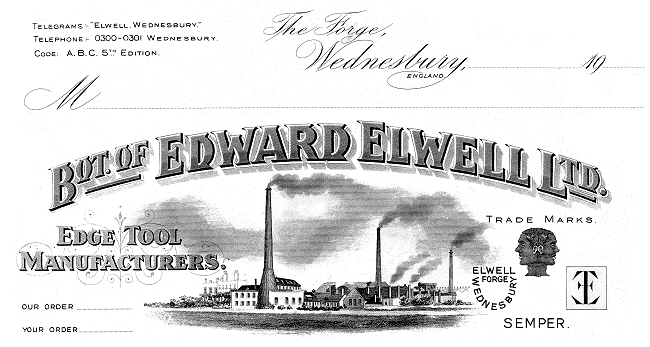
A company letterhead.
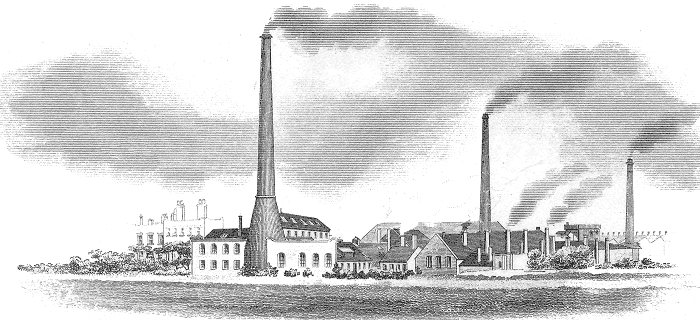
A close up view of the factory from the
above letterhead. On the left is the Elwell family's house.
|
|
|
Read about Old
Park Works and The Patent Shaft & Axletree Company |
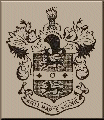 |
|
|
|
|
Read about
Britain's largest foundry -
F. H. Lloyd & Company Limited |
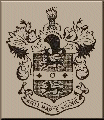 |
|
|
|
|
|
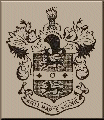 |
Read about Crown Tube
Works and Tube Making |
|
|
|
|
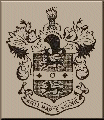 |
Read about Richard
Garbett and the Monway Gas, Steam and Water Cock
Manufactory |
|
|
|
|
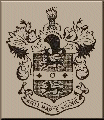 |
Read about John
Bagnall & Sons at Lea Brook |
|
|
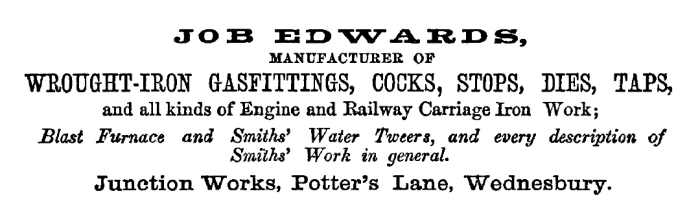
An advert from 1851.
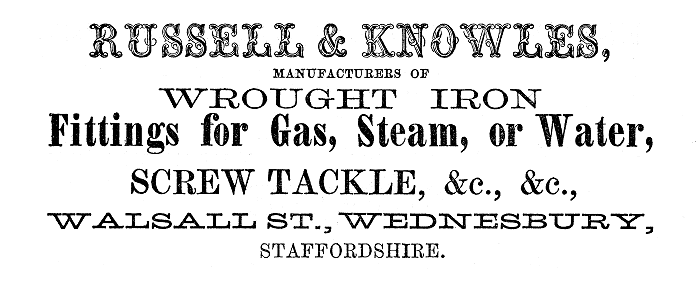
An advert from 1861.
In the 1860s Josh. & Thos. Davies
manufactured a wide range of products, including high
and low pressure steam engines on the vertical direct
action, beam and horizontal principles, steam donkeys
for feeding boilers, improved metallic pistons and
safety valves without stalk or guide, winding and
pumping machinery, and brakes for collieries, hydraulic
presses, lift and force pumps by hand or power, portable
mounted steam threshing machines, improved water heaters
by waste steam, blowing fans by hand or power, hoisting
crabs and cranes, circular saw and rack benches,
shearing and punching presses, pipe fittings, nut and
bolt screwing machines, forge hammers, and boring and
grooving machines for coach axle work, sluice glan plug,
valve and other cocks, lathes, carriage shafting,
pulleys and couplings, etc. The firm also carried out
turning, boring, planing, fitting, shaping, and repairs
done to order.
The firm's small steam engines were
as follows: |
Other
Companies and Products
Henry Hope
& Sons Limited. Windows
|
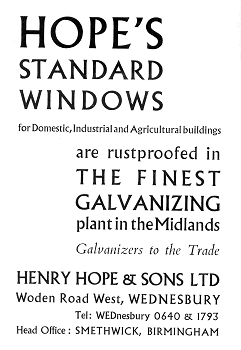
An advert from the early 1960s, |
The company started in 1818 in
Birmingham and started to produce metal casements in
1819. In between 1845 and 1857 they made all of the
windows for the Houses of Parliament, and by 1900 their
main product was metal windows.
In 1904 the company purchased some
land at the corner of Dartmouth Road and Halford's Lane,
Smethwick and in 1905 built the Halford Works. In 1919
the whole business was transferred there, and by the
late 1950s the factory covered around 10 acres.
The company acquired a 37 acre, old
coal mining site in Wednesbury in 1938 and built a new
works there which included a hot dip galvanising plant.
The plant included a 120 ton bath of zinc at a
temperature of 852 degrees Fahrenheit.
|
By 1957 Hopes made over 500 types and sizes of
windows and installed a specially designed, highly
mechanised galvanising plant at Wednesbury for the
production of reversible steel windows for multi-storey
flats. The company had a large export market and in
1965 merged with another metal window manufacturer, the
Crittall Manufacturing Company Limited of Braintree to
form Crittall-Hope Limited. Braintree then became the
new company's headquarters. |
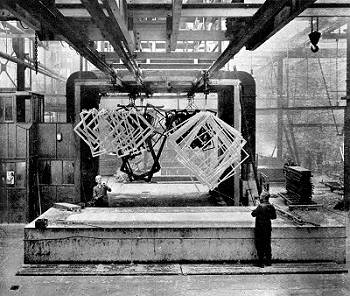
The hot dip galvanising tank. |
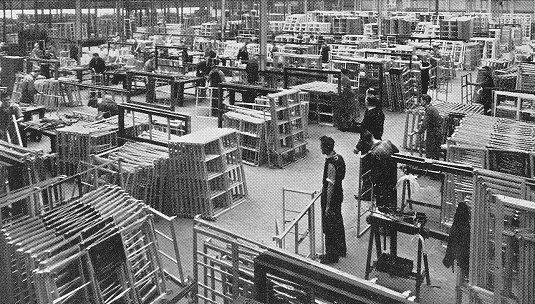
Hope's assembly and storage department.
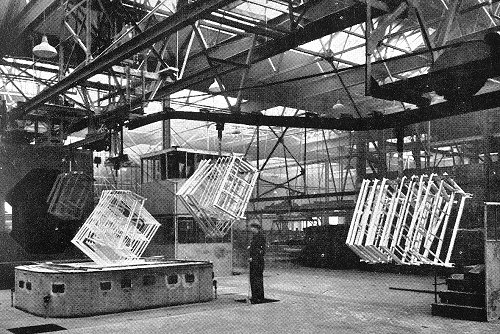
Part of Hope's mechanised galvanising
plant.
|
|
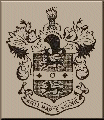 |
Read about William
Mills Limited, producer of accurate aluminium castings |
|
|
Read about Wednesbury's
electrical equipment manufacturers:
William Sanders, and The
Power Centre. |
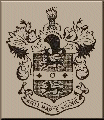 |
|
|
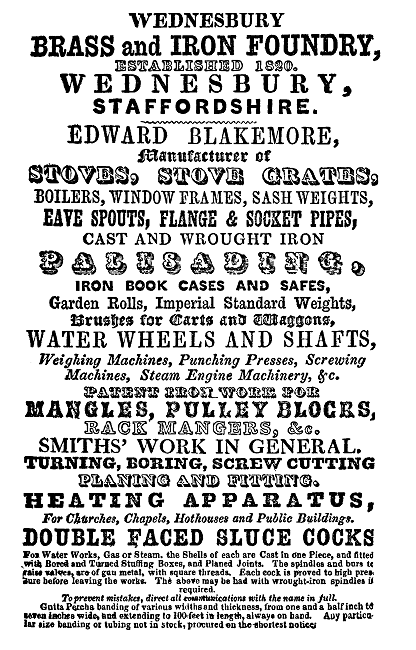
An advert from 1851.
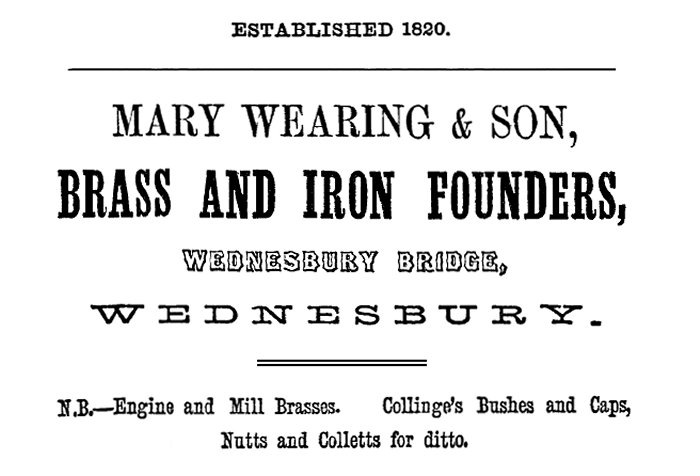
An advert from 1865.
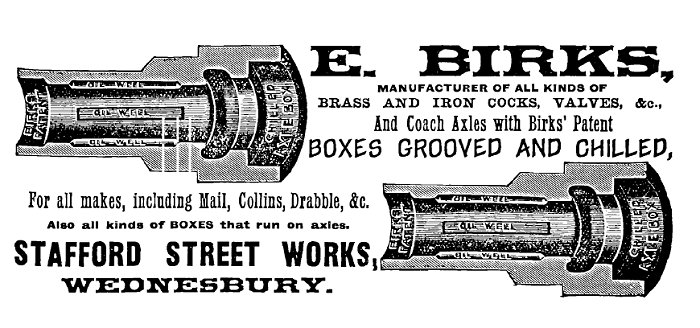
An advert from 1896.
|
Crown Metal
(Wednesbury) Limited Crown Metal
(Wednesbury) Limited was founded in 1919 by W. G.
Hitchman, and became a limited liability company in
1952. At the time, the Managing Director was the
founder's son. The non-ferrous foundry used a range
of alloys including brass, gunmetal, phosphor
bronze, and high tensile alloys of aluminium bronze,
and manganese bronze. Alloys were also made to
individual customer's requirements. Castings were
supplied to many industries including
manufacturers of machinery, hydraulic equipment,
electrical equipment, and ship builders, varying in
weight from a few ounces to five hundredweights.
They were supplied in small or large quantities as
required. The firm prided itself in its quick
service, especially when castings were needed for
plant maintenance. |
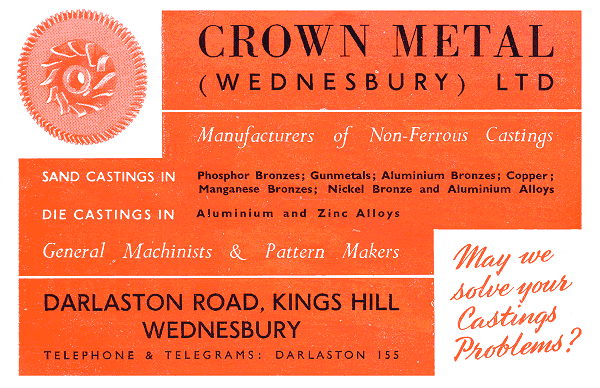
An advert from 1954.
J. Frankel
(Aluminium) Limited First class aluminium
alloys were produced in Wednesbury by J. Frankel
(Aluminium) Limited at Victoria Works, Alma Street.
The company was incorporated on 17th January, 1948.
Before the year was out the firm began to refine
aluminium on the site of the former Globe Ironworks
in Charles Street, Walsall. By 1974 the factory was
producing aluminium alloy ingots from scrap, for use
in foundries, rolling mills, and steelworks. In May
1977 some of the firm's buildings in Bridgeman
Street, Walsall were sold to the South Staffordshire
Waterworks Company for £105,000.
Unfortunately the company only had a short life.
The following notice appeared in the London Gazette
on 8th October, 1982:
J. Frankel
(Aluminium) Limited
At an
extraordinary general meeting of the
above named company, duly convened,
and held at the Holiday Inn, ATV
Centre, Birmingham, on 15th
September 1982, the subjoined
extraordinary resolution was duly
passed:
That it has
been proved to the satisfaction of
this meeting that the company cannot
by reason of its liabilities
continue its business, and that it
is advisable to wind up the same,
and accordingly that the company be
wound up voluntarily, and that
Bernard Phillips, of New Cavendish
House, 18 Maltravers Street, London
WC2 R3EJ and David Zackheim, of 48
Welbeck Street, London W1M 7HE, be
and they are hereby appointed joint
liquidators for the purpose of such
winding-up. |
|
|
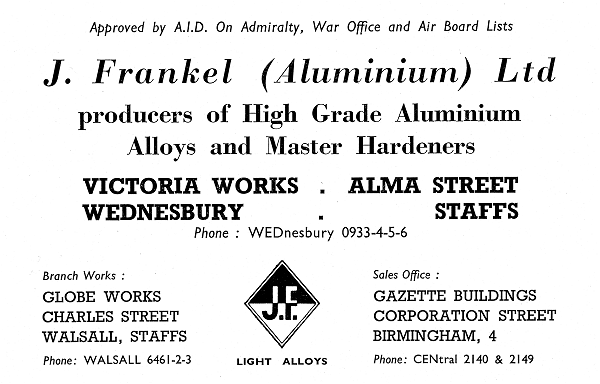
An advert from 1954.
Roberts & Company (Wednesbury) Limited The
firm, based in Franchise Street, was founded in 1919
and became a limited liability company on 22nd
August, 1931.
It specialised in the production of galvanised
steelwork for overhead electrical transmission
lines, carried on wooden poles.
The firm had a large, well-equipped forge and
bending shop where special steelwork of all kinds
was produced including motor body parts, hinges, tow
bars, towing brackets, and signal ladders for
railways.
The firm also specialised in flame-cut and welded
fabrications.
Unfortunately the business, like many others,
suffered during the recession in the 1990s. The
company went into receivership on 17th May, 1993,
and went into voluntary liquidation on 31st January,
1998. |
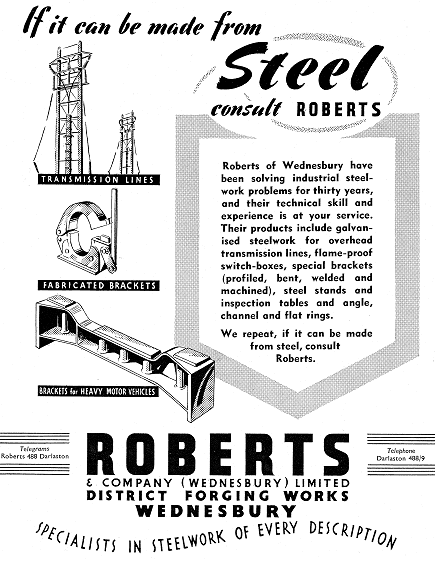
An advert from 1954. |
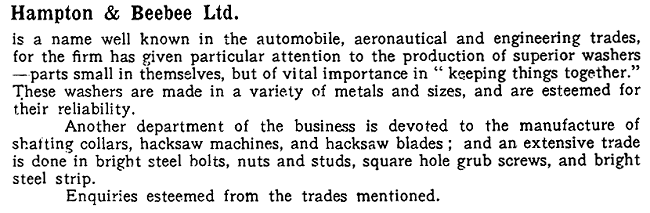
The text above and the advert
below were taken from the 1918 Wednesbury Official
Handbook. |
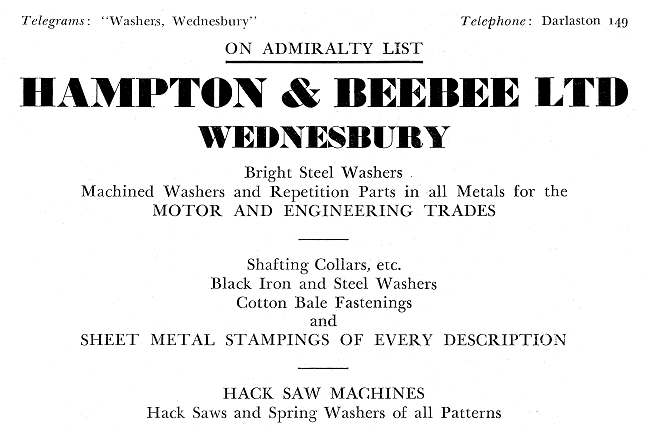
An advert from 1954.
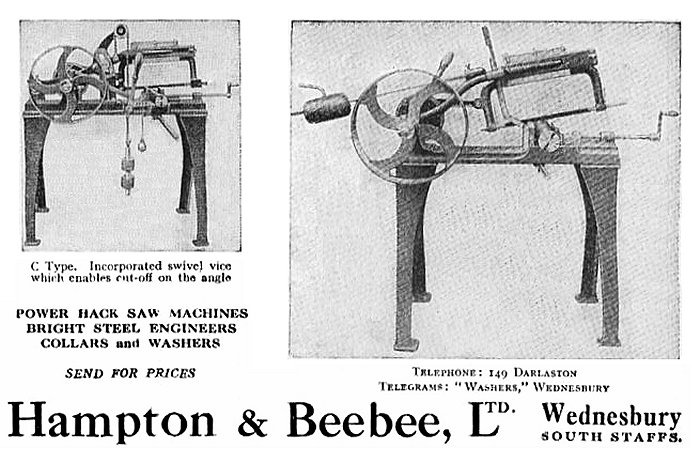
An advert from 1956.
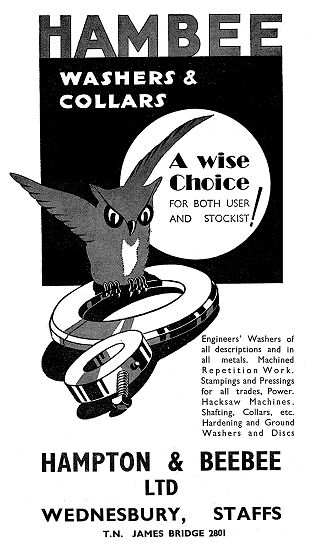
An advert from 1958.
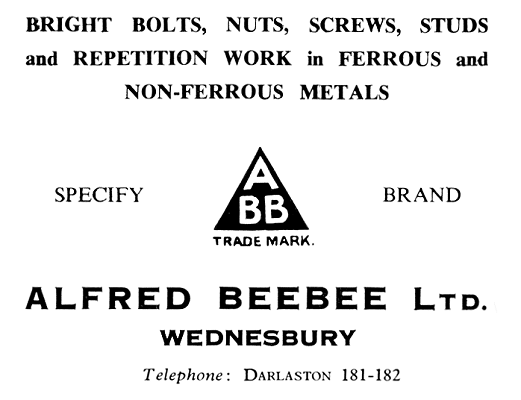
An advert from the mid 1950s. Courtesy of
Christine and John Ashmore.
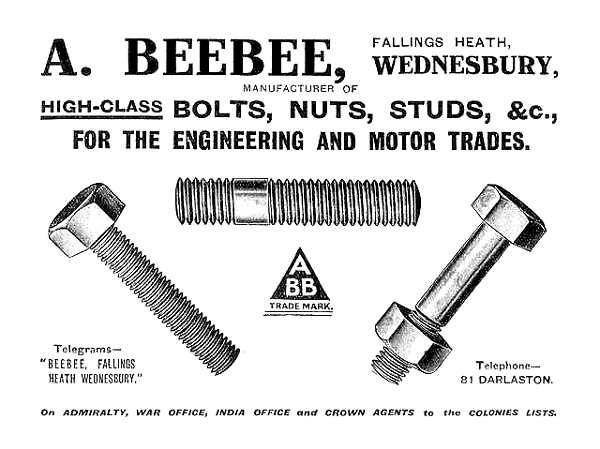
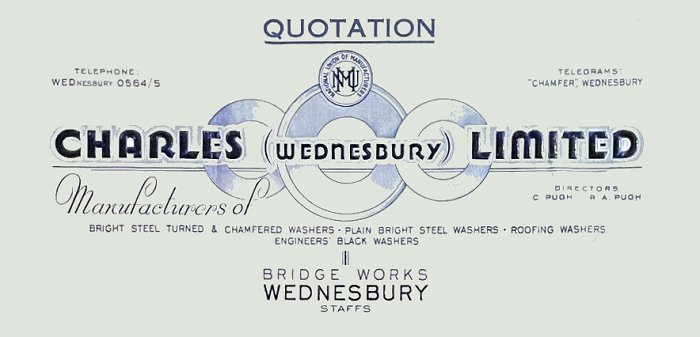
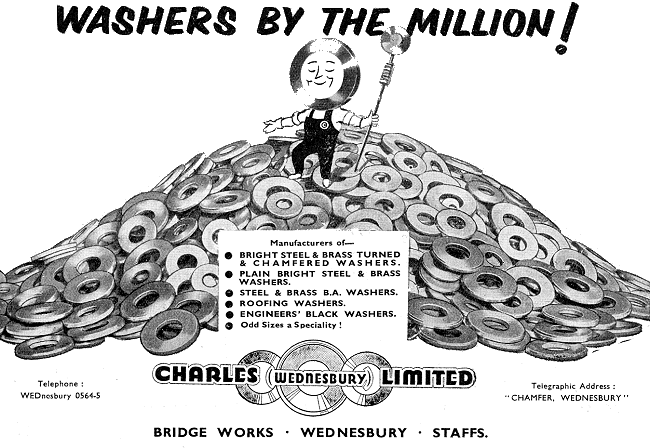
An advert from 1958.
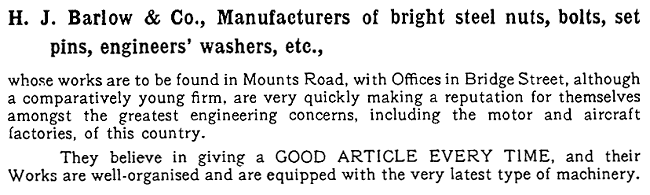
The text above and the advert
below were taken from the 1918 Wednesbury Official
Handbook. |
Quilliam
Limited. Jute Bag Manufacturers
|
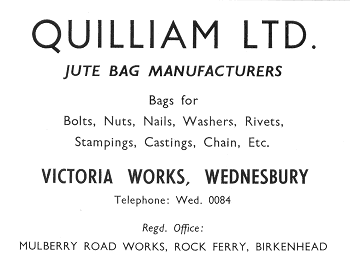
An advert from the early 1960s. |
Quilliam Limited manufactured all kinds of jute
sacks and bags for industrial use at Victoria Works,
Potter's Lane.
They produced new and reconditioned sacks for all
types of small metal components, steel strip and wire,
nuts, bolts, nails, washers, rivets, stampings,
castings, and chains.
The factory survived until the early 1960s when it
was destroyed in a disastrous fire. |
|
|
Read about Edwin Richards &
Sons who made coach axles, springs, and fittings. |
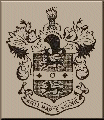 |
|
|
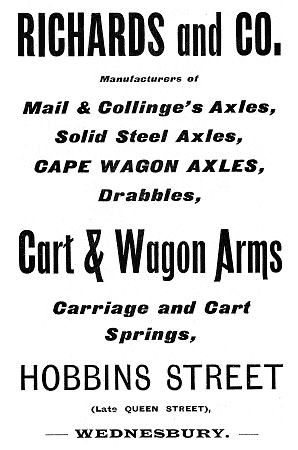 |
Another local company,
with a similar name, supplying the same range of
products as Edwin Richards & Sons was based in
Hobbins Street, off Portway Road. This advert is
from the 1909 Ryder's Annual.
The Ordnance Survey map from
that time does not show any obvious factory in
Hobbins Street, only houses. There were more
sizeable buildings at the the ends, fronting on the
Holyhead Road, and in Portway Road, but that is all.
It could be that Richards &
Company were suppliers of Edwin Richards & Sons'
products, and possibly run by a member of Edwin
Richards' family. |
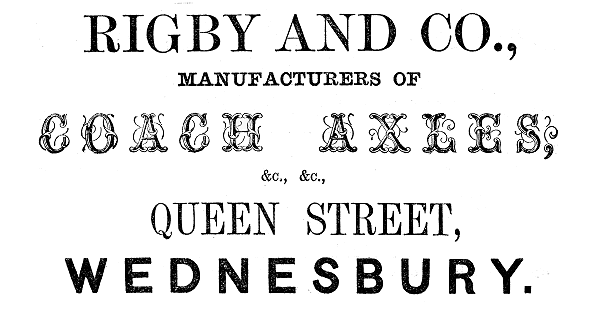
Another coach axle manufacturer. The
advert is from 1861.
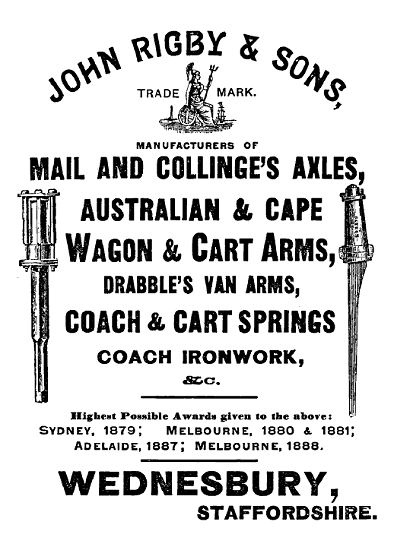 |
Another advert for John
Rigby & Sons who were based at Phoenix Works.
This advert is from 1896. |
Wednesbury also had at
least one cycle maker.
S. J. Taylor is listed in Peck's 1896 Trade
Directory of Birmingham. The address given is Apsley
Place, Pritchard Street, Wednesbury.
The advert opposite is from
Ryder's Annual, 1911. |
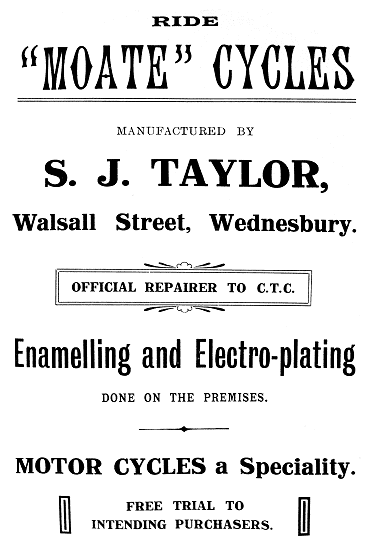 |
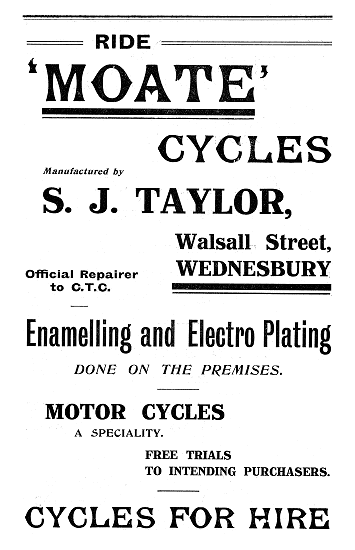 |
The advert opposite is
from the 1909 edition of Ryder's Annual. |
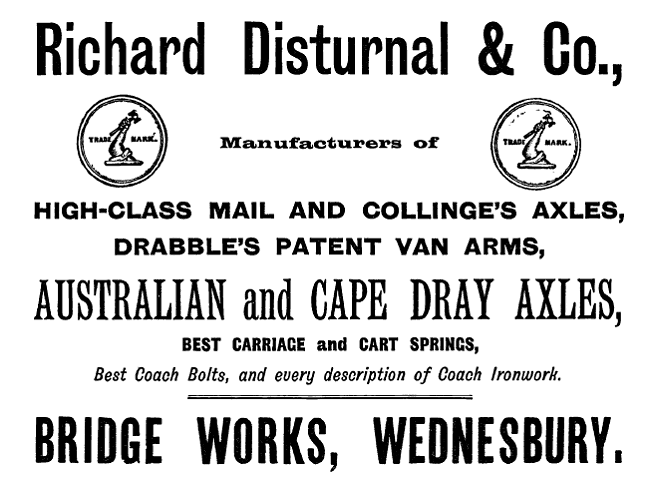
Richard Disturnal & Company also
produced axles. The advert is from 1896.
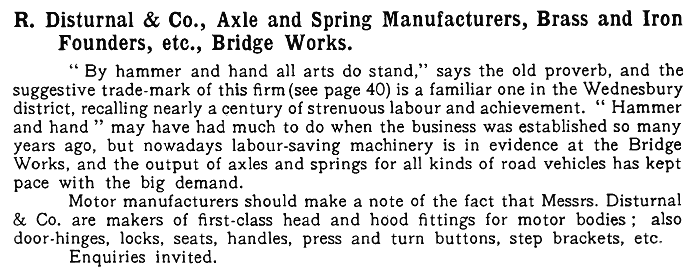
From the 1918 Wednesbury
Official Handbook. |
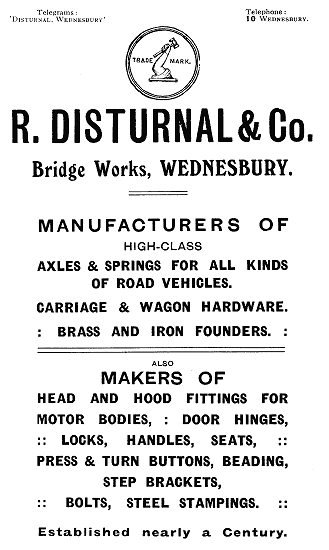 |
|
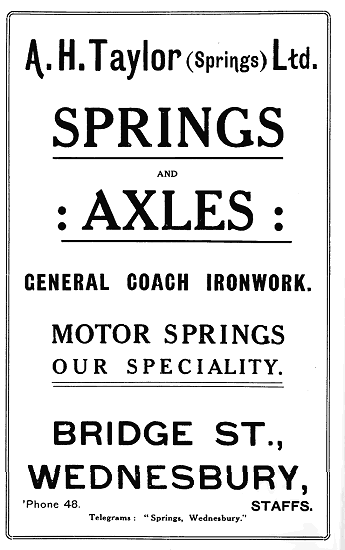 |
Two
adverts from 1918.
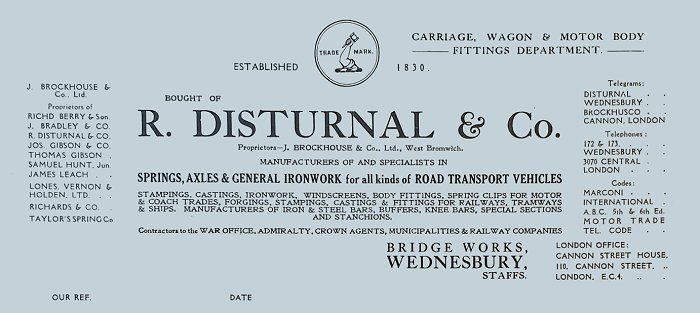
A letterhead from
1924. |
|
Hickinbottom's Bakers
Many people will fondly remember
Hickinbottom's excellent bread, baked in the Albert
Street bakery and delivered door to door by expert
roundsmen.
The business started in 1893 when Sam Hickinbottom, a wheelwright at the Patent Shaft and
Axletree Company was on short time, and couldn't find
alternative work. His wife Martha had previously worked
as a domestic help at Priddins Bakers in Bridge Street,
where she learned the art of bread making. Because of
their financial hardship, the young couple decided to
establish their own bakery.
They rented a shop with a small
bakehouse in Lower High Street, opposite the Board
School and began to bake and
sell bread. Sam realised that the best way to sell their
bread was to take it around the local area. He began by
selling bread to his ex-workmates, delivered in a small
basket. He soon acquired a hand cart. Sales were good
and so the Hickinbottoms acquired a pony and cart.
|
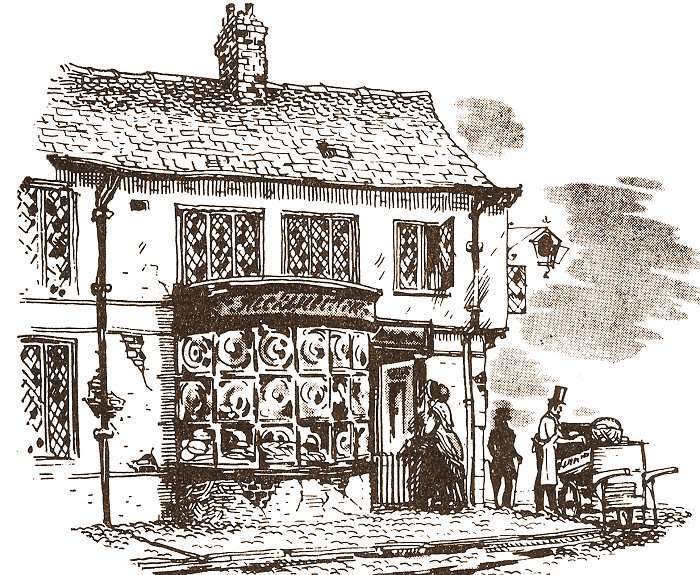
An impression of
Hickinbottom's first shop in Lower High
Street. |
Within a short while the business
moved across the road into larger premises with a new bakehouse. Martha soon became pregnant and had the job
of bringing-up her first son Joe, followed by two others
Bert and Len. Sam then employed a baker and was able to
greatly increase the product range.
Early success encouraged him to purchase a pony and
cart but such was their financial position that this was
sometimes hired out when not required for the
Hickinbottom business. The income from this hiring
helped to feed the pony.
As business increased an
opportunity arose to move to better premises. The owner
of a business opposite their shop offered to build a
small new bakehouse onto the existing building in return
for them signing a seven year lease. Sam and Martha
seized this opportunity and Sam further increased the
facilities by building a small stable for the pony and a
covered area for loading.
By the time the seven year lease
had expired the Hickinbottoms had three sons, Joe
(1893), Bert (1897) and Len (1901) and when old enough,
the boys helped in the business by delivering bread in
three wheeled baskets. Despite this help, Sam did not
usually finish work on a Saturday until between 8pm and
9pm. |
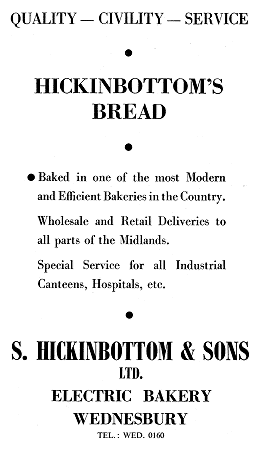 |
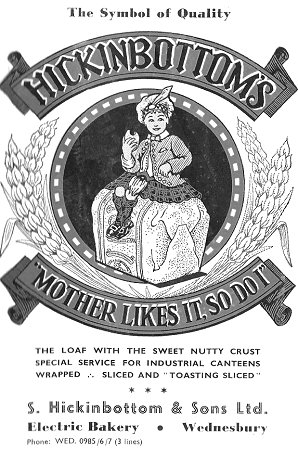 |
In 1906 at the age of 13, Joe started
classes in shorthand, typewriting and book-keeping and
began work at Stockdale and Sargent, solicitors, in
Lower High Street. The Senior Partner wanted Joe to take
Articles and become a lawyer, but instead he took his
father's offer of joining the family business.
The business became extremely successful. By the
First World War, Sam had been joined by his three sons,
and had moved into a larger premises in Victoria Street
with better facilities, including two Cornthwaite ovens.
Only the best ingredients were used including top grade
flour from Rank's Flour Mills. The bread
gained a deserved reputation for high quality.
During the war the business thrived because other
foods were in short supply and so the demand for bread
greatly increased. By this time Joe was going out with
Annie Lett of Tipton, whom he had met at Camp Street
Sunday School. She later became his wife and was recruited into
the business to take charge of a horse and cart to help
with deliveries. |
The firm soon outgrew the Victoria Street premises
and so a larger bakery was built nearby in Victoria
Street. It included a lot of second-hand equipment from
Birmingham bakeries, and opened in June 1923. The
employees even hauled 30,000 glazed bricks for the
building, to the site, after normal working hours. The
second-hand equipment was slowly updated, and the firm
acquired its first motorised van and a large horse-drawn
flat wagon to transport 25 tons of flour weekly, from the nearby GWR goods
depot to the bakery. The second hand equipment was
gradually updated. Sam died in 1939 and his eldest son Joe became
Managing Director.
In 1951 Hickinbottoms joined Allied Bakeries of
London, makers of Sunblest bread. By 1960 the Victoria
Street bakery supplied around 30,000 customers, and it
became essential to extend the bakery in order to cope
with increasing demand. The Hickinbottom brothers stayed
in control of the Wednesbury operation, Joe as Managing
Director, Bert as Transport Director, Len as Sales
Director and Bert's son Geoffrey as Sales Manager.
The firm decided to build a new bakery at Wednesbury
and if possible acquire the area around the existing
bakery so that the new bakery could link-up with the
existing buildings. Over the next two years Bert
Hickinbottom set about purchasing adjoining properties, which were
demolished to make way for a new bakery.
In 1961 the family lost two members
from the second generation, Bert and Len. Third
generation Geoffrey was appointed Managing Director and
his cousin Michael, Director, and second generation Joe
became Chairman.
Building work soon got underway and the
new Electric Bakery in Albert Street opened in May 1963.
At the time the bakery supplied around 30,000 retail
customers, 800 wholesale customers, and employed 180
people. The company operated eighty vehicles and had its
own maintenance department.
Michael Hickinbottom soon became Chief Executive of
the group, leaving Geoffrey in charge of the operation
at Wednesbury. In 1977 Geoffrey decided to retire to
Norfolk. At the time there were 600 employees and well
over 200 vehicles at the Wednesbury site. Soon the Hickinbottom name ceased to be used
and door to door deliveries were
discontinued. The Wednesbury bakery closed in 1989 and
production was transferred elsewhere. Demolition of the
bakery soon followed, to make way for the Mecca Bingo
Club, which stands on the site today. |
The Steel
Nut & Joseph Hampton Limited. Fastenings, Steel Bars,
Tools |
The Steel Nut & Joseph Hampton Limited made a wide
range of products at their Fallings Heath works. As well
as nuts, bolts, set screws, and studs they produced a
wide range of bright drawn steel bars, and tools,
including vices for wood and steel, clamps, dowelling
jigs, holdfasts, and wood planes. In 1955 the company
produced its patented quick release screw vice. The
factory was known locally as "the Woden". For
a detailed history look at the
Darlaston industry
section on this website. |
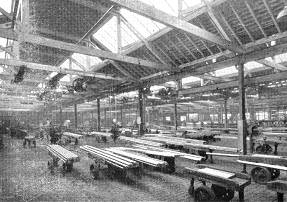 |
|
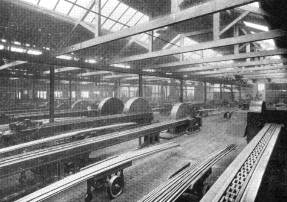 |
Two views of the
Steel Department. |
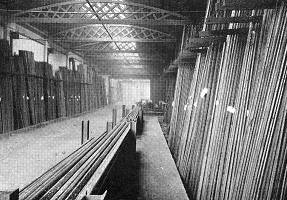
The Steel Store. |
|
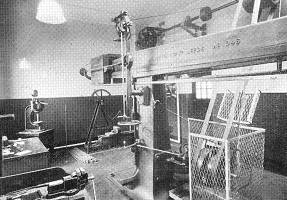
The Test House. |
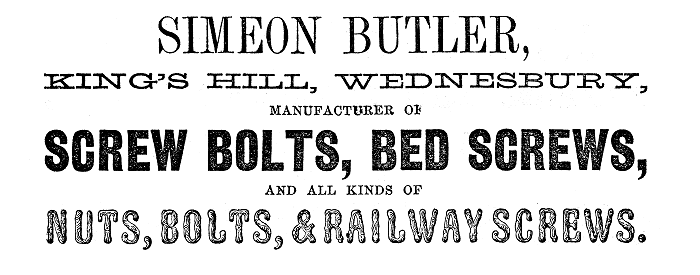
Another nut and bolt manufacturer. The
advert is from 1861.
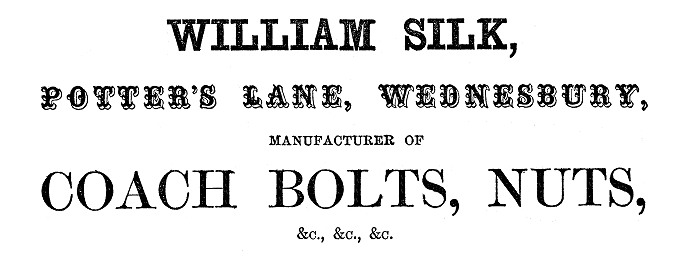
Another nut and bolt maker in 1861.
|
|
Read about
Samuel Platt Limited based at King's Hill
Foundry. |
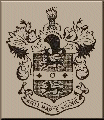 |
|
|
Read about
Prodorite Limited.
A well known and
important manufacturer. |
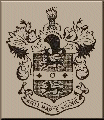 |
|
|
Isaiah Platt Limited
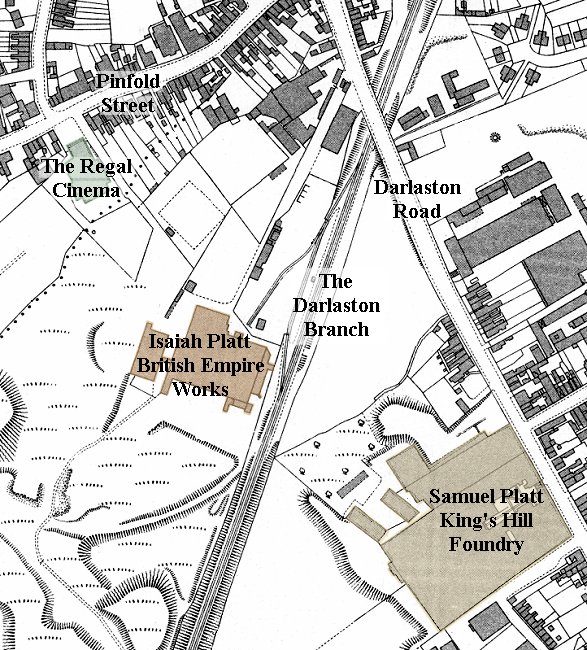
The location of
Isaiah Platt's British Empire Works.
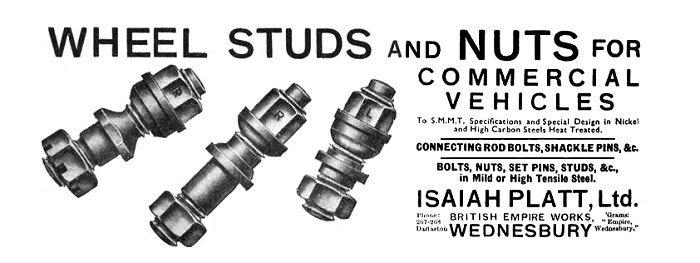
An advert from
1938.
The
following
description is
from his
obituary,
produced by the Institution of
Mechanical Engineers in 1931. Isaiah
Platt, O.B.E., who was born in
1860, was the youngest son of the late
Mr. Samuel Platt, founder of the
firm of Messrs. Samuel Platt, King's
Hill Foundry, Wednesbury, with whom he
served his time from 1876 to 1881. He then entered the drawing office,
of which he was given sole charge in
1886, and subsequently became a partner.
In 1918 he severed his connexion with
the firm and established the firm of
Messrs. Isaiah Platt of Wednesbury,
where he built up a most successful
business. Mr. Platt was 71 years of age at the
time of his death which occurred on 1st
August 1931. He had been a Member of the
Institution since 1903. |
|
Isaiah Platt Limited was
established 1919. It had a
capital £50,000 and employed
200 people. The directors
were: Isaiah Platt, O.B.E. (Governing), W. G. Berry
(Managing) and H. W. Wilson.
Manufactures. The firm specialised in bright steel bolts,
set-screws, studs, bright and
black faced nuts, bright drawn steel in
rounds, hexagons and squares. |
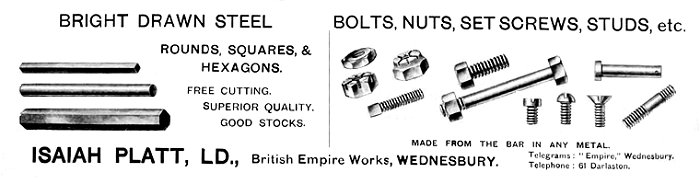
An advert from
1921.
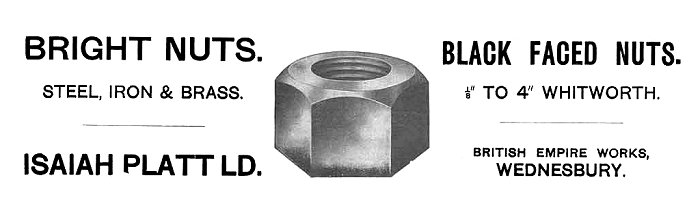
An advert from
1928.
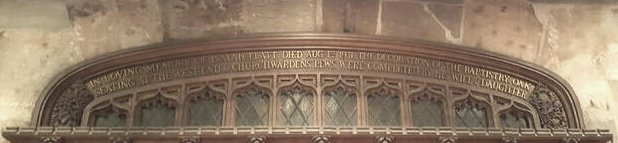
The Platt
memorial.
There is a memorial to Isaiah Platt
in the Choir Vestry at Saint
Bartholomew's Church in Wednesbury. It
reads as follows:
In
loving memory of Isaiah Platt, died Aug
1st 1931. The decoration of the
Baptistry, Oak Seating at the West End &
Churchwardens’ Pews were completed by
his wife & daughter.
|
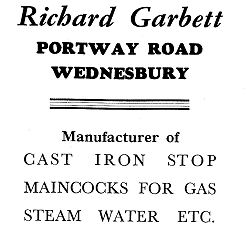 |
|
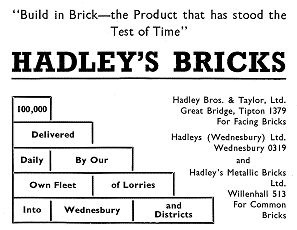 |
Two adverts
from 1949. |
There were several galvanisers in the town
including Frost & Sons of Falcon Works, Church
Street, Moxley which specialised in galvanising
electricity transmission towers for the Central
Electricity Board, and galvanising every kind of
wrought and cast iron work, and tubes and
fittings. The company had a reputation for quick
service, high quality work, and low prices. |
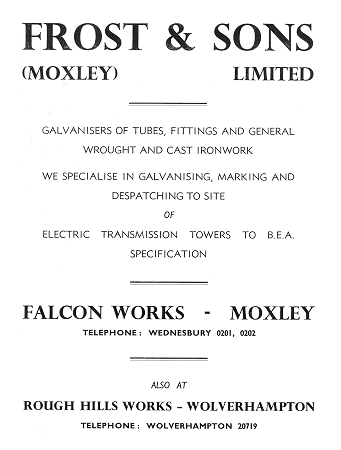 |
|
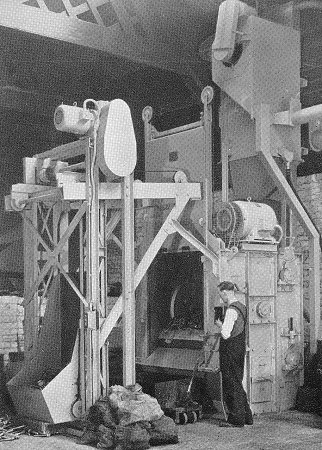 |
An
advert from 1954. |
|
A shot
blasting machine. |
|
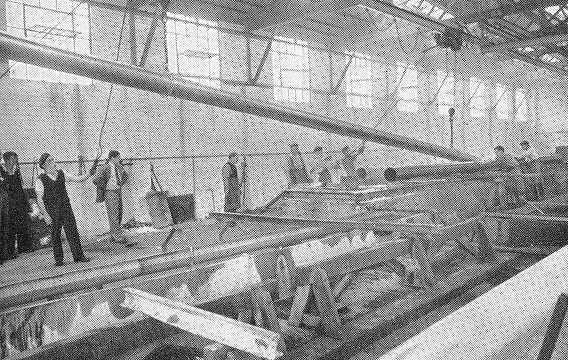
Galvanising tubes,
forty feet long and eleven inches in
diameter.
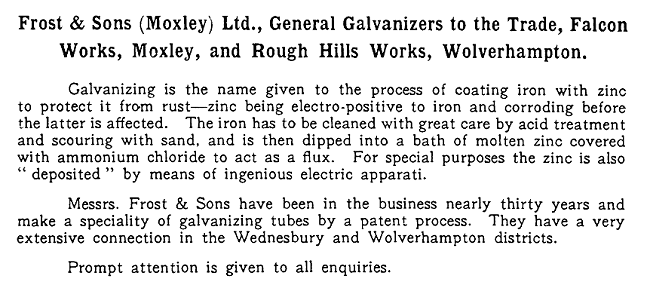
The text above
and the advert below were taken from
the 1918 Wednesbury Official
Handbook. |
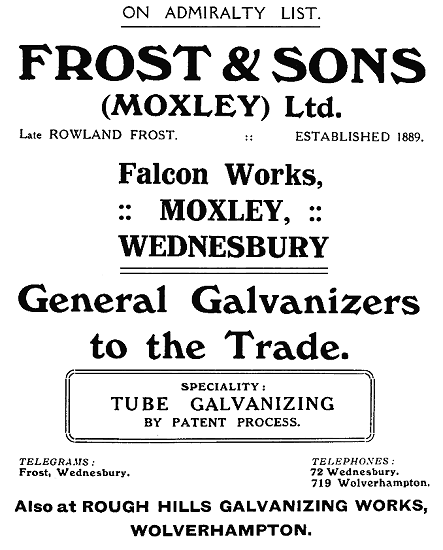 |
Frost & Sons (Moxley) Limited
was founded in 1889, and initially
specialised in tube and general
galvanising. There were two
branches, one at Rough Hills,
Wolverhampton, and another at Ebro
Works, Tividale, Tipton, which
specialised in galvanising bolts,
nuts, and washers etc. by
centrifugal force. The business was
wound-up in March 2002. |
Wednesbury, like many other local town had its
share of brick makers. The very last one was
Hadley (Wednesbury) Limited, based at Brunswick
Park Brickworks in Crankhall Lane.
Hadleys started producing bricks in 1876, and
by 1950 150,000 bricks were leaving the factory
each week. Production ended in about 1960 when
the business closed. Another long-standing
Wednesbury business was Isaiah
Oldbury Limited, founded in 1861 to
manufacture coach and cart axles at
the Reliance Coach Ironworks.
The
founder, Isiah Oldbury, J.P. born at
Wednesbury in May, 1840 was Chairman
of the Wigmore Schools Management
Board, a Borough Magistrate, a
prominent member of the Liberal
Party, a Wesleyan Methodist, and
Mayor of Wednesbury in 1896 to 1898. |
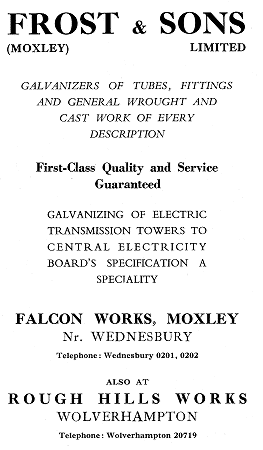
An advert from 1949. |
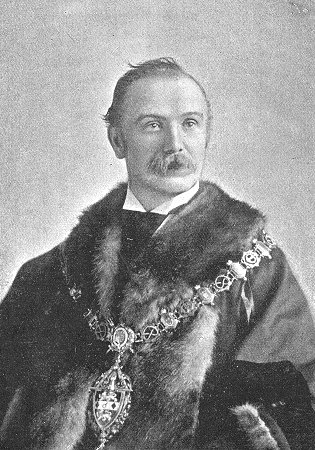
Councillor
Isaiah Oldbury in his mayoral robes. |
The firm was a pioneer in the
development of trailer undergear,
and opened a factory in West
Bromwich for the production of axles
and drop-forgings. The firm had
its own malleable and grey iron
foundry, a spring shop, and a
machine shop for the production and
supply of general machined parts.
The factory was complete with a
range of drop stamps, drop hammers,
and machine tools.
Trailer axles and components were
regularly exported to much of the
world, including Rhodesia, where the
firm built-up a large export market
in heavy cart axles.
The many products included roller
bearing hubs, internal expanding
brakes, brake fittings, towing
couplings, drawbars, jockey wheels,
steel wheels, springs and fittings.
Large numbers of specially designed
chassis were supplied to
manufacturers of caravans, portable
welding compressors, and vacuum
plant.
In 2000 the company was acquired
by Skan Group Holdings and moved to
its present 2½
acre site in Wobaston Road,
Wolverhampton. |
From Wednesbury
Faces, Places and
Industries, published in
1897: The Reliance
Coach Ironworks, owned by
the present Mayor, Mr.
Isaiah Oldbury occupy a high
and influential position in
this important branch of
manufacturing activity. It
is about twenty three years
since the present works were
started, and thirty three
years since the business was
founded by Mr. Oldbury. Its
very successful career from
the inception to the present
time abundantly testifies to
the energy and ability
brought to bear upon its
management. The works have
been enlarged from time to
time to meet the increased
demands, and only recently a
malleable iron foundry has
been added.
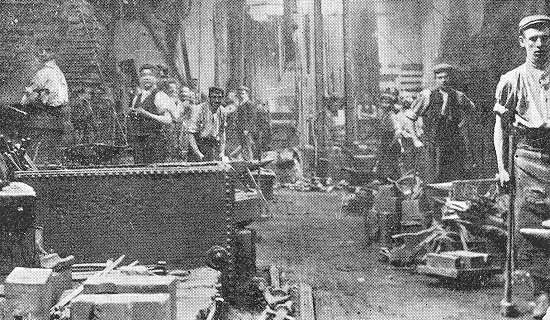
The Smithy.
They now
cover a considerable area of
ground, giving constant
employment to between one
hundred and fifty and two
hundred hands, and being
equipped with all the
requisite steam power
machinery and labour-saving
appliances to facilitate
rapid and economical
production. The chief
manufactures include coach
bolts and nuts, steps,
scrolls, dash irons, clips,
shackles, and coach ironwork
in general; also mail,
Collinges, drabbles, and
other axles, and springs.
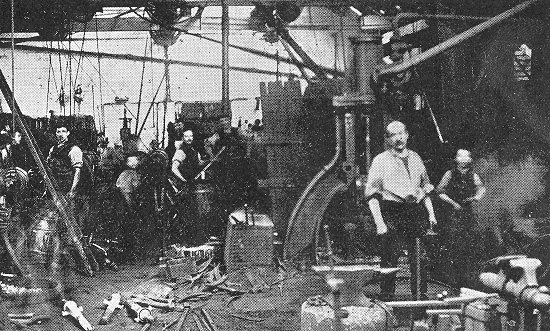
Axle and turning shop.
For all
these productions Mr.
Oldbury enjoys a high
reputation both at home and
abroad, hence his large and
steadily increasing
connections; and it may be
stated that he is a
well-known contractor to Her
Majesty's Government, the
War Office, and Admiralty;
also to Sir W. G. Armstrong,
Mitchell and Co., Limited,
and Sir Joseph Whitworth and
Co., Limited. None but the
most durable and best
finished goods leave the
premises, whilst the
productive facilities are
such as to ensure the speedy
execution of all orders. |
|
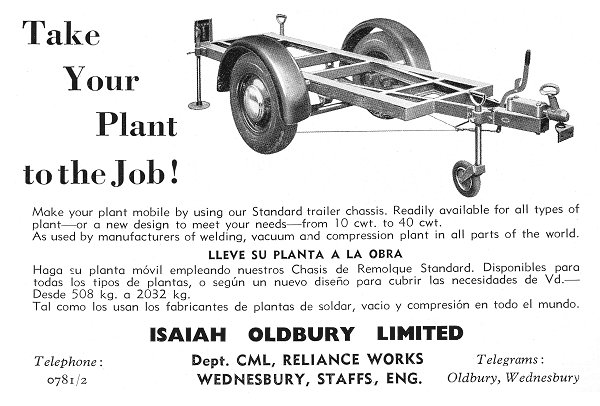
An advert from 1954.
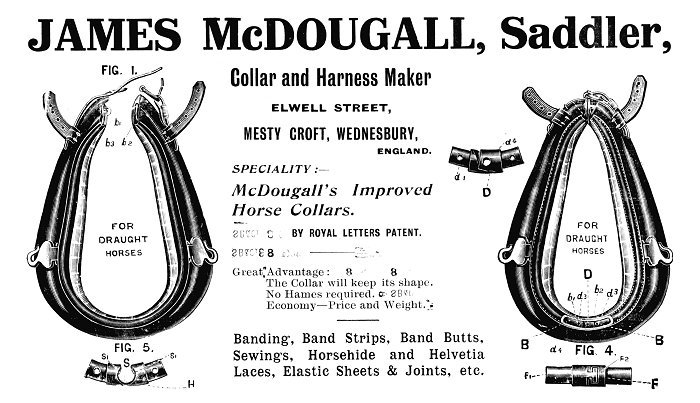
An advert from 1916.
M. H. Lowe Limited were one of the
oldest engineer's merchants in the
Midlands. The shop in Union Street
was a delight for anyone interested
in tools.The business was
registered on Saturday, January 4,
1947 but is now dissolved.
The firm specialised in all kinds
of engineer's supplies and equipment
for local companies, and carried
comprehensive stocks of all
reputable makes of tools. They were
the sole agents in the West Midlands
for 'Lion' brand 'G' clamps and
strap clamps, and were stockists and
technical advisers for 'Universal'
grinding wheels. Nuts, bolts, and
Allen screws were also stocked, as
well as drill chucks, pipe tools,
and precision measuring tools. |
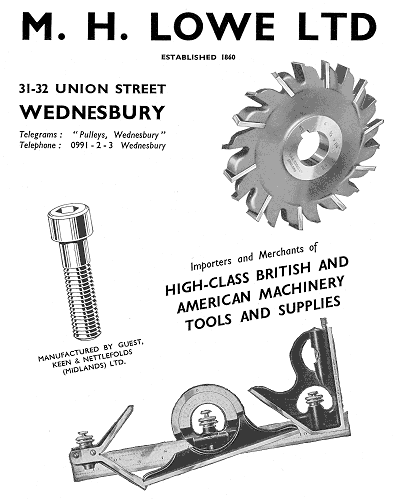
An advert from
1954. |
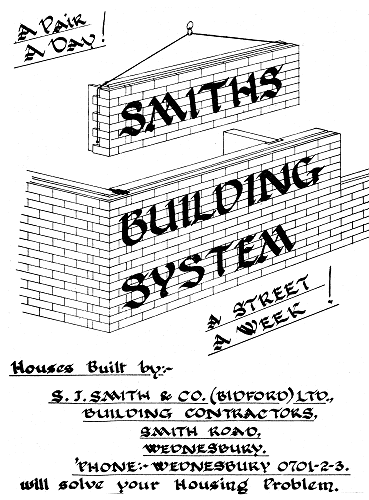
An advert from
1954. |
The housing shortage after World
War 2 led to the construction of
many pre-fabricated houses which
were relatively cheap, and fast to
build.
Mr. H. Howard-Smith developed a
method of building
traditional-styled brick houses
quickly, by assembling factory-built
components. S. J. Smith (Bidford)
Limited was founded
to mass-produce the components, and
to build the houses in record time.
The company Chairman was Mr. H.
Howard-Smith, and the Managing
Director was Mr. S. J. Smith.
Using the Smith system, a house
could be built in half the normal
time. By the mid 1950s the firm had
built over four thousand houses in
the Midlands, at a rate of one
thousand a year, and with a labour
force of less than 500 men.
It was extremely difficult to
distinguish the houses from those
built using traditional methods. |
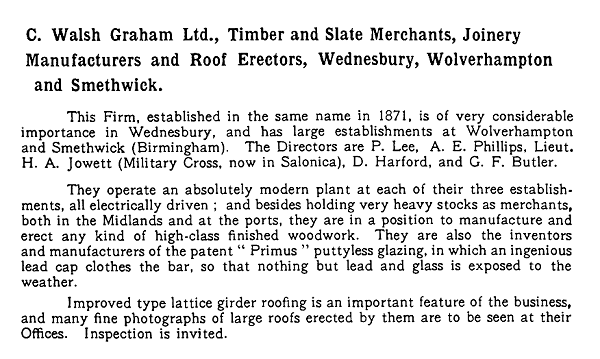 |
A once
familiar sight in Potters Lane was
C. Walsh Graham's timber yard. The
text opposite and the advert below
were taken from the 1918 Wednesbury
Official Handbook. |
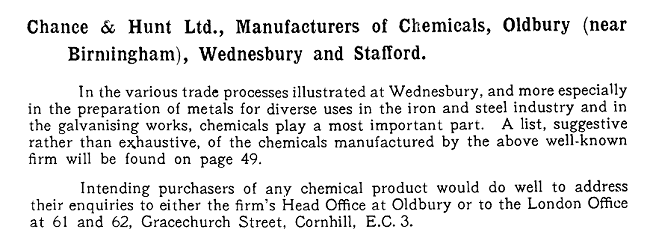
The text above
and the advert below were taken from
the 1918 Wednesbury Official
Handbook. |
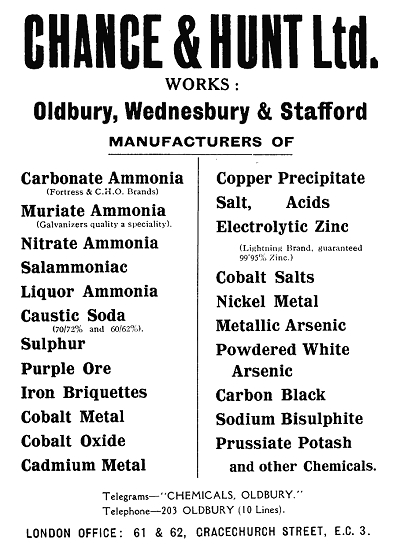
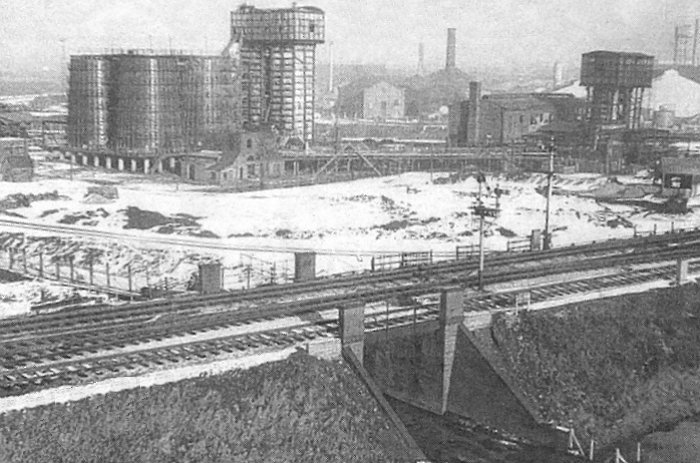
The Chance and
Hunt chemical works at Wednesbury.
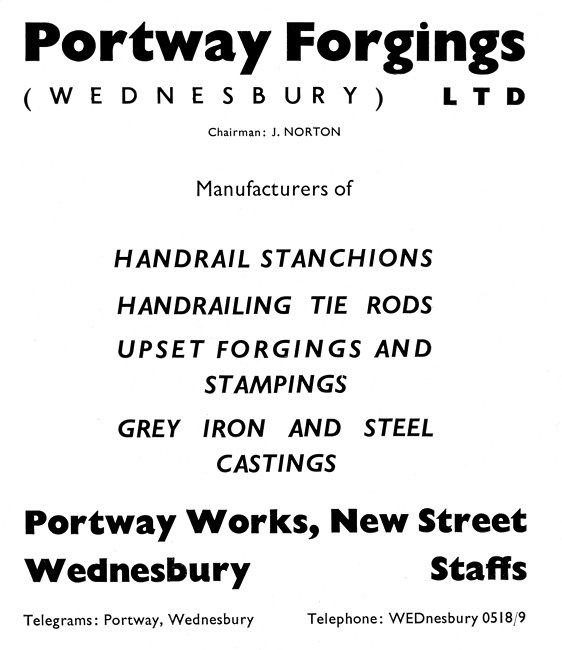
An advert from
1954.
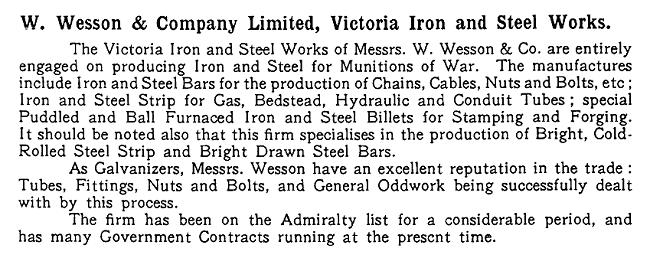
The text above and the
advert below were taken
from the 1918 Wednesbury
Official Handbook. |
|
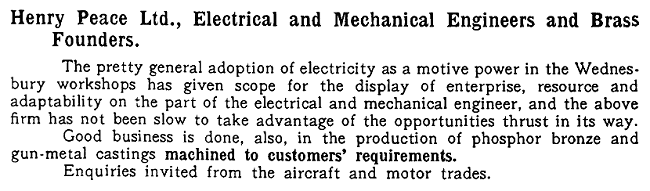
The text above
and the advert below were taken from
the 1918 Wednesbury Official
Handbook. |
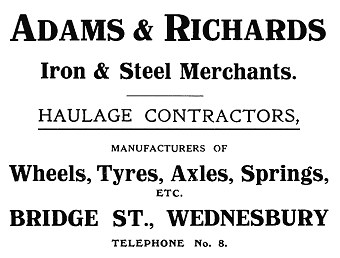 |
|
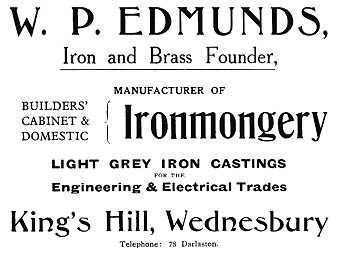 |
Two
adverts from 1918. |
|
|
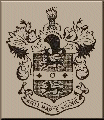 |
|
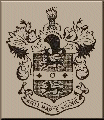 |
|
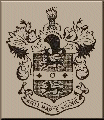 |
Return to
Growth |
|
Return to
the contents |
|
Proceed to
Education |
|